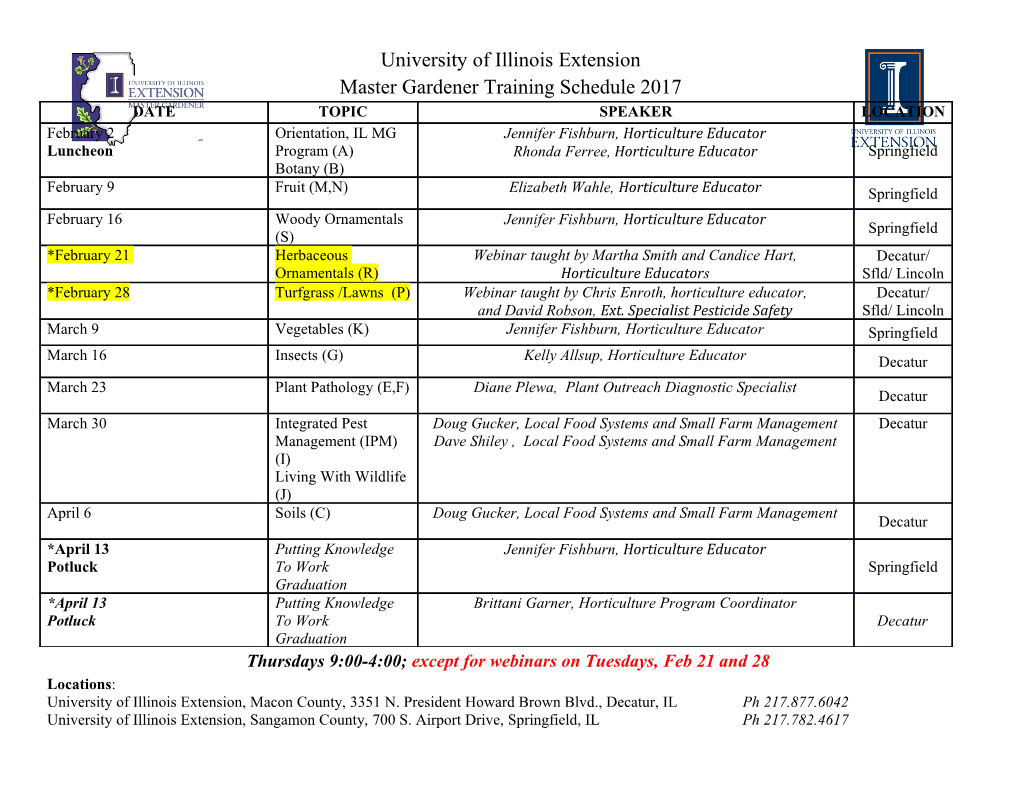
SYNCHRONOUS COMPENSATORS FOR MINI-GRIDS AND ISLANDING Final Report CONTRACT NUMBER: K/EL/00267/00/00 URN NUMBER: 04/1444 The DTI drives our ambition of ‘prosperity for all’ by working to create the best environment for business success in the UK. We help people and companies become more productive by promoting enterprise, innovation and creativity. We champion UK business at home and abroad. We invest heavily in world-class science and technology. We protect the rights of working people and consumers. And we stand up for fair and open markets in the UK, Europe and the world. ii SYNCHRONOUS COMPENSATORS FOR MINI-GRIDS AND ISLANDING K/EL/00267/00/00 URN04/1444 Contractor Econnect Ltd The work described in this report was carried out under contract as part of the DTI Technology Programme: New and Renewable Energy, which is managed by Future Energy Solutions. The views and judgements expressed in this report are those of the contractor and do not necessarily reflect those of the DTI or Future Energy Solutions. First published 2004 Econnect 2004 iii EXECUTIVE SUMMARY Objective The objective of the project was to demonstrate the viability of operating a stand- alone power system with 100% wind power using standard (grid-connected design) induction generator wind turbines, with synchronous compensators and Distributed Intelligent Load Controllers providing voltage control and frequency regulation respectively. Background There is a large global requirement for rural electrification as 2 billion people are without electricity. To supply these by extending existing grid systems would require massive investments in transmission and distribution plant in addition to the power stations to feed them. An alternative is to use local mini-grids to provide electricity using local indigenous renewable resources. The use of non-dispatchable renewable resources requires management of the balance between the available power and the system loads to ensure that the system's voltage and frequency remain within acceptable limits. Econnect has developed a new generation of Distributed Intelligent Load Controllers to enable mini-grids (island grids, wind-diesel systems or autonomous systems) to use one or many standard (grid-connected design) wind turbines. The controllers use highly innovative software algorithms to control system frequency within the statutory limits, based on measurements of the frequency and rate of change of frequency of the supply. This information is processed using a fuzzy control algorithm, embedded in each controller, which informs load-switching decisions. There is no central controller and no communications link between the controllers. The global effect of the independent devices is to maintain power system stability for autonomous power systems powered solely from wind power. The controllers have undergone extensive modelling as well as successful site and laboratory tests on wind turbines. In conjunction with the use of robust and well-established synchronous compensator technology to manage system voltage, the controllers offer a flexible, low-cost and efficient means of incorporating large amounts of renewable energy in electrical power systems. The main purpose of the project was to develop equipment suitable for use in remote locations which would permit islanded operation of wind turbine systems equipped with induction generators. The project aimed to demonstrate methods by which induction wind turbine generators can operate in islanded mode, receiving voltage control from synchronous compensators and frequency control from distributed intelligent load controllers. This was to be achieved by developing a design methodology and applying it to the construction of two test systems, incorporating a 20kW stall-regulated wind turbine and a 300kW pitch-regulated wind turbine respectively. Each wind turbine was to be islanded from the electricity grid, fitted with the synchronous compensator and distributed load control technology, and tested. iv Work carried out The project incorporated the following activities: • Selection of appropriate test sites and agreement with wind turbine operators The 20kW, stall-regulated Gazelle, and the 300kW, pitch-regulated Windmaster were identified as suitable test vehicles. The Gazelle had a simple control system. The Windmaster was more complex than the Gazelle and provided a natural progression in the development of the system. • Data collection for wind turbines, and discussion with manufacturers / operators • System design Suitable synchronous compensators were selected in conjunction with Newage AVK-SEG, and appropriate load control configurations were specified. • Dynamic computer modelling of the system A computer model of each intended