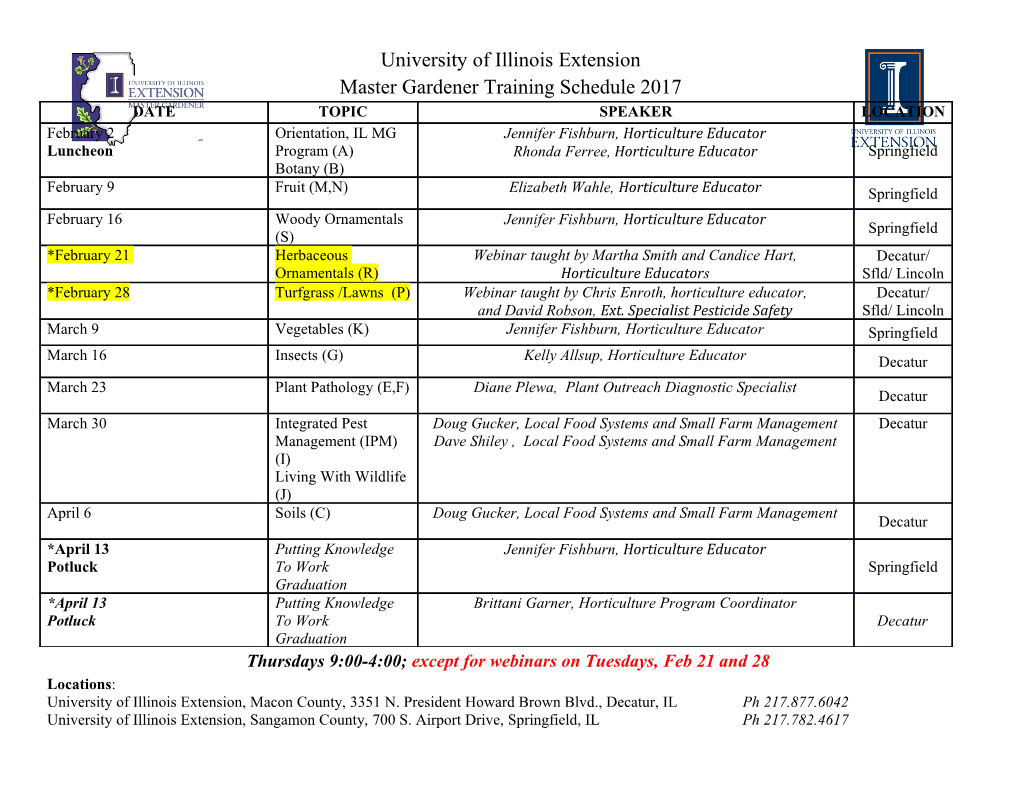
2141 Probability Analysis in Determining the Behaviour of Variable Amplitude Strain Signal Based on Extraction Segments Abstract M. F. M. Yunoh a This paper focuses on analysis in determining the behaviour of vari- S. Abdullah b, * able amplitude strain signals based on extraction of segments. The M. H. M. Saad c constant Amplitude loading (CAL), that was used in the laboratory d Z. M. Nopiah tests, was designed according to the variable amplitude loading e (VAL) from Society of Automotive Engineers (SAE). The SAE strain M. Z. Nuawi signal was then edited to obtain those segments that cause fatigue a damage to components. The segments were then sorted according to Department of Mechanical and Materials their amplitude and were used as a reference in the design of the Engineering, Faculty of Engineering & CAL loading for the laboratory tests. The strain signals that were Built Enviroment, Universiti Kebangsaan obtained from the laboratory tests were then analysed using fatigue Malaysia, 43600 UKM Bangi, Selangor, life prediction approach and statistics, i.e. Weibull distribution anal- Malaysia. [email protected] b ysis. Based on the plots of the Probability Density Function (PDF), [email protected] c Cumulative Distribution Function (CDF) and the probability of fail- [email protected]; d ure in the Weibull distribution analysis, it was shown that more than [email protected]; e 70% failure occurred when the number of cycles approached 1.0 x [email protected] 1011. Therefore, the Weibull distribution analysis can be used as an alternative to predict the failure probability. * Corresponding author: S. Abdullah, [email protected] Keywords Fatigue, signal processing, strain signal, variable amplitude, http://dx.doi.org/10.1590/1679-78254036 Weibull distribution Received 16.05.2017 In revised form 10.08.2017 Accepted 13.08.2017 Available online 26.08.2017 1 INTRODUCTION Fatigue failure is a frequent phenomenon in industries, especially in the automotive field. According to a study by Gupta et al. (2006), the material damage caused by the phenomenon of fatigue results in major degradation in the structure. Early detection of fatigue damage is very important because continuous damage can result in catastrophic failure that will lead to components destruction and 2142 M.F.M. Yunoh et al. / Probability Analysis in Determining the Behaviour of Variable Amplitude Strain Signal Based on Extraction Segments probably the loss of life. This failure could happen even though most of the properties of metal alloys have been thoroughly researched (Colin and Peter, 2009). Currently, various methods and tools have been developed to detect and reduce fatigue failure such as cracks and fractures. Most of the common methods used are concerned with laboratory tests, data collection and anal- ysis using specific software (Lee and Han, 2009; Tsapi and soh, 2015). The field of signal processing in the analysis of fatigue data has attracted the interest of researchers until today. The prediction of fatigue life should be studied with an actual load to ensure a more accurate analysis. Therefore, in determining the fatigue life of automotive components, the actual loading must be used as the input data for the analysis of fatigue to obtain highly accurate results for the study (Wang et al. 1995). However, it is very expensive and time consuming to conduct the study in a real situation. In actual applications, most of the engineering components are exposed to variable amplitude loading (VAL) that lead to failure and eventually cause cracks to appear (Wei et al. 2002; Mansor et al. 2017). The characterisation of fatigue life on materials is mostly done under a constant amplitude loading (CAL) to facilitate the analysis with existing equipment (Post et al. 2008). Hence, a method is needed to convert the VAL loading to a CAL loading that has almost the equivalent degree of fatigue damage. In this paper, the process of editing the strain signals obtained in real situations was used to design a constant signal that can be used in laboratory experiments to obtain the same results. The main focus of this paper was to predict the fatigue life of materials through laboratory tests and analyses using the Weibull distribution analysis. 