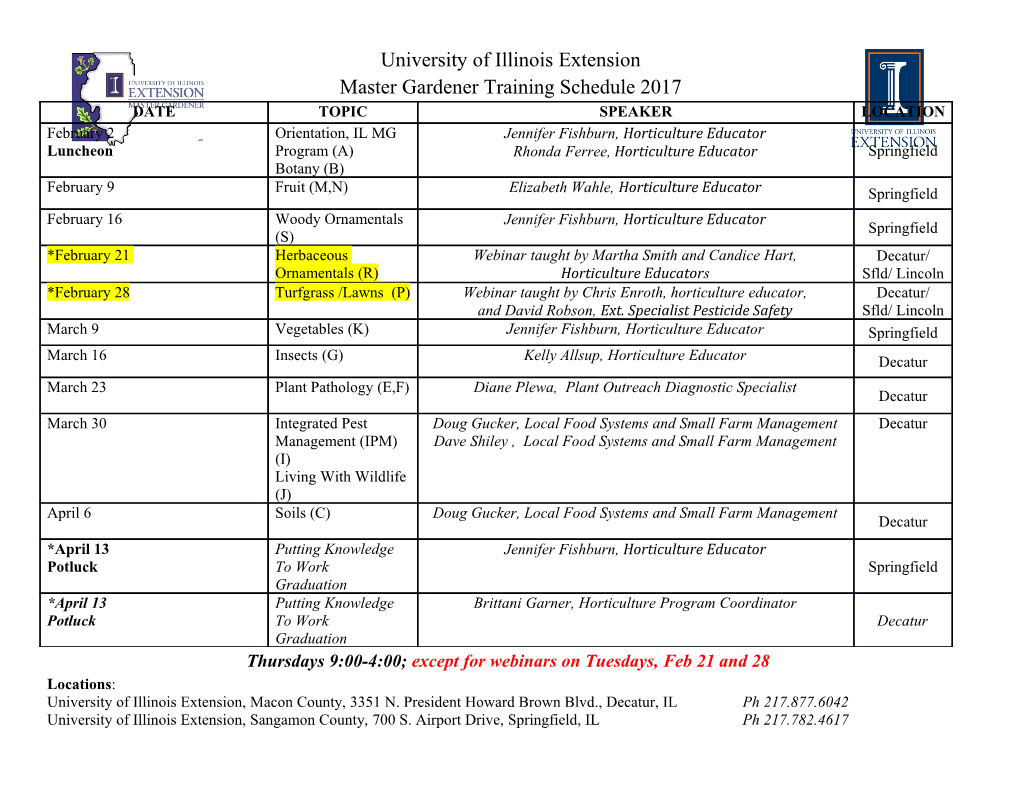
SSRG International Journal of Electronics and Communication Engineering (SSRG - IJECE) – Special Issue ICETST Nov 2018 Power Loom Control using PIC18F4620 Sundarraj R, Mr.A Arunraja, M.E., Student, Assistant Professor Department of Electronics and Communication Engineering, Sri Ramakrishna Engineering College, Coimbatore. Abstract This paper proposes an the process to decrease manufacturer is in a better position to pay more for the man power and the concept of an automation is to new machinery. provide a simulation test in a microcontroller based The major problem faced in textile industry system to be embedded in weaving machine for is that the fabric gets damaged when the thread gets Monitoring and controlling the design operation. cut. This leads to produce damaged fabric which case Power loom automation replace conventional unwanted production. The proposed system is mechanical methods as a forward step in embedded designed in such a way that the machine is stop and systems for industrial automation and mechatronics prevented from damages. It uses PIC18F4620 as the applications. The proposed embedded system aimed main controlling unit. The LCD, Shuttle sensor, Warp to read the design parameters entered by the designer sensor and Relay are interfaced with the using calculate the productions of loom, generate the microcontroller. design in sequences of binary digits and apply the The shuttle sensor and warp sensor gives the design on the machine with machine status status of thread condition and given to the consideration. Peripheral Interface Controller (PIC) microcontroller unit as input. The control unit shut microcontroller, pin needle, Liquid Crystal Display down the machine through relay switching unit. (LCD), relays, sensors and switches are used for The shuttle and warp sensor status are system programming in C language and Proteus displayed in the LCD screen and monitored message electronics simulation environment. is also displayed on the screen. Keywords - PIC18F4620, relay, LCD, motor, shuttle II. PEER REVIEW sensor, weft sensor, proximity sensor. Now-a-days the use of textile fabric is prominent. Choosing the fabric according to the quality is a I. INTRODUCTION challenging task. Monitoring the weaving machine by the manual method is difficult if the unit of The layers of warp yarn, and each pick of weft production machine count is high. (Wang lei et al - beaten up into the cloth after each (one after the 2009). Control system based position and Power other) passage of the shuttle across the fabric-making loom control is monitored. Using genetic techniques machine. Is cloth still to be woven this way during the Power loom is controlled. the next hundred years and after, or will some other Gorbunov Vladimir et al (2017) have method replace the history of weaving shows that describes the method of automated monitoring of man's clever genius has been working continuously weaving loom quality product. The density of the on the problem of producing a woven fabric, and material produced is determined by the fabric there are definite cycles during which certain ideas structure. The vision system consists of a web camera are reawakened and brought to the front and seen as and a micro-computer and allows to determine the something completely new. There are not enough geometric dimensions of the intervals between the weavers in the industry, and the in-take of new basic yarns of the fabric. The management of these recruits is not enough. Wages in the fabric industry dimensions provides an opportunity to control the have changed a great deal since the war and this has density of the manufactured fabric. The described increased the wages of the weaving (related to system makes it possible to automate the quality surgery). Manufacturers are getting a very much control of the loom. better price for the cloth which they produce, and M. W. Burton and J.S. Culver (2015) have although we are supposed to be approaching a (prices developing specialized carpet weaving machines. are low and there are a lot of things for sale), these Brinton’s machines are developed in-house because prices will probably hold for some time. The chief machines from other suppliers are not capable of results of these three reasons for increased interest are meeting our requirements and are, in general, less that it becomes very important for one (related to technologically advanced. Brinton’s have recently surgery) to pay attention to take care of more completed a prototype of a 5m wide face-to-face machines in order to maintain volume of output it is Wilton Loom which has been designed to increase very important on account of higher wages that each productivity by up to 100% compared to the existing worker agent should produce more fabric, and lastly, 12 ft. machine. This has required a radical change in because cloth is selling at a better price, the ISSN: 2348 – 8549 http://www.internationaljournalssrg.org Page 31 SSRG International Journal of Electronics and Communication Engineering (SSRG - IJECE) – Special Issue ICETST Nov 2018 the design philosophy, both to allow the productivity this paper, we compare all considered encoding improvement and to minimize machine tuning. Axes schemes by means of examples, which illustrate their are powered by DC servo motors and are controlled distance properties. The above mentioned papers reveal using a Euro herm FMC controller. about the concept of controlling the motor for various Kunal Joardr and D. Raviv (1995) have applications. In all the above mentioned papers only proposed visual looming is related to an increased the shutdown of the machine is taken as a parameter to projected size of an object on a viewer's retina as the control the power loom machine which reduces the relative distance between the viewer and the object man power of the system and focused on the fabric. In decreases. Psychologists have reported about subjects the proposed system the main motor is shut down when avoiding collision using this information by reacting thread gets cut, and monitor the fabric production. The defensively. In this paper we present a quantitative proposed system uses PIC18F4620 as the controlling approach to visual looming and describe a novel unit. Shuttle sensor is interfaced with the digital port of method to measure this visual cue using visual the controller which provides the status of thread in fixation and studying the relative change in irradiance power loom machine. LCD is used to display the in the image. This visual cue can be used in the sense message. of a threat of collision for autonomous obstacle III. HARDWARE DESCRIPTION avoidance. This project proposes an embedded system for Michael bailey and van kuren (2002) Power loom Control. The proposed system mainly Automation can be used to supplement the manual concentrates on monitoring the thread condition on processing of used electronic products in order to both vertical and horizontal bunch of thread. offset the increasing volumes in electronic waste Depending on the condition of thread in the power streams. The application of automation to loom weaving machine get shut down. This chapter demanufacturing requires high levels of flexibility. In deals with the Block diagram of the project and order to study the utility of automation for details of each hardware component chosen in such a demanufacturing of used products, a flexible cover way that it suits best for the design of the proposed removal process was implemented within an automated system. demanufacturing work cell. The process demonstrates two of the key objectives in automated processing of A. Block Diagram used products: feature identification and connection Figure 1 shows the block diagram of Power removal. The study is limited to threaded connections loom Control. PIC18F4620 is the main controlling that can be detected on the external surface of the unit of the proposed system. The shuttle sensor & product. Feature detection is performed through the use warp sensor gets the vertical and horizontal cross of stereo machine vision with a simple search thread status and is fed as input to the PIC algorithm. Once a positive feature is discovered, a microcontroller unit. The proximity sensor gets the material removal approach is used to eliminate the quantity of fabric and is fed as digital input to the threaded connections. A flexible material removal micro controller unit. LCD will display the status of platform has been established with on hand tooling thread and machine shutdown message. When mounted to a 6 DOF industrial robot. Experiments reached the maximum quantity of fabric the identified key issues in the recognition and removal proximity sensor giver output to the controller unit process. Constraints to the range of product that can be and shut down the machine by switched on the relay. processed are identified based on feature recognition When the shuttle sensor and warp sensor gives the and material cutting limits. Product design output to the controller unit and shut down the considerations for automated demanufacturing are machine. presented. Jürgen Freudenberger et al (2001) have proposed convolutional and block encoding schemes which are variations of woven codes with outer warp. We propose methods to evaluate the distance characteristics of the considered codes on the basis of the active distances of the component codes. With this analytical bounding technique, we derived lower bounds on the minimum (or free) distance of woven convolutional codes, woven block codes, serially concatenated codes, and woven turbo codes. Next, we show that the lower bound on the minimum distance can be improved if we use designed interleaving with unique permutation functions in each row of the warp of the woven encoder. Finally, with the help of simulations, we get upper bounds on the minimum distance for some particular codes and then investigate their performance in the Gaussian channel.
Details
-
File Typepdf
-
Upload Time-
-
Content LanguagesEnglish
-
Upload UserAnonymous/Not logged-in
-
File Pages4 Page
-
File Size-