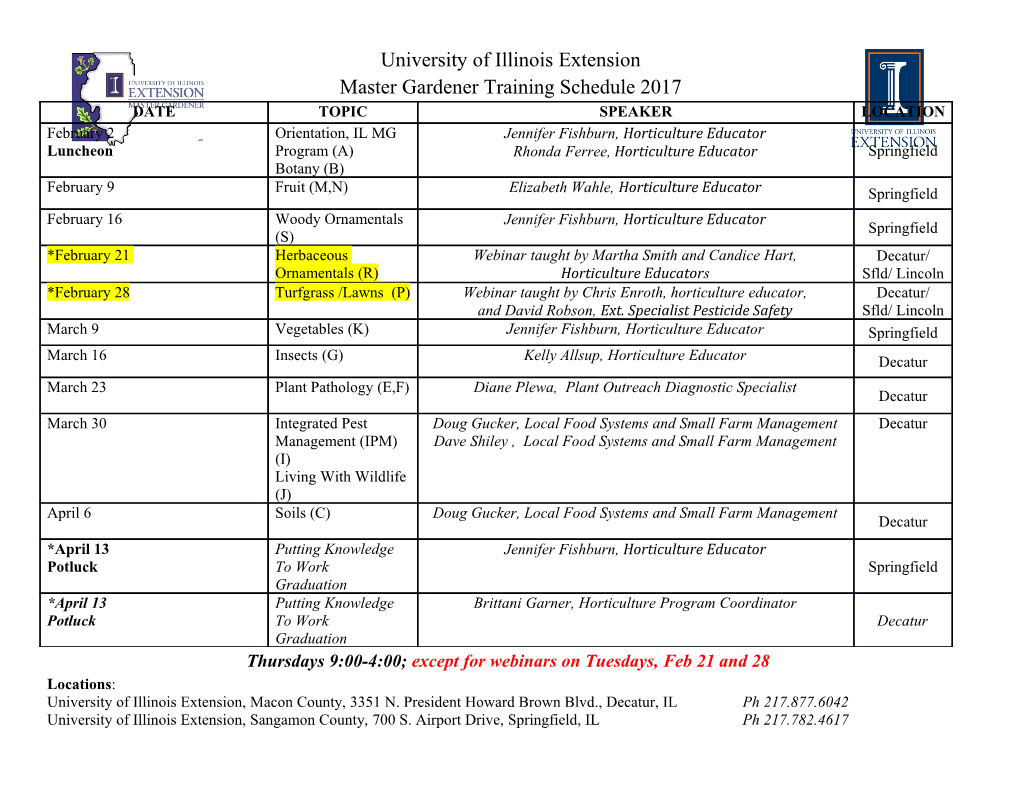
Terahertz System Analysis Using Zemax Prepared by Andrew Mueller for Ted Stinson and other members of the Basov Infrared Laboratory I. Introduction The commercial optical design software Zemax was used to model and evaluate the performance of a THz Near Field microscope. In this system, geometric optics approximations were not valid due to the long wavelength of Thz radiation. So by using the Physical Optics Propagation (POP) tool build into the engineering version of Zemax, it was possible to model the beam using a paraxial approximation. The initial goals of this venture are listed below. For the most part, all were at least partially fulfilled, though some conclusions were realized late in the process of building the experiment, or did not easily suggest a revised experiment design. Goals of the THz system analysis using Zemax: . Determine the intensity and power of Thz radiation that could make it from the emitter and be focused onto the AFM tip. Learn what simple modifications to the system’s geometry could yield even better focusing performance at the tip . Discover if the paraxial Gaussian beam approximation of Thz radiation would show a situation where the light would not be focused as desired. Develop a working knowledge of Zemax and its applicability to projects of this type, since it may be useful again in this lab. Basic Layout This image shows the basic geometry of the system. A broadband THz signal with wavelengths ranging from 100um to 3000um is focused onto an AFM tip using parabolic mirrors. Some lengths, like length A and B as shown in the image, were not set to specific values in the Zemax file. The intention was to leave these lengths as variables so that changing them might improve the focus on the AFM tip. However, using the system with a broadband signal showed that it could not be optimized for specific paraxial beam waist locations. What worked best for one wavelength would not translate to others. After working with the system for some time, it appeared the best lengths for A and B were as short as possible, as permitted by hardware and spatial constraints. But the lengths still did not have a large impact on the system's performance. For example, increasing A from 30mm to 130mm caused the radius of the beam at the tip to increase by less than 2% both for 100um and 3000um light. Keeping A and B short has more of an effect on ratio of power that makes it to the tip, because of clipping at the various reflective surfaces. Increasing A from 30mm to 130mm decreased the power transmitted to the tip by less than 5% for wavelengths shorter than 1000um. Objective of this Report This report is focused on the modeling of an optical instrument and covers insights gained using Zemax with significance for the project. Though not a general guide on how to use Zemax, it does outline techniques that would be useful for modeling of similar systems. This report would be useful for any projects that involve off-axis layouts, parabolic mirrors, or Gaussian beam models of long wavelength light. II. System Layout and Geometric Optics A. System-Specific Layout 1. Sequential vs Non Sequential Zemax has two modes with different features and advantages for building and analyzing off axis systems: Sequential and Non- Sequential. The mode is chosen under the File menu. For sequential mode, the order that surfaces are listed in the Lens Data Editor matters. Rays are only traced from surface 1 to surface 2 and so on. This means rays will not interact with a surface twice and will pass through a surface if it is not the next in the list. Using sequential mode requires a good understanding of exactly how the rays are supposed to propagate. It was mainly used during this investigation because physical optics propagation is only supported for a set of surfaces in this mode. For Non-Sequential mode, the order of surfaces in the Lens Data Editor does not matter, and rays will interact with any surface they encounter. Also in this mode, the incident rays can be defined in many more ways. As described in a later section, a point source of radiation can be modeled which was used for studying how light would propagate from the tip to the THz detector. Also, more arbitrary 3D surface shapes can be modeled or imported for use in Non-Sequential mode. 2. Aperture Type – Incidence Angle For the sake of viewing the experiment setup in the Zemax 3D layout viewer, correctly tracing some rays through the system can be helpful. However, there is not a strong correlation between how a beam is defined for raytracing and for Physical Optics Propagation. Defining the incident beam in the Zemax general settings only applies to the tracing of rays. Still, we modeled the incident beam geometrically using the Object Cone Angle Feature. This was useful because we did not know or care yet what the stop or smallest aperture was in our system. But we did know, from specifications of the Thz emitter, that most of the beam was inside a cone angle of 12.1 degrees. 