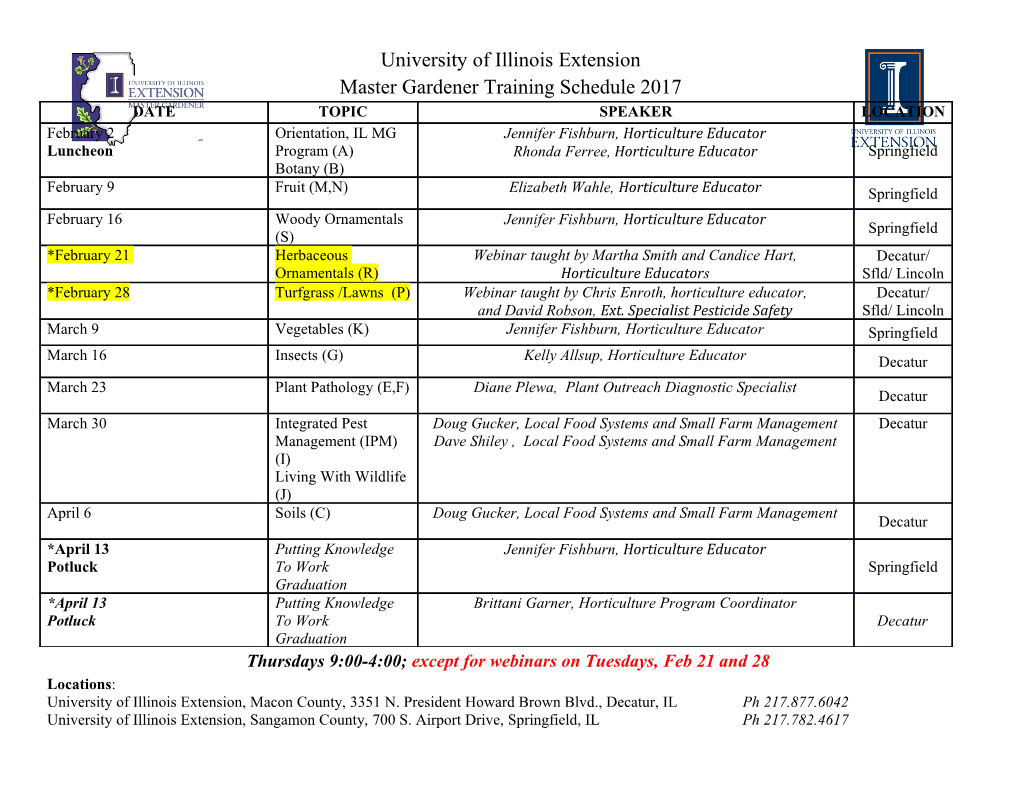
ASM Handbook, Volume 9: Metallography and Microstructures Copyright © 2004 ASM International® G.F. Vander Voort, editor, p644–669 All rights reserved. DOI: 10.1361/asmhba0003766 www.asminternational.org Metallographic Techniques for Tool Steels George F. Vander Voort, Buehler Ltd. TOOL STEELS can be prepared for macro- hot working axis) are preferred. However, lon- disks cut from failed components; however, scopic and microscopic examination using the gitudinal disks are better suited to studying de- room-temperature macroetching, which is also same basic procedures used for carbon and al- formation fiber or segregation. Transverse disks quite common, often uses a 10% aqueous nitric loys steels. However, because many tool steels are preferred for general-quality evaluations. If acid (HNO3) solution. Smooth-ground speci- are highly alloyed and are generally heat treated very hard, the disks should be tempered before mens are immersed for up to a few minutes in to much higher hardness than most carbon and etching. For routine-quality studies, a saw-cut this solution to reveal such surface conditions as alloy steels, specific aspects of their preparation surface is adequate. If better resolution of detail decarburization, carburization, nitriding, hard- differ slightly. The reasons for these differences is required or if photography is to be conducted, ened layers, and grinding damage. Internal qual- and the required procedural modifications are surface grinding is performed after cutting. ity problems, such as segregation, are revealed discussed in the following sections. Also cov- Macroetching. The macroetchant most but usually less effectively than by hot-acid etch- ered are the effects of hot working, composition, widely used to evaluate macrostructural quality ing. After etching, the surface is washed, austenitizing, and tempering on microstructure. of tool steels is the standard immersion solution scrubbed to remove etching smut, and dried. of equal parts of hydrochloric acid (HCl) and Etching of small polished sections in 2 to 5% Macroexamination water at 70 to 80 ЊC (160 to 180 ЊF) for 15 to 45 nital will also bring out surface conditions that min. Such etching will reveal segregation, cannot be as clearly revealed by the cold 10% cracks, porosity, inclusions (manganese sulfides, aqueous HNO solution. However, nital is less Specimen selection is generally based on the 3 original ingot locations. Sampling is usually per- for example), flow lines, surface decarburization effective on a smooth, ground surface. Figure 2 formed after primary hot working to billet or or carburization, and hardness variations. Inter- shows the carbide distribution on longitudinal bloom shapes. Disks 12 to 25 mm (0.5 to 1.0 in.) pretation of results is aided by referring to stan- planes of M2 and T1 high-speed steels revealed thick are most often cut from billet or bloom dard charts (Ref 1–4). Figure 1 illustrates the use by macroetching discs of varying diameter with locations corresponding to the top and bottom of of the 50% hot HCl macroetch to reveal the case 10% nital. Figures 3 and 4 show the carbide seg- the ingot. They are sometimes cut from the mid- depth in different sized brine-quenched and tem- regation by light microscopy examination in