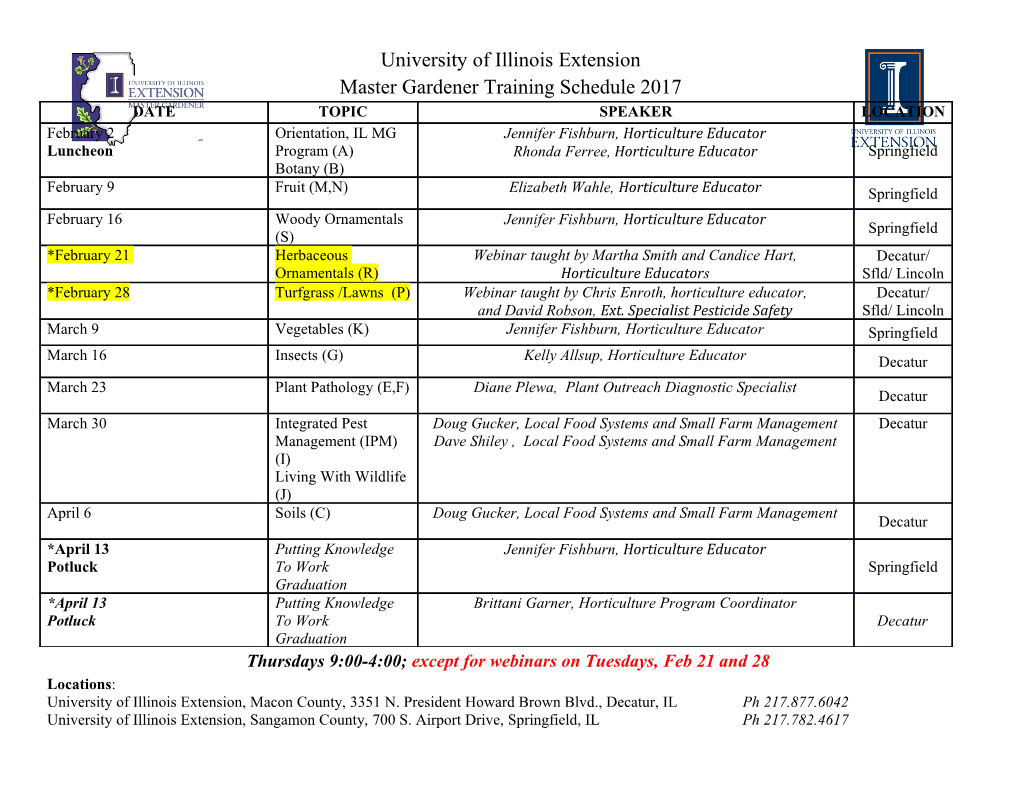
Thrust to Weight Improvement of JetCat P100-RX Turbojet Engine Thomas Coulon, Riley Johnson, Lauren Jones, Michael Mines, Grant Schumacher, and Colton Swart Mechanical & Aerospace Engineering, Oklahoma, Stillwater, 74075 The purpose of the presented design is to improve the thrust-to-weight ratio of the JetCat P100-RX small turbojet engine, a project sponsored by the Air Force Research Laboratory. This project is a year-long endeavor ending with a competition at the Wright-Patterson Air Force Base in Dayton, Ohio. The primary challenge is to increase thrust with minimal increase in weight. Several solutions were considered such as nozzle geometry optimization, exit guide vane addition, and material improvement. The final design included the optimized nozzle geometry configured with seven exit guide vanes with leading edges oriented 10-degrees into the exhaust flow. This new nozzle was additively manufactured in titanium to reduce weight and mitigate deformation from high exhaust gas temperatures. An inlet cowling of the original geometry was fabricated from foam to reduce weight. Finally, a new battery was substituted to reduce additional weight. The improved nozzle resulted in a thrust increase of 23%, and the material and battery improvements resulted in a weight reduction of 8%, leading to an overall thrust-to-weight improvement of 32%. The thrust-to-weight ratio was improved from 6.64 to 8.75. Nomenclature F = uninstalled thrust ṁ = mass flow rate of air gc = proportionality constant cp = constant pressure specific heat 훾 = specific heat ratio Pt = total pressure P = static pressure Tt = total temperature M = Mach Number 휋 = total pressure ratio 휂 = component efficiency f = fuel/air ratio I. Introduction The purpose of this year-long project, sponsored by the Air Force Research Laboratory Aerospace Propulsion Outreach Program (APOP), is to increase the JetCat P100-RX turbojet thrust-to-weight ratio. The project is a competition which includes participating student teams from more than ten universities and will conclude at Wright- Patterson Air Force Base in Dayton, Ohio. The competition will include an engine run for one minute at maximum throttle, obtaining a time-averaged thrust. The current published thrust-to-weight ratio is 9.4 (not including the battery) with a maximum reported thrust of the engine is 22 lbf. The original weight of the engine is 1080 grams. The engine is shown in Figure 1 with specifications provided by the manufacturer. Many alternatives were considered to improve 1 American Institute of Aeronautics and Astronautics thrust-to-weight ratio, while factoring in time, budget, and experience of the team. Options deemed viable were analyzed and implemented to improve engine capability. Figure 1. JetCat P100-RX Turbojet (left) and Manufacturer Specifications (right) II. Design Alternatives Design alternatives that were considered generally included: increased mass flow rate through the engine, re-design of turbomachinery, afterburner, inlet and nozzle geometries, and material selection. The uninstalled thrust equation shown below indicates that increased mass flow rate and exhaust velocity contribute to improved thrust; manipulating the identified two variables is the focus of the project. Equation 1 Figure 2. Turbojet Station Numbers1 A. Increased Fuel Mass Flow Rate By increasing the fuel mass flow rate into the combustion chamber, the overall mass flow rate of the engine would increase, which in turn increases thrust. This increase is shown in the overall thrust equation by the mdot terms on the right side of the equation: as mdot increases, thrust increases. To increase the fuel mass flow rate, the fuel pump for the engine could be reprogrammed to increase by a specified amount. However, the combustion process sets some limits on the values of the fuel to air ratio. In operation, there is a maximum burner exit temperature, Tt4, which is determined by material limits. If the engine is operated at a higher temperature than the maximum rated temperature, the burner and turbine could be damaged. Furthermore, this higher fuel-to-air ratio could quench the flame in the burner, having a detrimental effect on operability of the engine. The amount of fuel that was needed to create a significant increase in thrust was calculated and found to be too high for the combustor to hold a flame. For these reasons, increasing the fuel mass flow rate into the engine was not pursued for this design. 