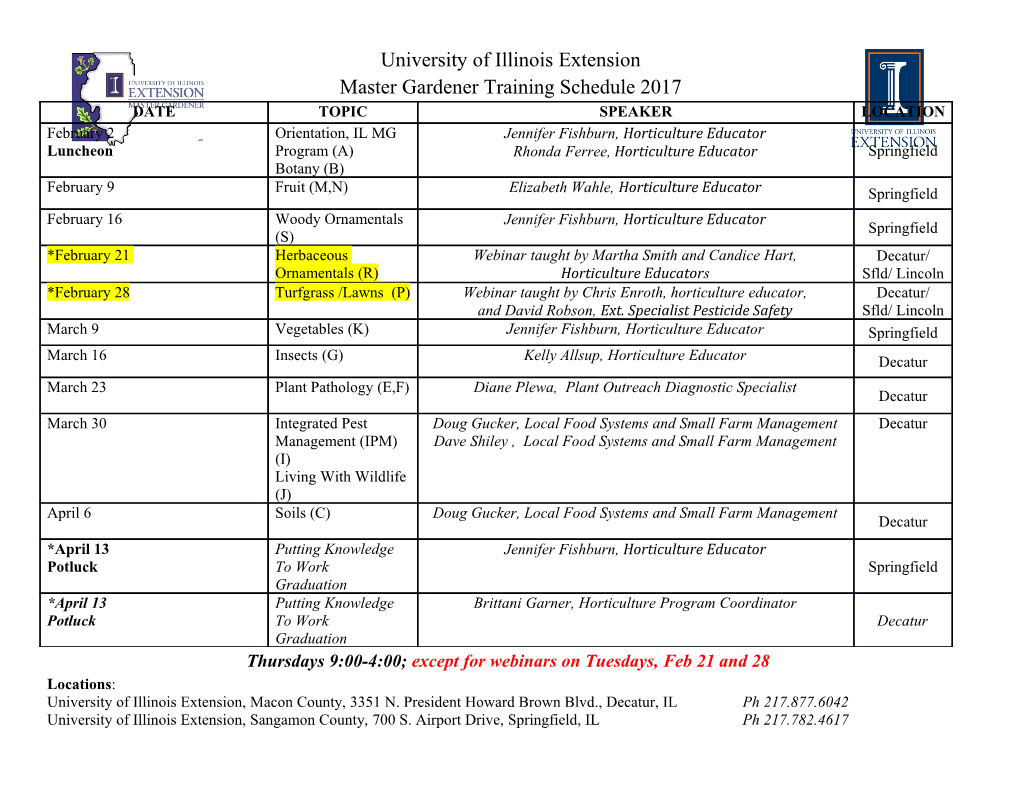
Mechanical Properties of HSLA Steel Buried Gas Tungsten Arc Weldments Thick-section A 710 steel was successfully welded without edge preparation or the use of filler metal BY VV. E. LUKENS ABSTRACT. The possibility of welding Introduction cation of this process to steel welding. ASTM A710 Grade A Class 3 high- Shtrikman (Ref. 5) investigated the possi­ strength low-alloy steel (HSLA-80) up to The welding processes extensively bility of welding Types VNS2 and 19 mm (0.75 in.) thick by the buried gas used for joining thick-walled components 30KhGSA steels up to 22.1 mm (0.87 in.) tungsten arc process has been investi­ such as forgings, pressed or spun-end in thickness by the buried GTAW pro­ gated. This process eliminates edge prep­ closures, shapes, castings, and plate nec­ cess. The 30KhGSA is a medium-alloy aration, reduces the number of passes essitate edge preparation with a large steel, and the VNS2 is a heat-resistant required, eliminates the need for filler included angle (45 to 60 deg) (Ref. 1). stainless steel containing age-hardenable metal wire, and reduces the total heat Research and development work aimed martensite (Ref. 6). Acceptable weld input per unit length of finished weld­ at eliminating edge preparation is current­ fusion zone and heat-affected zone ment, when compared to standard indus­ ly under way in the area of narrow (HAZ) properties were obtained in the try processes, such as submerged arc groove joints (Ref. 2). Another method to 30KhGSA steel and the VNS2 steel after a welding. eliminate edge preparation is to weld postweld heat treatment. In 1982, anoth­ Two gas tungsten arc weldments were with a nonconsumable electrode and er Soviet article (Ref. 7) stated that this fabricated with ASTM A710 high-strength with the arc immersed. This method is process was used extensively in Soviet low-alloy steel as autogenous square- known as the buried gas tungsten arc industry in the welding of various metals groove welds. Forced convective cooling welding process. because the welding equipment is simple, by gas impingement on the weld bead The use of this process was first it is possible to weld large components, surface was used on one of the weld­ reported (Ref. 3) by the Soviets in 1964, and requirements on the variation of the ments to enhance the cooling rate of this where results were given concerning welding root opening are not stringent. high heat input process. The mechanical research into the buried GTAW of titani­ Because of the high potential for pro­ properties and microstructure of these um alloys. Butt joint weldments in 25.4- duction welding cost reduction by the weldments were evaluated. mm (1-in.) thick plate were fabricated in buried GTAW process through elimina­ The results of microstructure observa­ only four passes without any edge prep­ tion of edge preparation, reduction in the tions and mechanical testing indicate that aration. In the following year, an investi­ number of passes required, elimination of ASTM A710 can be successfully welded gator from the United States reported the need for filler metal, and reduction in by the autogenous buried gas tungsten (Ref. 4) the use of this