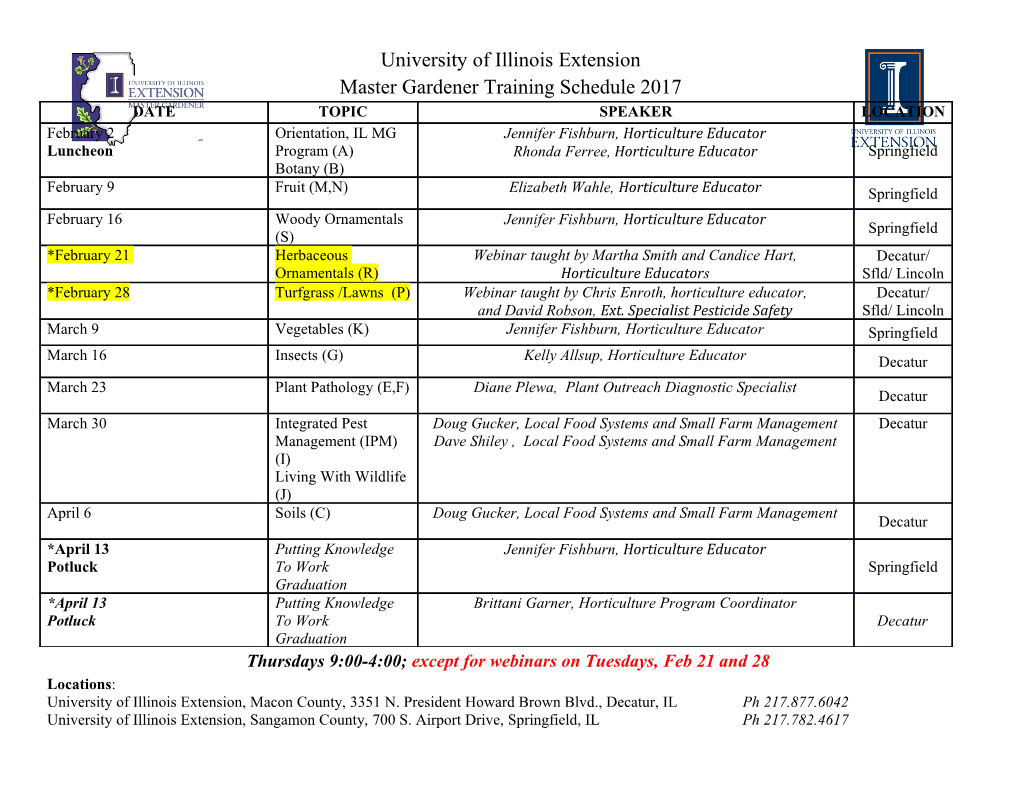
2,971,011 United States Patent Office Patented Feb. 7, 1961 2 scription of this invention is set forth in detail herein after. 2,971,011. Although the literature teaches a decomposition tem PROCESS OF PREPARING TREMELLITIC perature for trimellitic acid of 216 C., it has now ANHYDRDE been discovered that trimellitic acid may be dehydrated to trimellitic anhydride at a rapid rate at temperatures Hsiang P. Liao, Park Forest, and Philip H. Towle, Chi. as low as 170° C. by heating in the presence of a cago, I., assignors to Standard Oil Company, Chicago, moving inert gas stream to carry away water vapor. The Ill., a corporation of Indiana dehydration temperature should not, however, exceed No Drawing. Filed Feb. 27, 1958, Ser. No. 717,825 0 250 C. in order to avoid color degradation of the anhy dride. The moving inert gas stream may either be 9 Claims. (C. 260-346.3) an inert, i.e. anhydride nonreactive, noncondensible gas Such as nitrogen or it may be vapors generated in situ by refluxing an inert water-immiscible relatively volatile This invention relates to trimellitic acid anhydride and 5 liquid such as a hydrocarbon. Dehydration at these more particularly is concerned with an improved process conditions, however, is not complete and hence the for the preparation of high purity trimelitic anhydride anhydride must be separated from the mixture of tri from trimellitic acid. The invention has particular ap mellitic anhydride and acid. It has also been discovered plicability when the trimellitic acid has been produced by that, while trimellitic anhydride is very soluble in aro the oxidation of a 1,2,4-aliphatic-substituted benzene 20 matic hydrocarbons, neither the acid nor any oxidation with molecular oxygen in the liquid phase and in the catalysts dissolve to any appreciable extent. Thus, presence of a heavy metal catalyst. partial dehydration in the presence of an inert gas, Trimelitic acid, the 1,2,4 benzene tricarboxylic acid, followed by extraction with an aromatic solvent, is is useful as an intermediate in the production of quality capable of producing high purity trimelitic anhydride plasticizers and polyester resins. For these application, without the use of either chemical dehydrating agents in which trimellitic acid is esterified with a monohydric or vacuum distillation. If required to provide a trimei or a polyhydric alcohol, the evolution of water as an litic anhydride product having a specified maximum TEG esterification byproduct together with the attendant dif color, the anhydride-aromatic solution may be treated ficulty of eliminating water from esterification reaction with activated carbon to remove color bodies before re mixtures favors the desirability of employing trimelitic 30 covering high purity trimelitic anhydride. acid as the anhydride rather than as the acid. Resins Crude trimellitic acid may be prepared by the oxida and plasticizers may further require a trimelitic anhy tion of various 1,2,4-aliphatic-substituted benzenes by dride which is relatively free from color bodies and also way of Several known routes. Chemical oxidizing agents free from the heavy metals employed as catalysts for Such as nitric acid, chromic acid, potassium permanganate the air oxidation of aliphatic-substituted benzenes to 35 and the like can oxidize a tri-alkylbenzene such as produce trimellitic