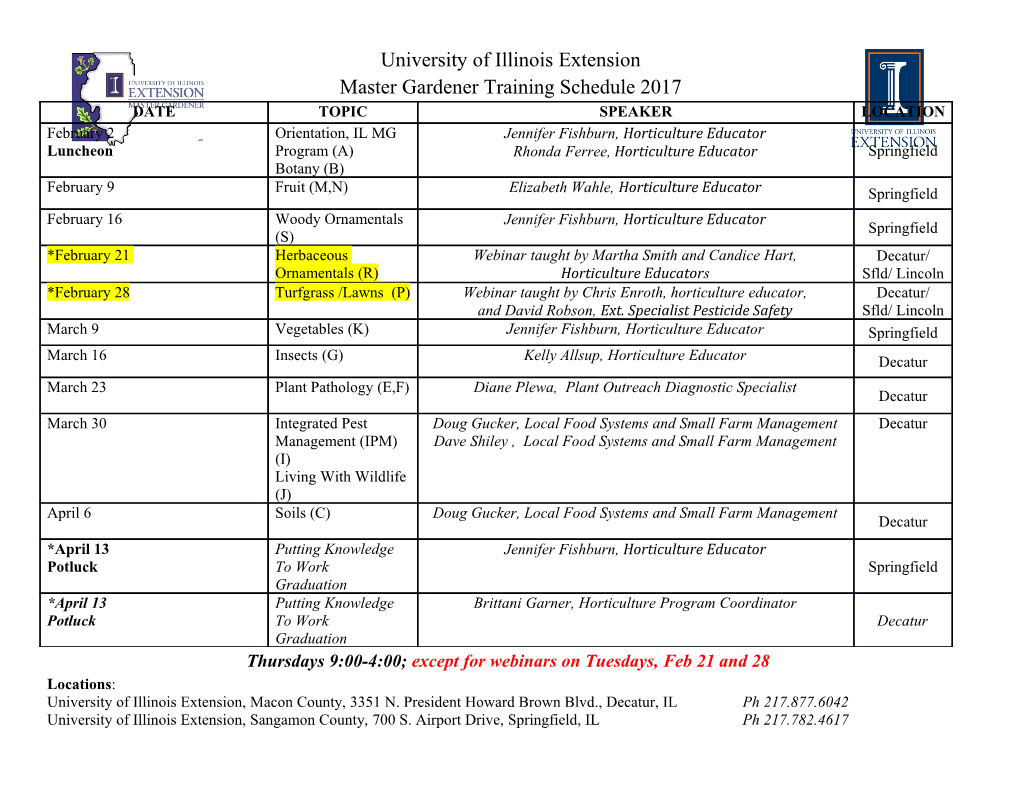
University of Pennsylvania ScholarlyCommons Department of Chemical & Biomolecular Senior Design Reports (CBE) Engineering 4-2011 Renewable 1,4-Butanediol Erinn R. Bibolet University of Pennsylvania Gabriel E. Fernando University of Pennsylvania Somil M. Shah University of Pennsylvania Follow this and additional works at: https://repository.upenn.edu/cbe_sdr Bibolet, Erinn R.; Fernando, Gabriel E.; and Shah, Somil M., "Renewable 1,4-Butanediol" (2011). Senior Design Reports (CBE). 22. https://repository.upenn.edu/cbe_sdr/22 This paper is posted at ScholarlyCommons. https://repository.upenn.edu/cbe_sdr/22 For more information, please contact [email protected]. Renewable 1,4-Butanediol Abstract The purpose of this project is to design a commercial-scale facility to produce 50 million pounds per year of 1,4-butanediol (BDO) from a renewable feedstock. A genetically engineered strain of Escherichia coli developed by Genomatica, Inc. will metabolize a molasses feed, delivered from an adjacent sugar and ethanol facility, into BDO. The BDO product purity and quality must meet or exceed current commercial requirements for polymer-grade material to be acceptable to prospective customers. The innovative technology to produce environmentally-friendly BDO will convert biomass-derived and renewable feedstocks in fewer steps than traditional petrochemical routes, with no toxic byproducts and minimal greenhouse gas emissions. Our BDO plant will be built in São Paulo, Brazil. This location was chosen due to its proximity to our sister sugar and ethanol facility. Despite the need to stop production for three months in mid-December through mid-March during the rainy season, when our sister plant will cease its molasses production, we determined that the low cost per amount of sugar from the Brazilian molasses will outweigh the ability to run year-round in a corn-based facility in the Midwestern United States. To account for the downtime associated with the rainy season, our facility has included extra molasses storage capacity to extend production for an additional month after our sister facility shuts down. We also anticipate 10 days of downtime due to maintenance and cleaning, which will result in about 290 days of full-scale facility operation. An economic analysis of our design demonstrated profitability after the firstear y of operation. Our feed materials, corn steep liquor, oleic acid, process water, and molasses, will cost us a total of about $200 per ton of BDO produced. But our vinasse co-product, which will be sold back to our sister sugar and ethanol plant for fertilizer, will result in additional revenues of $190 per ton of BDO produced. The selling price of the vinasse is discounted by 70% of the current fertilizer market price since we are selling it back to our sister facility, in return for discounted molasses and electricity. The direct permanent investment of the plant will be about $10.5 million and startup costs will be about $1.5 million, which results in a total permanent investment of $13.5 million. The net present value (NPV) of our facility with 15 years of production is $283 million and the internal rate of return (IRR) is 157%. We intend to sell our 99% pure BDO at $2,420 per ton produced, which will result in revenues of $72.5 million per year based on our commercial-scale production of 8,600 pounds of BDO per hour. Due to the profitability of our design, we will be able to sell our BDO at the low end of the U.S. market price range of $2,420 – $2,840 per ton, as was reported in the third quarter of 2010. Future research may need to be conducted to find out if additional equipment is needed in the actual plant, or if we were too optimistic on our pricing for the raw materials and utilities. This working paper is available at ScholarlyCommons: https://repository.upenn.edu/cbe_sdr/22 Professor Leonard Fabiano Mr. Stephen M. Tieri Professor Daniel A. Hammer Department of Chemical and Biomolecular Engineering Room 311A Towne Building 220 South 33rd Street University of Pennsylvania Philadelphia, PA 19104 April 12, 2011 Dear Professor Fabiano, Mr. Tieri, and Professor Hammer, The enclosed report contains our renewable process to generate 1,4-butanediol (BDO) from a renewable sugarcane feedstock via anaerobic fermentation of a genetically engineered strain of Escherichia coli (E. coli). We designed our plant to produce approximately 50 million pounds per year of 99% pure BDO using a combination of continuous and batch processing. Our plant will be built adjacent to a sugar and ethanol sister facility in Brazil, which will provide us with our renewable molasses feedstock. This feedstock will be fed into a continuous fermenter along with corn steep liquor media, water, and E. coli cells. The BDO excreted by the E. coli, along with remnants of the