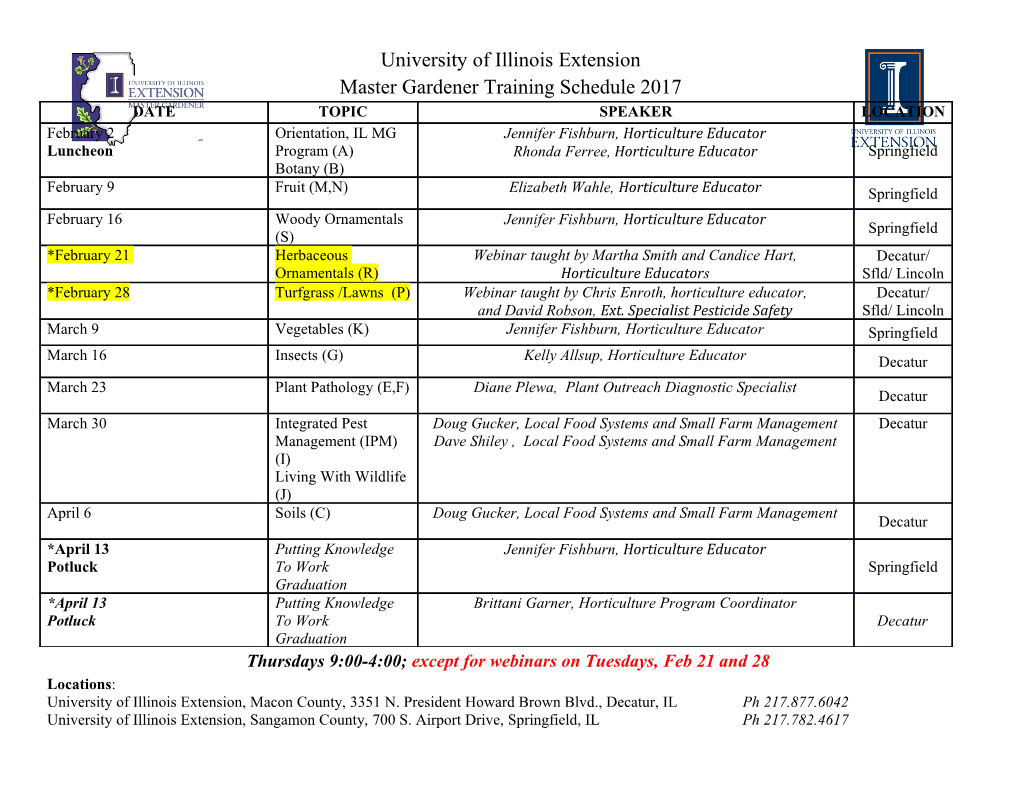
ICL TECHNICAL JOURNAL Volume 6 Issue 2 November 1988 Published by INTERNATIONAL COMPUTERS LIMITED at OXFORD UNIVERSITY PRESS iCL The ICL Technical Journal is published twice a year by TECHNICAL International Computers Limited at Oxford University JOURNAL Press. Editor J. Howlett ICL House, Putney, London SV ISW, UK Editorial Board F.F. Land J. Howlett (Editor) (London Business School) H.M. Cropper (F International) K.H. Macdonald D.W. Davies, FRS M.R. Miller G.E. Felton (British Telecom Research M.D. Godfrey Laboratories) (Imperial College, London J.M.M. Pinkerton University) E.C.P. Portman C.H.L. Goodman B.C. Warboys (University (STC Technology Ltd of Manchester) and King’s College, London) All correspondence and papers to be considered for publication should be addressed to the Editor. The views expressed in the papers are those of the authors and do not necessarily represent ICL policy. 1988 subscription rates: annual subscription £32 UK, £40 rest of world, US $72 N. America; single issues £17 UK, £22 rest of world, US $38 N. America. Orders with remittances should be sent to the Journals Subscriptions Department, Oxford University Press, Walton Street, Oxford 0X2 6DP, UK. This publication is copyright under the Berne Convention and the Inter­ national Copyright Convention. All rights reserved. Apart from any copying under the UK Copyright Act 1956, part 1, section 7, whereby a single copy of an article may be supplied, under certain conditions, for the purposes of research or private study, by a library of a class prescribed by the UK Board of Trade Regulations (Statutory Instruments 1957, No. 868), no part of this publication may be reproduced, stored in a retrieval system or transmitted in any form or by any means without the prior permission of the copyright owners. Permission is, however, not required to copy abstracts of papers or articles on condition that a full reference to the source is shown. Multiple copying of the contents of the publication without permission is always illegal. © 1988 International Computers Limited Printed by H Charlesworth & Co Ltd, Huddersfield ISSN 0142-1557 - i d TECHNICAL Contents JOURNAL Volume 6 Issue 2 Foreword E. Sweeney 205 Flexible manufacturing Manufacturing at ICL’s Ashton plant R.W. Fisher 209 Information technology in manufacturing Knowledge based systems in computer based manufacturing S. Nagarkar 219 Open systems architecture for CIM P.J. Russell 233 MAES - An expert system applied to the planning of material supply in computer manufacturing D. Saxl, R. Philips and B. Rudd 265 JIT and IT R. Westbrook 280 Computer Aided Process Planning (CAPP): Experience at Dowty Fuel Systems G. Jackson 292 Use of integrated electronic mail within databases to control processes D. A. Pass 300 Value engineering - a tool for product cost reduction S. Lynn 311 Design and manufacture of printed circuit boards ASP: Artwork specifications in Prolog E. F. Hill 321 ICL Technical Journal November 1988 i Elastomer technology for probing high density printed circuit boards C. B. Calam 336 The effects of back driving surface mounted digital integrate circuits C. J. Sherrat and R. Tomlinson 342 Reliability of surface mounted component soldered joints produced by vapour phase infrared soldering techniques H. C. Harman and C. G. Tanner 365 Materials science supporting services Materials evaluation S. R. Billington 377 Technology and human factors in industry On