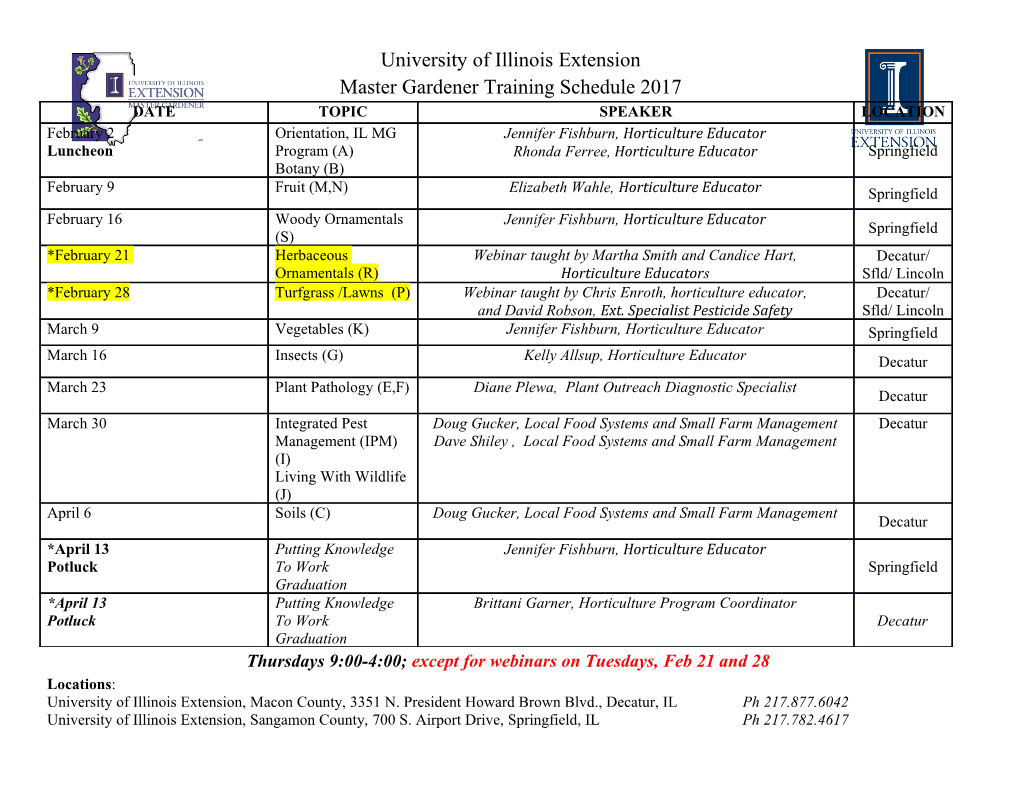
University of Wollongong Research Online University of Wollongong Thesis Collection 1954-2016 University of Wollongong Thesis Collections 2016 Development of an energy-harvesting magnetorheological fluid damper Yun Lu University of Wollongong Follow this and additional works at: https://ro.uow.edu.au/theses University of Wollongong Copyright Warning You may print or download ONE copy of this document for the purpose of your own research or study. The University does not authorise you to copy, communicate or otherwise make available electronically to any other person any copyright material contained on this site. You are reminded of the following: This work is copyright. Apart from any use permitted under the Copyright Act 1968, no part of this work may be reproduced by any process, nor may any other exclusive right be exercised, without the permission of the author. Copyright owners are entitled to take legal action against persons who infringe their copyright. A reproduction of material that is protected by copyright may be a copyright infringement. A court may impose penalties and award damages in relation to offences and infringements relating to copyright material. Higher penalties may apply, and higher damages may be awarded, for offences and infringements involving the conversion of material into digital or electronic form. Unless otherwise indicated, the views expressed in this thesis are those of the author and do not necessarily represent the views of the University of Wollongong. Recommended Citation Lu, Yun, Development of an energy-harvesting magnetorheological fluid damper, Master of Philosophy thesis, School of Mechanical, Materials and Mechatronic Engineering, University of Wollongong, 2016. https://ro.uow.edu.au/theses/4738 Research Online is the open access institutional repository for the University of Wollongong. For further information contact the UOW Library: [email protected] Development of an Energy-Harvesting Magnetorheological Fluid Damper A thesis submitted in fulfillment of requirements for the award of degree of Master of Philosophy Yun LU Faculty of Engineering and Information Science, University of Wollongong August 2016 Wollongong, New South Wales, Australia CERTIFICATION I, Yun Lu, declare that this thesis, submitted in partial fulfilment of the requirements for the award of Master of Philosophy, in the School of Mechanical, Materials and Mechatronic Engineering, University of Wollongong, is wholly my own work unless otherwise referenced or acknowledged. The document has not been submitted for qualifications at any other academic institution. Yun Lu 22th July 2016 ACKNOWLEGEMENTS ACKNOWLEGEMENT I wish to thank my supervisors, Prof. Weihua Li and Prof. Guoliang Hu, for their enthusiastic support, professional direction and constant encouragement that inspired me to overcome the challenges on my road of study. Particular thanks are extended to Shuaishuai Sun and Xin Tang for their help on operating of laboratory facilities and Labview programing. Without their assistance of my lab mates, I could have a lot of problems to complete this dissertation. I thank all who helped me during my studies. Finally, I especially would like to thank my parents for