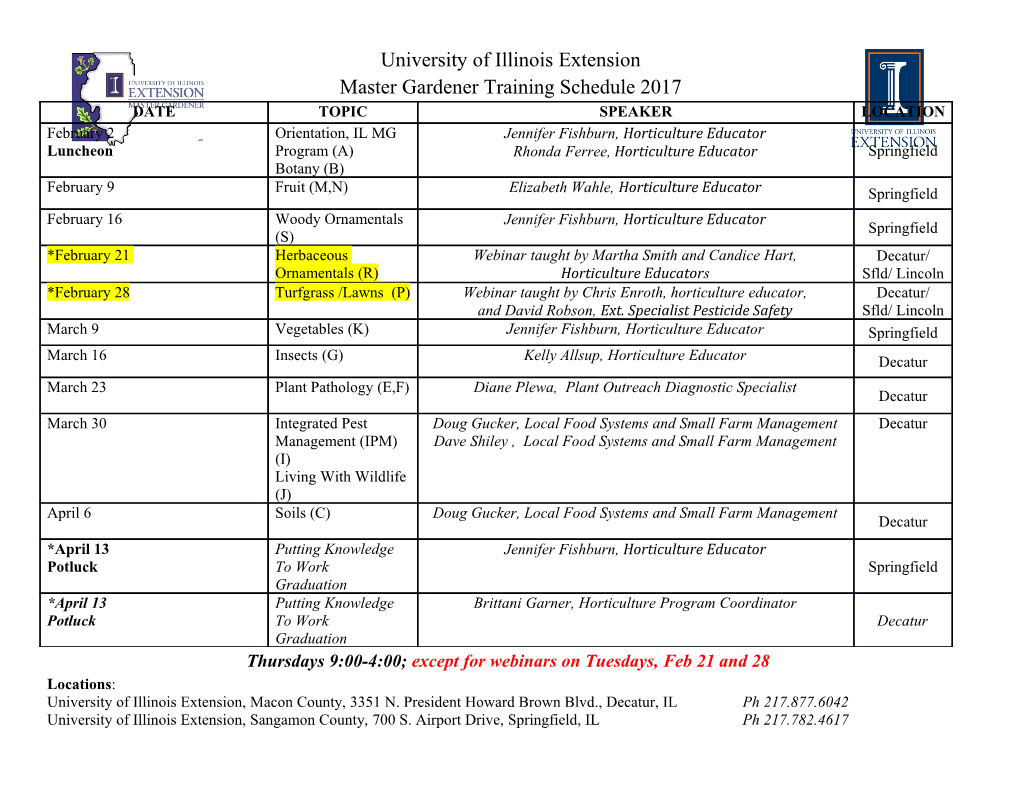
(12) INTERNATIONAL APPLICATION PUBLISHED UNDER THE PATENT COOPERATION TREATY (PCT) (19) World Intellectual Property Organization International Bureau (43) International Publication Date PCT (10) International Publication Number 26 June 2008 (26.06.2008) WO 2008/076755 Al (51) International Patent Classification: (81) Designated States (unless otherwise indicated, for every C08J 9/00 (2006.01) C08J 9/14 (2006.01) kind of national protection available): AE, AG, AL, AM, AT,AU, AZ, BA, BB, BG, BH, BR, BW, BY,BZ, CA, CH, (21) International Application Number: CN, CO, CR, CU, CZ, DE, DK, DM, DO, DZ, EC, EE, EG, PCT/US2007/087231 ES, FI, GB, GD, GE, GH, GM, GT, HN, HR, HU, ID, IL, IN, IS, JP, KE, KG, KM, KN, KP, KR, KZ, LA, LC, LK, (22) International Filing Date: LR, LS, LT, LU, LY,MA, MD, ME, MG, MK, MN, MW, 12 December 2007 (12.12.2007) MX, MY, MZ, NA, NG, NI, NO, NZ, OM, PG, PH, PL, PT, RO, RS, RU, SC, SD, SE, SG, SK, SL, SM, SV, SY, (25) Filing Language: English TJ, TM, TN, TR, TT, TZ, UA, UG, US, UZ, VC, VN, ZA, ZM, ZW (26) Publication Language: English (30) Priority Data: (84) Designated States (unless otherwise indicated, for every kind of regional protection available): ARIPO (BW, GH, 60/869,932 14 December 2006 (14.12.2006) US GM, KE, LS, MW, MZ, NA, SD, SL, SZ, TZ, UG, ZM, (71) Applicant (for all designated States except US): PACTIV ZW), Eurasian (AM, AZ, BY, KG, KZ, MD, RU, TJ, TM), CORPORATION [US/US]; 1900 West Field Court, Lake European (AT,BE, BG, CH, CY, CZ, DE, DK, EE, ES, FI, Forest, IL 60045 (US). FR, GB, GR, HU, IE, IS, IT, LT,LU, LV,MC, MT, NL, PL, PT, RO, SE, SI, SK, TR), OAPI (BF, BJ, CF, CG, CI, CM, (72) Inventor; and GA, GN, GQ, GW, ML, MR, NE, SN, TD, TG). (75) Inventor/Applicant (for US only): HANDA, Y., Paul [CA/US]; 16 Coddington Grove, Pittsford, NY 14534 Published: (US). — with international search report — before the expiration of the time limit for amending the (74) Agents: CHIARINI, Lisa, A. et al.; Baker Botts L.L.P., claims and to be republished in the event of receipt of 30 Rockefeller Plaza, New York, NY 101 12-4498 (US). amendments (54) Title: EXPANDED AND EXTRUDED BIODEGRADABLE AND REDUCED EMISSION FOAMS MADE WITH METHYL FORMATE-BASED BLOWING AGENTS (57) Abstract: Expanded and extruded biodegradable polymer foams are obtained using biodegradable polymers and environmen tally benign non-VOC methyl formate as a blowing agent. The blowing agent can be a blend further including at least one co- blowing agent, preferably an environmentally friendly species (e.g., non-soc), which is either a physical co-blowing agent (e.g. an inorganic agent, a hydrocarbon, a halogenated hydrocarbon, a hydrocarbon with polar, functional group(s), water or any combination thereof), or a chemical co-blowing agent, or combinations thereof. The blowing agent blend can include any combination of methyl formate and one or more co-blowing agents. The polymer foam can include a biodegradable polymer or its blends with other biodegradable polymers or conventional (non-biodegradable) polymers. The methyl formate-based blowing agent blends produce stable foams for various applications, including containers, packaging systems, as well as for insulation and protective cushioning. Processes for the preparation of such foams are also provided. EXPANDED AND EXTRUDED BIODEGRADABLE AND REDUCED EMISSION FOAMS MADE WITH METHYL FORMATE-BASED BLOWING AGENTS by Y. Paul Handa CROSS REFERENCE TO RELATED