process for weld­ the total heat input per unit length of arc process. The mechanical properties ing aluminum. Butt joint weldments in finished weldment, this process could be of the A710 autogenous welds fabricated 31.8-mm (114-in.) thick plate were fabri­ competitive with submerged arc welding with and without convective cooling of cated in only two autogenous passes (SAW) for application to high-strength the weld bead surface were similar to without any edge preparation. Liptak steels. This paper presents an analysis of base plate properties, except for slightly reported (Ref. 4) that the greatest single the benefits and feasibility of the process, lower weld metal yield strength. The cost advantage arose from the elimina­ the development of welding variables, weld Charpy V-notch energy values tion of filler metal. and the mechanical properties of buried ranged widely, but the higher values There are few references to the appli- GTAW weldments in ASTM A710 Grade were close to those of the base plate, A Class 3 high-strength low-alloy (HSLA- except at — 51 °C (—60°F), where they 80) steel. were lower. The ASTM A710 weldment KEY WORDS produced with convective cooling to Materials and Procedures enhance the cooling rate had higher Buried GTA Weldments Charpy V-notch energy values than the Forced Convection The material selected for this investiga­ weldment produced without convective Convective Cooling tion was ASTM A710 Grade A Class 3 cooling. Gas Impingement high-strength low-alloy steel with the fol­ Immersed GTAW Arc lowing analysis in wt-%: carbon —0.05, Buried Autog GTAW manganese — 0.51, phosphorus - 0.004, W. E LUKENS is with the David Taylor ASTM 710 HSLA Steel sulfur-0.008, silicon-0.34, nickel- Research and Development Center, Bethesda, Low Arc Voltage GTAW 0.95, chromium —0.66, molybdenum — Md. Autogenous GTA Welds 0.21, copper-1.25, columbium-0.040, Paper presented at the 67th Annual AWS NDT Inspectn Results aluminum —0.037, and nitrogen —0.009, Meeting, held April 13-18, 1986, in Atlanta, with iron as the balance. Ga. All plates were 19 mm (0.75 in.) thick WELDING RESEARCH SUPPLEMENT | 215-s Weldment Characterization Procedures Following welding, the weldments were magnetic particle inspected to determine surface defects, such as crack­ ing, and radiographed to determine inter­ nal defects, such as porosity and/or cracking. The buried GTA weldments were opti­ cally examined for microstructure. The microstructure examination included the base plate material, the HAZ, and the fusion zone. Chemical analysis was per­ formed on the fusion zone. Microhard­ ness tests were made on transverse cross-sections of the weld 6.4 mm (VA in.) from the surface of the second side, and also from surface to surface through thickness along the weld centerline. The mechanical properties of these weldments were evaluated. The mechan­ ical properties included yield strength, ultimate tensile strength, elongation, reduction of area, and fracture tough­ Fig. 1 — Plate assembly prior to buried gas tungsten arc welding ness. The fracture toughness of the welds was determined by the Charpy V-notch (CVN) impact test. The CVN tests were and were cut into 438- X 152-mm (19- welds. The