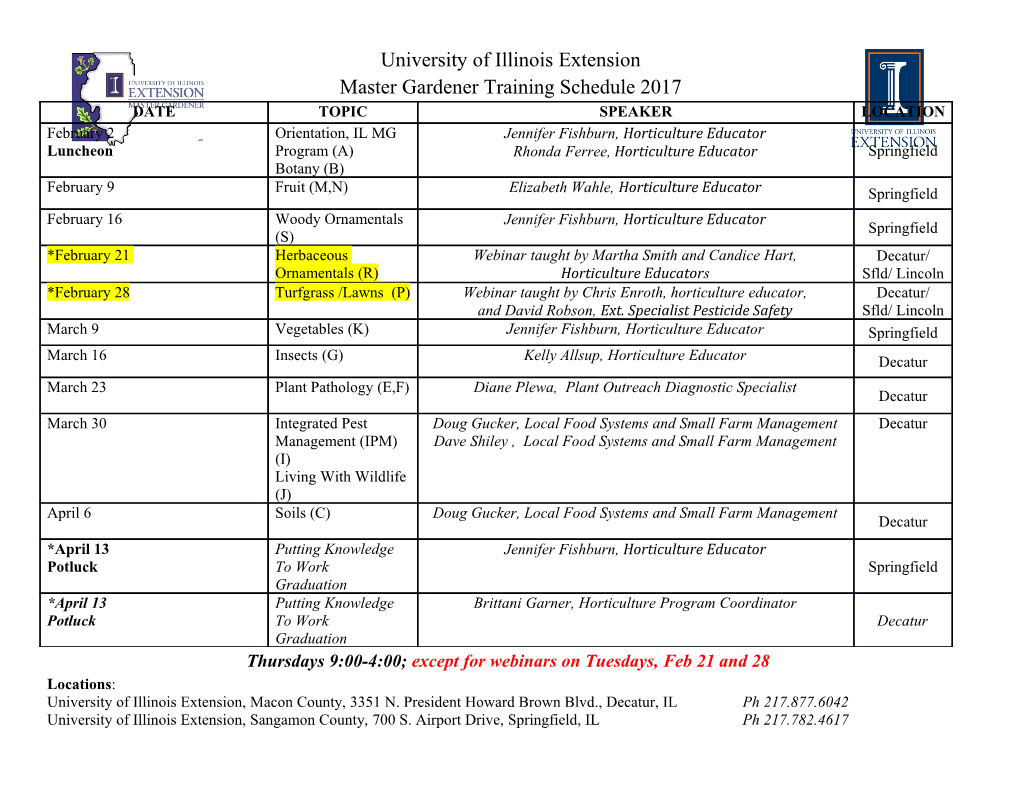
Bulk Micromachining Review • Definition: Etching pits, trenches or all the way through the silicon wafer to make mechanical Surface Micromachining: structures. Techniques and Materials • Methods • Wet etching • Dry etching (plasma or vapor) Dr. Thara Srinivasan Lecture 3 • Etching modes • Isotropic: etches all crystal directions equally • Anisotropic: etches certain directions faster than others • Diffusion (or transport) -limited vs. Reaction-limited Picture credit: Texas Instruments 3 Reading and Project Info. Bulk Micromachining Review • Reading • Senturia, sections from Chapter 3. • Etch stops for wet etching • From reader • Bustillo et al., “Surface Micromachining of Microelectromechanical Systems,” pp. 1552-6, 1559-63. • Plasma etching • Williams, “Etch Rates for Micromachining Processing,” pp. 256-69. • Etching species: ions and neutrals (radicals) • Print out lecture notes before lecture • “Plasma” etching: neutrals • http://www-bsac.eecs.berkeley.edu/projects/ee245/index.htm • Reactive ion etching: ions and neutrals • For the project later on in the semester, you will… • Pick a fabrication method and materials for your MEMS device • Explain fabrication decisions • Deep reactive ion etch (DRIE) • Vertical, deep trenches • Alternate between etch step and protective Teflon deposition step 2 4 1 2 Bulk Micromachining Review Surface Micromachining • Bulk etching and metallization • Possible structures 5 7 Lecture Outline Micromachining a Cantilever • Today’s Lecture • Introduction • Thin film deposition • Thin film etching techniques • Material combinations Sacrificial etch. This step “releases” the ca • Lateral resonator process flow Deposit & pattern oxide Deposit & pattern poly Oxide Poly-Si Anchor Cantilever 10 µm Si substrate Si substrate Si substrate 6 8 3 4 One Structural Poly, One Oxide Process History • History of surface micromachining • 1984: Howe and Muller used polysilicon and oxide to make beam resonator as gas sensor • 1988: Pin joints, springs, gears, rotary electrostatic side drive motors (Fan, Tai, Muller) • 1989: Lateral comb drive (Tang, Nguyen, Howe) Lateral resonator with electrostatic comb drives, Sandia Labs 9 11 Surface Micromachining History • Basic process sequence • History of surface micromachining • Structural layer • 1991: Polysilicon hinge (Pister, Judy, Burgett, Fearing) • Sacrificial layer • 1992: MCNC starts MUMPS (a MEMS foundry) • Release etch • Early 1990’s: First surface micromachined accelerometer sold (Analog Devices, ADXL50) Polysilicon level 1 Plate Polysilicon level 2 Polysilicon level 2 Staple Polysilicon level 1 Silicon substrate Digital Micromirror Device, Hinge staple Silicon substrate Texas Instruments Support arm Prof. Kris Pister Meshing gears on a moveable platform, Sandia Analog Devices 10 Integrated accelerometer 12 5 6 Polysilicon Mechanical Properties Today’s Lecture • Mechanical properties of polycrystalline • Introduction silicon (polysilicon or “poly”) • Thin film deposition techniques • Stronger than stainless steel: fracture strength of poly ~ 2-3 GPa, steel ~ 0.2GPa-1GPa • This film etching techniques • Young’s Modulus ~ 140-190 GPa • Material combinations • Extremely flexible: maximum strain