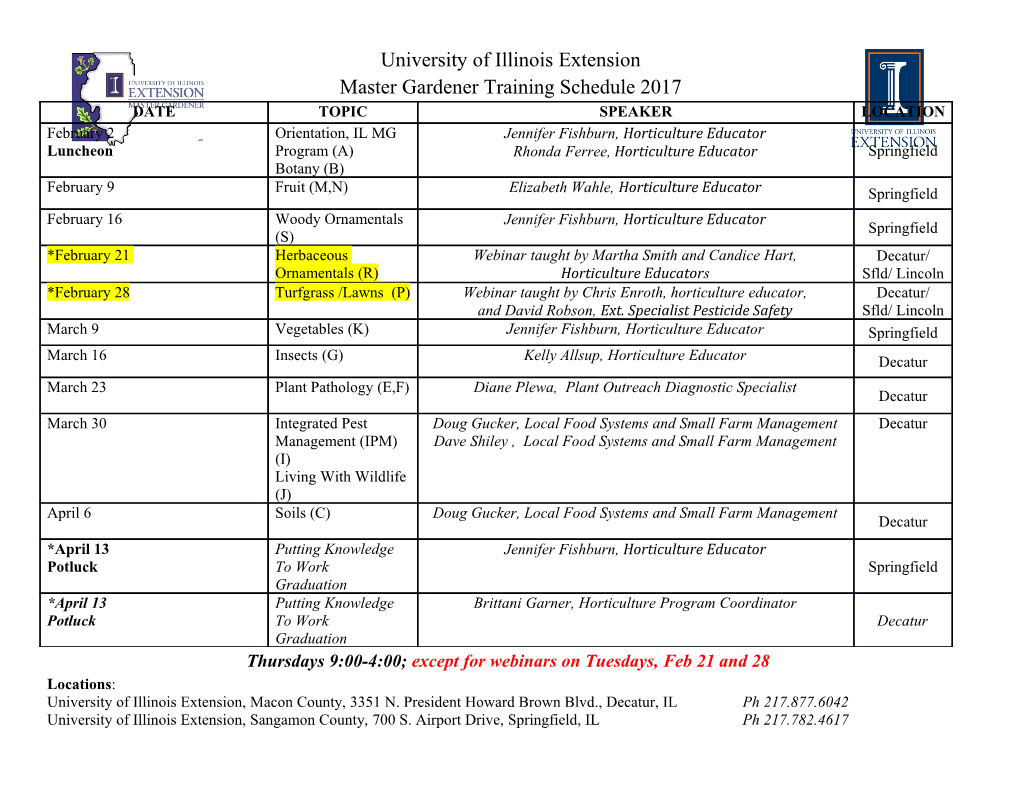
C95S4 Page 1 Project Title: Real Time Analysis And Control of Batch Dyeing Processes Project Number: C95-S4 PI(s): R. McGregor (Leader NCSU), K. R. Beck, G. K. F. Lee, C. B. Smith, W J. Jasper Graduate Students: M. S. Arora, C. E. Bright, R. P. Joshi, M. R. Lefeber Wallace, J. T. Merritt. Industrial Collaborator: W. Hunter (Cotton Inc.). Goals: The overall objective of this project is to optimize batch-dye process control by monitoring dyebaths, and by understanding and controlling the state of the dyeing process, both in the laboratory and commercial dyeing machines. Specific objectives are to: 1. Educate graduate students and advance dyeing knowledge and technology. 2. Develop neural network/fuzzy logic control for dyebath monitoring and colorant formulation. 3. Develop control systems and strategies for closed loop control via dosing, fuzzy logic and neural networks. 4. Comparatively evaluate control strategies and the absolute levels of control possible. 5. Develop useful theoretical kinetic and thermodynamic models and generic process models. Abstract: This report describes our (Dye Applications Research Group, DARG) recent progress in real-time monitoring, modeling, and controlling batch dyeing processes. The flow injection analysis (FIA) system was modified to allow injection of a small volume of dyebath into a high performance liquid chromatograph (HPLC). This FIAIHPLC system is being used to study four different procedures for exhaust dyeing cotton with reactive dyes. Data are reported for isothermal dyeings at different temperatures. Preliminary work to develop a spectrophotometric method for monitoring exhaustion of vat dyes, especially indigo, is reported. Calibration models developed from indigo powder and indigo paste under a nitrogen atmosphere indicate significant differences in the purity of the dye in these two forms. Once developed, these models will be incorporated into a FIA system for monitoring indigo in a dye range. A neural network shade matching program has been developed and is briefly described. The dye-concentration prediction of the neural network model was shown to be more accurate in predicting the actual experimental dye-concentrations than conventional linear models. Closed-loop control of acid dyeing is reported. The DARG direct dyebath monitoring system was modified to allow computerized control of dosing of acid and base for pH control, individual dye concentrations, and total sorption of each dye during the dyeing process. Relevance to NTC Goals: 1. This project has developed innovative and improved closed-loop dyeing processes based upon modern dyeing theory and modem control strategies and methods. 2. Our development of a new portable dyebath monitoring and control system will both enhance our research capabilities, and facilitate the transfer of our approach to industry. 3. The strong contacts already developed with industrial companies have been formalized through the formation of an industrial Dye Applications Research Consortium (DARC), which will transfer our results to commerce. National Textile Center Annual Report: November 1997 245 C95S4 Page 2 4. Education and training, both of graduate students and industry personnel, will be continued to ensure the future competitiveness of the industry. 5. There is a unique collaboration between textile chemists, mechanical and aerospace engineers, and textile engineers at the heart of this project, which may serve as a model for the industry. Technical Approach: Key questions: 1. Can the consistency of batch-dyeing be improved by closed-loop control? 2. What are the best modeling, control, and monitoring procedures and strategies? 3. Can these strategies be adapted for specific commercial dyeing machinery and processes? The barriers: 1. The limitations of the best existing theoretical models of the physical chemistry of dyeing. 2. The multiplicity of parameters which can influence a dyeing process, and the difficulty of monitoring and evaluating them all. 3. The proprietary natures and complex compositions of commercial dye preparations. 4. The complexity of the mass transfer processes characteristic of specific batch dyeing machinery. 5. The length of time required to develop absorbance-to-concentration models for any multi-dye system. Current state of the art: 1. Our NTC work to date represents, to the best of our knowledge, the state of the art in closed-loop-adaptive, and fuzzy-logic-based control methods for dyeing processes, and in the application of both FIA and spectral transmittance measurements for dyebath monitoring. This viewpoint is shared by the U. S. industry. We are also at the leading edge with our new developments in the use of neural nets for color matching. 