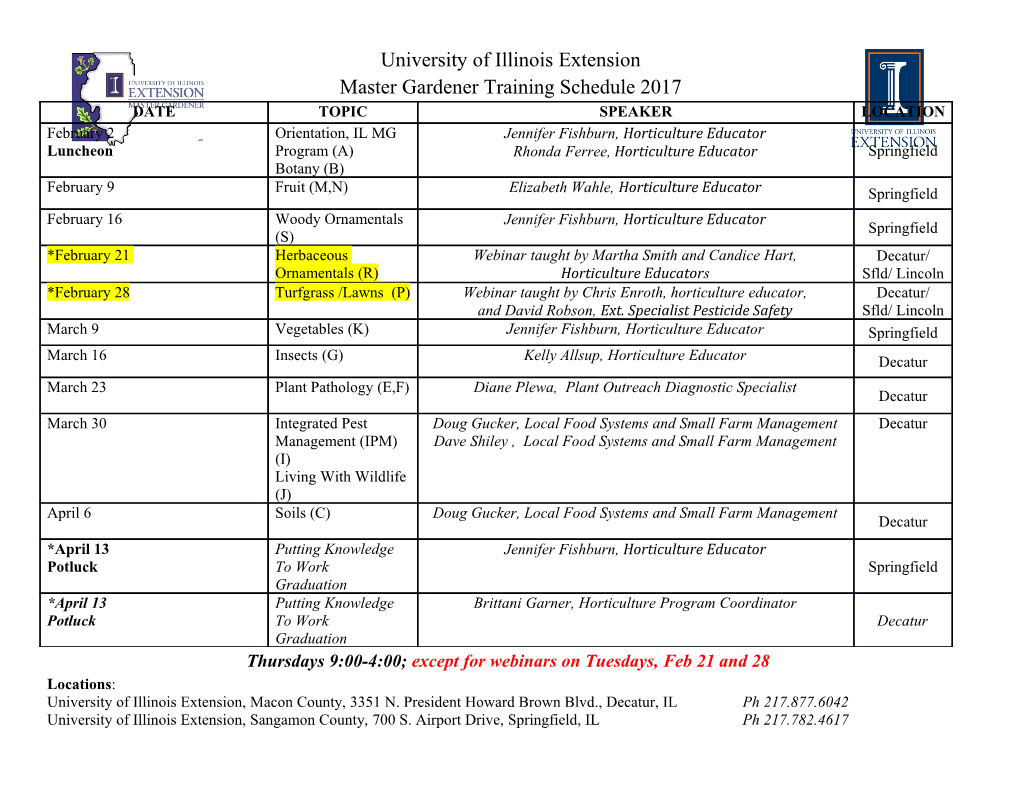
OPERATING AIR PERMIT Pursuant to the Regulations of the Arkansas Operating Air Permit Program, Regulation #26: Permit #: 766-AOP-R0 IS ISSUED TO: Superior Graphite Co. 3225 Dow Drive Russellville, AR 72802 Pope County CSN: 58-0145 THIS PERMIT AUTHORIZES THE ABOVE REFERENCED PERMITTEE TO INSTALL, OPERATE, AND MAINTAIN THE EQUIPMENT AND EMISSION UNITS DESCRIBED IN THE PERMIT APPLICATION AND ON THE FOLLOWING PAGES. THIS PERMIT IS VALID BETWEEN: and AND IS SUBJECT TO ALL LIMITS AND CONDITIONS CONTAINED HEREIN. Signed: Keith A. Michaels Date SECTION I: FACILITY INFORMATION PERMITTEE: Superior Graphite Co. CSN: 58-0145 PERMIT NUMBER: 766-AOP-R0 FACILITY ADDRESS: 3225 Dow Drive, Russellville, AR 72802 COUNTY: Pope CONTACT POSITION: Scott Anderson, Quality Manager TELEPHONE NUMBER: (501) 968-8810 REVIEWING ENGINEER: Vladimir Korolev UTM North-South (X): 3899 UTM East-West (Y): 486 2 Superior Graphite Co. CSN: 58-0145 Permit #:766-AOP-R0 SECTION II: INTRODUCTION Superior Graphite Co. owns and operates a facility at 3225 Dow Drive, Russellville, AR. The company manufactures graphite electrodes (SIC Code 3624) at this facility. The graphite electrodes are made by mixing petroleum coke with liquid coal tar pitch. The coke is delivered to the site in large bags or hopper rail cars. The coke is unloaded at Coke Receiving Pits #1 (SN-19). The on-site coke bagging operations consist of packing the material in bags, drums, or bulk bags (SN-13). Received coke is crushed and screened. Emissions from these operations are controlled by a baghouse (SN-03). Crushed and screened coke is milled (SN-02). Particulate matter is captured by a baghouse. Then milled coke is mixed with liquid coal tar pitch (SN-01). Particulate matter is controlled by a baghouse. Coal tar pitch is stored in a molten state in an aboveground heated storage tank. The mixture is extruded to form different size electrodes. The formed electrodes are placed in small rail cars and placed into natural gas fired baking ovens (SN-04, SN-05, SN-06, SN-07). Volatiles generated from the baking operations are oxidized by afterburners. A baghouse collects particulates as baking cans (saggers) are loaded and unloaded with electrodes (SN-11). The baked electrodes are impregnated with petroleum pitch to increase density and strength. Before impregnation, the electrodes are preheated in a vacuum drawn vessel (SN-10). The preheater is fired with natural gas and equipped with a baghouse. Petroleum pitch is stored in two aboveground heated tanks. After impregnation, the electrodes are rebaked in the Oven #5 (SN- 14). The VOC emissions are controlled by an afterburner. A 2.24 MM BTU/hr boiler (SN-12) is used to heat petroleum pitch and coal tar pitch tanks. Emissions from the boiler are uncontrolled. The rebaked electrodes are heated in electric graphitizing furnaces (SN-08) to convert amorphous carbon stock into graphite. There are eight (8) graphitizing furnaces at the facility with up to five