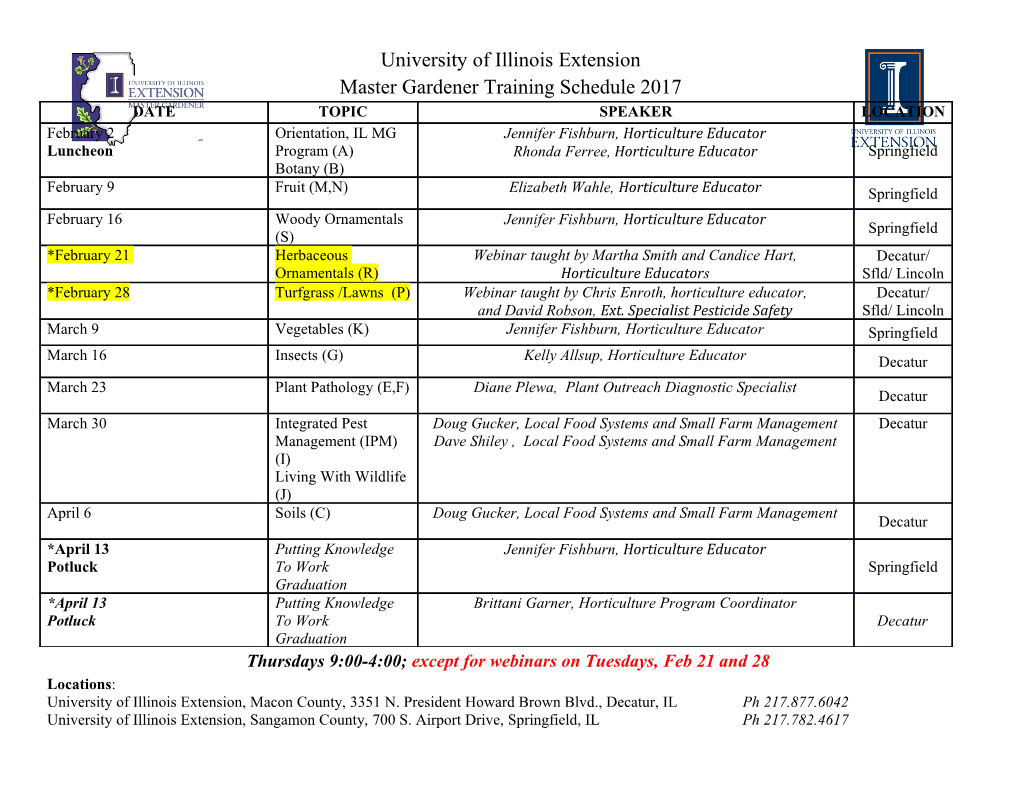
materials Article Optimization of the Iron Ore Direct Reduction Process through Multiscale Process Modeling Rami Béchara 1,2, Hamzeh Hamadeh 1,2, Olivier Mirgaux 1,2 and Fabrice Patisson 1,2,* ID 1 Institut Jean Lamour, CNRS, Université de Lorraine, 54011 Nancy, France; [email protected] (R.B.); [email protected] (H.H.); [email protected] (O.M.) 2 Laboratory of Excellence on Design of Alloy Metals for Low-Mass Structures (DAMAS), Université de Lorraine, 57073 Metz, France * Correspondence: [email protected]; Tel.: +33-372-742-670 Received: 29 May 2018; Accepted: 20 June 2018; Published: 27 June 2018 Abstract: Iron ore direct reduction is an attractive alternative steelmaking process in the context of greenhouse gas mitigation. To simulate the process and explore possible optimization, we developed a systemic, multiscale process model. The reduction of the iron ore pellets is described using a specific grain model, reflecting the transformations from hematite to iron. The shaft furnace is modeled as a set of interconnected one-dimensional zones into which the principal chemical reactions (3-step reduction, methane reforming, Boudouard and water gas shift) are accounted for with their kinetics. The previous models are finally integrated in a global, plant-scale, model using the Aspen Plus software. The reformer, scrubber, and heat exchanger are included. Results at the shaft furnace scale enlighten the role of the different zones according to the physico-chemical phenomena occurring. At the plant scale, we demonstrate the capabilities of the model to investigate new operating conditions leading to lower CO2 emissions. Keywords: ironmaking; direct reduction; iron ore; DRI; shaft furnace; mathematical model; simulation; CO2 emissions 1. Introduction Steel is one of the key materials of today’s industrial world. Moreover, its production is characterized by high energy consumption along with important carbon dioxide emissions. World steel production amounts to 6% of anthropogenic CO2 emissions [1]. Beside the current reference steelmaking route (integrated plant with sinter and coke making, blast furnace, and basic oxygen furnace), less CO2 emitting alternative routes are attracting greater interest. Direct reduction (DR) in a shaft furnace followed by electric arc steelmaking thus results in 40 to 60% lower CO2 emissions compared with the reference route [2]. Direct reduction converts solid iron ore pellets into so-called direct reduced iron (DRI), using a mixture of CO and H2 produced by reforming natural gas. Due to independence from coke and coal imports, sizeable units to meet demand, reduced investment costs, and reduced construction time [3], direct reduction units are becoming more numerous, particularly in countries where natural gas is cheap and abundant. These advantages have spurred increased research activity, namely in modeling and simulation, in order to correctly evaluate these processes and ultimately optimize them. The present work contributes to this effort with the key objective to provide an accurate simulation of the whole DR process, enabling us to propose new avenues for CO2 emission mitigation. A distinctive feature of our