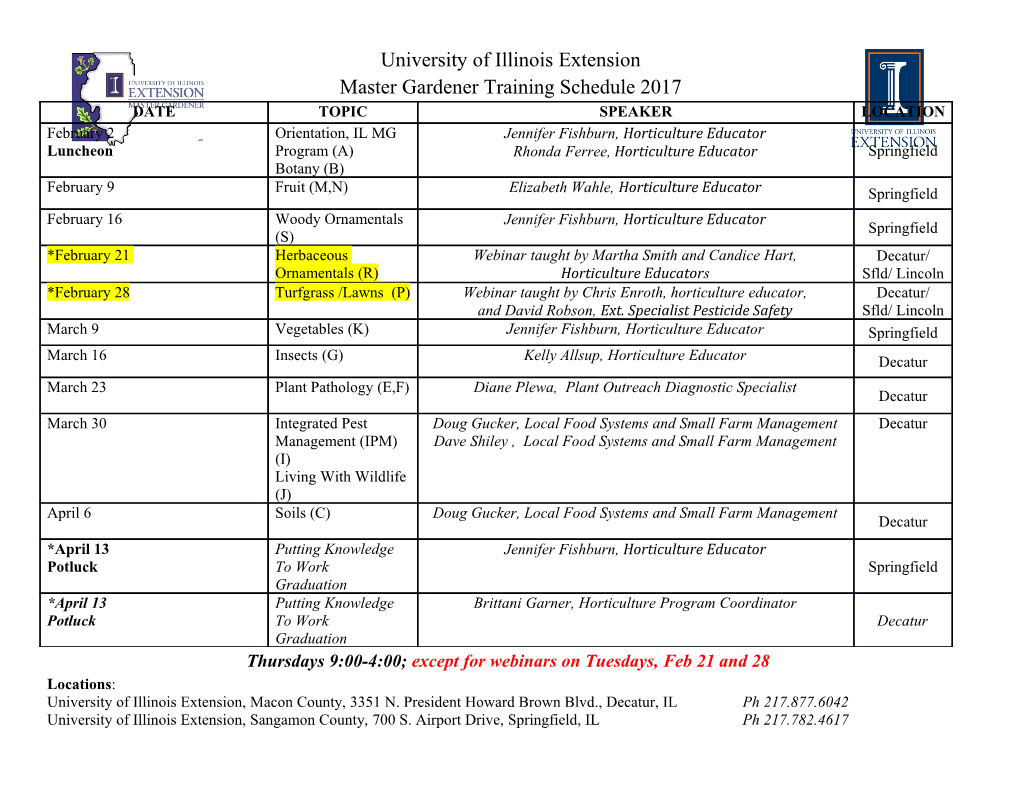
PRELIMINARY ANALYSIS OF AN INNOVATIVE ROTARY DISPLACER STIRLING ENGINE AmirHossein Bagheri Thesis Prepared for the Degree of MASTER OF SCIENCE UNIVERSITY OF NORTH TEXAS 'HFHPEHU 2015 )VTFZJO#PTUBODJ .BKPS1SPGFTTPS 4FJGPMMBI/BTSB[BEBOF $PNNJUUFF.FNCFS 1IJMMJQ3'PTUFS $PNNJUUFF.FNCFS "[J[F"LDBZPHMV $PNNJUUFF.FNCFS Bagheri, AmirHossein. Preliminary Analysis of an Innovative Rotary Displacer Stirling Engine. Master of Science (Engineering Technology- Mechanical Systems ), December 2015, 53 pp., 5 tables, 29 figures, references, 27 titles. Stirling engines are an external combustion heat engine that converts thermal energy into mechanical work that a closed cycle is run by cyclic compression and expansion of a work fluid (commonly air or Helium) in which, the working fluid interacts with a heat source and a heat sink and produces net work. The engine is based on the Stirling cycle which is a subset of the Carnot cycle. The Stirling cycle has recently been receiving renewed interest due to some of its key inherent advantages. In particular, the ability to operate with any form of heat source (including external combustion, flue gases, alternative (biomass, solar, geothermal) energy) provides Stirling engines a great flexibility and potential benefits since it is convinced as engines running with external heat sources. However, several aspects of traditional Stirling engine configurations (namely, the Alpha, Beta, and Gamma), specifically complexity of design, high cost, and relatively low power to size and power to volume ratios, limited their widespread applications to date. This study focuses on an innovative Stirling engine configuration that features a rotary displacer (as opposed to common reciprocating displacers), and aims to utilize analytical and numerical analysis to gain insights on its operation parameters. The results are expected to provide useful design guidelines towards optimization. The present study starts with an overview of the Stirling cycle and Stirling engines including both traditional and innovative rotary displacer configurations, and their major advantages and disadvantages. The first approach considers an ideal analytical model and implements the well-known Schmidt analysis assumptions for the rotary displacer Stirling engine to define the effects of major design and operation parameters on the performance. The analytical model resulted in identifying major variables that could affect the engine performance (such as the dead volume spaces, temperature ratios and the leading phase angle). It was shown that the dead volume could have a drastic effect over the engine performance and the optimum phase angle of the engine is 90o. The second approach considers a non-ideal analytical model and aims to identify and account the main sources of energy losses in the cycle to better represent the engine performance. The study showed that the ideal efficiency and the non-ideal efficiency could have 15% difference that could have as an enormous effect on the engine performance. Copyright 2015 by AmirHossein Bagheri ii ACKNOWLEDGEMENT To my beloved parents, sisters, their sons and their husbands and to those who are always concerned of me. iii Table of Contents 1 INTRODUCTION ............................................................................................................ 1 1.1 Motivation ................................................................................................................. 1 1.2 Objectives ................................................................................................................. 2 1.3 Approach ................................................................................................................... 3 2 LITERATURE REVIEW ................................................................................................. 4 2.1 An Overview of the Stirling Cycle and Engines ....................................................... 4 2.1.1 Stirling Cycle ..................................................................................................... 4 2.1.2 Stirling Engines ................................................................................................. 5 2.1.3 Traditional Stirling Engine Configurations ....................................................... 8 2.1.4 Rotary Displacer Stirling Engine Configuration ............................................. 12 2.2 Past and Recent Studies .......................................................................................... 17 3 ANALYTICAL METHODS .......................................................................................... 20 3.1 Ideal Analytical Model ........................................................................................... 