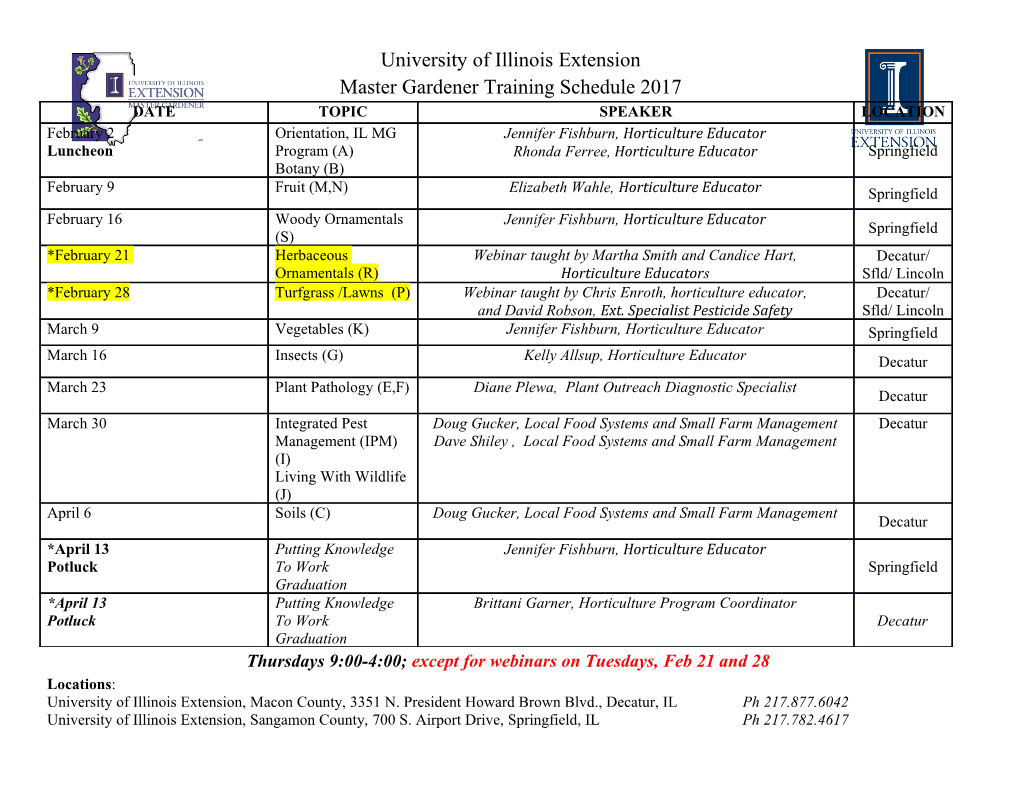
International Conference of Electrical, Automation and Mechanical Engineering (EAME 2015) A Design of an Autonomous Agricultural Robot to Navigate between Rows I.H. Celen, E. Onler E. Kilic Faculty of Agriculture, Dept. of Biosystem Eng. Namik Vocational School of Technical Sciences, Agricultural Kemal University Machinery Program, Namik Kemal University Tekirdag, Turkey Tekirdag, Turkey Abstract———An ultrasonic distance measuring based row guidance instance, plant cutters have vibration analysis liquid flow, and method is presented to guide a robot platform which is designed sensitive agriculture has GPS. independently to drive through the row crops in a field. The offset of the robot platform are detect-ed real-time for guiding In factories, the interaction between robots and human are the robot inside the crop row and also turn at the end of the rows more systematic and protected. However, in agriculture this is to adjacent row au-tomatically. Preliminary experiments of row not the case and such systems are not available. To make the guidance were implemented in rose field. Experimental results matter worse, people must work together in agricultural work. show that algorithms of row guidance and headland turn are This puts human life at more risk, since the interaction is according to the parameters measured and ana-lysed such as the relatively more. As a result, security systems must be offset for row guidance and the difference between the motion developed accordingly. trajectory of the robot and the expected trajectory. The accuracy Many studies about autonomous robot for agricultural of row guidance is ±70mm at the speed of 1 m/s. Tractacus got the 3rd place at free style category of Field ROBOT Event 2012 with applications can be found in scientific literature (Comba et al. smart spraying application which is starting to spray only if it 2010; Bakker et al. 2010; Slaghter et al. 2008) In most cases sees the crop canopy. robotic platforms have be conceived to operated in open field, Where autonomous guidance is rather complex owing to the Keywords-ultrasonic sensor; navigation; row guidance; lack of fixed references as well as the variability of the agricultural robot operative environment. For this reasons only in very rare cases prototypes have achieved a commercial stage. On the contrary, I. INTRODUCTION pot-plant nurseries are more suitable to the introduction of Agriculture sector is labor intense, predominantly autonomous robotic platform than open field (Belforte et al depending on man power. However, in countries where labor 2006; Comba et al 2011)[2]. is scarce, the cost of employing agricultural workers is high In this study, software and a robot which runs on this and most importantly, agricultural yield is high, there is a software was designed so that it could navigate be-tween row, tendency toward a highly automated agriculture. Automation turn at the end of a row, and handle tasks assigned to it is required not only during the whole process of growing autonomously. This agricultural robot was named plants but also during the storage and transportation of the TRACTACUS. agricultural products [1]. Every technological automation application contains elements of mechatronics. In agriculture, II. MATERIAL AND METHODS the detection of crop, plant and animals, harvesting and The robot developed has an electric motor system, two maintenance of the field are among the mechatronics activities prime wheels and two omni wheels, a control unit mounted on (Comba et al. 2011). top of it, and it can move in-between rows without touching The use of robots in agriculture sector has a wide range of them, turn at the end of the row and enter the next one. Figure purposes. The value of using robots in agricultural activities is 1 shows all the components of Tractacus. providing significant value to farmers. In agriculture, Chassis is made of lightweight material, fiberglass 5 mm in mechatronics is used in seeding, pest control robots thickness. Likened to a box, the chassis system has a round autonomous and remote controlled, crop damage robots, front where sensors can sit at different angles. All the feeding and irrigating robots, milking machines, crop components are secured to each other with bolts. Assembly categorization and processing robots without any holes are drilled so that components could be put together. categorization. This robot with its sensors can gather data from Moreover, holes were drilled on top of the chassis for cables. its environment, analyse the data, make decision based on the The electronic unit is mounted inside. A covering is used to data, then send command to other parts to take action and protect the electronic units from external conditions [3-5]. finally stop the robot. Ultrasonic sensors, MB1040 LV-MaxSonar®-EZ4, In all agricultural robots sensors play a key role. They produced by maxbotix are used in the study. LSM303 slope range in complexity from simple to sophisticated. Thanks to compensated compass module is also used (Figure 3) [6]. agricultural crops, robot sensor systems are widely used. For © 2015. The authors - Published by Atlantis Press 349 FIGURE II. DIFFERENTIAL DRIVE. FIGURE I. COMPONENTS OF THE AGRICULTURAL ROBOT. Vr= ω*(R+l/2) (1) As a main control unit, Arduino MEGA I/O is used to Vl= ω*(R-l/2) (2) analyze data coming from the sensors and adjust motors based on such data. A programming language, Arduino developed by Where l is the distance between the centers of the two Arduino is used to run the robot. wheels, Vr ;Vl are the right and left wheel velocities along the Dual VNH2SP30 Motor Driver Carrier MD03A model DC ground, and R is the signed distance from the ICC to the motor card is used to run the motors so that control card can midpoint between the wheels (Dudek et al. 2010). At any operate the robot (Figure 3) [7]. The motor card has two instance in time we can solve R and ω: channel, and it can operate and control two motors at the same time. Differential driving technique is operated accordingly. ω =( Vr - Vl)/ l (3) In order for Tractacus to move, two DC motors with a 75:1 R=0.5*( Vr +Vl)/ ( Vr - Vl) (4) drive wheel are used. The robot has a front wheel drive. Each front wheel is controlled separately and this makes it possible 1. If Vl=Vr, then we have forward linear motion in a to drive the robot. Technical features of DC motors are: straight line - 6V operating voltage 2. If Vl=-Vr, then we have a rotation about the midpoint - 130 RPM maximum turn speed of the wheel axis - 130 oz-in torque 3. If Vl=0, then we have rotation about the left wheel - Maximum load capacity 6 A voltage 4. If Vr=0, then we have a rotation about the right wheel - 450 mA current A. Straight Move In a straight move, Tractacus is expected to sensor sloping Tractacus has a front-drive wheel. The front wheel is plants, and move forward without hitting the plants. It uses produced by VEX company, each of which has a 5 inch sensors number 2 and 6 to determine lines. Two threshold diameter. Because of cogwheel surface, and the quality of the limits – lower and upper- are set so that Tractacus could sensor material, it can move on different grounds. DC engines are lines. directly embedded in wheels. Tractacus’s location is determined on the basis of the Differential driving technique is used and it requires that readings of the values by the sensors number 2 and 6. Under rear wheels can show increased resistance and therefore could ideal conditions, both sensors are expected to measure the easily turn. To achieve this purpose, Omni wheels are used same distance from the plants on both sides of the line, which with its multipurpose feature. They can turn just like regular in turn makes it sure that Tractacus goes right through the line. wheels and as a result of custom-made design, Tractacus can also move sideways. When Tractacus is driven autonomously, Depending on the value read by the sensors number 2 and it has two different algorithms: one to go to straight and head 6 help Tractacus determine which direction to turn: either right turn. or left. If the value measured by the sensor number 2 is greater, then the robot makes a right turn; if the value measured by the The point that the robot rotates around is known as the ICC sensor number 6 is greater, then the robot makes a left turn. – Instantaneous Center of Curvature (Figure 2). By varying the velocities of the two wheels, we can vary the trajectories that Once the direction toward which Tractacus is determined, the robot takes. Because the rate of rotation ω about the ICC then turning intensity is identified. If the meas-urement must be the same for both wheels, we can write the following difference between two sensors is lower than the bottom limit, equations: about the ICC must be the same for both wheels, then Tractacus will not turn; if it is be-tween the upper and we can write the following equations: bottom limit, then it will make a slight turn, and if it is higher then the upper limit, then Tractacus will turn substantially. 350 4 3 5 2 6 1 7 FIGURE III. THE LOCATION OF SENSORS. B. Row-end Turn A different algorithm is used to determine the end of row FIGURE IV. SAMPLE OF CURVED CROP ROWS. and make the decision turn to the next line. In order for Tractacus to realize that it has reached the end of the line, III. RESULTS sensors number 1, 2, 6 and 7 were used.
Details
-
File Typepdf
-
Upload Time-
-
Content LanguagesEnglish
-
Upload UserAnonymous/Not logged-in
-
File Pages4 Page
-
File Size-