the human side of technology T. A. Kochan 391 Notes on Authors 401 jj ICL Technical Journal November 1988 Foreword ICL manufacturing and logistics ICL Manufacturing and Logistics (M&L) is an organisation of approxi­ mately 4000 people located on five major UK sites - in Kidsgrove (Staffordshire), Ashton under Lyne (Greater Manchester), Reading (Berk­ shire) and Letch worth and Stevenage (Hertfordshire). The Division, as part of the newly formed Product Operations, is responsible for supplying to ICL customers worldwide the full range of ICL products, whether in software or in hardware. Supplying products to customers requires an organisation that not only manufactures those products but also delivers them to the customers, either from internal manufacture of from third-party suppliers. The organisation that supports these objectives consists of five major functions: Manufactur­ ing, Systems Logistics, Purchasing, Spares and Engineering & Information Technology. Within Manufacturing, products such as terminals and DRS Personal Workstations are assembled in Letchworth, medium and large systems in Ashton and printed circuit boards, network products and software are supplied by the Component & Software organisation based in Kidsgrove. Purchasing is responsible for the procurement of all internally used commod­ ities such as silicon, peripherals, printers and terminals. System Logistics is responsible for the management of customer orders, from receipt of the order to delivery of the product, and of all ICL inventory worldwide. Worldwide Spares is responsible for ensuring that the customer support units throughout the world have the material required to service ICL customers; this organisation includes a number of product repair centres. Engineering & Information Technology (EIT) is the technical arm of Manufacturing and Logistics, responsible for setting technological direction as well as supplying a service in IT and product design. The majority of the papers in this issue of the Technical Journal are written by members of EIT staff and reflect the range of technical subjects that are of particular interest to M & L business. M & L is concerned with the manage­ ment of complex processes at controlled cost, a problem that can only be ICL Technical Journal November 1988 205 solved by the application of information technology. For this reason the Division has the largest IT spend in ICL, exceeding £10 million 1988 and covering the development costs associated with traditional Information Systems programming work, design and manufacturing integration, design productivity tools, ‘Fifth Generation’ computing and on-going systems support. It is critically important that the Division is ready to support product designers and marketing groups in the manufacture, procurement and supply of new products. Reduction of the time to market is an important competi­ tive weapon and vital to the Company’s success. To achieve this the organisation must be forward looking, and the Engineering and Information Technology Group, being responsible for Manufacturing and Logistics’ technical direction, has a particular interest in ensuring that world-class tools are available to ensure that this is achieved efficiently. I hope all this is reflected in the papers that follow. Eugene Sweeney Manager, ICL Engineering & Information Technology, Kidsgrove, Staffordshire. 