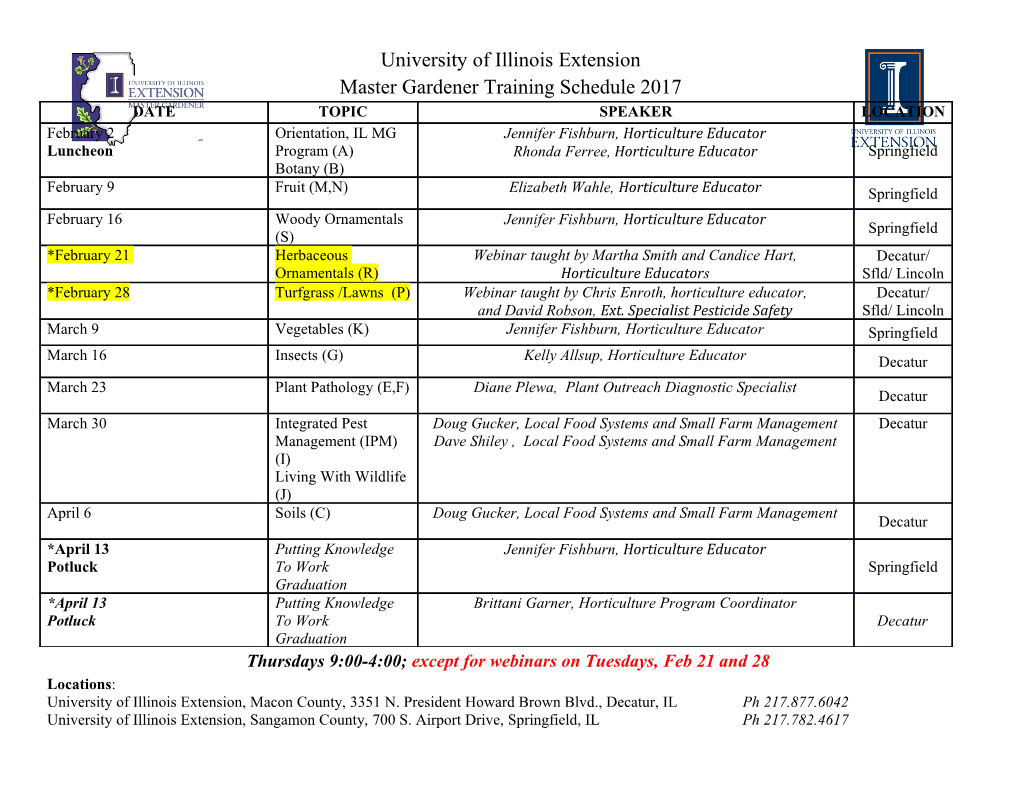
Comparison of erosion-corrosion behaviour of hot isostatically pressed and welded stellite coatings by M. Wong-Kian *, L.A. Cornisht, and A. van Bennekomt Synopsis Introduction Stellite coatings are advantageous for use in erosion-corrosion environments, and can even samples qffour different In certain environments, either where two moving function at relatively high temperatures. This is stellite materials were surfaces come into contact or where there is prepared by either hot because wear resistance is promoted by the impingement of a slurry onto a surface, wear is isostatic pressing (HIP) harder complex carbides of chromium and qf the powder or tung- unavoidable. There is usually progressive tungsten, while corrosion resistance is enhanced sten inert-gas welding deterioration of the surface resulting from the by the presence of cobalt in the matrix. The qfrod onto a 316L removal of material by at least one of the specifications for some common stellite alloys stainless-steel substrate. following mechanisms: abrasion, erosion, and are presented in Table I. Cobalt is resistant to The samples were sub- erosion-corrosion. Additionally, forms of jected to a series qf sulphuric, nitric, and phosphoric acids, but corrosion may occur locally to exacerbate the comparative erosion- vulnerable to attack by hydrochloric acid. This is corrosion tests, and damage. Wear reduces the working efficiency of because the more reducing acid attacks the generallY the HIpped an operation, and results in increased running chromium oxide passive layer. samples experienced costs due to repairs and replacement, which Most cobalt-based alloys possess good between 13 and 24 per include both new components and time lost for cavitation resistance, and moderate abrasion and cent less loss in mass refitting or repair. slurry erosion resistance. The last two features than the equivalent Wear is a surface effect, and can be hindered are independent of the carbon content, and have welded alloys. by the addition of a wear-resistant surface. An Resistance to been attributed by Crook2 to crystallographic erosion-<:orrosion advantage of this approach is that the original, transformation, under stress, from the fcc to the increased with increas- and usually economic, method of component hcp structure by twinning. During the transfor- ing carbon, chromium, manufacture can often be retained, with the mation' energy is absorbed, and the effect of the and tungsten contents. coating applied last. Additionally, the best stress is decreased2. Dilution of the cobalt Metallographic studies materials for protecting the surfaces are usually content is detrimental, because the fee structure indicated the dffferences hard, and hence brittle, and are thus not suitable in carbide content is stabilized, so that the twinning transformation between the different for the manufacture of the entire component. is hindered. Except for Bester and Bal13,most stellite materials, and Although an understanding of the various authors deal with erosion and corrosion effects the dffferences in mor- mechanisms of surface protection has increased separately, and do not address the likely phology between the greatly, allowing better coatings to be designed, synergistic effects between these two destructive HIpped and welded there is still a tendency for older methods, to be mechanisms. samples. Finer and more used because they are more familiar and thus homogeneous micro- more readily accepted by industry!. structures were South African industry benefits from the prolonged life of components due to the application of surface coatings. Examples of these applications include valves, impellers, and ducts. Debex CarbideDivision, P.O. Box 11178, Selcourt 1567. Table I t School if Process and Materials Engineering, Specifications for stellite alloys University if the Witwatersrand, Private Bag 3, WITS 2050. @ The South JYrican Institute if Mining and Metallurgy, 1995. SA ISSN oo38-223X/3.oo + 0.00. Paper received Feb. 1995; revised paper received Aug. 1995. .Specified maximum The Journal of The South African Institute of Mining and Metallurgy NOVEMBER/DECEMBER 1995 319 .... Comparison of erosion-corrosion of stellite coatings observed in the HIpped Erosion-corrosion can be defined as an The substrate beneath a coating is also spedmens. These trends acceleration in the deterioration of a surface due important. There must be sufficient adhesion to were also observed in to the combined attack of erosion and corrosion provide adequate strength during service, but the the wear surfaces. mechanisms. Metal is removed as dissolved ions, reaction between coating and substrate must be Hardnesses increased with increas- or as a corrosion product. The deleterious minimal. Usually a reaction promotes the forma- ing carbon content, and synergistic effect of the erosion removes either tion of brittle intermetallic compounds along the resulted in decreasing the corrosion product or the passive layer that is fusion boundary, which is deleterious to the absorbed impact protecting the underlying surface. Surfaces that performance of the alloy. During welding energies. have experienced