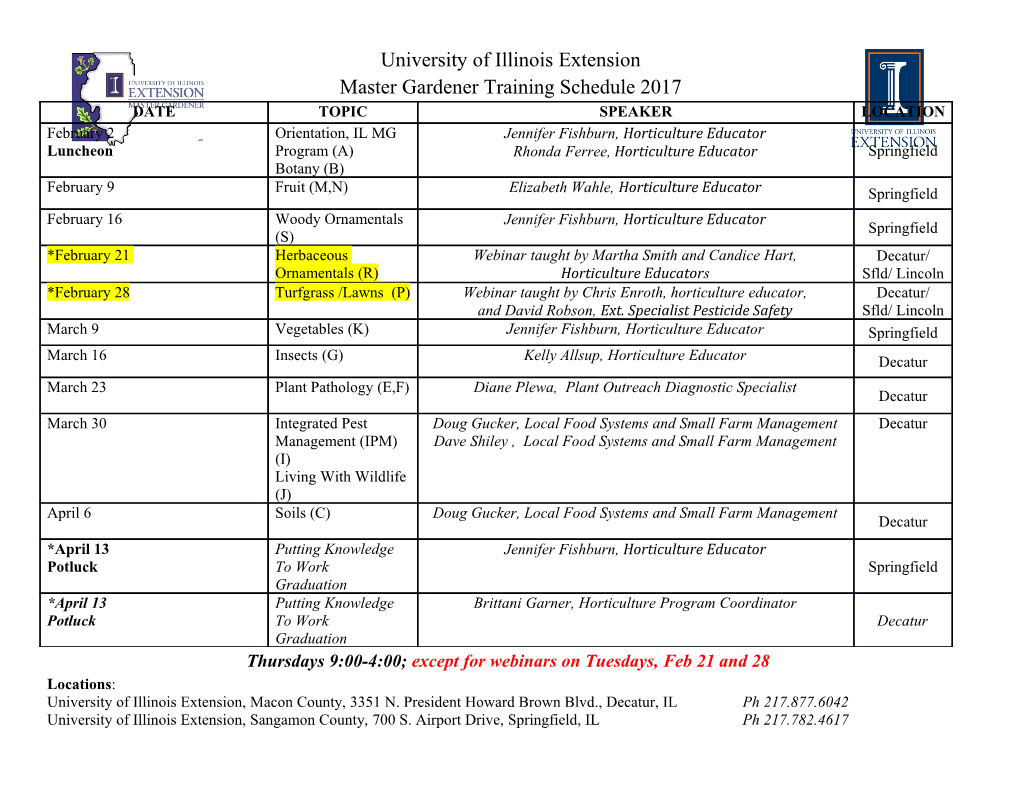
3,781,233 United States Patent Office Patented Dec. 25, 1973 1. 2 3,781,233 1 to 4 carbon atoms, hydroxyl or nitro groups or halo BLOWING AGENTS gen atoms and Erwin Muller, Leverkusen, Wolf-Dieter Wirth, Odenthal, X denotes a bond or a radical such as phenylene, naphthyl Johannes Blahak, Cologne, and Harry Rohr, Lever ene, diphenylene substituted with nitro or alkyl groups, kusen, Germany, assignors to Bayer Aktiengesellschaft, enediamine and N,N-dimethyl-N,N-dimethylene Leverkusen, Germany ylene, methylene dicyclohexylene, cyclohexylene, ethyl No Drawing. Filed May 25, 1972, Ser. No. 256,730 ene, dimethylene carbonate, N,N'-dimethylene-ethyl Claims priority, application Germany, May 26, 1971, enediamine and N,N'-dimethyl - N,N'-dimethylene P 21. 26 145.0 Int. C. C08 1/20 ethylenediamine or a radical obtained by removal of U.S. C. 260-2S R 13 Claims O two hydrogen atoms from a diphenylether or from ca as blowing agents for the production of cellular or porous ABSTRACT OF THE DISCLOSURE synthetic resin articles based on acrylonitrile, butadiene The invention relates to the use of bisbenzazimide com and styrene copolymers. pounds as blowing agents for the production of cellular The compounds according to the invention are suitable and porous articles from acrylonitrile, butadiene and for the production of foam plastics from thermoplastic styrene copolymers. The blowing agents do not liberate synthetic resins. The following are examples of com any corrosive, discoloring, malodorous or toxic decon pounds according to the invention: position products. 5,5'-dinitro-bisbenzazimide; 20 5,5'-dichloro-bisbenzazimide; This invention relates to the use of compounds of the 4,4'-dichloro-bisbenzazimide; bisbenzazimide series as blowing agents for the production 5,5'-dimethyl-bisbenzazimide; of cellular and porous articles based on acrylonitrile, 4,4'-dimethyl-bisbenzazimide; butadiene and styrene copolymers. 5,5'-isopropyl-bisbenzazimide; It is known that foam plastics can be produced from 25 4,4'-isopropyl-bisbenzazimide; thermoplastic synthetic resins by incorporating an organic 5,5'-tert-butyl-bisbenzazimide; blowing agent with the synthetic resin or by adding to 4,4'-n-butyl-bisbenzazimide; a granulate synthetic resin a blowing agent which de 5,5'-dibromo-bisbenzazimide; composes with the evolution of gas, at temperatures at 30 4,4'-dibromo-bisbenzazimide; which the synthetic resin becomes plastic. Substances be 3,3,5,5'-tetrabromo-bisbenzazimide; longing to various classes of compounds have been de 3,3,5,5'-tetrachloro-bisbenzazimide; scribed for this purpose in the literature, e.g. diazoamino 5,5'-dihydroxy-bisbenzazimide; benzenes, azo-bisisobutyronitrile, dinitrosopentamethyl 4,4'-dihydroxy-bisbenzazimide; ene tetramine, N,N'-dinitroso-N,N'-dimethyl-tetraphthal 35 bisbenzazimide. imide, azodicarbonamide and benzene sulphonic acid hy The blowing agents according to the invention may drazides (see Angewandte Chemie 64 (1952), pp. 65 also be bisbenzazimides which are obtained by joining 76). Substances belonging to these classes of compounds the two benzazimide rings through alkylene, cycloalkylene have, however, certain disadvantages which restrict their or arylene