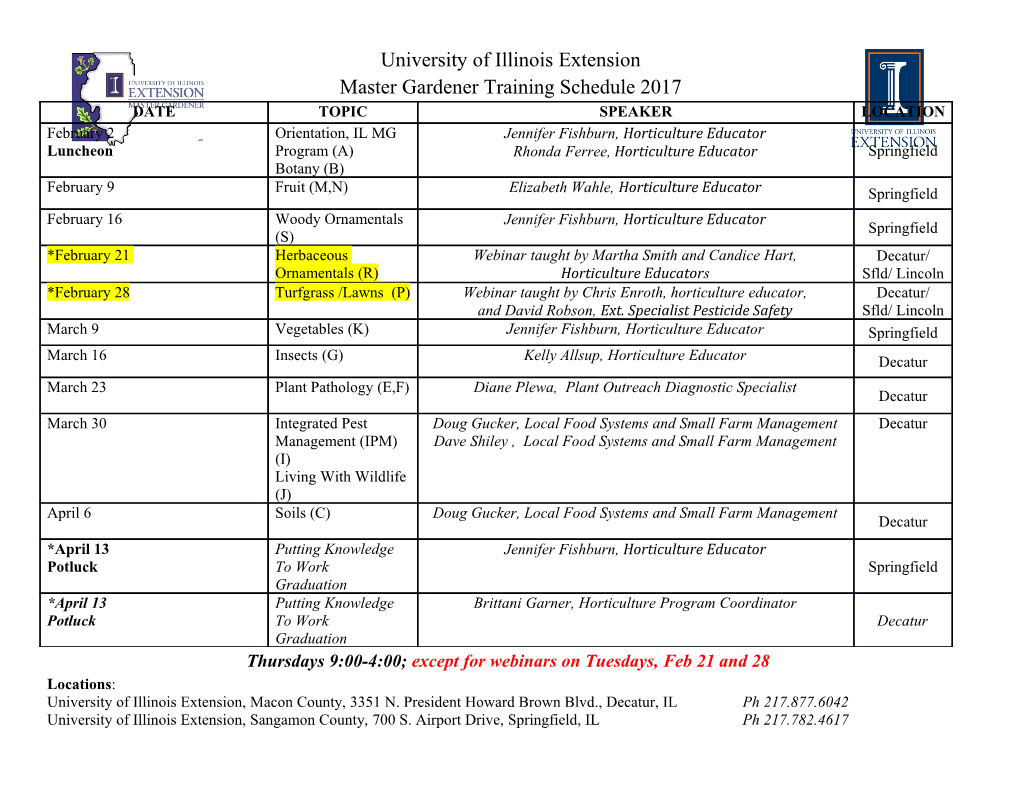
DESIGN AND ANALYSIS OF MECHANICAL ASSEMBLY VIA KINEMATIC SCREW THEORY A Dissertation Presented in Partial Fulfillment of the Requirements for the Degree Doctor of Philosophy in the Graduate School of The Ohio State University By Leonard Priyatna Rusli, M.S. ***** The Ohio State University 2008 Dissertation Committee: Approved by Dr. Anthony Luscher, Co-adviser _____________________________ Dr. James Schmiedeler, Co-adviser Co-adviser Dr. Gary Kinzel _____________________________ Dr. Krishnaswamy Srinivasan Co-adviser Graduate Program in Mechanical Engineering Copyright by Leonard Priyatna Rusli 2008 ABSTRACT The essential function of a mechanical assembly is the removal of degrees of freedom (DOF) and transfer of load between two bodies. Assemblies using integral attachments are composed of unilateral mating surfaces, where quality is greatly affected by the location and orientation of assembly features. Feature-level design is concerned with the dimension, stress, and strain of individual assembly features. This dissertation is concerned with attachment-level design, where design decisions are made on the type, location, and orientation of assembly features. Previous research in theoretical kinematics, robotic grasping, and fixture design have produced either a binary test for form closure or design optimization for a specific loading condition. There is currently no tool available to: (1) analyze an assembly‟s quality with a quantitative metric and (2) optimize the design of the assembly constraint configuration (location and orientation of features) to resist motion effectively. Therefore, the objective of this dissertation is to develop an analysis and design tool to address these needs. The analysis tool models the assembly features as wrench systems. The point, pin, line, and plane constraints in assembly are modeled with equivalent first, second, and ii third order wrench systems. The methodology used is based on composing a five-system pivot wrench combination to which a screw motion is reciprocal. The resistance effectiveness of each constraint to these motions is calculated as the ratio of the reaction forces at each resisting constraint to the input wrench magnitude. Based on these individual resistance values, a set of rating metrics is calculated to evaluate an assembly‟s quality from different perspectives. A design tool based on this analysis methodology is developed to optimize assembly design by constraint modification, constraint reduction, and constraint addition. A set of case studies is used to verify commonly known design principles, explore the design space of attachment, and understand trade-offs in assembly constraint redundancy and resistance quality. The main contributions of this dissertation are: (1) an analysis tool that is able to model assembly as kinematic constraints and calculate the load amplification ratio in the form of different rating metrics to measure assembly quality, (2) a design tool that is able to explore the design space and find optimal solutions for improving constraint effectiveness and optimize the number of constraints, and (3) an understanding of how constraint modification, reduction, and addition affect the quality of an assembly. iii Dedicated to my parents iv ACKNOWLEDGMENTS I would like to thank Dr. Anthony Luscher for his direction, insight, and advice throughout my graduate school. I learned so much about engineering design philosophy, practice, teaching, and research through working together for so many years. I‟m also thankful for his personal encouragement, sincere support, and friendship along the path. I would like to thank Dr. James Schmiedeler for giving substantial knowledge and advice in kinematics and screw theory and for his commitment in reviewing my dissertation. I would like to thank Dr. Krishnaswamy Srinivasan and Dr. Gary Kinzel for being in my committee, the financial support through my Ph.D. program, and the opportunity to coordinate the capstone design program in the department, which I really enjoy. I would like to thank my wife for being a faithful friend, for better or for worse, in good and bad times. I would like to thank my parents, brother, and sister for their love, sacrifice, and for giving me the privilege of studying in the United States. Above all else, I thank Jesus Christ for saving me and giving me the meaning of true and abundant life as he promised, and for all my dear friends and fellow leaders in the Indonesian Christian Fellowship with whom I experience what this life is all about. v VITA August 17th, 1978 Born – Jakarta, Indonesia December, 2000 B.S., Mechanical Engineering, The Ohio State University March, 2003 M.S., Mechanical Engineering, The Ohio State University September 2001-present Graduate Teaching and Research Associate, The Ohio State University