their understanding, patience and unwavering support of my studies. - i - TABLE OF CONTENTS TABLE OF CONTENTS ACKNOWLEGEMENT i TABLE OF CONTENTS ii LIST OF FIGURE iv LIST OF TABLE vi Abstract 1 CHAPTER 1 INTRODUCTION 2 1.1 BACKGROUND AND MOTIVATION 2 1.2 OBJECTIVES AND SCOPES 3 1.3 THESIS OUTLINE 4 CHAPTER 2 LITERATURE REVIEW 5 2.1 INTRODUCTION 5 2.2 MR TECHNOLOGY 6 2.2.1 MR Fluid and MR Effect 6 2.2.2 The Working Modes of MR Damper 7 2.2.3 Damping Force Model for MR Damper 8 2.3 ENERGY HARVESTING THECHONOLOGY 17 2.4 SELF-SENSING THECHNOLOGY 19 2.5 CHAPTER SUMMARY 22 CHAPTER 3 DESIGN OF EHMR DAMPER 23 3.1 KEY CONSEPTION AND WORKING PRINCIPLE 23 3.1.1 The Operation Principle of the Prototype 23 3.1.2 Consideration in Structure Design 24 3.2 MATERIALS USED IN DESIGN 27 3.3 CONFIGURATION OF THE EHMR DAMPER 31 3.3.1 Modelling of the MR Damper 31 3.3.2 The Simulation Based on Finite Element Method 36 - ii - LIST OF FIGURES 3.4 CONFIGURATION OF LINEAR POWER GENERATOR 38 3.5 DEVELOPMENT OF A SELF-SENSING ALGORITHM 43 3.6 CHAPTER SUMMARY 47 CHAPTER 4 PROTOTYPING AND TESTING OF EHMR DAMPER 48 4.1 FABRICATION AND ASSEMBLING OF PROTOTYPE 48 4.2 TESTING PROCESS 51 4.3 THE PERFORMANCE OF EHMR DAMPER 52 4.3.1 Testing of the Damping Property 52 4.3.2 Modeling of Damping Force 56 4.3.3 Identification of Damping Force Modeling 61 4.4 THE PERFORMANCE OF THE ENERGY HARVEST CAPABILITY 64 4.4.1 Performance of the Linear Generator 69 4.4.2 Frequency Multiplication Effect 71 4.4.3 Performance of Energy Harvest Effect via Rectification 71 4.5 THE PERFORMANCE OF SENSING CAPABILITY 74 4.5.1 Comparison Between Guessed Voltage and Initial Measurement 74 4.5.2 Sensing of Velocity and Displacement 74 4.5.3 Discussion of Self-sensing Result 78 4.6 CHAPTER SUMMARY 78 CHAPTER 5 CONCLUSION AND FUTURE WORK 80 5.1 CONSLUSION 80 5.2 FUTURE WORKS 81 REFERENCE 82 APPENDIX A: DETAILS AND CONSIDERATIONS OF UESING MTS 91 iii LIST OF FIGURES LIST OF FIGURES Figure 2.1 MR Effect in MR Base Materials Figure 2.2 Basic Operating Mode of MR Fluid Figure 2.3 A Coulomb Friction Element in Parallel with a Viscous Dashpot Figure 2.4 Gamota and Filisko’s modified Bingham model Figure 2.5 Schematic of simple Bouc-wen model Figure 2.6 Schematic of modified Bouc-wen model Figure 2.7 A typical shock absorber with mechanical energy harvesting system Figure 2.8 A Typical EHMR damper based on EMI technology Figure 2.9 Self-sensing technology for MR damper Figure 3.1 The schematic of EHMR damper Figure 3.2 The different between single-ended and double-ended structure Figure 3.3 The simulation of linear generator from Chen Figure 3.4 The simulation of isolation of magnetic interference Figure 3.5 Shear stress vs. shear rate under no magnetic field applied Figure 3.6 Yield stress vs. magnetic field strength Figure 3.7 Typical magnetic properties Figure 3.8 Magnetic properties of steel 1020 Figure 3.9 Magnetic properties of NdFeB permanent magnet (N52) Figure 3.10 Principle of operation of MR damper Figure 3.11 Key diagram of the basic magnetic circuit of MR damper Figure 3.12 Structure of piston head Figure 3.13 Finite element analysis of MR damper part Figure 3.14 Magnetic flux density under different applied current Figure 3.15 Magnetic flux density in the annular gap under