groups on the nitrogen atom in the 3-position, use as blowing agents. For example, the blowing agents 40 may liberate decomposition products which are acid or which alkylene, cycloalkylene and/or arylene groups may alkaline in reaction or are toxic; furthermore, decomposi be interrupted by aryl groups and hetero atoms, prefer tion products which have a discoloring effect may be form ably oxygen or sulphur. The following compounds are ed, which is a disadvantage, for example, in the production suitable for use according to the invention: of foam plastics from polyvinyl chlorides. In the case 45 ethylene-5,5'-dichloro-bisbenzazimide; of azodicarbonamides, which are frequently used in ethylene-3,3,5,5'-tetrachloro-bisbenzazimide; practice as blowing agents, ammonia is produced as one ethylene-5,5'-dinitro-bisbenzazimide; of the decomposition gases and causes corrosion in the ethylene-5,5-dihydroxy-bisbenzazimide; metal moulds used for the production of the foams. ethylene-5,5'-dimethyl-bisbenzazimide; Another important factor is the decomposition tem 50 ethylene-5,5'-diisopropyl-bisbenzazimide; perature at which the blowing gas required for the foam ethylene-bisbenzazimide; ing process is liberated. This decomposition temperature hexylene-5,5'-dibromobisbenzazimide; may be below or above the decomposition temperature hexylene-5,5-dinitro-bisbenzazimide; determined in the pure blowing agent, depending on hexylene-4,4'-dinitro-bisbenzazimide; the synthetic resin used or on the other substances added 55 hexylene-3,3,5,5'-tetrabromo-bisbenzazimide; to the synthetic resin. hexylene-5,5'-dimethyl-bisbenzazimide; It was an object of the invention to find blowing agents heXylene-5,5'-isopropyl-bisbenzazimide; which would not liberate any corrosive, discoloring, hexylene-bisbenzazimide; malodorous or toxic decomposition products. o,m,p-phenylene-5,5-dichloro-bisbenzazimide; This invention thus relates to the use of compounds of o,m,p-phenylene-4,4'-dibromo-bisbenzazimide; the following General Formula I 60 o,m,p-phenylene-3,3,5,5'-tetrachloro-bisbenzazimide; o,m,p-phenylene-5,5'-dinitro-bisbenzazimide; o,mp-phenylene-4,4'-dimethyl-bisbenzazimide; R^YY-x{YY-R o,m,p-phenylene-5,5'-isopropyl-bisbenzazimide; 65 o,mp-phenylene-4,4'-di-n-butyl-bisbenzazimide; N N o,m,p-phenylene-bisbenzazimide; R8 NN/ SN/ R8 naphthylene-5,5-dimethyl-bisbenzazimide; naphthylene-bisbenzazimide; R R (I) naphthylene-4,4'-dichloro-bisbenzazimide; wherein 2-nitrodiphenylene-bisbenzazimide; R-R may be the same or different and denote hydro 70 2-ethyldiphenylene-5,5-dimethyl-bisbenzazimide; gen, straight or branched chain alkyl radicals having diphenylene-bisbenzazimide; 3,781,233 3 4. 5,5'-dichloro-bisbenzazimido-diphenylether; butyl phthalate, dibutyl adipate or tricresylphosphate, (3,3,5,5'-tetrachloro-bisbenzazimido-diphenylether; lubricants or peroxides. 