feed, will subsequently be sent to a continuous centrifuge. The impurities will then be removed through distillation, carried out in the bottoms using oleic acid, and recovered with a decanter. The resulting mineral-water mixture, called vinasse, will be sold back to our sister plant as fertilizer. The BDO product from the top of the distillation tower will be sold for use as a solvent and in the manufacturing of plastics, elastic fibers, and polyurethanes. The plant design has a positive economic forecast, assuming no significant shocks in the demand for BDO. Moreover, since our process is based on sugar cane, we would not expect our costs to co- vary with the rising price of oil as much as that of our competitors, who use petroleum-based feeds. The net present value (NPV) of the project 15 years after construction is $283 million. The total permanent investment required is about $13.5 million and the internal rate of return (IRR) is 157%. Due to the high profit margins attainable by this process, licensing our technology will capture 1 additional revenues. We would expect to negotiate licensing fees of about $1700 per ton BDO produced, based on a selling price of $2,420 per ton BDO. Future research may need to be conducted to find out if additional equipment is needed in the actual plant, or if we were too optimistic on our pricing for the raw materials and utilities. If there are any questions, comments, or concerns regarding this report, please do not hesitate to contact us. Thank you for your time, support, and guidance throughout the duration of the project and for your current consideration. Sincerely, _________________________ Erinn R. Bibolet _________________________ Gabriel E. Fernando _________________________ Somil M. Shah 2 Renewable 1,4-Butanediol CBE Senior Design Project 2011 Erinn R. Bibolet Gabriel E. Fernando Somil M. Shah April 12, 2011 Professor Leonard A. Fabiano Professor Daniel A. Hammer 3 Bibolet, Fernando, Shah Table of Contents Table of Contents .............................................................................................................................................. 4 Abstract ............................................................................................................................................................... 6 Introduction ........................................................................................................................................................ 8 Project Charter ................................................................................................................................................. 10 Innovation Map ................................................................................................................................................ 11 Concept Stage ................................................................................................................................................... 12 Market and Competitive Analysis ............................................................................................................. 13 Market Analysis of 1,4-Butanediol ....................................................................................................... 13 Competitive Analysis of 1,4-Butanediol Industry .............................................................................. 14 Customer Requirements ............................................................................................................................. 16 Feedstock and Location Choice ................................................................................................................ 17 Option 1: United States ......................................................................................................................... 17 Option 2: Brazil ....................................................................................................................................... 18 Decision ................................................................................................................................................... 18 Preliminary Process Synthesis ................................................................................................................... 19 Design History and Logic ...................................................................................................................... 19 Determining Water Content: Concentration vs. Viscosity ............................................................... 23 Assembly of Database ................................................................................................................................ 25 Chemical Kinetics
Details
-
File Typepdf
-
Upload Time-
-
Content LanguagesEnglish
-
Upload UserAnonymous/Not logged-in
-
File Pages244 Page
-
File Size-