206 ICL Technical Journal November 1988 FLEXIBLE MANUFACTURING Flexible m anufacturing at ICL’s Ashton plant R.W. Fisher ICL Manufacturing Operations, Ashton-under-Lyne, Manchester Abstract ICL's manufacturing plant at Ashton-under-Lyne, Manchester, as­ sembles the Series 39 mainframe and the S25 mini-computer ranges. The plant is nearing completion of an ambitious implementation of Flexible Manufacturing Systems (FMS) as the means of securing Just In Time manufacture. 1 Background An account of the first phase of the Ashton plant, the Mercury production line for the automated assembly and test of the ICL Series 39 Level 30 machine, was given in the paper by R.K. Shore in the May 1985 issue of this journal (Ref. 1). Since then the functions of the plant have been considerably extended; the present paper summaries its present state. The approach taken has been to subdivide the plant into a number of manufacturing cells based on process and size of product. Each cell is given its own control system, which ensures that the cell operates in accordance with a pre-defined inventory plan. Figure 1 is a simplified diagram showing the layout and material flow; here the box labelled “lm3 ASSEMBLY FMS” represents the original Mercury line. Products are “pulled” from the final assembly cells to meet firm customer orders. As the product kits are consumed by the assembly process the empty containers are returned to the upstream feeder cell output stores, and to MAIN STORES, for refilling. Note that there is no box labelled OUTPUT STORE - the plant does not produce complete systems for storing. There is however an output store for SUB-ASSEMBLY FMS, and the refilling of containers with product kits results in the automatic raising of manufacturing orders to restore stocks here to the planned level, where appropriate. The execution of these orders then places a demand on MAIN STORES for the replenishment of the corresponding component kit. Planned stock levels are reviewed regularly and adjusted to conform to customer requirements. ICL Technical Journal November 1988 209 Fig. 1 Plant layout and materials flow Clearly the whole process is “market driven”, in that manufacture cannot occur except in response to an actual customer order. Further, before any manufacture is initiated the system checks that all the resources are available that are needed to ensure completion. This means that Production Manage­ ment are freed from the traditional constant juggling of manufacturing schedules and reallocation of materials in line with ever-changing output forecasts. They can now concentrate on the process itself, to secure improve­ ments in quality, costs and process times. Indeed, each cell is considered a business in its own right and is measured on the level of customer service achieved from the resources employed. The lm 3 ASSEMBLY FMS and the SUB-ASSEMBLY FMS are complete; the 2m3 ASSEMBLY FMS and CABLEFORM are scheduled for comple­ tion in the autumn of 1988. As already mentioned, the first of these, the Mercury line, has been described earlier (Ref. 1); the remainder of this paper describes the SUB-ASSEMBLY FMS. 2 The SUB-ASSEMBLY FMS: Layout This is shown diagrammatically in Fig. 2. The major elements are as follows: Automatic Kit Store. Based on a horizontal carousel and incorporating a pick/place device; this is used for storing sub-assembly kits in “totes”, of dimensions 600 x 400 x 220 mm.
Details
-
File Typepdf
-
Upload Time-
-
Content LanguagesEnglish
-
Upload UserAnonymous/Not logged-in
-
File Pages201 Page
-
File Size-