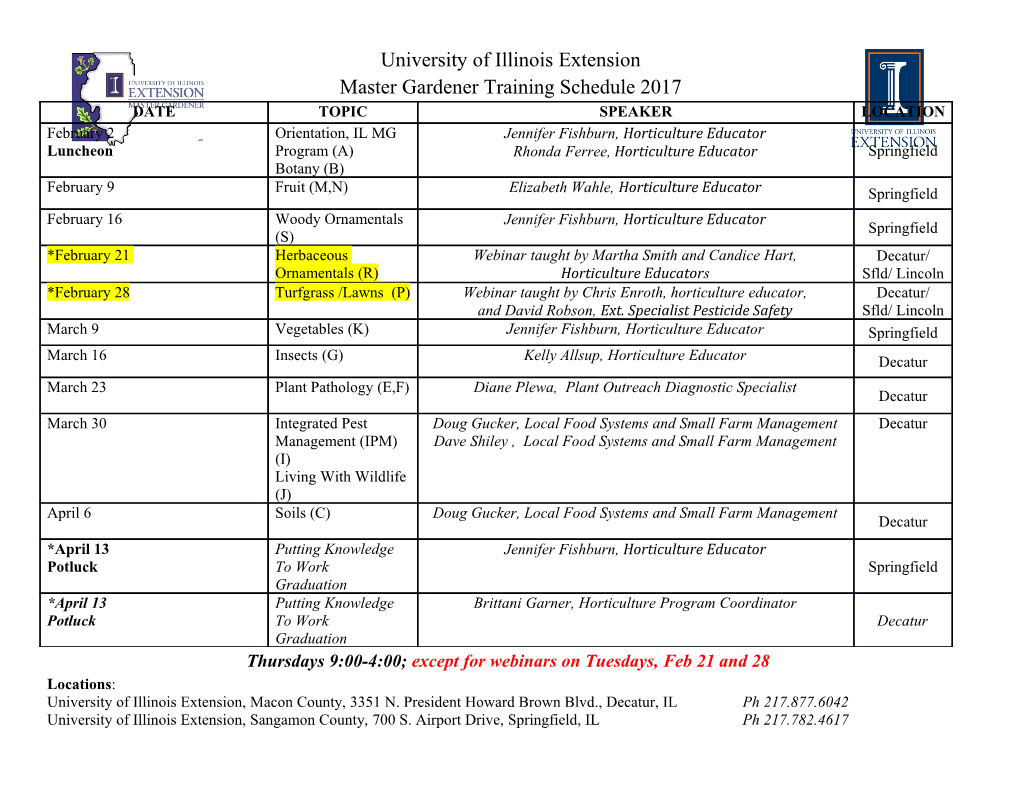
https://ntrs.nasa.gov/search.jsp?R=19940032314 2020-06-16T10:53:31+00:00Z NASA Technical Memorandum 4555 June 1994 Review of Advanced Radiator Technologies for Spacecraft Power Systems and Space Thermal Control Albert J. Juhasz and George P. Peterson National Aeronautics and Space Administration NASA Technical Memorandum 4555 1994 Review of Advanced Radiator Technologies for Spacecraft Power Systems and Space Thermal Control Albert J. Juhasz Lewis Research Center Cleveland, Ohio and George P. Peterson Texas A&M University College Station, Texas National Aeronautics and Space Administration Office of Management Scientific and Technical Information Program Trade names or manufacturers' names are used in this report for identification only. This usage does not constitute an official endorsement, either expressed or implied, by the National Aeronautics and Space Administration. REVIEW OF ADVANCED RADIATOR TECHNOLOGIES FOR SPACECRAFT POWER SYSTEMS AND SPACE THERMAL CONTROL Albert J. Juhasz Lewis Research Center Cleveland, Ohio and George P. Peterson Texas A&M University College Station, Texas Summary Introduction The thermal management of manned spacecraft traditionally The traditional means for rejecting heat from manned space- has relied primarily on pumped, single-phase liquid systems to craft are heat-rejection systems composed of single-phase fluid collect, transport, and reject heat via single-phase radiators. loops (Peterson 1987). These single-phase fluid loops use a Although these systems have performed with excellent reliabil- mechanically pumped coolant to transfer heat from the habita- ity, evolving space platforms and space-based power systems tion portion of the spacecraft to the radiators where it is rejected will require lighter, more flexible thermal management sys- to the space environment. Although these systems have per- tems because of the long mission duration, large quantities formed with excellent reliability in the past, evolving space of power system cycle reject heat, and variety of payloads platforms and space-based power systems will require more involved. The radiators are critical elements in these thermal flexible thermal management systems because of the multiyear management systems. This report presents a two-part overview mission durations, large quantities of heat to be rejected, long of progress achieved in space radiator technologies during the physical distances, and large variety of payloads and missions eighties and early nineties. Part I contains a review and com- that must be accommodated (Mertesdorf et al. 1987). parison of the innovative heat-rejection system concepts pro- In general, space thermal management systems, whether posed during the past decade, some of which have undergone serving life support or future space power systems, consist of preliminary development to the breadboard demonstration three separate subsystems: stage. Included are space-constructable radiators with heat (1) A heat acquisition subsystem that collects heat from pipes, variable-surface-area radiators, rotating solid radiators, the various payload or power system heat-rejection moving-belt radiators, rotating film radiators, liquid droplet interfaces radiators, Curie point radiators, and rotating bubble-membrane (2) A heat transport subsystem that transports heat from radiators. the acquisition sites to the radiating surfaces Part II contains a summary of a multielement project effort, including focused hardware development under the Civil Space (3) A heat-rejection subsystem composed of radiating sur- Technology Initiative (CSTI) High Capacity Power program. faces that form the space radiator A key project under this program carried out by the NASA An example of a typical space thermal management system Lewis Research Center and its contractors was the develop- proposed for large space platforms, namely a two-phase heat- ment of lightweight space radiators applicable to the Space rejection system consisting of the subsystems listed above, was Exploration Initiative (SEI) power systems technologies. Prin- presented by Edelstein (1987). These three subsystems com- cipal project elements include both contracted and in-house prise a thermal utility that would employ the high latent heat of efforts conducted in a synergistic environment designed to a working fluid to transport heat from its acquisition sources to facilitate accomplishment of project objectives. The contracts the radiators, where it would be rejected by radiation to the with Space Power Inc. (SPI) and Rockwell International are particular space environment. aimed at development of advanced radiator concepts, whereas The last of the three subsystems, the radiators, are critical the in-house work has been guiding and supporting the overall components of virtually all proposed