APPLICATIONS This application claims the benefit under 35 U.S.C. § 119(e) of U.S. provisional patent application number 60/869,932 filed on December 14, 2006, the entirety of the disclosure of which is explicitly incorporated by reference herein. FIELD OF INVENTION The present invention relates generally to foams made from biodegradable polymers and environmentally benign blowing agents, and processes of making the same. Particularly, the present invention relates to biodegradable and reduced emission stable foams made from biodegradable polymers that undergo hydrolytic decomposition or biodegradation, using methyl formate-based blowing agents, and processes of making the same. The biodegradable polymer foams serve as environmentally friendly replacements in applications where foams made from petroleum-derived polymers are traditionally used. BACKGROUND OF THE INVENTION Presently, foams used in packaging, protective, and insulating materials are made from oil and natural gas derived thermoplastics such as alkenyl aromatic polymers (e.g., polystyrene) or polyolefins (e.g. polyethylene and polypropylene) Such polymers, designated herein "conventional polymers" or "conventional plastics," do not undergo biodegradation and become a fixture of landfills and litter. On the other hand, biodegradable polymers are thermoplastics that are easily melt processed just like the conventional thermoplastics, but with the added attribute that they undergo hydrolytic decomposition or biodegradation in aerobic (such as composts) and anaerobic (such as landfills) environments where microbes break down the polymer to give primarily methane, carbon dioxide, organic residue called humus, and water. Biodegradable polymers can be made from petrochemical feedstock or, alternatively, from renewable biomass such as, for example, corn, sugarcane, wood, switchgrass or soybeans. Petrochemical based biodegradable polymers include, for example, various polyesters such as Biomax and Ecoflex. Biomass based polymers, also known as biopolymers, include, for example, polymers containing hydroxy acids such as polylactide or their esters such as polyhydroxyalkanoates. It should be noted, however, that not all biopolymers are biodegradable, and not all petroleum based polymers are non-biodegradable. Recently, the advent of biomass derived polymers has shown that biodegradable thermoplastics having properties similar to those of conventional plastics can be prepared on a commercial scale. If means can be found to further improve the properties of biodegradable polymers (e.g. mechanical strength, elongational viscosity, stability over a wide temperature range, compatibility with conventional and other biodegradable polymers, etc.) then, by replacing conventional polymers with biodegradable polymers, the environmental aspects of solid plastic waste can be largely mitigated and, for certain applications, can be completely eliminated. The biodegradable foams can be used for various packaging applications where foams made from conventional polymers are currently employed. Foams are commonly manufactured as expanded beads, extruded sheets, or extruded boards. The difference between the expanded and extruded foams is that the extruded foams, in the form of continuous sheets or boards, are made in a single-step process; whereas, expanded foams, in the form of discrete, small-size pieces, are made in a multi-step process. Thus, the dimensions of expanded foam are much smaller than those