approach is the multiscale nature of modeling, from, say, 1 µm (grain size) to 1 hm (plant size). We thus developed a single pellet model, a shaft Materials 2018, 11, 1094; doi:10.3390/ma11071094 www.mdpi.com/journal/materials Materials 2018, 11, 1094 2 of 18 Materials 2018, 11, x FOR PEER REVIEW 2 of 18 furnacemodel, model,and a plant and a plantmodel, model, using using different different and and complementary complementary modeling modeling strategies. strategies. These These are presented in the next sections, togethertogether withwith referencesreferences toto previousprevious works.works. 2. Single Pel Pelletlet Model Iron oreore pellets pellets (roughly (roughly spherical, spherical, typically typically 7–15 mm7–15 diameter)mm diameter) for DR arefor industriallyDR are industrially produced fromproduced natural from hematite natural grains hematite (irregular, grains typically (irregular, 20 µtypicallym). In a shaft20 µm). furnace, In a shaft these furnace, pellets are these chemically pellets ◦ reducedare chemically at 600–950 reducedC byat 6 both00–950 CO °C and by Hboth2 in CO three and steps, H2 in hematite three steps, Fe2O hematite3 −! magnetite Fe2O3 ⟶ Femagnetite3O4 −! wustiteFe3O4 ⟶ Fe wustite0.95O −! Fe0.95ironO ⟶ Fe, iron thus Fe, thus involving involving six gas-solidsix gas-solid reactions reactions at at the the grain grain scale. scale. Numerous models for gas-solidgas-solid reactions are available in the literature, from the simplest unreacted shrinking core model to pore models and grain modelsmodels (Figure(Figure1 1))[ [4]4].. The grain model matchesmatches well the grainy structure ofof thethe DRDR pellets;pellets; however,however, itit was was not not used used as as such such in in the the current current study study because because it it requires requires a numericala numerical solution solution of of the the diffusion-reaction diffusion-reaction equations, equations, which whichis is incompatibleincompatible forfor computationcomputation time reasons because of its integration in a multi-particlemulti-particle reactor model (next(next section).section). Instead, we used an alternate approach, the additive reaction times law, whichwhich givesgives anan approximateapproximate analytical solution to calculatecalculate the reactionreaction ratesrates andand cancan accountaccount forfor mixedmixed regimesregimes [[5].5]. According to experimentalexperimental observations, wewe also also introduced introduced an an evolution evolution of grainof grain and poreand structurepore structure with the with reactions the reactions as follows: as thefollows: hematite the grainshematite become grains covered become with covered small poreswith aftersmall conversion pores after to conversion magnetite and to magnetite wustite. At and the wustitewustite. stage,At the the wustite pores stage, enlarge the and pores the wustiteenlarge grainsand the break wustite down grains into break smaller down particles into smaller termed “crystallites”.particles termed These “crystallites”. subsequently These grow subsequently (typically fromgrow 1 (typically to 10 µm) from and join1 to 10 to formµm) and the join molten-like to form structurethe molten of-like sponge structure iron (another of sponge name iron for (another DRI). These name changes for DRI) of. Thes coursee changes influence of the course kinetics influence of the transformation,the kinetics of the mostly transformation, via the diffusion mostly resistances. via the diffusion Details of resistances. the single pelletDetails model of the used single and pellet of its resultsmodel used are given and of in its [6, 7results]. are given in [6,7]. (a) Figure 1. EvolutionEvolution of of pellet pellet structure structure along along with with reaction: reaction: (a) (Unreaca) Unreactedted Shrinking Shrinking Core Core Model Model;; (b) (Grainb) Grain Model. Model. The The porous porous structure structure evolution evolution (b ()b was) was determined determined from from experimental experimental observations observations [7]. [7]. 3. Shaft Furnace Model gas reactants CO and H2 3.1. Previous WorksWorks The shaft furnace ( (FigureFigure 22)) isis thethe corecore ofof thethe DRDR process.process. IronIron oreore pelletspellets areare chargedcharged atat thethe top,top, gas film descend due due to to gravity gravity,, and and encounter encounter an an upward upward counter counter-flow-flow of ofgas. gas. The The red reducingucing gas gas (CO (CO and and H2, ◦ Hplus2, plus CH4 CH, CO4,2, CO and2, andH2O, H at2O, about at about 950 °C) 950 is C)injected is injected peripherally peripherally at mid at- mid-heightheight and exit ands exitsat the at top. the Fe top.In the In lower the lower section section of the of furnace, the furnace, of conical of conical shape, shape, cold natural cold natural gas is injected gas is injected to cool tothe cool iron the pellets iron pelletsproduced. produced. The upper The section upper section(reducing (reducing zone and zone intermediate and intermediate zone) is zone) cylindrical is cylindrical (typically (typically height FeO 15 m; diameter 5 m). Two processes, MIDREX and HYL-ENERGIRON, share most of the DR market. Fe3O4 FeF2EO3 Diffusion in and out through the gas film gas products CO2 and H2O Materials 2018, 11, 1094 3 of 18 Materials 2018, 11, x FOR PEER REVIEW 3 of 18 height 15 m; diameter 5 m). Two processes, MIDREX and HYL-ENERGIRON, share most of the DR market.Their shaft Their furnace shafts furnaces exhibit exhibitsome differences some differences (mostly (mostly in gas incomposition gas composition and pressure, and pressure, size, size,and andinternal internal equipment equipment details) details) but the butir their basic basic characteristics characteristics are similar. are similar. Pellets Top gas Reduction zone Reducing gas Cooling gas Cooling zone Cooling gas Figure 2. Schematic layout of a direct reduction shaft furnace. ReflectingReflecting the greatgreat effort put in the simulation and development of the DR DR processes, processes, numerous numerous mathematical andand numerical numerical models models of the of shaft the furnaceshaft furnace were published, were published differing, by differing the assumptions, by the theassumptions, physico-chemical the physico phenomena-chemical accountedphenomena for, accounted
Details
-
File Typepdf
-
Upload Time-
-
Content LanguagesEnglish
-
Upload UserAnonymous/Not logged-in
-
File Pages18 Page
-
File Size-