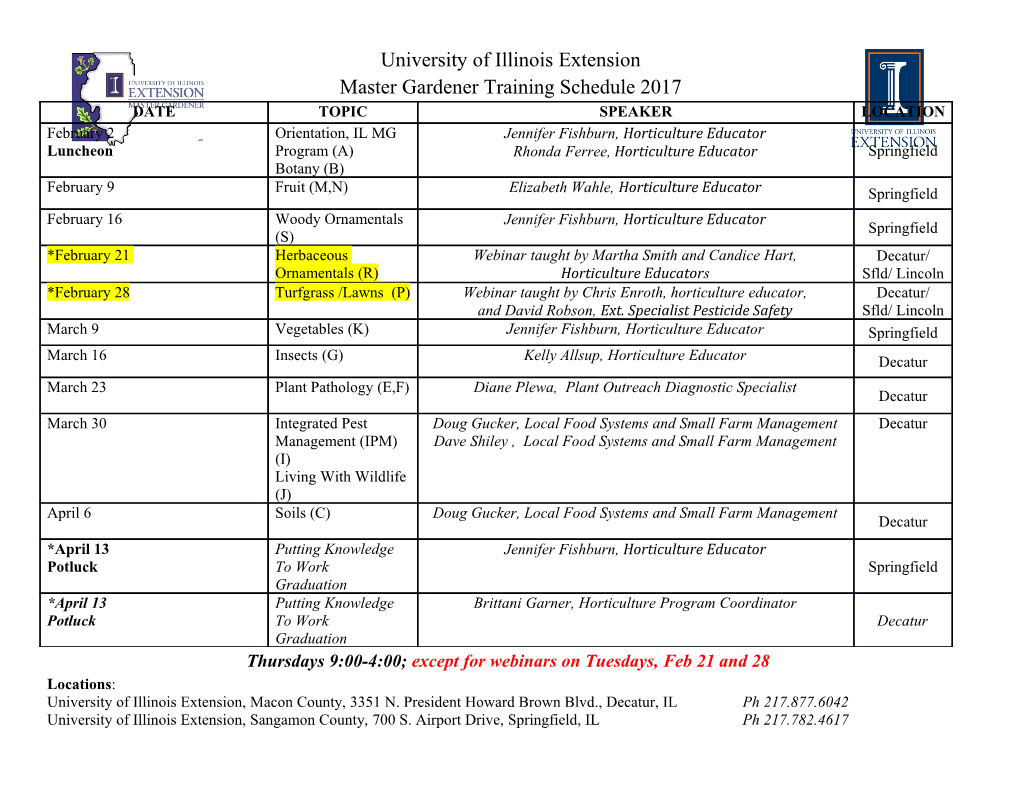
Optimization of Heat Spreader A thesis presented to the faculty of the Russ College of Engineering and Technology of Ohio University In partial fulfillment of the requirements for the degree Master of Science Rahat M. Taposh June 2012 © 2012 Rahat M. Taposh. All Rights Reserved. 2 This thesis titled Optimization of Heat Spreader by RAHAT M. TAPOSH has been approved for the Department of Mechanical Engineering and the Russ College of Engineering and Technology by Khairul Alam Moss Professor of Mechanical Engineering Dennis Irwin Dean, Russ College of Engineering and Technology 3 ABSTRACT TAPOSH, RAHAT M., M.S., June 2012, Mechanical Engineering Optimization of Heat Spreader Director of Thesis: Khairul Alam One of the important components of a heat sink is the heat spreader which improves the heat dissipation from the chip into the environment. The improvement due to the spreading of the heat flux over a wider area is partially counteracted by the spreading resistance, i.e., resistance due to the longer path taken by the heat flux. Several studies have been carried out to determine the spreading resistance; which includes cylindrical as well as cartesian co-ordinate system. The heat spreader tends to be the most significant mass in the heat sink. Therefore selection of the heat spreader dimension deserves serious consideration; this is particularly true in high heat flux situations. The focus of this is to examine the optimum dimension of heat spreader as a function of the thermal and geometric parameters of the heat sink problem. Approved: _____________________________________________________________ Khairul Alam Moss Professor of Mechanical Engineering 4 ACKNOWLEDGMENTS I would like to express my deepest gratitude to my academic advisor, Professor Khairul Alam for his continuous flow of support and outstanding guidance during my Master of Science in Mechanical Engineering program. I am very grateful to him for giving me the opportunity to work on such a cutting edge research. I would like to thank Dr. Xiaoping Shen, Dr. Hajrudin Pasic, and Dr. Daniel Gulino for valuable guidance and critical comment being my thesis committee members. I am extremely grateful to my family members for their lifelong support and encouragement in pursuing my higher education. I am especially thankful to my mother and aunt for supporting and helping me during various stages of my life. 5 TABLE OF CONTENTS Page Abstract ........................................................................................................................... 3 Acknowledgments ........................................................................................................... 4 List of Tables................................................................................................................... 6 List of Figures ................................................................................................................. 7 Nomenclature ................................................................................................................ 11 Chapter 1: Introduction .................................................................................................. 13 Chapter 2: Background .................................................................................................. 18 Chapter 3: Modeling and Analysis ................................................................................. 34 Chapter 4: Heat Spreader for High Heat Flux System .................................................... 56 Chapter 5: Conclusions and Summary ........................................................................... 67 References ..................................................................................................................... 70 6 LIST OF TABLES Page Table 1 Comparative Results and Validation……………………………………55 Table 2 Optimum Thickness and Total Resistance of Heat Spreader……….......64 7 LIST OF FIGURES Page Figure 2.1 Different configurations of extended surface (a) pin fin (Source: “Heat Sink” n.d.) (b) straight fin (Source: “Heat Sink” n.d.) (c) flared fin (Source: “Heat Sink” n.d.) (d) metal foam between heat spreaders (Source: “Open Cell-Foam” n.d.). .......................................... 18 Figure 2.2 Contribution of different resistances, when heat flows from source to environment through a heat sink ........................................................ 22 Figure 2.3 Variations of total resistance as a function of the spreader thickness in non dimensional form; and the ratio of the source length to the length of the heat spreader (ℓ/ ) for ℎ/ =10 ......................................... 23 Figure 2.4 Variations of total resistance as a function of the spreader thickness in non dimensional form; and the ratio of the source length to the length of the heat spreader (ℓ/ ) for ℎ/ =20 ......................................... 