erosion-corrosion often show a processes, a liquid reaction can cause dilution Tensile testing qf directional distribution of grooves or waves, effects, which are changes in composition due to the HIpped diffusion especially when the wear component is dominant. bond between the stel- the mixing of the coating and the underlying lite and 316 L stainless The rate of mass loss is considerably enhanced substrate. Dilution effects can also occur when steel produced variable in an erosion-corrosion environment, compared there is a large amount of diffusion. They can results, with an esti- with an environment of static corrosion. alter both the chemical and the physical proper- mated bond strength qf When a passive layer is removed, the time ties, such as corrosion and wear resistance, and 400 to 500 MPa. taken for its re-formation is an important are thus an important consideration. The coeffi- consideration in the assessments of wear rates. cients of expansion of the substrate and coating A layer that takes a longer time to re-form does should also be considered because too large a not provide as good a protection against difference can cause excessive residual stresses. corrosion as one that re-forms rapidly. The performance of a coating must be tested Factors affecting wear rates during erosion- under its manufacturing conditions, even though corrosion in a slurry environment include the bulk data may be available, since its size and shape of the particles in the slurry, and performance depends not only on its material their direction of impingement; the velocity and properties, but also on its thickness and the turbulence of the slurry; and the corrosiveness of mode in which it was deposited. For example, a the liquid. The interrelationship of these factors welded coating invariably has an as-cast is complex: for example, increased velocity of the structure, and some liquid mixing with the slurry particles can increase the wear rates as a substrate is sure to result, which may alter the result of the removal of more material, or the properties. Conversely, the properties of a opposite can occur if potential sites of crevice sprayed coating may be impaired by the presence corrosion are removed. of residual stresses. The quality and properties of coatings are Tungsten inert-gas (TIG) weldingusually affected by the method of manufacture. Welding employs a filler in rod form, and the process can is relatively cheap and quick, but the coating is be manual or automated. The coating thickness not homogeneous, owing to the as-cast structure attained can be varied from 2 to 10 mm, and and its inherent segregation, and hence the between 5 and 15 per cent dilution should be properties are not optimized. Another disadvan- expected. Stellites are vulnerable to dilution tage is that only components of simple shape can effects, since the change in the cobalt content of be welded, because of the problem of distortion. the surface decreases the corrosion resistance. Thermal spraying techniques can easily be applied This problem is partially solved by the use of on complex shapes, and can be used to produce multiple passes so that dilution in the outermost various thicknesses of coating. However, the weld beads is less than in the inner beads. A thicker coatings can be vulnerable to failure from good bond is formed, and the work pieces have residual stresses within the coating. In a process good resistance to thermal and mechanical used by Debex Carbide Division, stellite powder shock. An additional benefit is that re-surfacing is hot isostatically pressed onto the substrate and repair are easy. surface. The process is highly controlled, in terms of both time and temperature, and produces more homogeneous and finer microstructures. Owing to the better control. the properties of these coatings are expected to be much better than those produced via the traditional welding route. ~ 320 NOVEMBER/DECEMBER 1995 The Joumal of The South African Institute of Mining and Metallurgy ------ ---- Comparison of erosion-corrosion of stellite coatings Hot isostatic pressing (HIP) is a much newer The application of pressure during HIP allows technique, and its use to provide a wear-resistant for shorter times at elevated temperatures, as surface is even more novel. In normal use, the well as lower temperatures for full densification. technique can be employed to promotepowder This also means that the times at elevated consolidation, diffusion bonding, and the healing temperatures are limited, so that grain growth of casting defects. As used to produce a diffusion- and precipitate re-distribution are limited, and bonded coating, it has none of the deleterious mechanical properties such as toughness and effects of welding, which include unhomogeneity yield stress are retained. The combination of (segregation), dilution effects, and the risk of powder -metallurgy variables with those of HIP distortion. The diffusion bonding in HIP occurs allows for a certain manipulation of the micro- at elevated temperatures and pressures, but is a structureS.
Details
-
File Typepdf
-
Upload Time-
-
Content LanguagesEnglish
-
Upload UserAnonymous/Not logged-in
-
File Pages16 Page
-
File Size-