3. Using Coordinate Breaks A three dimensional system of mirrors and lenses can be built and analyzed in Zemax while still using Sequential Mode. But because rays are propagated through surfaces in a specific order, the location of surfaces is defined in the context of this order. The location and orientation of a surface is not defined by a single universal coordinate system, but instead by the surface that preceded it. This way of building in 3D can be confusing for those with previous 3d modeling experience. Coordinate breaks are ‘pseudo-surfaces’ that are added in the Lens Data editor. They are not true surfaces because they have no effect on rays propagated through the system. They only work to modify the coordinates system for the following surface in the Lend Data Editor list. To add a coordinate break, add another surface in the Lens Data editor with the Insert key. Double click the first column entry of this surface to bring up the surface properties. Inside the Surface Type dropdown menu the Coordinate Break option is found. Coordinate Breaks have six parameters as shown here in the Lens data Editor: When the order parameter is set to zero, coordinate break applies the five transformations in this order: Decenters x and y, tilts about the local Z, tilts about the new Y, and then about the new x. When the order is set to any other number, then the transformations are applied in the opposite order. This can be useful when one needs one coordinate break to put a surface in an arbitrary configuration, and one coordinate break to bring the coordinate system back to what it was before that surface. Finally, the thickness of the coordinate break acts the same way as it does for any other surface. It is the length between the current surface and the next surface (or added after the transformations of a coordinate break). The image shows a simplified 2D representation of the order in which a coordinate break applies transformations. 4. Making custom shape fold mirror The aperture of a mirror or lens is the two dimensional shape that is projected over the surface of the element. The plane of the projection is normal to the (local) optical axis. Rays inside the shape are modified by the lens or mirror as normal; rays outside the shape are clipped or ignored. Essentially the lens or mirror is this shape when viewed along the optical axis. Custom shaped apertures for lenses and mirrors can be defined using a .UDA file which is selected for a particular surface on the Aperture tab of the surface properties menu. Starting on page 78, the Zemax manual provides an excellent explanation on how to define a custom aperture using a list of User Defined Aperture Entities. Through this method, fold mirrors with one semicircular edge and three straight edges were added to the system. 5. Making an Off Axis Parabolic Mirror Zemax fully supports mirror surfaces, but the technique for making an Off Axis Parabolic Mirror (OAP) is rather involved. The procedure is to make the full parabolic mirror that the final OAP is part of. Then the parts of the mirror that are not needed are ‘cropped’ away. First, add a Mirror type surface. Enter double the desired mirror focal length as the radius of curvature value. The focal length of a parabolic mirror is the closest distance from the mirror surface to the point of focus. For a 90 degree off axis parabolic mirror, the distance from the focus to the center of the mirror is double the focal length of the ‘parent’ parabola. So if you know this distance, shown as the Reflected Focal Length in the image, then it can simply be entered in the radius of curvature value to build the parent parabola. In the Thz system, the first collimating OAP has a Parent Focal Length of 25.4mm and a Reflected Focal Length of 50.8mm. -50.8 was used as the Radius value for this surface. The radius is negative just so the mirror is oriented correctly in the system. Second, enter -1 for the Conic value of the mirror surface in the Lens Data Editor. A parabola has a conic constant of -1. The Semi-Diameter of the mirror is its radius as measured from its optical axis. Make sure the Semi-Diameter is large enough so this ‘parent’ parabola includes the surface of the OAP.
Details
-
File Typepdf
-
Upload Time-
-
Content LanguagesEnglish
-
Upload UserAnonymous/Not logged-in
-
File Pages12 Page
-
File Size-