different currents Figure 3.16 Schematic of linear power generator Figure 3.17 Equivalent magnetic circuit for the proposed power generator Figure 3.18 Distribution of magnetic density distribution Figure 3.19 Distribution of Cogging Force Figure 3.20 The principle of velocity-sensing algorithm Figure 4.1 Main components of the proposed EHMR damper iv LIST OF FIGURES Figure 4.2 Main components arrangement for the prototype testing Figure 4.3 The proposed MR damper Figure 4.4 Damping force vs. amplitude under 1Hz frequency Figure 4.5 Damping force vs. excitation frequency under 5mm amplitude Figure 4.6 Damping force vs. excitation current under 5mm amplitude Figure 4.7 Force-displacement relation of the MR damper test with different current under 1 Hz, 5mm amplitude Figure 4.8 Mathematical model of MR damper based on Bouc-wen mode Figure 4.9 Matlab program for the proposed mathematic model Figure 4.10 Comparison of mathematic model and experimental data base on time-force relation Figure 4.11 Comparison of damping force based on Bouc-wen model and measurement Figure 4.12 Desired damping force from mathematical model vs. initial measured data Figure 4.13 The desired damping force when piston operates under different excitation Figure 4.14 The desired damping force from mathematic model vs. the measured data Figure 4.15 Comparison between experiment and calculation result: coils 1 Figure 4.16 Comparison between experiment and calculation result: coils 2 Figure 4.17 Generate voltage under open loop: 5mm 2Hz Figure 4.18 Generate voltage under open loop: 5mm 3Hz Figure 4.19 Generate voltage under open loop: 5mm 4Hz Figure 4.20 Comparison of generative voltage under different amplitude and frequency Figure 4.21 Frequency multiplication effect under frequency of 4 Hz and amplitude of 10mm Figure 4.22 Frequency multiplication effect under frequency of 4 Hz and amplitude of 15mm Figure 4.23 Schematic of the AC-DC rectifier Figure 4.24 Assembled EHMR damper with AC-DC rectifier Figure 4.25 The experiment result of performance of generator with AC-DC rectifier Figure 4.26 Comparison between experiment and calculation result: coils 1 Figure 4.27 Experimental result of sensing velocity under excitation of 3Hz 5mm Figure 4.28 Experimental Result of Sensing Velocity Under Excitation of 5Hz 15mm Figure 4.29 Experimental result of sensing displacement under excitation of 3Hz 5mm Figure 4.30 Experimental result of sensing displacement under excitation of 4Hz 15mm v LIST OF TABLES LIST OF TABLES Table 3.1 Key parameter of the cylinder Table 3.2 Key Parameter of the Piston Table 3.3 Magnetic flux in each region of the piston Table 3.4 Magnetic induction intensity of each region Table 3.5 The magnetic field strength of each region Table 3.6 material used in main component Table 3.7 parameter for main structure Table 4.1 Parameter of the fabricated MR damper part Table 4.2 Parameter of the damping force model - vi - ABSTRACT Abstract Due to the unique property of magnetorheological (MR) effect, the MR-base device takes the advantage in rapid response, large dynamic range in strength and low energy consumption.
Details
-
File Typepdf
-
Upload Time-
-
Content LanguagesEnglish
-
Upload UserAnonymous/Not logged-in
-
File Pages101 Page
-
File Size-