before fracture • Lateral resonator process flow ~ 0.5% • Does not fatigue readily • Compatible with IC fabrication processes, process parameters well-known 13 15 Lateral Resonator Thin Film Deposition • Electrostatic force is applied by a drive comb to a • Chemical Vapor Deposition suspended shuttle • Polysilicon • Motion is detected • Silicon nitride capacitively by a sense comb • Silicon dioxides • Operated at resonant frequency • Thermal oxidation • Silicon dioxide • Physical Vapor Deposition • Evaporation of metals C. T.-C. Nguyen and R. T. Howe, IEEE IEDM, 1993 • Sputtering of metals, dielectrics 14 16 7 8 Mean Free Path Chemical Vapor Deposition • Definition: distance a molecule travels before hitting another molecule • Mean free path for gases Pressure Energy Source APCVD 100-760 torr 350-400°C Transport-limited πRT η λ = LPCVD 100-500 mtorr 500-800°C Reaction-limited 2M P PECVD 2-5 torr plasma + Reaction-limited • Atmospheric 760 torr →λ= 40 nm 300-400°C • Low vacuum 0.76 torr →λ= 40 µm • Medium vacuum 7.6 mtorr →λ= 4 mm • High vacuum 7.6 µtorr →λ= 4 m 760 Torr = 101 kPa = 1 atm 1 mTorr = 0.13 Pa = 1.3×10-6 atm APCVD and PECVD furnaces 17 19 Chemical Vapor Deposition Chemical Vapor Deposition tube • Gases react at hot wafer surface to create solid films door gate valve injector boats waferscantilever baffles • Materials: polysilicon, silicon nitride, phosphosilicate glass (PSG), low temperature oxide (LTO) exhaust • Parameters: T, P, gas flowrates pump mass flow mass flow controller controller 4 6 4 6 3 2 H H N 2 2 SiH PH B Si GeH LPCVD furnace Jensen 18 20 9 10 Doped LPCVD Polysilicon CVD and Film Conformality • Film coverage • Doping “in situ” • Low pressure = long mean free path • n-type: 1 vol % phosphine (PH ), p-type: diborane (B H ) • Molecules hit surface with extra energy to 3 2 6 • [ ] = 1020 cm-3, R = 1-10 mΩ/cm migrate • n-type, dep. rate ↓ • Conformal coverage, case (a) • p-type dep. rate ↑ • If there is no surface migration, • Large stresses ~ 500 MPa • Coverage depends on range of arrival angles, case (c) • Diffusion • Use PSG layers Deposited at 590°C, 5 5 µm2, rms ~ 12 nm • 900-1000°C, hours × • Heavy doping possible, R = 0.1 mΩ/cm • Ion implantation • As-deposited doped films also have high stress (500 MPa) a) b) c) 21 23 LPCVD Polysilicon Residual Stress in Thin Films • Undoped polycrystalline silicon (poly) • Uses: IC layers, interconnect, MEMS structural material • Residual film stress • Pyrolysis of silane, SiH4, and dichlorosilane, SiH2Cl2 • Microstructure • T = 550-700°C, P = 100’s mTorr • Thermal mismatch • Deposition rate: 10 nm/min at 630°C, 70 nm/min at 700°C (undoped) • Compressive vs. tensile stress • Conformal coverage (aspect ratio < 10) • Large stresses (500 MPa) and stress gradients Under compressive stress, Under tensile stress, film film wants to expand. wants to shrink Constrained to substrate, Constrained to substrate, Deposited at 590°C, bends it in convex way. bends it in concave way. 5×5 µm2, rms ~ 5 nm 22 24 11 12 Stress Gradients Controlling PolySi Stress compressive • Resonant frequency for lateral resonator, L = 150, W = • Stress gradient: (+) or (-) tensile 2 µm. 4E tW 3 Stress term dominates + 1 y 24σ rtW – f0 ≈ + 2π ML3 5ML 25 27 Annealing out