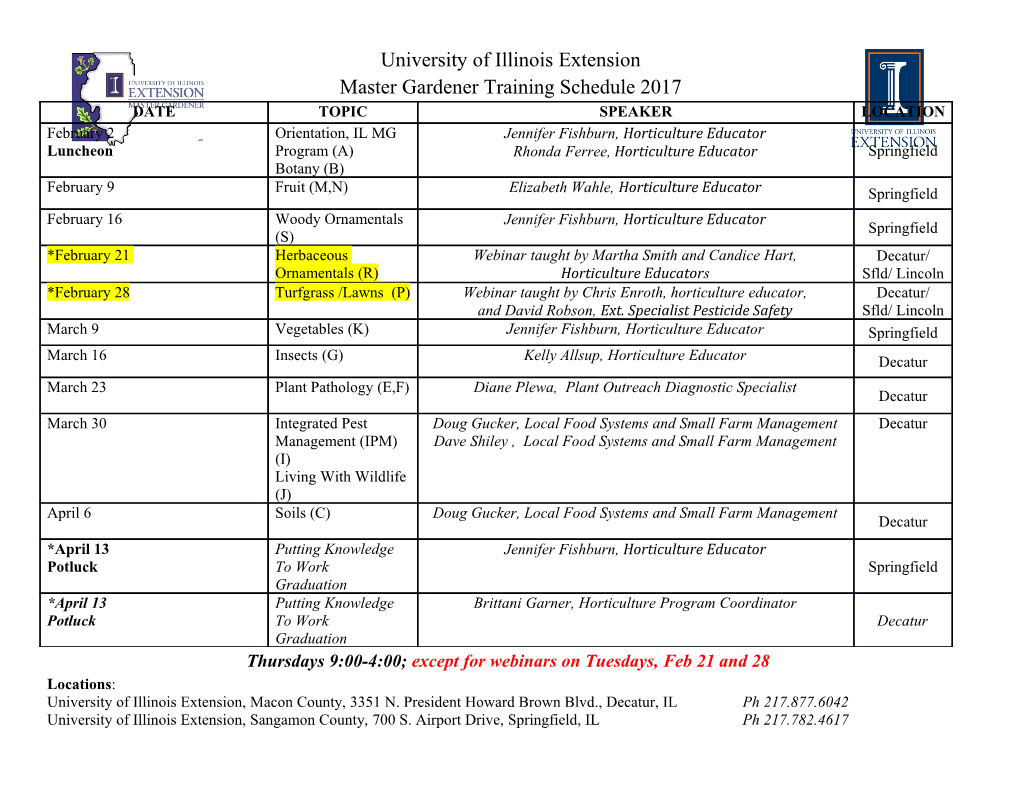
applied sciences Article Investigation of Seal Cavity Leakage Flow Effect on Multistage Axial Compressor Aerodynamic Performance with a Circumferentially Averaged Method Dong Liang 1 , Donghai Jin 1,2,* and Xingmin Gui 1,2 1 Aeroengine Simulation Research Center, School of Energy and Power Engineering, Beihang University, Beijing 100191, China; [email protected] (D.L.); [email protected] (X.G.) 2 Jiangxi Research Institute, Beihang University, Nanchang 330096, China * Correspondence: [email protected]; Tel.: +86-010-8231-6870 Featured Application: This method can be used to quickly analyze the seal cavity leakage effect during compressor design as well as performance degradation caused by labyrinth wear in mul- tistage axial-flow compressors. After being verified in turbine, it can be further used to consider the influence of seal cavity leakage flow in whole aero-engine simulation. Abstract: The seal cavity leakage flow has a considerable impact on the performance of the aeroengine, especially on the multistage compressor. Thus, a quasi-three-dimensional simulation program named CAM is developed basing on circumferentially averaged throughflow method. The program enables a rapid diagnosis for the performance degradation of multistage compressor caused by labyrinth wear. The coupling flow field between the seal cavity leakage flow and the main flow field at the root of the shrouded stator of a high-loading three-stage compressor with inlet guide vanes (IGV) was simulated Citation: Liang, D.; Jin, D.; Gui, X. by CAM and the results indicate that seal cavity leakage flow has a significant impact on the overall Investigation of Seal Cavity Leakage performance of the compressor. That is, for a 1% increase in the seal-tooth clearance-to-span ratio, the Flow Effect on Multistage Axial decrease in total pressure ratio was 2.6%, and the reduction in efficiency was 0.6%. Stage performance Compressor Aerodynamic Performance with a Circumferentially shows that the seal cavity leakage flow reduces the pressurization capacity of the current stator and Averaged Method. Appl. Sci. 2021, 11, the work capacity of the downstream rotor, but has little effect on the upstream blade row. Spanwise 3937. https://doi.org/10.3390/ distribution of blade element performance shows that the leakage flow leads to an increased flow app11093937 blockage near the hub, resulting in spanwise migration. The incidence of the stator and rear rotor then change through the entire span. The leakage flow leads to the flow blockage and migration and hence Academic Editor: Kambiz Vafai changes the incidence angle, which results in the deterioration of compressor performance. Received: 7 March 2021 Keywords: seal cavity leakage flow; shrouded stator; flow field destruction; deterioration; circumfer- Accepted: 24 April 2021 entially averaged throughflow model Published: 27 April 2021 Publisher’s Note: MDPI stays neutral with regard to jurisdictional claims in 1. Introduction published maps and institutional affil- iations. Deterioration, induced by operational and environmental effects, leads to a gradual decline of the performance of an aircraft engine [1–3]. Therefore, requirements for rapid full- engine simulations occur. Numerical calculation methods for aeroengines can be divided into three different types: zero-dimensional, two-dimensional/quasi three-dimensional and three-dimensional. The zero-dimensional calculation does not need detailed geometric Copyright: © 2021 by the authors. parameters, has very low requirements in terms of computer resources and is very fast. Licensee MDPI, Basel, Switzerland. It is suitable for scheme evaluation and preliminary design. However, the accuracy of such This article is an open access article distributed under the terms and a calculation depends on the characteristic lines of the existing components and reliable conditions of the Creative Commons experimental data. At the same time, the flow field of the main channel and the secondary Attribution (CC BY) license (https:// air system (SAS) of the engine cannot be simulated, so the flow field information cannot be creativecommons.org/licenses/by/ used in the optimization of specific components. 