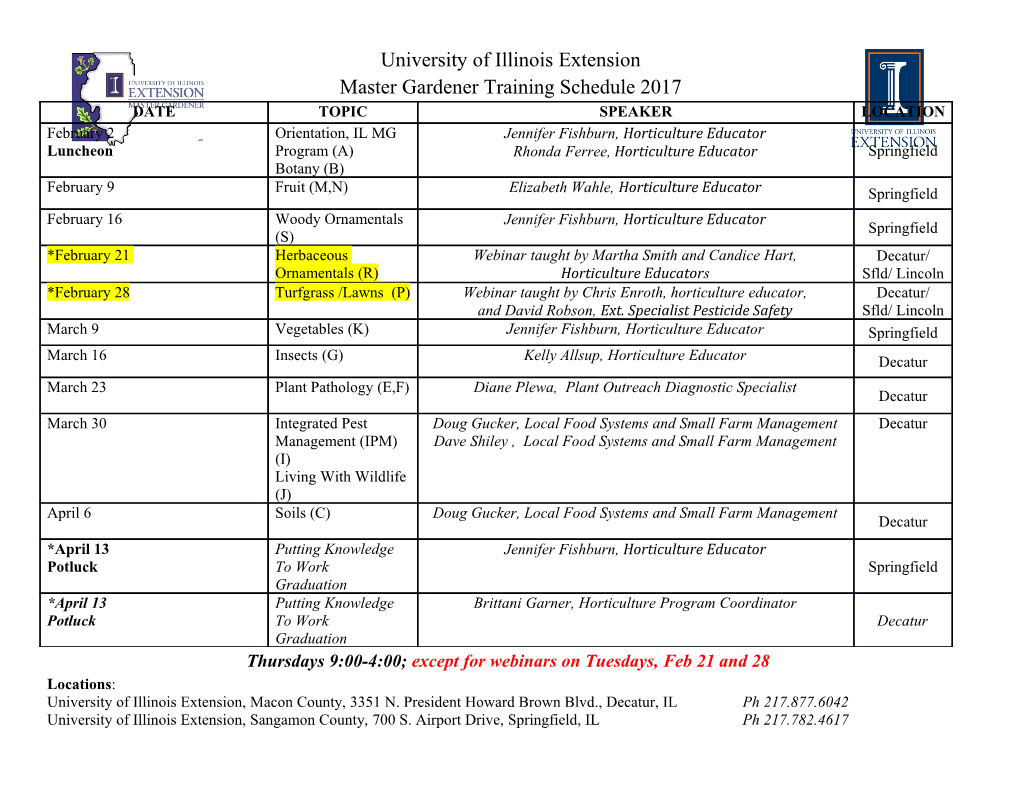
Johannes Braumann Robots in Architecture Towards New Robotic Design Tools UfG Linz Sven Stumm Using Collaborative Robots within the Creative Industry IP RWTH Aachen Sigrid Brell-Cokcan Robots in Architecture IP RWTH Aachen 1 ABSTRACT This research documents our initial experiences of using a new type of collaborative, industrial robot 1 Sensitive robotic assembly informed in the area of architecture, design, and construction. The KUKA LBR-iiwa differs from common through haptic programming. Showcased at the Hannover Fair robotic configurations in that it uses seven axes with integrated force-torque sensors and can be 2016. programmed in the Java programming language. Its force-sensitivity makes it safe to interact with, but also enables entirely new applications that use hand-guiding and utilize the force-sensors to compen- sate for high tolerances on building sites, similar to how we manually approach assembly tasks. Especially for the creative industry, the Java programming opens up completely new applications that would have previously required complex bus systems or industrial data interfaces. We will present a series of realized projects that showcase some of the potential of this new type of collab- orative, safe robot, and discuss the advantages and limitations of the robotic system. 164 INTRODUCTION Ten years ago, the use of industrial robots within architectural research was considered to be high-end, often depending on robotic engineers that worked with designers to realize projects. Today, these robots have turned into well-researched tools that can be found at many larger universities, and are also starting to leave the field of research towards full-scale applications, as demonstrated in the work of Gramazio & Kohler, Achim Menges, and others (Figure 2). 2a Companies such as Branch Technology are now basing their innovative applications on reliable robotic platforms, thus allowing them to focus on their construction-specific tasks, rather than having to develop an entire robotic system. Whereas robots are often used to perform tasks similar to existing CNC machines, our main research interest lies in the core of construction strategies and how we can advance robotic software technology to assist in assembling tasks (refer to the project section and Stumm et al. 2016). 2b 2c Currently, significant development in the area of software can be observed in our field, enabling tablet-like interaction with the control panel and new networked devices to act as a robot controller through software options like KUKA mxAutomation (Munz et al. 2016, Braumann and Brell-Cokan 2015). Within the context of architecture and design, the community of creative robot users itself has become the main enabling factor to greatly lower the entry bar for new users of robotics by exchanging ideas on the same level and providing accessible but powerful 3a 2 Architectural robotic projects: ICD/ tools such as KUKA|prc, HAL, and others. ITKE Research Pavilion 2015–16 (a), Branch Technologies (b), Echord ETH Zurich (c). Recently, we can observe changes happening within the robot industry as well, as companies are moving their focus away from 3 Save interaction with a collabo- rative robot: Compliant mode (a), traditional robot installations within safety fences towards safe collision detection (b). human-robot collaboration, while also investigating new applica- tions beyond the automotive sector. INTELLIGENT WORK ASSISTANT For this purpose, a number of robotics companies have devel- 3b oped a new generation of lightweight robotic arms such as KUKA’s LBR iiwa (intelligent industrial work assistant), with similar Furthermore, the LBR iiwa employs seven axes, enabling the “safe” machines being available from ABB (YuMi), UR, and a range robot to move the kinematic chain behind its tool, without of smaller robotic startups, building upon research such as by moving the tool itself. The additional redundant axis greatly the DLR (Albu-Schäffer et al, 2007). The iiwa (Figure 3) differs increases the robot’s kinematic flexibility, offering mathematically from the common robotic-arm template. Immediately visible is infinite possibilities to move to a defined point in space, which its design, which is optimized to reduce the potential of harming can be used to avoid obstacles, and to offset the comparably the user by minimizing the amount of sharp edges and reducing limited axis range. The force-torque sensors within every axis crushing hazards, thus making it possible to safely interact with constitute another step-change in robotic technologies, enabling the robot in a haptic way. the robot to feel and react to contact and pressure. Previously, GENERATIVE ROBOTICS 165 4 SunriseWorkbench: Defining robot topology, safety and program within the IDE and synchronizing it directly to the LBR iiwa robot. force-torque sensors for industrial robots were mostly mounted Workbench, a modified version of the open-source software directly between the tool and the flange, or the drive currents for Eclipse. In addition to making complex tasks easier to program, individual axes were used to