5,5'-dinitro-bisbenzazimido-diphenylether; The compounds of the General Formula I used ac (5,5'-dimethyl-bisbenzazimido-diphenylether; cording to the invention may be prepared by the known bisbenzazimido-diphenylether; method described in Journal f. prakt. Chemie 2, 118, pp. bisbenzazimido-diphenylsulphone; 141 and 146, in which isatoic acid anhydride is first 4,4'-bisbenzazimido-diphenylmethane; reacted with hydrazine to produce N,N'-bis-2-aminoben 4,4'-bisbenzazimido-dicyclohexylmethane; zoyl-hydrazine and ring closure to produce the required p,p'-bis-5,5'-dimethyl-bisbenzazimido-dicyclohexyl bis-benzazimide is then effected by reaction with sodium methane; nitrite. Compounds of the General Formula I may also N,N'-bisbenzazimido-urea; be obtained by first reacting isatoic acid anhydride with bisbenzazimido-dimethylenecarbonate; diamines instead of hydrazine to form bis-2-aminoben bisbenzazimido-dimethyleneethylenediamine; Zoyl compounds and then carrying out ring closure by bisbenzazimido-dimethylene-N,N'-dimethyl-ethylene reaction with sodium nitrite. diamine. 15 EXAMPLE 1. The compounds are added optionally in amounts of 0.01-30% by weight, preferably 1-10% by weight, based The following substances were applied to mixing rollers on the synthetic resin. The bisbenzazimides according to at a temperature of 150° C. and homogenized by rolling the invention may also be used in combination with for 10 minutes: known blowing agents. 20 The following mixtures of various thermoplastic poly 96.5 parts of a commercial ABS graft polymer consist mers and so-called thermoplastic polyphasic synthetic ing of 20.5% of acrylonitrile, 12.5% of butadiene and resins are mentioned as examples of thermoplastic syn 67.0% of styrene, thetic resins: Acrylonitrile-styrene-butadiene polymers; 2.5 parts of bis-benzazimide, mixtures of polysulphone and styrene-acrylonitrile or 0.5 part of calcium stearate and acrylonitrile -butadiene - styrene polymers; mixtures of 0.5 part of ionol. polycarbonate and acrylonitrile-butadiene-styrene poly The rolled sheet is size reduced and worked up into mers; mixtures of polyvinyl chloride and acrylonitrile shaped products in an injection moulding machine at 240 butadiene-styrene polymers or of polyvinyl chloride and to 260° C. The amounts fed into the machine are so ethylene-vinyl acetate copolymers; mixtures of polysty 30 calculated that the shaped products produced have a gross rene and rubbery elastic copolymers or segmental poly density of 0.7 g./cm.. These products were found to mers based on butadiene-, or styrene-acrylonitrile copoly have the following properties according to ASTM test mers with butadiene-acrylonitrile polymers. standards D 790 and D 256: In a preferred embodiment of the invention, diphasic synthetic resins are used, in which the hard phase based 35 Flexural strength: 426 kg./cm. on polystyrene or a copolymer of styrene and alkyl sty Impact strength: 24 cm. kg./cm. (Charpy 4'). rene or halostyrene is made impact resistant by modifica tion with a rubbery elastic phase based on butadiene. EXAMPLE 2 It is preferred to use diphasic synthetic resins in which the hard phase based on copolymers of styrene and/or 40 The procedure is the same as described in Example 1 alkyl styrene and/or methyl methacrylate with acryloni but using 3 parts of 5,5'-dinitro-bisbenzazimide and tem trile is rendered impact resistant by modification with a peratures of 220-240° C. A material having the follow rubbery elastic phase based on butadiene
Details
-
File Typepdf
-
Upload Time-
-
Content LanguagesEnglish
-
Upload UserAnonymous/Not logged-in
-
File Pages4 Page
-
File Size-