of extruded foam. Furthermore, the expanded foams do not necessarily have to s be in the form of beads or peanuts, but can also be made from pellets, rods, platelets, thin sheet or film. For the sake of convenience, the term "bead" or "pellets" will be used throughout this application to imply other shapes in which small, discrete particles of the polymer resin can be used to make expanded foams. Generally, foams in the form of beads or sheets having a thickness of less than o about one-half inch can be used to make packaging materials such as containers (e.g. cups, bowls, clamshells, picnic chests) for hot or cold beverages or food whereby the beads are fused or the sheet is thermoformed in a mold to form the packaging material of a desired shape. Such foams are also used as protective and cushioning materials for transportation of delicate or shock sensitive articles whereby the foam beads can be used as loose fill dunnage material and thin sheets can be used to provide protective wrapping. Packaging and insulation foam products with a thickness greater than about 0.5 inch are called planks or boards. Such foam boards are produced in the desired shape and size by direct extrusion and cutting if needed, or by fusing the expanded foam beads. The foam boards can be used for protective packaging by die-cutting the boards to various shapes, for insulation, for dissipating mechanical energy as in automotive parts, or for cushioning floats. It is desirable that the foams used in such diverse applications be dimensionally stable; this characteristic is even more desirable for planks or boards. Polymer foams are commonly made using a continuous process where a blowing agent laden molten resin is extruded under pressure through an appropriate die into a lower pressure atmosphere. Alternatively, a batch or staged process can be used, where small polymer beads (also called particles or pellets) are impregnated with blowing agent and then expanded by heating rapidly to a temperature near or above the glass-transition or crystal-melt temperature of the polymer—blowing agent system, or subjected to an external compressive stress at a temperature up to the glass- transition or crystal-melt temperature of the polymer-blowing agent system. Presently, physical blowing agents more commonly used for making thermoplastic polymer foams are hydrocarbons, chlorinated hydrocarbons, hydrochlorofluorocarbons, hydrofluorocarbons, or combinations thereof. Hydrocarbons with three or more carbon atoms are considered volatile organic compounds (VOCs) that can lead to formation of smog. Furthermore, some halogenated hydrocarbons are either VOCs or may have high ozone depletion potential (ODP) or global warming potential (GWP), or may be hazardous air pollutants (HAPs) and, at times, may fall into more than one of these categories. Therefore, the use of hydrocarbon and halogenated hydrocarbon blowing agents for preparing polymeric foams is not preferred environmentally and imposes many limitations on the manufacturing process, thus complicating and significantly increasing the cost of manufacturing. In efforts to make biodegradable polymer foams (beads or sheets), the conventionally used blowing agents, such as VOCs, have been the obvious choice, albeit such uses are associated with the same environmental concerns as noted above.
Details
-
File Typepdf
-
Upload Time-
-
Content LanguagesEnglish
-
Upload UserAnonymous/Not logged-in
-
File Pages48 Page
-
File Size-