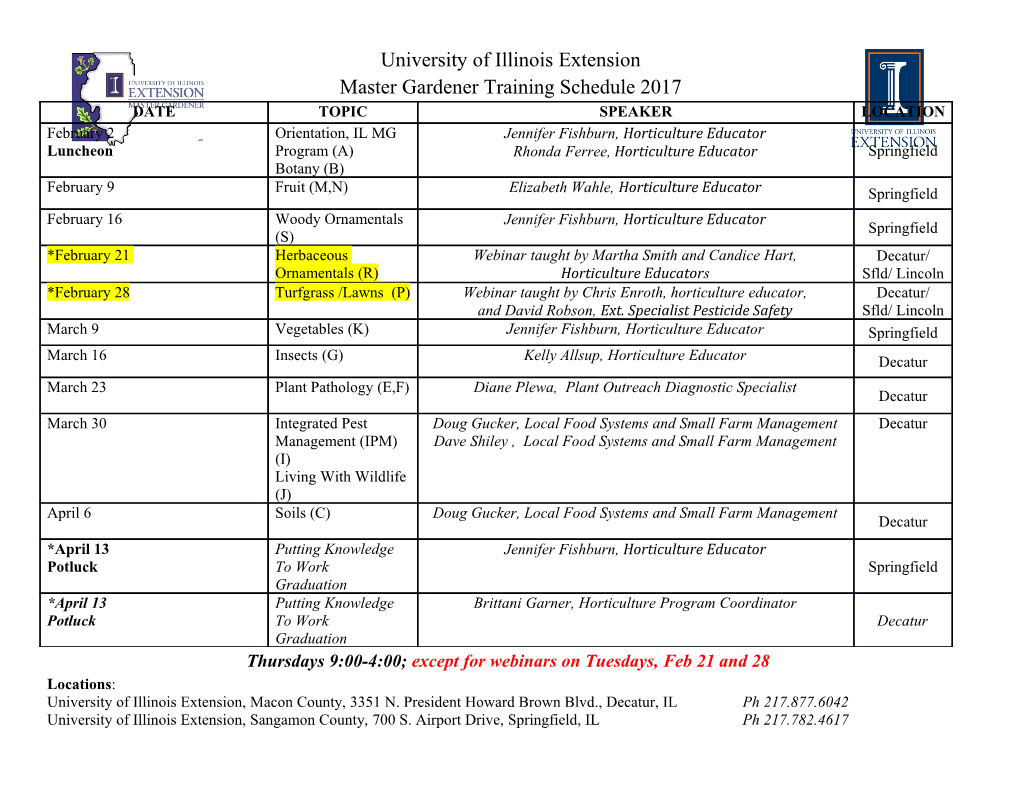
Europaisches Patentamt J European Patent Office 00 Publication number: 0 455105A2 Office europeen des brevets EUROPEAN PATENT APPLICATION © Application number: 91106522.5 © int. CIA C08F 240/00, C09J 157/02 (§) Date of filing: 23.04.91 ® Priority: 24.04.90 US 513654 © Applicant: HERCULES INCORPORATED Hercules Plaza © Date of publication of application: Wilmington Delaware 19894-0001 (US) 06.11.91 Bulletin 91/45 @ Inventor: Chu, Sung Gun © Designated Contracting States: 8 Liveoak Court BE DE ES FR GB IT NL Hockessin, Delaware 19707(US) Inventor: Daughenbaugh, Norman Edward, Jr. 68 & Highland Avenue Turtle Creek, Pennsylvania 15145(US) Inventor: Rosner, Mark Jay 705R Michigan Avenue Jeanette, Pennsylvania 15644(US) © Representative: Lederer, Franz, Dr. et al Lederer, Keller & Riederer, Patentanwalte, Lucile-Grahn-Strasse 22 W-8000 Munchen 80(DE) Light colored, aromatic-modified piperylene resins. © A tackifier resin is prepared by polymerizing a monomer mixture of 10 to 70% piperylene concentrate and 30 to 90% of a vinyl aromatic monomer in the presence of a boron trifluoride catalyst. The resin is water white in color, has a Gardner number of less than one, a softening point of 60 to 100° C and a polydispersity of 1 to 5. The tackifier is used in formulations based on EVA, block copolymers or polyolefins for hot melt and pressure sensitive adhesive applications. Lf> IA Ifl Q. Ill Rank Xerox (UK) Business Services EP 0 455 105 A2 This invention relates to tackifier resin compositions for use in adhesives and to methods for their preparation. Tackifier resins can be used for making thermoplastic adhesives such as hot melts and pressure sensitive adhesives. The adhesives are made of elastomers, block copolymers, ethylene-vinyl acetate 5 (EVA), or amorphous polyolefins along with low molecular weight oligomer tackifiers. A common tackifier is made of aliphatic petroleum hydrocarbon feed-stocks from ethylene crackers in the oil refinery, using cationic polymerization. C5 resins are commonly made from piperylene concentrates using AICI3 catalyst at 30 to 50° C. These resins have a softening point from 60 to 120° C with a Gardner color of 4 to 6. There is a need for light 10 color resins, since the dark color and poor heat stability of the C5 resins limit their use. Therefore, the hydrogenated products from aromatic petroleum resins or styrene-modified terpene resins are commonly employed for light colored adhesives. U.S. Patent No. 4,046,838 discloses a mixture of (i) an unvulcanized elastomeric block copolymer having the structure A-B-A where A is a nonelastomeric styrene block polymer and B is an elastomeric 75 diene block polymer of 1 ,3-butadiene and (ii) a tackifying resin derived from piperylene, 2-methyl-2 butene, dicyclopentadiene, and a-methylstyrene. The tackifying resin has a Gardner color of 4 to 10 and is prepared by polymerizing the monomers in the presence of an AICI3 or ethylaluminum dichloride catalyst. Thermoplastic adhesives can be prepared from elastomers such as block copolymers, oil and tackifiers. These adhesives can be prepared using solvent or hot melt techniques. Depending on the room tempera- 20 ture tackiness, thermoplastic adhesives can be divided into pressure sensitive adhesives (PSA) and hot melt adhesives. PSA are tacky at