4.0/). Appl. Sci. 2021, 11, 3937. https://doi.org/10.3390/app11093937 https://www.mdpi.com/journal/applsci Appl. Sci. 2021, 11, 3937 2 of 15 Compared with the zero-dimensional simulation, 3D simulation can describe the three- dimensional relationship between the components and the whole flow channel, and can be used to discuss the complex physical phenomena and flow field structure inside the components. However, in order to obtain such abundant flow field details, a large amount of computer resources are required. In the current literature, there are a few published studies on 3D high fidelity simulation calculation of an aeroengine. The center for turbulence simulation (CITS) of Stanford University has carried out a series of research aimed at developing integrated high fidelity aeroengine simulation technology and has been able to achieve preliminary simulation of the whole aircraft engine [4,5]. Medic et al. [6] completed the simulation of a 20 degrees sector of a gas turbine engine including the fan, compressors, turbines, the exit nozzle and the combustor. The simulation was performed on two different meshes; one was fine, and the other was coarse. For the coarse mesh which contained 14 million cells, the simulation was performed on 700 processors and required around two weeks to converge [7–10]. Three-dimensional simulation of the aeroengine main channel requires a computational speed of more than 1012 per second [11]. Full 3D simulation requires enormous amounts of relatively accurate data such as boundary conditions and initial conditions, which is not easy to obtain. Wang et al. [12] pointed out that even if the current computing capabilities can meet these requirements, considering the large number of resources required for full 3D calculations, it is still difficult to use the full 3D simulation as a tool for conventional research in Aeroengine Design in the short term. In contrast with 0D and 3D simulation, quasi three-dimensional simulation exhibits unique advantages. First of all, quasi-3D simulation can provide more abundant S2 flow field information. Secondly, quasi-3D simulation is easy to implement due to the small amount of calculation. Finally, for specific cases, the quasi-3D simulation can use empirical or semi-empirical models, such as loss and blockage models obtained from the experimental data, to modify the flow field results, so as to avoid the amplification of the flow field calculation error caused by the limitations of the turbulence model. Last but not least, the simulations of full-engine in the literature mentioned above have not included the SAS, which is known to have a considerable impact on the engine performance [13]. As a part of the SAS, seal cavity leakage flow occurs in the seal cavity at shrouded stator root (in compressors and turbines) or shrouded rotor tip (usually in turbines). Figure1 shows the seal cavity leakage in a compressor with shrouded stator. Although the flow exchange between the main channel and the cavity below the axial gap is often suppressed by engineering measures such as a labyrinth seal, it is difficult to fully eliminate the leakage from the axial gap. In recent years, more and more studies have shown that seal cavity leakage flow will obviously deteriorate the performance of axial compressor and turbine in aeroengines, and such influence cannot be ignored. Usually, for every 1% increase in seal-tooth clearance-to-span ratio, the decrease in pressure rise is 3%, and the reduction in efficiency is 1% [14,15]. As a reference, a usual relationship between efficiency deterioration and blade tip clearance in an axial compressor is that the compressor efficiency decreases by 1.5% when the rotor tip clearance increases by 1% with respect to the span [15–18]. For a cantilevered stator, the decrease ranges from 1.0% to 2.0% [15,17,19]. Mahmood and Turner [20] investigated the effect of seal cavity leakage flow on 1.5 stages of a 10 stage axial flow compressor. Numerical results indicate 0.86% efficiency reduction for a seal clearance of 1.3% span. Kato et al. [21] have performed a full three-dimensional unsteady calculation for a high-speed six-stage advanced axial-flow compressor. The calculation results with a sealed cavity under the stator blade reduce the efficiency by 1.7% compared with the results without a cavity. Similar to compressors, losses caused by leakage through the shrouded cavity contribute significantly to the overall losses of turbines [22]. Rosic et al. [23] compared experimental data and numerical simulations in a three-stage turbine and pointed out that calculation of the leakage flows and cavities is necessary in order to get good agreement between calculation and measurement. The flow in a two-stage LP-turbine at relatively low Reynolds numbers is simulated by Kuerner et al. [24] with an in-house 3D code. The overall isentropic efficiency derived from computations with Appl. Sci. 2021, 11, x FOR PEER REVIEW 3 of 16 Appl. Sci. 2021, 11, 3937 3 of 15 cavities is necessary in order to get good agreement between calculation and measure- ment. The flow in a two-stage LP-turbine at relatively low Reynolds numbers is simulated by Kuerner et al. [24] with an in-house 3D code. The overall isentropic efficiency derived fromcavities computations lies within 0.2% with of cavities the experimental lies within result, 0.2% and
Details
-
File Typepdf
-
Upload Time-
-
Content LanguagesEnglish
-
Upload UserAnonymous/Not logged-in
-
File Pages15 Page
-
File Size-