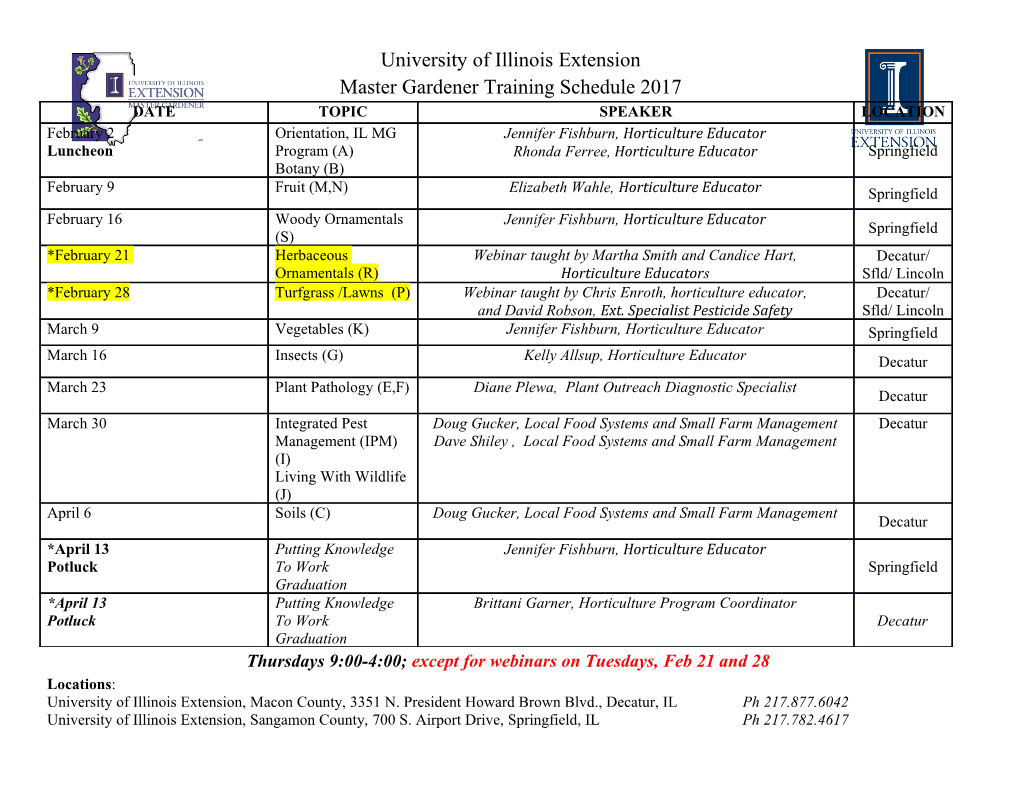
AAAS Research Volume 2020, Article ID 1398903, 10 pages https://doi.org/10.34133/2020/1398903 Research Article Intrinsically Stretchable Organic-Tribotronic-Transistor for Tactile Sensing Junqing Zhao ,1,2 Tianzhao Bu ,1,2 Xiaohan Zhang,1,2 Yaokun Pang,1,2 Wenjian Li,1,2 Zhi Zhang,1,2 Guoxu Liu,1,2 Zhong Lin Wang,1,2,3 and Chi Zhang 1,2,4 1CAS Center for Excellence in Nanoscience, Beijing Key Laboratory of Micro-Nano Energy and Sensor, Beijing Institute of Nanoenergy and Nanosystems, Chinese Academy of Sciences, Beijing 100083, China 2School of Nanoscience and Technology, University of Chinese Academy of Sciences, Beijing 100049, China 3School of Material Science and Engineering Georgia Institute of Technology, Atlanta, GA 30332, USA 4Center on Nanoenergy Research, School of Physical Science and Technology, Guangxi University, Nanning 530004, China Correspondence should be addressed to Chi Zhang; [email protected] Received 8 April 2020; Accepted 25 May 2020; Published 24 June 2020 Copyright © 2020 Junqing Zhao et al. Exclusive Licensee Science and Technology Review Publishing House. Distributed under a Creative Commons Attribution License (CC BY 4.0). Stretchable electronics are of great significance for the development of the next-generation smart interactive systems. Here, we propose an intrinsically stretchable organic tribotronic transistor (SOTT) without a top gate electrode, which is composed of a stretchable substrate, silver nanowire electrodes, semiconductor blends, and a nonpolar elastomer dielectric. The drain-source current of the SOTT can be modulated by external contact electrification with the dielectric layer. Under 0-50% stretching both parallel and perpendicular to the channel directions, the SOTT retains great output performance. After being stretched to 50% for thousands of cycles, the SOTT can survive with excellent stability. Moreover, the SOTT can be conformably attached to the human hand, which can be used for tactile signal perception in human-machine interaction and for controlling smart home devices and robots. This work has realized a stretchable tribotronic transistor as the tactile sensor for smart interaction, which has extended the application of tribotronics in the human-machine interface, wearable electronics, and robotics. 1. Introduction which can effectively convert mechanical energy into electric- ity [20–22]. In recent years, tribotronics as a new field has Stretchable electronics are grabbing more and more attention been proposed by using the triboelectric potential generated for a wide range of applications in wearable devices, soft by TENG to control the carrier transport in semiconductors, mechanics, robotic skin, human-machine interfaces, and so which has established the direct interaction mechanism on [1–6]. To date, a series of stretchable functional devices between human/environment and electronics [23–29]. have been developed with prominent tactile-sensing proper- Moreover, a variety of tribotronic functional devices have ties based on various physical transduction mechanisms such been demonstrated for tactile perception and control, includ- as piezoresistivity [7, 8], capacitance [9], magnetism [10, 11], ing smart tactile switch [30], tactile-sensing arrays [31], and optics [12]. However, most of the tactile-sensing mecha- active modulation of conventional electronics [32], and nisms for stretchable electronics are passive, lacking direct mechanosensation-active matrix [33]. In addition, tribotro- interaction with human/environment [13–17]. This compli- nic devices have demonstrated the diversity of material selec- cates the process of information acquisition and further tion [24–36], which is very promising for the intrinsically influences the tactile perception ability of stretchable func- stretchable electronics for active tactile sensing by further tional devices. Therefore, developing stretchable electronics coupling with stretchable materials. with an active sensing mechanism is highly desired. Here, we propose an intrinsically stretchable organic tri- Since 2012, the triboelectric nanogenerator (TENG) as a botronic transistor (SOTT) without a top gate electrode, new energy technology derived from the Maxwell displace- which is composed of a stretchable substrate, silver nanowire ment current has been invented by Wang et al. [18, 19], (Ag NW) electrodes, semiconductor blends, and a nonpolar 2 Research elastomer dielectric. The drain-source current of the SOTT PDMS, the P3HT NF solution was subsequently spin-coated can be modulated by external contact electrification with onto the drain-source electrodes through a polyimide the dielectric layer. Under 0-50% stretching both parallel shadow mask to achieve a patterned semiconductor layer and perpendicular to the channel directions, the SOTT (iv). Contained in the