PUBLICATIONS Rusli, L., Luscher, A., Sommerich, C., A Study of the Effect of Force and Tactile Feedback to Snap-fit Manual Assembly, Under Review for International Journal of Industrial Ergonomics, 2008. Rusli, L., Luscher, A., Evaluation of Rapid Prototyping Methods for Functional Testing in Snap-fits, ANTEC conference paper, 2001. FIELDS OF STUDY Major field: Mechanical Engineering vi TABLE OF CONTENTS Abstract ............................................................................................................................... ii Acknowledgments............................................................................................................... v Vita ..................................................................................................................................... vi List of Tables ................................................................................................................... xiii List of Figures ................................................................................................................... xv CHAPTER 1 Introduction to assembly design ................................................................... 1 1.1 Threaded fastener vs. integral attachment features ................................................. 1 1.2 Feature level design vs. attachment level design .................................................... 4 1.3 Assembly design and analysis tool ......................................................................... 7 1.4 Dissertation overview ............................................................................................. 7 CHAPTER 2 Literature review ......................................................................................... 10 2.1 Research in theoretical kinematics, screw theory, and extensions of screw theory ............................................................................................................................... 11 2.2 Research in analysis and synthesis of robotic grasping ........................................ 11 2.2.1 Form closure vs. force closure ..................................................................... 11 2.2.2 Form and force closure test .......................................................................... 14 2.2.3 Force distribution analysis ........................................................................... 17 2.2.4 Quantitative metric for constraint configuration.......................................... 19 2.3 Research in analysis and synthesis of fixture design ............................................ 21 2.4 Research in assembly design ................................................................................ 31 2.5 Research on constraint analysis in assembly ........................................................ 36 2.6 Summary ............................................................................................................... 37 CHAPTER 3 Overview of screw theory and applications in constraint analysis ............. 40 3.1 Overview of screw theory ..................................................................................... 40 vii 3.2 Kinematic methods for fixture configuration planning by Bausch and Youcef- Toumi [7] .............................................................................................................. 46 3.3 Constraint analysis of assembly by Bozzo [9] ...................................................... 49 3.4 Two major limitations of Bausch and Bozzo‟s model .......................................... 52 3.4.1 Modeling of line and planar constraints....................................................... 52 3.4.2 Inconsistent scaling between finite pitch screw motion and pure translation ...................................................................................................................... 55 3.5 Other minor issues with Bausch and Bozzo‟s model............................................ 57 3.5.1 Inaccurate post-processing of rating matrix ................................................. 58 3.5.2 Failure to calculate ratings for bilateral motion separately .......................... 59 3.6 Objectives and Scope of Research ........................................................................ 60 3.6.1 Assembly constraint analysis ....................................................................... 61 3.6.2 Assembly Constraint Synthesis / Design ..................................................... 62 CHAPTER 4 Modeling assembly constraints using higher order constraint model ........ 64 4.1 From contacts into constraints .............................................................................. 64 4.2 Higher
Details
-
File Typepdf
-
Upload Time-
-
Content LanguagesEnglish
-
Upload UserAnonymous/Not logged-in
-
File Pages318 Page
-
File Size-