2 American Institute of Aeronautics and Astronautics B. Water Injection Using a spray device to inject water into the inlet of the engine, the overall mass flow rate through the engine can be increased, increasing thrust by the same method discussed in Part A. The same evaporation enthalpy will allow a higher mass flow in the intake, and thus, a higher mass flow in the combustion chamber can be achieved, resulting in more thrust. However, the fuel in the combustion chamber must also be fully evaporated for effective combustion, which takes more time and energy. If not, the flame could once again be quenched, this time due to the cooling of the flow. Lastly, the weight added from the fuel flow system and water tank would be detrimental to the thrust-to-weight ratio. C. Turbomachinery Figure 3 represents a Temperature-Entropy diagram for a turbojet engine. An increased compressor pressure ratio could be accomplished by modifying the compressor. This change could lead to an improved thermal efficiency, however, if the burner temperature does not change, this change would limit the design on the compressor, which could decrease the specific thrust. Furthermore, an increased compressor ratio would mean a change in the turbine geometry to handle the new load. For the burner, a change in the increased burner temperature would mean a change in the turbine material. These options are detrimental to time and budget. Any changes in the core of the engine have a high technical risk in terms of precision manufacturing, retaining pressure seals, and acquiring static and dynamic balancing. Figure 3. T-S Diagram D. Addition of Afterburner The fuel in a turbine engine burns in an excess amount of air, providing enough oxygen to support further combustion. Because of this effect, it is possible to inject additional fuel for burning downstream of the turbine, increasing the overall thrust of the engine. The difficulty, however, is anchoring the flame and maintaining its stability for the fuel to reignite. With the high temperatures during this process, material selection is critical due to thermal fatigue and material operating temperature limits. This new component could potentially add an undesirable amount of weight from the fuel delivery and flame holder. E. Supersonic Nozzle A supersonic nozzle could increase the exit velocity of the engine by using a converging-diverging configuration and accelerating the flow to supersonic speeds. However, an analysis is shown in Section IV using Figure 12 to illustrate why a supersonic nozzle is not possible for the JetCat P100 engine. The engine chamber pressure is not high enough to overcome the back pressure, which would be critical for reaching supersonic speeds. This low chamber pressure results from the compressor pressure ratio being a mere 2.9. The pressure ratio at the exit may not be sufficient to achieve supersonic flow. Furthermore, the turbine extracts energy from the flow exiting the combustor 3 American Institute of Aeronautics and Astronautics and then expands it to reduce the total pressure. Therefore, the combustor would also have to be modified because they are interrelated. F. Material Improvements For weight reduction, specific components of the engine were weighed. The stated weight of the entire engine from JetCat is 1080 grams. The original nozzle weighed 61 grams, the starter cap 2 grams, and the engine inlet cowling 33 grams. Options for the inlet cowling modification were removal entirely, eliminating excess material, or using a lighter material. For the nozzle, weight was not the only characteristic under consideration, but material properties as well, due to the high exhaust gas temperatures. The current nozzle is made from a steel alloy, experiencing exit gas temperatures upwards of 1300 degrees F. Figure 4 shows three materials that were considered to manufacture the nozzle, based on operating temperature ranges, densities, and cost. Figure 4. Material Properties The lightest material shown is an aluminum alloy with a density of 42.64 grams per cubic inch. However, the melting point is only 1200 degrees F, with an operability range a few hundred degrees lower. The exhaust gas temperature is too high for this material to handle. Stainless steel alloys can experience much higher temperatures, but the density is the highest of the three materials shown, resulting in the most weight. Finally, titanium not only has the highest melting point of 3100 degrees F and operating range upwards of 2800 degrees F, but the density is almost half that of stainless steel. However, the problem with this material is that titanium is almost six times more expensive than stainless steel and twice as costly as aluminum. Titanium was chosen of the three materials for its high-temperature operating range and low density. III. Parametric Cycle Analysis A. Parametric Cycle Analysis Parametric cycle analysis (PCA) is commonly used in aircraft engine design to study the thermodynamic changes of air as it moves between each component within the engine. The inputs of the real PCA performed in this analysis include engine specifications given by the manufacturer, gaseous properties of air, and assumptions about component efficiencies which are based on similar engines and an assumed level of technology. For turbojet nomenclature and the T-S diagram, see Figure 5. 4 American Institute of Aeronautics and Astronautics Figure 5. Turbojet T-S Diagram With the goal of designing a new nozzle, a PCA was performed to predict the engine’s theoretical maximum exit Mach number, and a mass flow parameter (MFP) analysis was performed to determine the optimal nozzle exit area to achieve this Mach number.
Details
-
File Typepdf
-
Upload Time-
-
Content LanguagesEnglish
-
Upload UserAnonymous/Not logged-in
-
File Pages20 Page
-
File Size-