20 iv 3.2 Non-Ideal Analytical Model ................................................................................... 30 4 RESULTS AND DISCUSSIONS .................................................................................. 36 4.1 Ideal Analytical Model ........................................................................................... 36 4.2 Non-Ideal Analytical Model ................................................................................... 44 5 CONCLUSIONS ............................................................................................................ 50 5.1 Remarks .................................................................................................................. 50 5.2 Recommendations for Future Work........................................................................ 51 REFERENCES ............................................................................................................................. 52 v List of Figures Figure 2-1: A Stirling cycle processes [3]. ..................................................................................... 5 Figure 2-2: Major components of the Alpha configuration of a Stirling engine [1]. ...................... 9 Figure 2-3: The Beta configuration of Stirling engines [1]. ......................................................... 10 Figure 2-4: The Gamma configuration of Stirling engines [1]. .................................................... 11 Figure 2-5: Major components of a Rotary Displacer Stirling Engine in exploded view. ........... 13 Figure 2-6: Halved view of the displacer housing. ....................................................................... 14 Figure 2-7: Segment schema. ........................................................................................................ 15 Figure 2-8: Displacer housing filled with segments. .................................................................... 15 Figure 2-9: Rotary displacer Stirling engine valve mechanism. ................................................... 16 Figure 3-1: Schematic design of Stirling engines with rotary displacers ..................................... 21 Figure 3-2: Pressure volume schematic diagram. ......................................................................... 29 Figure 3-3. The schematic of a Stirling engine considering losses {Formosa, 2010 #116}. ........ 30 Figure 3-4. General scheme of a rotary displacer Stirling engine. ............................................... 31 vi Figure 3-5. The simple mechanism of a power piston. ................................................................. 33 Figure 4-1. Volume vs. crank shaft angle during one completed cycle. ....................................... 37 Figure 4-2. Pressure vs. crank shaft angle for one complete cycle when Tc = 373 K and Th = 923 K. ................................................................................................................................................... 38 Figure 4-3. Pressure vs Volume at different phase angles when Tc = 373 K and Th = 923 K. ..... 40 Figure 4-4. Comparison between P-V diagrams of the prototype for different hot side temperatures at a constant cold side temperature (373 K) and phase angle of 90o. ...................... 40 Figure 4-5. Generated work comparison with the phase angle at different values of temperature ratio and cold side temperature of 323 K. ..................................................................................... 41 Figure 4-6. Generated work vs. temperature ratio at different cold side and hot side temperatures at the phase angle of 90o ............................................................................................................... 42 Figure 4-7. Work ratio vs shuttled volume ratio at different dead volume ratios at ൌ ͵͵ and ൌ ͻʹ͵. ........................................................................................................................... 44 Figure 4-8. Reynolds variation vs. frequency in the connecting ports. ........................................ 46 Figure 4-9. Pressure drop over the mean pressure vs. temperature ratio at different frequencies. 47 Figure 4-10. Output power vs. Temperature ratio at different frequencies when ൌ ͵͵. 48 vii Figure 4-11. Mechanical efficiency vs. Temperature ratio at different frequencies when ൌ ͵͵. ......................................................................................................................................... 49 viii List of Tables Table 4-1. Geometrical features of the prototype engine. ............................................................ 36 Table 4-2. Volume ratios of the prototype engine. ....................................................................... 36 Table 4-3.
Details
-
File Typepdf
-
Upload Time-
-
Content LanguagesEnglish
-
Upload UserAnonymous/Not logged-in
-
File Pages64 Page
-
File Size-