transparent PDMS, the semiconductor exhibits good output performances. After being stretched to layer has revealed great optical transparency, which is 50% for thousands of cycles, the SOTT can survive with important for the application in wearable and bionic excellent stability. Moreover, the SOTT can be conformably electronics (Figure S2). The stretchable dielectric layer, attached to the human hand, which can be used for tactile which is composed of PDMS, was spin-coated onto a signal perception in human-machine interaction and for polytetrafluoroethylene (PTFE) block and then transferred controlling smart home devices and robots. This work has onto the P3HT NF/PDMS semiconductor layer to form the realized a stretchable tribotronic transistor as the tactile sen- final SOTT (v and vii). The complete structure of the SOTT sor for smart interaction, which has extended the application shown in Figure 1(b) was obtained by peeling off the whole of tribotronics in human-machine interface, wearable elec- device from the PTFE block (viii), which has demonstrated a tronics, and robotics. simple structure without a top gate electrode. The channel length is about 500 μm, as shown in Figure 1(c). Since all 2. Results and Discussion components of the device are stretchable, the prepared SOTT can be stretched both parallel and perpendicular to the 2.1. Fabrication of the Stretchable Tribotronic Transistor. channel directions. Figure 1(d) shows the optical graphs of a Poly(3-hexylthiophene-2,5-diyl) (P3HT), as a polymer semi- stretched device in two directions. As clearly seen from the conductor, has a high hole mobility and a low band gap width graphs, the device can be deformed without physical damage [37]. The P3HT nanofibril (P3HT-NF) combined with the upon stretching. Moreover, optical microscopy and atomic stretchable elastomer materials has high stretchability, which force microscopy (AFM) images of the P3HT NF/PDMS is good for developing stretchable semiconductor devices [38, blends have demonstrated that the semiconductor blends can 39]. Among a lot of elastomers, the polydimethylsiloxane be stretched without any obvious cracks under 50% strain, as (PDMS) with a simple preparation process can sustain large shown in Figures 1(e) and 1(f), which is very helpful for strains. Moreover, the PDMS has a good triboelectric prop- promoting the stretchability of the SOTT. erty, which is good for tribotronic devices [40–42]. Ag NWs have good conductivity, which have been widely used 2.2. Mechanism and Performances of the Stretchable in the field of stretchable electrodes [43, 44]. Therefore, in Tribotronic Transistor. The working mechanism of the SOTT order to obtain highly stretchable SOTT, we exploit the is presented in Figure 2(a). The drain and source electrodes P3HT nanofibril-percolated PDMS rubber composite as a of the SOTT are connected with a voltage source. An alumi- stretchable semiconductor, the Ag NWs dispersed within num (Al) film, as an external triboelectric layer, fully contacts the PDMS as a stretchable conductor, and the PDMS as a gate with the dielectric layer in the initial state for electrification as dielectric. Through the contact electrification between the shown in Figure 2(a), i. The Al film is electrified with positive external triboelectric layer and the PDMS gate dielectric layer, charges while the PDMS dielectric layer with negative the drain-source current of the transistor can be modulated. charges for the difference in charge affinities. Owing to the The schematic illustration of the fabrication process for electrostatic balance, electrical potential difference is not the SOTT is shown in Figure 1(a). The detailed process is applied to the channel region, and no obvious changes take elaborated in Materials and Methods. The SOTT consists of place in the drain current. When the Al film gradually sepa- a stretchable substrate, Ag NW electrodes, semiconductor rates from the PDMS dielectric layer by an external force as blends, and a nonpolar elastomer dielectric, which is fabri- shown in Figure 2(a), ii, negative charges on the dielectric cated throughout a sequential lamination transfer process. layer surface will induce an inner charge polarization, which To prepare the stretchable drain and source electrodes, Ag will build an inner electric field across the channel and the NWs were spray coated onto an octadecyltrimethoxysilane- dielectric surface, leading the holes to accumulate at the (OTS-) pretreated silica wafer through a shadow mask (i), interface of the channel and the dielectric layer. As a result, then followed by embedding into a nonpolar elastomeric an enhancement zone is achieved in the p-type P3HT PDMS substrate (ii). To build an ohmic contact between
Details
-
File Typepdf
-
Upload Time-
-
Content LanguagesEnglish
-
Upload UserAnonymous/Not logged-in
-
File Pages10 Page
-
File Size-