acid. A TEG (Tri-Ethylene Glycol pseudocumene directly to trimelitic acid. Rather than esterification) color of below 500 is often specified for use chemical oxidizing agents, molecular or gaseous oxy trimelitic anhydride used in white or transparent resins, gen may be employed to effect a liquid phase oxidation and a metal content of less than about 50 p.p.m. (parts of an aliphatic-substituted benzene in the presence of per million) is desirable to achieve good color and oxida 40 a heavy metal oxidation catalyst such as cobalt or man tion stability. While the more commonly employed ganese. In this manner, 1,2,4-triisopropyl benzene is maleic and phthalic acid anhydrides are readily prepared oxidized to trimellitic acid. Another process involving by thermal dehydration of the corresponding acids, and molecular-oxygen oxidation is the heavy-metal-catalyzed the anhydrides are easily purified by atmospheric pres liquid phase oxidation of pseudocumene by repeatedly sure sublimation, trimellitic anhydride cannot be proc 45 oxidizing one methyl radical to a carboxyl group, esteri essed in this manner. Firstly, the acid requires tem fying that carboxyl group with a lower alkanol, and peratures in excess of 200 C. for thermal dehydration oxidizing anther methyl radical on the intermediate to to take place, and even at these temperatures dehydra another carboxyl group, followed by hydrolysis of the tion is not complete. Secondly, trimelitic anhydride is dialkanol ester of trimellitic acid to trimelitic acid. A essentially nonvolatile and must be distilled at tempera 50 more direct preparation is the one step oxidation of a tures above 250 C. under vacuums on the order of trialkylbenzene such as pseudocumene with molecular 10-60 mm. mercury absolute to prevent color degrada oxygen in an inert liquid medium at about 150-250° C. tion. Also, to increase the ordinarily-slow rate of dehy employing a catalyst comprising, in conjoint presence, dration, it has previously been proposed to employ a heavy metal oxidation catalyst and bromine. Suit chemical dehydrating agents such as acetic anhydride, 55 able metal catalysts are selected from metals having sulfuric acid, phosphorus pentoxide, or the like to de atomic numbers of 13, 21-32, 39-51, 57-84 all in hydrate the last traces of trimellitic acid before distill clusive, and the actinide earths, and may be added either ing the anhydride. These chemical dehydrating agents in elemental form or as a soluble compound such as are costly to recover and regenerate, and consequently cobalt chloride, iron acetate, ammonium chromate, man h impose an expensive operating burden on existing proc 60 ganese acetyl acetonate, or the like. Likewise, bromine esses for the purification of trimelitic anhydride. Fur may be added as elemental bromine, HBr, sodium thermore, their use in some cases results in the substitu bromide, nickel bromide, benzyl bromide, etc. Trimel tion of one impurity for another. litic acid yields from the air oxidation of pseudocumene Accordingly, an object of the present invention is to in the presence of a heavy metal oxidation catalyst and provide an improved process for preparing high purity 65 bromine are in excess of 120 weight percent. trimellitic anhydride from trimellitic acid without the In all of the foregoing oxidation processes, a crude trimelitic acid is obtained from the reaction mixture by