2. In general, pre-developed and “pre-optimized” dyeing procedures are used without closed-loop feedback control. These are compromise procedures, for a family of dyes and a general class of fiber for example, and are not truly optimal. 3. Dyebath monitoring for dye exhaustion, if used at all, is generally based on relatively primitive methods which yield insufficient information. 4. Dosing of dyes and chemicals for process control is common, but closed-loop control of dosing appears not to be used. Dosing profiles are pre-set (See # 1 above). 5. At least one group in England has developed a computer model of the package dyeing process, which is stated to produce information on the instantaneous distribution of dye in the fibers, and in the yams and packages. The mathematics involved has not been published to our knowledge, but it is most probably a simplified model. 246 National Textile Center Annual Report: November 1997 C95-S4 Page 3 Industry Outreach: Several companies, including Milliken, Dystar, Cotton Incorporated, Datacolor International, Glen Raven, Guilford Mills, Liberty Fabrics, Ovelacq (Belgian Yarn Dyeing Company), Gaston County Dyeing Machine Co. continue to closely follow the progress of our research. We have been approached by an instrument manufacturer to consider production of our flow injection analysis system and are currently doing a dyeing project for a major fiber producer. In the past three years DARG graduates have been hired by Monsanto (now Solutia), Crompton and Knowles, Burlington Industries, Dystar, and companies specializing in control software and hardware. We expect to continue as a source of highly educated personnel for our industry. We have an excellent group of graduate students who will complete their programs in the next few years, and can help us to train their successors before they leave us. These valuable contacts and interactions will increase as this research continues, through the formation of the DARC. Current Progress: Presented here is progress in various continuing areas of research and in one new area (indigo dyeing). Optimization of Reactive Dyeing Processes Since flow injection analysis for dyebath analysis was developed by our group earlier in this project, we have continued to develop FL4 as a monitoring tool. FIA has been used to monitor reactive dyeing of cotton, direct dyeing of cotton, cationic dyeing of acrylic, and disperse dyeing of polyester and cellulose acetate. To our knowledge, our ability to monitor disperse dyeings is unique. Our FIA systems have been used to monitor dyeings on a pilot scale package dyeing machine, a laboratory beaker dyeing machine, a laboratory package dyeing machine, and a pilot scale jet dyeing machine. In the dyeing of cotton with reactive dyes, monitoring exhaustion of individual dyes has been possible since the development of our FIA system. The spectral data obtained by FIA do not contain enough information to determine the degree of hydrolysis of reactive dyes during the dyeing process. Information about hydrolysis can, however, be obtained from analysis by high performance liquid chromatography (HPLC). We have successfully merged the exhaustion monitoring capabilities of FL4 with the separation abilities of HPLC into a system that reports exhaustion data once per minute and hydrolysis data once per five minutes. This FWHPLC system is currently being used to compare the efficiencies of four different reactive dyeing processes (all-in, constant temperature, traditional, and high-temperature) involving a heterobifunctional blue dye and a heterobifunctional yellow dye. In order to monitor the hydrolysis of these dyes, an isocratic HPLC method was developed to separate the various reactive and hydrolyzed forms of the dyes. Samples of partially hydrolyzed dyes were taken to Sequa Chemicals in Chester, SC and separated by HPLC. The eluent was deposited on a rotating germanium disk, and an IR spectrum was obtained at several different points along the deposition path to match up with the chromatogram peaks. The FTIR data, in conjunction with supporting knowledge from the dyeing process and the basic principles of HPLC separation, tentatively identified the chromatogram peaks as occurring in the following order: dihydrolyzed dye, monohydroxytriazine/ P-sulfatoethyl sulfone, monochlorotriazine/ hydroxyethyl sulfone, monochlorotriazine/ P-sulfatoethyl sulfone (original dye), monohydroxytriazine/ vinyl sulfone, monochlorotriazine/ vinyl sulfone. With this information, the disappearance, production, and conversion of each form of the dyes can be followed continuously during the dyeing procedure. National Textile Center Annual Report: November 1997 247 C95-S4 Page 4 Isothermal dyeings at five different temperatures (100, 120, 140, 160, and 180 OF) were conducted in order to determine
Details
-
File Typepdf
-
Upload Time-
-
Content LanguagesEnglish
-
Upload UserAnonymous/Not logged-in
-
File Pages9 Page
-
File Size-