room temperature with applications as tape and label adhesives. Hot melt adhesives are not tacky at room temperature and have applications as bookbinding and box closing adhesives. Hot melt adhesives used for bonding in a particular use or application may be completely unsuitable for 25 other uses or applications. Depending upon the type of construction employed, the adhesive must possess certain physical properties. Perhaps the most stringent properties are those required for adhesives to be used in the bonding of polyethylene films to tissue or non-woven substrates in the production of disposable articles, such as diapers, sanitary napkins and bed pads. Using multi-line construction presents unique problems for the adhesive formulator. The adhesive should possess a high degree of tackiness, since it is 30 applied in the form of very fine parallel longitudinal stripes, thus requiring each line of adhesive to possess exceptionally high bonding properties. The adhesive should also possess sufficient adhesive and cohesive strength to provide high bond strength values when subjected to stress so the contructions cannot be easily separated. As an additional criteria, it is necessary that the adhesive, upon application, not be absorbed throughout the actual disposable construction and that the adhesive bonds not only remain secure but also 35 be flexible even after prolonged periods of storage. In addition to requiring heat and oxidation resistance on aging, they should also possess sufficient bonding range and should be white or clear in color. Recently, hot melt pressure sensitive technology has been developed for non-woven adhesive applica- tions, specifically for diaper adhesives. The requirements for the adhesives are stringent in that they should have good adhesion onto polyethylene and non-woven substrates. In addition, hot melt pressure sensitive 40 adhesives are currently being applied by spray techniques at 275 to 350° F (135 to 177° C), requiring good rheological properties at the melt stage. Prior to the present invention, adhesive compositions using piperylene resins as a tackifier normally had dark color and poor color and viscosity stability upon heat aging. The adhesive compositions also had unbalanced adhesive and cohesive strengths for hot melt applications. Hence, these adhesive compositions 45 had a limited use on a commercial basis. According to the invention there is provided a tackifier resin prepared from piperylene and an aromatic hydrocarbon, characterized in that it is water white in color, has a Gardner number of less than one with excellent color stability under heat, a softening point of 60 to 120° C, a weight average molecular weight (Mw) of 2,000 to 8,000, a Z average molecular weight (Mz) of 3,000 to 12,000, and a molecular weight 50 distribution (Mw/Mn) of 1 to 5. The resin is prepared from a monomer mixture consisting essentially of (a) 70 to 10% by weight of a piperylene concentrate having a boiling point of 30 to 50 °C produced from cracking of a petroleum oil fraction in a gasoline manufacturing process and having a 2-methyl-2-butene content of less than 15% by weight, and a dicyclopentadiene content of less than 5% by weight, and (b) 30 to 90% by weight of a vinyl aromatic monomer. 