space-borne installations. program with system integration studies, heat pipe testing, In most current designs, the radiator is composed of an array of analytical code development, radiating surface emissivity tubes or tube-fin structures through which liquid coolant is enhancement, and composite materials research to develop circulated. The tube wall must be sufficiently thick to minimize and analyze lightweight, high-conductivity fins. These tasks micrometeoroid penetration. As a result, the radiator mass are key prerequisites in the effort to reduce specific mass of could comprise as much as half of the total system mass (Juhasz space radiators. and Jones 1987). The technical challenges associated with the development of Part I.—Innovative Radiator heat-rejection systems capable of meeting future requirements have been described previously (Ellis 1989). Presented here is Technologies a review and comparison of the heat-rejection systems that have been proposed for development for space platforms and space- Space-Constructable Heat Pipe Radiator based power systems. The first part discusses innovative concepts that have under- The heat-rejection system presently used on the space shuttle gone only limited development but are documented for poten- orbiters consists of over 250 small, parallel tubes embedded tial future consideration. These include space-constructable within a honeycomb structure. Warm, single-phase Freon from radiators, variable-surface-area radiators, rotating solid the heat collection and transport circuit is circulated through radiators, moving radiators, and rotating bubble-membrane these tubes (fig. 1). Heat is transferred from the coolant by radiators. convection to the tube walls, conduction through the honey- The second part contains a summary of a multielement comb structure, and finally, radiation to space. Application of project effort including focused hardware development under this technology to the station heat-rejection subsystem would the CSTI High Capacity Power program carried out by the require over 750 interconnected tubes. Moreover, if only a NASA Lewis Research Center and its contractors for the single redundant loop were used, a puncture in any single tube purpose of lightweight space radiator development in support could disable the entire system, making this type of system of Space Exploration Initiative (SEI) power systems technol- infeasible for long-tetra missions. ogy. Principal project elements include both contracted and in- A space-constructable radiator (SCR), composed of a series house efforts conducted in a synergistic environment designed of individually sealed heat pipe elements similar to that shown to facilitate accomplishment of project objectives. The con- in figure 2, has been proposed (Ellis 1989), and several advan- tracts with Space Power Inc. (SPI) and Rockwell International tages of this type of system over pumped single-phase fluid are aimed at development of advanced radiator concepts, loops have been identified. These advantages include a signifi- whereas the in-house work has been guiding and supporting the cant reduction in weight due to the reduction in fluid inventory, overall program with system integration studies, heat pipe increased heat-rejection capacity due to the uniform tempera- testing, analytical code development, radiating surface emis- ture of the radiating surface, and increased reliability, because sivity enhancement, and composite materials research aimed at penetration by a single micrometeoroid or piece of space debris development and analysis of lightweight, high-conductivity, would result in the failure of only a single heat pipe element and high-emissivity fins. These tasks are considered to be key therefore cause only a slight degradation in performance. prerequisites in the effort to reduce specific mass of space High-capacity, SCR elements have been investigated in radiators. several shuttle flight experiments, including the STS-3 flight Shuttle-Type State-of-the-Art Space Station High-Capacity Radiators Heat Pipe Radiator Heat Pipe Radiators /--Heat transfer 32 °C 32 °C (90 °F) 4.5 °C (40 °F) / contact surface 4.5 °C (40F °F • Fluid must be pumped over • Fluid needs to be pumped • Two-phase fluid interfaces radiator entire radiator area only through radiator manifold only at manifold • Over 250 parallel tubes • Less than 75 heat pipes • Only 50 heat pipes required for required for 25-kW station required for shuttle type system 75-kW station • Puncture of any tube destroys • Heat pipes independent of • Heat pipes independent of each other radiator each other; a puncture of one tube only reduces • Contact heat exchanger allows on- efficiency orbit assembly and repair of radiator
Details
-
File Typepdf
-
Upload Time-
-
Content LanguagesEnglish
-
Upload UserAnonymous/Not logged-in
-
File Pages26 Page
-
File Size-