dle location. The hardness of these products can pered specimens of W1 tool steel with three lev- three of the sizes for the M2 and T1 discs. be rather high, unless the billet or bloom was els of hardenability. Note that there is excellent The sulfur print test (Ref 5, 6), another prev- subjected to a full annealing cycle. Thus, sec- contrast between the hardened case and the non- alent technique, is used to evaluate the distri- tioning of such specimens may be more difficult hardened core. bution of manganese sulfides. Fracturing of than for carbon or alloy steels. For most work, This etching procedure can be used to evaluate hardened transverse etch disks is also performed transversely oriented disks (perpendicular to the disks cut from sections smaller than billets or to detect oxide inclusion stringers or graphite on Fig. 1 AISI W1 tool steel austenitized at 800 ЊC (1475 ЊF), brine quenched, and tempered2hat150ЊC (300 ЊF). Black rings are hardened zones in 75, 50, and 25 mm (3, 2, and 1 in.) diameter bars. Core hardness decreases with increasing bar diameter (all one-half actual size). (a) Shallow-hardening grade. Case, 65 HRC; core, 34 to 43 HRC. (b) Medium-hardening grade. Case, 64.5 HRC; core, 36 to 41 HRC. (c) Deep-hardening grade. Case, 65 HRC; core, 36.5 to 45 HRC. Hot 50% HCl Metallographic Techniques for Tool Steels / 645 the longitudinally oriented fracture. The fracture Microexamination hacksaws. However, such operations produce a surface is often heated to produce a blue temper substantial zone of deformation beneath the cut color, because the uncolored oxides exhibit Sectioning. Relatively soft specimens (less and rather rough surfaces. Thus, the initial rough strong contrast against the dark fracture. than 35 HRC) can be cut using band saws or grinding with a coarse abrasive (80- to 120-grit silicon carbide, for example) must remove this damage. However, such coarse abrasives gener- ate large amounts of damage. Sectioning with an abrasive wheel developed for metallography is recommended, because it produces less damage and yields a better surface finish, so that dam- aging, coarse abrasive grinding can be mini- mized or eliminated. Then, a somewhat finer abrasive, which generates less damage, can be used for the first step (often called planar grind- ing with automated, multispecimen preparation systems). This procedure facilitates generation of a correctly prepared surface so that the true microstructure can be observed. Higher-hardness specimens must be cut using water-cooled abrasive cutoff wheels. The blade should have a “soft” bond (that is, it breaks down readily, exposing fresh abrasive to the cut) for effective cutting and avoidance of burning. Ef- fective water cooling limits heat generation but is inadequate by itself if the wrong blade is used, that is, a blade that does not break down at the proper rate. Dull abrasives generate excessive heat and damage in cutting. Cutting as-quenched specimens is very difficult without introducing some damaging heat that may cause burning or cracking. Cutting quenched and lightly tempered tool steels is much easier but still requires use of a wheel designed for such steels. Heat generated by improper technique can produce a highly tem- pered appearance in the martensite and, if heat- ing is excessive, can