need for chemical dehydrating agents and without the physical means such as filtration, extraction, evaporation, use of vacuum distillation. A further object is to ob or distillation. This crude acid however is contaminated tain a trimelitic anhydride having a TEG color below 70 with highly colored yellowish or tan-colored tar-like oxi 500 and a metal content below 50 p.p.m. Other and dation byproducts and, where the oxidation is effected in more particular objects will become apparent as the de the presence of heavy metal catalysts, contains trimel 2,971,011 3. 4. litate salts of the heavy metals. Both of these contam weight of the water-immiscible reflux liquid to the tri inants must be removed prior to employment of the tri mellitic acid prior to heating, and refluxing the entire mellitic anhydride in the preparation of polyester resins quantity of non-aqueous distillate as fast as it is con and plasticizers. As noted previously, while phthalic densed. Larger amounts of an initially added reflux may acid and maleic acid can be purified simply by thermal 5 of course be employed but from 2 to 8% by weight of dehydration followed by atmospheric pressure Sublima an alkylbenzene on trimellitic acid dehydrates more than tion of the volatile anhydrides, trimelitic acid is con 90% of the trimellitic acid within less than one-half siderably more difficult to dehydrate and the anhydride hour at 200-230° C., and often is 90% effective within is essentially nonvolatile. 15 minutes. Larger amounts are not harmful but im In heating trimelitic acid to form trimelitic anhy O pose a greater heating burden on the dehydration System dride, it has been reported that decomposition does not while not substantially increasing the dehydration rate. take place until a temperature of about 216 C. is reached The dehydration vessel may be conveniently, an en ("Handbook of Chemistry and Physics,” p. 1083, Chem closed reboiler or tank or simple still adapted for uni ical Rubber Publishing Co., Cleveland, 1947; Beilstein's form indirect heating of the trimellitic acid by such means Handbuch gives values ranging from 216 up to 238 as gas or oil flame or by circulating a hot silicone or C.), but heating at that temperature for prolonged pe mixture of diphenyl and diphenyl oxide fluid through a riods may cause color degradation of the anhydride. heating coil or jacket. Since neither trimeilitic acid nor However, when according to the practice of the present the anhydride has an appreciable vapor pressure at de invention a moving gas stream is provided to carry away hydration temperatures, it is unnecessary to provide frac the water vapors, partial dehydration is effected at tem 20 tional distillation trays or plates in the vessel. If any peratures as low as about 170° C., and at 200-230 C, anhydride does distill, it may be washed back with the more than 90% of the acid may be dehydrated in less liquid reflux. A distillate condenser and receiver is than one-half hour. Although the dehydration may be necessary when a volatile water-immiscible liquid reflux conducted at pressures ranging from as little as one-half is employed in order to separate and reflux the water atmosphere to as much as five atmospheres or more, a 25 immiscible liquid.
Details
-
File Typepdf
-
Upload Time-
-
Content LanguagesEnglish
-
Upload UserAnonymous/Not logged-in
-
File Pages6 Page
-
File Size-