PolySi Stress Stress in Polysilicon Films • Control polySi stress by annealing at high temperatures, • Stress depends on crystal structure: P 900-1150°C d e • Grain boundaries move, relax • ≤ 600°C ~ films are initially amorphous, x ia u then crystallize q • Annealing between similarly doped oxides (symmetric dopant /e r s a drive-in) • Equiaxed crystals, isotropic u n o h m p lu • Also, rapid thermal anneal (RTA) • Crystals have higher density → tensile r o o c m stress a • Small stress gradient • ≥ 600°C ~ Columnar crystals grow during deposition • As crystals grow vertically and in-plane they push on neighbors → compressive stress • Positive stress gradient T 26 Biebl & Howe 28 13 14 LPCVD Oxides Thermal Oxidation • Phosphosilicate glass (PSG) and low- temperature oxide (LTO) • Oxidize silicon in dry O2 or • Uses: sacrificial layer, insulator steam (850-1150°C) • Pyrolysis of silane, and/or phosphine, • Dry oxidation diborane • Si + O Æ SiO • T = 400-450°C, P = 100’s mTorr 2 2 • Wet oxidation • Deposition rate: LTO ~ 150 nm/min at 450°C • Si + 2H O Æ SiO + 2H • Poor conformality 2 2 2 • Annealing • Uses: electrical isolation, sacrificial layer, etch mask, • T = 600-1000°C → “densification” O2 • T = 1000°C → softens and flows to biocompatible SiO conform to underlying topography • SiO2 volume greater than Si 2 • Stress: compressive 100-300 MPa • To grow 1 um SiO2 layer, 0.44 um Si consumed Silicon Silicon • TEOS: conformal oxide • Compressive stress: 100’s MPa 29 31 Silicon Nitride Deposition Evaporation • Local heating of target material • LPCVD deposition generates vapor that condenses on • Uses: etch mask, passivation layer, coating for structural substrate layers • Materials: Al, Ti, W, Au, Pd, Pt, Cr, Al2O3 • Dichlorosilane (SiCl2H2), ammonia (NH3) • T = 700-900°C, P = 100’s mTorr • Types • Thermal evaporation: resistively heat source • Types • Electron beam evaporation: accelerated • Stoichiometric, Si3N4 ~ up to 1000 MPa tensile electrons strike and melt target • Non-stoichiometric, SixNy ~ Si excess ≤100 MPa tensile, even compressive • Deposition rate ~ 0.05 - 1 µm/min • Depends on material’s vapor pressure V , • PECVD < 400°C → pinholes, high H2 content, can also p control stress measure of volatility • Pressure: µTorrs Madou 30 32 15 16 Evaporation Issues Today’s Lecture • Step coverage • Film evaporates in a straight • Introduction line to wafer, highly “directional” • Rotate substrate for film • Thin film deposition continuity with “planetary” holder • Thin film etching techniques • Amenable to lift-off process • Material combinations • Lateral resonator process flow • Pros and cons photoresist • Resistive metal + Simple – Contamination from filament, filament size limits film thickness • E-beam + Purer films, higher deposition rates, better adhesion – Complex system requires target cooling and x-ray shielding 33 35 Sputtering Film Etching Cooling water • Process Target (Material to be Deposited) • Target material at high (-) Cathode (Negative Voltage, DC or RF) Material Wet etchant Etch rate Dry etchant Etch rate potential is bombarded by [nm/min] [nm/min]
Details
-
File Typepdf
-
Upload Time-
-
Content LanguagesEnglish
-
Upload UserAnonymous/Not logged-in
-
File Pages12 Page
-
File Size-