55 Also according to the invention, a method for preparing the tackifier resin is characterized by polymerizing at a temperature of -10 to 60 °C a mixture of (i) 70 to 10% by weight of piperylene concentrate having a boiling point of 30 to 50° C produced from the cracking of petroleum oil in a gasoline manufacturing process and having a 2-methyl-2-butene content of less than 15% by weight and a EP 0 455 105 A2 dicyclopentadiene content of less than 5%, (ii) 30 to 90% by weight of vinyl aromatic monomer, (iii) 30 to 70% by weight of an inert diluent, and (iv) a sufficient amount of BF3 to catalyze the reaction, and removing the diluent and catalyst from the reaction mixture. Also according to the invention, the tackifier resins are used in adhesive compositions comprising 5 elastomer block copolymers, amorphous polyolefins, or ethylene-vinyl acetate copolymers. The tackifying resin of this invention has a molecular weight distribution Mu/Mn of 1 to 5 with the preferred range being 1.5 to 4.5 and the most preferred range being 2.0 to 4. The glass transition temperature is -10 to 70 °C with the preferred range being 20 to 60 °C. These resins exhibit a good solubility in a wide variety of polymeric materials used in adhesive compositions. 10 In the practice of this invention, the tackifying resin can be used in hot melt adhesive and non-woven adhesive compositions. The adhesive compositions comprise block copoiymers such as styrene-isoprene- styrene (SIS), styrenebutadiene-styrene (SBS), multiblock (SB)n where n is 100 to 1,000, or amorphous polyolefins and ethylene-vinyl acetate (EVA), plus the tackifier. The tackifier offers excellent tack, high shear strength, and unique solubility. The new resins are excellent tackifiers in STEREON 840A as well as in SBS 75 (KRATON 1102) and SIS (KRATON 1107) systems, since they exhibit good compatibility with the butadiene and isoprene domains of the block copolymers. The tackifiers are suitable for use in SBS, (SB)n and SIS systems for disposable products, and for pressure sensitive adhesive tapes. In addition, they can be used in hot melt EVA systems with a vinyl acetate content of 20 to 40%, e.g., in hot melt packaging adhesives, because the tackifiers offer light color, heat stability and an excellent balance in cohesive and adhesive 20 strengths. Various aliphatic and aromatic hydrocarbon diluents can be used to prepare the tackifying resin of this invention. Representative examples of such aromatic hydrocarbons are toluene and benzene; and repre- sentative examples of aliphatic hydrocarbons are pentane, hexane, heptane and octane. A particularly suitable hydrocarbon solvent is a mixture containing from 10 to 90 parts of toluene and from 90 to 10 parts 25 of hexane. The feed material used to produce the tackifier resin of the present invention is a hydrocarbon feed material having five carbons atoms. The preferred hydrocarbon feed material is a piperylene concentrate that is a mixture of an organic fraction produced from the cracking of petroleum oil in a gasoline manufacturing process. The primary constituents of this feed stream are the cis and trans isomers of 30 piperylene. In addition to the piperylene, C5 monomers such as methylbutenes and pentenes (both linear and cyclic) are present.
Details
-
File Typepdf
-
Upload Time-
-
Content LanguagesEnglish
-
Upload UserAnonymous/Not logged-in
-
File Pages17 Page
-
File Size-