re-austenitize the surface. In extreme cases, melting can occur at the sur- face, with an extensive heat-affected zone below this area. Subsequent grinding steps cannot eas- ily remove such damage without introducing more damage. Fig. 2 Carbide distribution on longitudinal planes of high-speed steels revealed by macroetching discs of varying When working with as-quenched high-alloy -tool steels, it may be helpful to fracture the spec ןdiameter with 10% nital. (a) M2 tool steel. (b) T1 tool steel. Both ϳ1 1 5 1 Fig. 3 AISI M2 round bars. Carbide segregation at the center of round bars of different diameters. (a) 27 mm (1 ⁄16 in.) diam. (b) 67 mm (2 ⁄8 in.) diam. (c) 105 mm (4 ⁄8 in.) diam. ןnital. 100 10% 646 / Metallography and Microstructures of Ferrous Alloys 3 1 1 Fig. 4 AISI T1 round bars. Carbide segregation at the center of round bars of different diameters. (a) 35 mm (1 ⁄8 in.) diam. (b) 64 mm (2 ⁄2 in.) diam. (c) 83 mm (3 ⁄4 in.) diam. 10% ןnital. 100 imen. This will produce a flat, damage-free sur- However, some mounts have poor resistance to ture, transparent methyl methacrylate compres- face due to the extreme brittleness of such steels. solvents such as alcohol, and most polymeric sion-mounting thermoplastic material can be The fractured surface can then be carefully mounts are badly degraded if heated etchants are used. Somewhat better results can be obtained ground, with adequate cooling, and polished for required. The compression-mounting epoxies using cast, “cold”-mounting epoxy resins. examination. prevent these problems. If a transparent mount Casting epoxies are the only materials that For high-hardness, high-alloy steels, section- is required to control grinding to a specific fea- produce true adhesive bonding to the sample. ing with a low-speed saw or with a linear-pre- cision saw at higher rotational speeds, with alu- mina wafering blades, diamond, or cubic boron Table 1 Five-step preparation practice for tool steels nitride non-consumable blades, can provide Load high-quality surfaces with minimum cutting-in- Speed, Surface Abrasive/size N lbf rpm/direction Time, min duced damage. Although the cutting rate is Waterproof grinding 120/P120- to 240/P280-grit SiC, 22–27 5–6 Comp Until plane slower than with an abrasive cutoff saw, such paper (or equivalent) water cooled surfaces are smooth, damage is minimal, and Silk cloth or rigid 9 lm diamond (with lubricant) 22–27 5–6 Comp 5 grinding can begin with rather fine grits (320- or grinding disk 400-grit silicon carbide, for example). Section- Woven (napless) or 3 lm diamond (with lubricant) 22–27 5–6 Comp 3 pressed cloths ing is a violent process, and excessive damage Woven or pressed cloths 1 lm diamond (with lubricant) 22–27 5–6 Comp 2 introduced in sectioning rarely is removed fully Medium-nap cloth ϳ0.05 lm colloidal silica or sol- 22–27 5–6 Contra 1.5–2 by the preparation method. gel-type alumina suspensions Mounting. Bulk samples frequently can be polished without mounting. Coding of un- mounted specimens is generally limited to a few Table 2 Four-step preparation practice for tool steels stamp marks (if the steel is soft enough to Load stamp), such as a job number.
Details
-
File Typepdf
-
Upload Time-
-
Content LanguagesEnglish
-
Upload UserAnonymous/Not logged-in
-
File Pages26 Page
-
File Size-