provide only a rather coarse feed- it also greatly opens up the scope of robot programming. Rather back. Adding these sensors to every axis does not just enable than being limited to certain interfaces and tech packages, we force-sensitive applications, but makes the robot potentially safe can define custom ways of communication and interaction, e.g., to work with, as it can now feel collisions at every joint, rather using high-performance technologies developed by the game than just at the tool tip. industry for Android, which also uses Java for its apps. The sensors are not limited to a Boolean yes/no collision, but An exemplary programming workflow via Sunrise Workbench provide fine-grained data that can be used for many different (Figure 4) starts with the user creating a new Java project and applications—e.g., those that require information about contact writing the logic using the provided KUKA-specific libraries state or process force. Additionally, the robot can be moved for movements, force conditions, etc. Tools and coordinate around manually in compliant mode, which does not simply systems are also created within the Sunrise Workbench and can release the brakes of the motors, but compensates gravity be intelligently nested, so that, for example,multiple tool-tip and measures the force applied at each joint to support any coordinate systems are assigned to a single tool. Finally, safe- user-given movement. Even the weight of workpieces can be ty-specific properties are set in the Safety Configuration and the compensated in a similar fashion, so objects mounted onto the IO configuration is loaded from WorkVisual, as with regular KRC4 robot can be moved as if they weighed nearly nothing. robots. The project can now be synced with the robot, replacing the previous program. On the robot, the previously set-up tools Within the scope of architecture and design, we see a special and coordinate system now show up and can be calibrated, thus potential for interactive design parametrization and force-guided matching the digital environment with the actual physical space. assembly, which is further discussed in the project section. The next synchronization between robot and IDE then pushes these changes back into the Workbench. A simulation in advance Robot as an App is not possible, only syntax errors are checked and highlighted. While similar applications have been possible before, the iiwa’s new programming provides accessible libraries that allows the Initial Experiences creative user to utilize these features at a high level without As the iiwa robot has only recently been introduced and is priced needing external data processing or specialized software. comparatively high, we could not build upon the knowledge of many other, creative robot users. For example, applications in the Unlike previous LBR iterations such as the LBR4, which relied creative industry are robotic scale model testing at the BRG/ETH on the regular KUKA Robot Language (KRL), the iiwa introduced Zurich (2016) and camera motion control for movies at CMOCOS SunriseOS, which uses Java as the robot’s programming language. (Shepherd and Buchstab 2014). The findings below represent This allows us to use state-of-the-art programming strategies, our initial conclusions and subjective evaluation after slightly less such as object-oriented programming, and most importantly, to than a year of using iiwa robots. implement external libraries that range from geometric functions to image processing and cloud networking. As an integrated • Acceptance: While negative connotations for robotic arms development environment (IDE), KUKA provides the Sunrise are common, the design of the iiwa seemed to greatly 166 Towards New Robotic Design Tools Braumann, Brell-Cokcan, Stumm increase public acceptance as it distanced itself from regular either put multiple commands into a MotionBatch, or execute industrial robots, while also not too directly emulating human motiontasks asynchronously, both of which caused problems arms. People were quick to interact with the iiwa without with very large, complex toolpaths. Troubleshooting is further hesitations or safety concerns, while students were curious to complicated by the fact that the only feedback provided work with a new machine. on the robot control panel are console messages as well as exceptions. While the older KRC4 controller presents the user a pointer at the currently active line, SunriseOS only allows • Mechanics: Immediately noticeable is the iiwa’s low weight the user to step through a program if a debugging process is of less than 30 kg, which makes it significantly easier to started through the Sunrise Workbench from a remote PC. move and set up than, for example, 50 kg Agilus robots. At Any kind of “block selection” has to be programmed in Java, the same time, the larger iiwa can manipulate up to 14 kg, e.g., through a custom debugging interface. while the Agilus series currently tops out at 10 kg, resulting in a very favorable weight to payload ratio.
Details
-
File Typepdf
-
Upload Time-
-
Content LanguagesEnglish
-
Upload UserAnonymous/Not logged-in
-
File Pages10 Page
-
File Size-