27 Figure 2.5 Schematic diagram of thermal system having square heat source of length 2ℓ, square heat spreader of length 2L, thickness t and a heat flux q applied on the top of heat spreader (Source: Feng & Xu, 2004) ................................................................................................... 30 Figure 2.6 Spreading resistance as a function of Bi and τ, while other geometric parameters are constant as β = 0.25, ε = 0.25, γ = 0.75. This is the corrected version of the Fig. 2 in the paper by Feng & Xu (2004), and is based on the corrected Equation 2.15 ........................ 30 Figure 2.7 Spreading resistance as a function of Bi and τ, while other geometric parameters are constant as β = 1(square heat spreader), ε = γ =0.167 ............................................................................................. 30 Figure 3.1 Minimum total resistance with respect to ℎ and at higher values of the parameters ........................................................................ 38 Figure 3.2 Minimum total resistance with respect to ℎ and length ratio, at lower values of the parameters .......................................................... 39 Figure 3.3 Contours of minimum total resistance (K/W) at of ℎ and .......................................................................................... 40 8 Figure 3.4 Contours of minimum total resistance (K/W) at of ℎ ....................................................................................................... 40 Figure 3.5 Contribution of conductive resistance, at minimum .................... 41 Figure 3.6 Contour plot for conductive resistance (K/W), with respect to ℎ and at minimum total resistance, ....................................... 42 Figure 3.7 Contour plot for convective resistance (K/W), with respect to ℎ and at minimum total resistance, ....................................... 43 Figure 3.8(a) Contour plot for spreading resistance, with respect to low ℎ and at minimum total resistance, .............................................. 45 Figure 3.8(b) Contour plot for spreading resistance (K/W), with respect to ℎ and at minimum total resistance, ............................................... 45 Figure 3.9 Contour plot for spreading resistance (K/W), at higher values of ℎ ....................................................................................................... 46 Figure 3.10 Different foams offering the effective heat transfer coefficient against power generated by the heater. Effective heat transfer coefficient provided by graphite foam found to be highest to date. (Source: “S-Bond Technologies” n.d.) .................................................. 47 Figure 3.11 Dimensionless optimum thickness, with respect to ℎ and at minimum total resistance, , where each side (2 ) of square source is 20 mm long .................................................................... 48 Figure 3.12 Contour plot for dimensionless optimum thickness, with respect to ℎ and at minimum total resistance, ....................... 49 Figure 3.13 Contour plot for dimensionless optimum thickness, at low ℎ and , where each side ( ) of square heat source is 20 mm long ...... 50 Figure 3.14 Contour plot for dimensionless parameter, ℎ at low ℎ and , where each side ( ) of square heat source is 20 mm long............. 52 Figure 3.15 Contour plot for dimensionless parameter, ℎ with respect to ℎ and , where each side ( ) of square heat source is 30 mm long ...................................................................................................... 52 9 Figure 3.16 Contour plot for dimensionless parameter, ℎ with respect to ℎ and , where each side ( ) of square heat source is 20 mm long (Source: Maranzana et al.,2004). ........................................................... 53 Figure 4.1 Total resistance of a heat spreader of different thermal conductivities as a function of its thickness when convective heat transfer coefficient = 250 W/m2K and heat source is 5x5 mm2 .............. 57 Figure 4.2 Total resistance of a heat spreader of different thermal conductivities as a function of its thickness when convective heat transfer coefficient = 5,000 W/m2K and heat source is 5x5 mm2 ........... 58 Figure 4.3 Total resistance of a heat spreader of different thermal conductivities as a function of its thickness when convective heat transfer coefficient = 10,000 W/m2K and heat source is 5x5 mm2 ......... 59 Figure 4.4 Total resistance of a heat spreader of different thermal conductivities as a function of its thickness when convective heat transfer coefficient = 20,000 W/m2K and heat source is 5x5 mm2.......................................
Details
-
File Typepdf
-
Upload Time-
-
Content LanguagesEnglish
-
Upload UserAnonymous/Not logged-in
-
File Pages73 Page
-
File Size-