operating simultaneously. The furnaces are heated up to 5400EF. The pollutants released during the graphitizing process include sulfur dioxide (SO2), carbon monoxide (CO), and hydrogen sulfide (H2S). Graphitized electrodes are cut (SN-16) and machined (SN-09) to the necessary specifications. Particulate emissions from these processes are captured in a baghouse. Scrap graphite electrodes are crushed to be sold as granular synthetic graphite (SN-15). The process is controlled by a baghouse. 3 Superior Graphite Co. CSN: 58-0145 Permit #:766-AOP-R0 This is facility’s first air permit under the Arkansas Air Operating Permit Program. The permit includes the following changes: 1. revised sulfur dioxide emissions from the Ovens #1-5 and graphitizing operation based on recent stack testing data; 2. installation of 1.5 MMbtu/hr batch oven; and 3. revised carbon monoxide (CO), hydrogen sulfide (H2S), and hydrogen cyanide (HCN) emissions from graphitizing operations based on recent stack testing data. The emission changes associated with the changes listed above are shown in the following table. Pollutant Previous Permit Contemporary Contemporary Current Permit Emission Limit Emission Emission Emission Limit (TPY) Increase (TPY) Decrease (TPY) (TPY) PM/PM10 54.2 6.5 0 60.7 SO2 129.7 110.4 0.5 239.6 VOC 11.9 0.1 3.2 8.8 CO 72.7 0 49.7 23.0 NOx 30.2 3.4 0 33.6 HCN 0.9 0 0.9 0 H2S 2.7 0 2.5 0.2 The summary of emissions from the facility is provided in the following table. Detailed information for individual sources may be found on cross reference pages of the permit. EMISSION SUMMARY Source Description Pollutant Emission Rates Cross No. Reference lb/hr tpy Page 01 Coke Mixing PM 2.4 10.4 9 PM10 1.4 6.2 4 Superior Graphite Co. CSN: 58-0145 Permit #:766-AOP-R0 EMISSION SUMMARY Source Description Pollutant Emission Rates Cross No. Reference lb/hr tpy Page 02 Coke Milling PM 1.5 6.4 9 PM10 0.9 4.0 03 Coke Handling PM 1.5 6.4 9 PM10 0.9 4.0 04-07, 14 Oven #1, #2, #3, #4, PM/PM10 1.6 5.5 12 and #5 SO2 62.6 57.0 VOC 0.5 1.2 CO 1.1 3.8 NOx 7.8 29.0 08 Graphitizing SO2 43.9 182.1 12 VOC 0.7 3.1 CO 4.3 17.8 NOx 0.1 0.5 H2S 0.047 0.2 09 Graphite Machining PM 1.1 4.9 9 PM10 0.6 2.7 10 Preheater PM/PM10 1.2 5.3 12 SO2 0.1 0.5 VOC 0.9 4.0 CO 0.2 0.9 NOx 0.6 2.7 11 Sagger Loading and PM 1.1 4.9 9 Unloading PM10 0.7 3.1 12 Boiler PM/PM10 0.1 0.5 12 VOC 0.1 0.5 CO 0.1 0.5 NOx 0.3 1.4 13 Coke Bagging PM 1.9 8.4 9 Operations PM10 1.1 4.9 5 Superior Graphite Co. CSN: 58-0145 Permit #:766-AOP-R0 EMISSION SUMMARY Source Description Pollutant Emission Rates Cross No. Reference lb/hr tpy Page 15 Graphite Crushing PM 1.1 4.9 9 PM10 0.1 0.5 16 Graphite Sawing PM 0.2 0.9 9 PM10 0.1 0.5 17 Petroleum Pitch De Minimis Emission Sources Storage Tanks 18 Coal Tar Storage De Minimis Emission Source Tank 19 Coke Receiving PM 0.5 2.2 9 Pit #1 PM10 0.3 1.3 PM 14.2 60.7 Total Allowable Emissions PM10 9.0 38.5 SO2 106.6 239.6 VOC 2.2 8.8 CO 5.7 23.0 NOx 8.8 33.6 H2S 0.05 0.2 6 Superior Graphite Co. CSN: 58-0145 Permit #:766-AOP-R0 SECTION III: PERMIT HISTORY In 1985, Superior Graphite Company acquired a graphite production facility previously owned by Dow Chemical Corporation in Russellville, Arkansas. In 1985, the first air permit #766-A was issued for the facility. Total ten (10) sources were permitted, including mixing and milling processes, coke handling, four (4) ovens, graphitizing, machining and sawing processes. In 1994, the air permit was revised in order to include some previously not permitted sources and update hourly emission rates. The on-site coke bagging operation (SN-13) installed in 1993 was also included in the permit #766-AR-1. In 1996, the second revision of the air permit was issued for the facility. The permit #766-AR-2 authorized the construction of the Oven #5 with bake and rebake capabilities (SN-14), installation of baghouses to control particulate matter emitted from graphite crushing (SN-15) and sawing (SN-16), and also identified sources which were previously unpermitted (SN-17 through SN-19). That permitting action also authorized continuous operations (i.e., 8760 hr/yr) for all sources and updated emission calculations for the existing graphitizing process. 7 Superior Graphite Co. CSN: 58-0145 Permit #:766-AOP-R0 SECTION IV: EMISSION UNIT INFORMATION Superior Graphite Co. CSN: 58-0145 Permit #:766-AOP-R0 SN-01: Coke Mixing SN-02: Coke Milling SN-03: Coke Handling SN-09: Graphite Machining SN-11: Sagger Loading and Unloading SN-13: Coke Bagging Operations SN-15: Graphite Crushing SN-16: Graphite Sawing SN-19: Coke Receiving Pit #1 Source Description Only particulate matter (PM/PM10) emissions are associated with the sources listed above. SN-01. At this source milled coke (SN-02) is mixed with coal tar pitch before being extruded. Coal tar pitch is accumulated in a storage tank. Particulate emissions from the mixing operations are controlled by a Ray-Jet baghouse. The control device has an efficiency of 99.5%. This dust collection system also controls particulate from the iron oxide elevator and remix crushing and conveying operations. The process was installed in 1970. SN-02. At this source crushed and screened coke (SN-03) is milled before being mixed with coal tar pitch (SN-01). Particulate matter generated from the milling activities is captured by a Purification Methods baghouse. The control device collects 99.5% of the particulate dust. The process was installed in 1970. SN-03. At this source coke received (SN-19) is crushed, separated, and screened before being milled (SN-02). Dust from the coke handling operations is captured by a Ray-Jet baghouse. The control device has an efficiency of 99.5%. The process was installed in 1970. SN-09. At this source graphitized electrodes (SN-08) are machined to the necessary specifications prior to be shipped. The emissions are controlled by a bagfilter with 99.5% efficiency.
Details
-
File Typepdf
-
Upload Time-
-
Content LanguagesEnglish
-
Upload UserAnonymous/Not logged-in
-
File Pages33 Page
-
File Size-