welds were made with a conducted at -51°C (-60°F) and -18°C X 6-in.) pieces with the short edge lying 6.4-mm (0.25-in.) thoriated tungsten elec­ (0°F). in the longitudinal (L) or rolling direction. trode. To enhance penetration, helium The longitudinal surface of the edge of was added to the argon torch gas to the plates to be welded was ground to produce a mixture of 80% helium and Results remove the flame cut surface. Two plates 20% argon. Arc current was maintained Magnetic particle inspection of the fin­ were tack welded to form a square- at 1000 A, arc voltage at 12 V, and torch ished weldments showed no evidence of groove in a butt joint with no root travel speed at 2.0 mm/s (4.75 ipm). The surface cracking. Similarly, radiographic opening. The plate assembly before square-groove weldments in 19-mm inspection showed no indications of welding is shown in Fig. 1. (0.75-in.) thick plate were made in the flat cracking, porosity, or tungsten inclu­ The buried GTAW process employs a position in two passes, one from each sions. high welding current with a low arc side. Forced convective cooling by gas All square-groove weldments were voltage to displace the molten weld pool impingement on the weld bead surface made in two passes, one from each side. beneath the tungsten electrode, thus per­ as developed by Wells (Ref. 8) was used Penetration of approximately 13 mm (0.5 mitting the tungsten to penetrate on one ASTM A710 weldment to in.) per pass was achieved, which beneath the plate surface until the arc enhance the cooling rate of this high heat resulted in a 7 mm (0.28 in.) overlap at pressure is offset by the weight of the input process. The convective cooling the weld root. The completed weldment, displaced molten metal. Two buried GTA device is shown attached to the welding BA6, is shown in Fig. 2, and macrosec­ weldments were fabricated in ASTM torch in Fig. 1. The welding variables for tions from both weldments are shown in A710 steel as autogenous square-groove each weld pass are shown in Table 1. Fig. 3. The microstructure of the A710 base plate shows the presence of polygonal Table 1—Variables Employed for Buried Gas Tungsten Arc Welding of Steel ferrite with dark areas, which are proba­ bly pearlite —Fig. 4A. The HAZ near the Weldment identification BA6 BA7 base plate consists of fine-grained poly­ Base plate material ASTM A710 ASTM A710 gonal ferrite plus the dark-etching micro- Grade A, Class 3 Grade A, Class 3 constituent, which is probably pearlite — Welding position flat flat Fig. 4B. The HAZ near the fusion zone Joint design square groove square groove consists of a light-etching matrix phase, Filler metal wire none — autogenous none — autogenous Welding polarity DCEN DCEN which is probably bainitic ferrite —Fig. Machine characteristics CC CC 4C. Dispersed throughout the bainitic Tungsten electrode diameter (mm) 6.4 6.4 ferrite are higher carbon regions, which 2% thoriated 2% thoriated appear dark. These regions consist of Torch shield gas 13.7 Ar 13.7 Ar cementite particles and martensite-aus- 63.7 He 63.7 He tenite (MA).
Details
-
File Typepdf
-
Upload Time-
-
Content LanguagesEnglish
-
Upload UserAnonymous/Not logged-in
-
File Pages4 Page
-
File Size-