2 THEORETICAL BACKGROUND The Wavelet Transform is a method for summarising the data or functions that are operating in different frequencies. Wavelet Transform is widely used to study signals where the resolution is rela- tive to the scale that is providing the information in both domains of time and frequency (Wu & Liu, 2007). Wavelet Transform can be classified as Continuous Wavelet Transform (CWT) and Discrete Wavelet Transform (DWT). Until now, Wavelet Transform analysis is being used extensively in the field of engineering such as data compression, signal processing, image processing, as well as in the medical field (Sifuzzaman et al. 2009). Piotrkowski et al. (2009) used the Wavelet Transform appli- cation in acoustic emissions to detect damage and corrosion, while Chang and Chen (2005) used the Wavelet Transform to detect the position and depth of cracks in beams. Discrete Wavelet transform can be defined as in Equation (1): W (m, n) x(t)a m 2 * (a m , t nb )dt 0 0 0 (1) where a represents the scale, and b, the time that is discretised from the continuous wavelet according m n to a a0 , b na 0 b0 , m and n are integers and b ≠ 0 is the translation step. In the automotive industry, the component that experiences service load is usually assessed using the fatigue strain-life approach. The fatigue strain-life method consists of measuring the changes in the loading history, the geometry and the material properties in predicting the fatigue life of a com- ponent (Rahman et al. 2009). The failure criteria for the strain life approach still does not have a Latin American Journal of Solids and Structures 14 (2017) 2141-2152 M.F.M. Yunoh et al. / Probability Analysis in Determining the Behaviour of Variable Amplitude Strain Signal Based on Extraction Segments 2143 fixed expression, where it is merely stated as a failure whenever a small crack is detected (Stephens et al. 2001). The strain life model that is commonly used in the prediction is the Coffin-Manson model. This model can provide a traditional prediction when the history of the compression load time is more influence and the mean stress is zero. This model can be defined by Equation (2): ' f b ' c a (2 N f ) f (2 N f ) (2) E Two other models are usually used in experiments involving the mean stress effect, namely the Morrow and Smith Watson Topper (SWT) models. The Morrow model involves modifying the elastic strain part in the strain-life curve by taking into account the mean stress. This model is suitable for studying steel materials and predicting the fatigue life by taking into account the strain amplitude. ' f m b ' c 1 (2 N ) f 2 N a ' f f (3) E f The parameter of damage that takes into account the maximum stress and the strain amplitude of a cycle for the SWT model can be expressed by Equation (4): ' 2 f (2 N ) 2b ' ' (2 N )b c (4) a mak E f f f f In terms of the statistical analysis used in the field of engineering, the Weibull distribution is a theoretical model that has been used successfully. Through this model, the general distribution can be modelled within the range of the life distribution (Sivapragash et al., 2008). The Weibull distribu- tion is also suitable to study a failure analysis of a small number of samples. In this study, the 2-P Weibull distribution is shown in the following Equation (5): x x f ( x : , ) exp (5) In this study, f (x: θ: β) is the fatigue life probability that is equal to or less than θ, β, which are the scale perimeter and shape perimeter, respectively. 3 METHODOLOGIES In this study, the strain signal standard from the Society of Automotive Engineers (SAE) was used in the design of the CAL load that was used in the laboratory test. This SAE strain signal was edited using the Wavelet Transform approach. In this analysis, the SAE strain signal of 122.4 seconds was edited to eliminate the strain amplitude which had no effect on fatigue damage. The Cut of Level (COL) was used to eliminate the low strain signal amplitude, while the high signal amplitude was maintained. These remaining segments of strain signal amplitude is considered to contribute to fatigue damage. Figure 1 shows the editing process of the strain signal using the Wavelet Transform ap- proach. Latin American Journal of Solids and Structures 14 (2017) 2141-2152 2144 M.F.M. Yunoh et al. / Probability Analysis in Determining the Behaviour of Variable Amplitude Strain Signal Based on Extraction Segments 8 x 10 1,000 10 500 5 -500 -1,000 0 20 40 60 80 100 120 Wavelet Energy 0 0 20 40 60 80 100 120 Strain Amplitude(ue) Time (s) Time(s) Input strain signal Set the Cut of Level (COL) and extract the high mag- nitude segments 255 235 250 209 183 200 157 e 131 150 1,000 105 100 Scale(1/Hz) 79 500 53 50 27 1 0 0.5 1 1.5 2 2.5 Data Points 4 -500 x 10 -1,000 0 20 40 60 80 100 120 Transform the input strain signal into time-frequency localisa- Strain Amplitude (u Time (s) 8 x 10 Transpose the time-frequency localisation into time 10 history 5 Wavelet EnergyWavelet 0 0 20 40 60 80 100 120 Time(s) Transpose into time-frequency magnitude distribution Figure 1: Process flow diagram of Wavelet Transform based on fatigue data editing method.
Details
-
File Typepdf
-
Upload Time-
-
Content LanguagesEnglish
-
Upload UserAnonymous/Not logged-in
-
File Pages12 Page
-
File Size-