autonomous power system was developed using MATLAB / Simulink. Variable wind speed inputs and consumer loads were applied to investigate power quality and system stability. • Specification and procurement of load control hardware, load banks, protection equipment, pony motors, variable speed drives, cabling, and datalogging equipment • Load control software development • System assembly and installation • Development of a modular, PC-based, instrumentation and datalogging system • Production of risk assessment and method statement documents • Transport of equipment to the wind turbine site • Synchronous compensator equipment commissioning • Wind turbine modification The objective during testing was to avoid any modification of the wind turbine system. However, in order to incorporate the synchronous compensator equipment, some changes had to be made. These were minor in the case of the Gazelle but more complex in the case of the Windmaster. • Wind turbine testing Following satisfactory commissioning tests, the wind turbines were disconnected from the grid and connected into the mini-grid system. A variety of tests were carried out, including optimisation of the wind turbine start procedures, simulated wind-diesel operation, and wind-only operation under a range of wind conditions. • Decommissioning of test equipment • Results analysis • Dissemination of the results v Results from computer simulation The results from the computer models predicted successful operation of the stand- alone systems. The simulated control loads were seen to contribute the difference between the varying wind turbine input power and the varying base load power requirement. The random nature of the control load switching was clearly demonstrated. Predicted system frequency was maintained between approximately 48 and 52Hz, slightly outside the BS EN 50160 recommendation. Predicted voltage control was good, well within the required +/-10% of 230V stated in BS EN 50160. The models achieved this with different amounts of base load applied, different ratings of power factor correction capacitors, and different wind speeds. Some voltage imbalance between the phases was predicted and would be expected, since the loads were single-phase loads. On the Gazelle model this imbalance was well within limits; the Windmaster model indicated a potential area of concern. The Windmaster model was employed to investigate the observed starting performance of the wind turbine in more detail, and was used to estimate the effects of modifying the starting strategy. It indicated that most of the power drain on the system during the start was due to the starting resistors rather than the motoring requirement of the wind turbine. Results from wind turbine testing Effective wind-only operation was achieved with both wind turbines. Under these conditions, the only power input into the system was from the wind turbine, and the only frequency (speed) control was provided by the load controllers. No adjustment to the load controller firmware was necessary to achieve stable frequency control in wind-only mode, and no additional adjustment was necessary to the AVR to achieve stable voltage control. Wind-only mode could be maintained stably for as long as there was enough wind to overcome the losses in the system, mainly the synchronous compensator's rotating losses. Periods of wind-only operation were analysed to evaluate each system's performance. Frequency control was good, within the BS EN 50160 requirement of +/-1Hz. With the Gazelle, there was a definite offset, however, with a low mean value of 48.6Hz, which put the system as configured outside acceptable limits. The load controller frequency setpoints were modified for the Windmaster tests and successfully removed this offset. On both systems, a slow oscillation in frequency was observed. The frequency of this oscillation, around 0.4Hz, was well outside the region where flicker would be a problem (8-10Hz). Voltage control was good. The voltages on all three phases remained well within the BS EN 50160 voltage requirements during wind-only operation on both wind turbines. As the load control employed single-phase loads, with no restriction on the relative loading on each phase, this result was particularly encouraging. The values of negative sequence voltage achieved were well within the nominal 2% limit in BS EN 50160. It was an aim of the work to be able to start the wind turbine without adversely affecting the power quality of the system. Starting the Gazelle was achieved with the vi frequency and voltages remaining within required limits. This was not the case with the Windmaster and would be an area for further development of the system. The rotating losses within each system were evaluated. Observed system losses of 10% of the Gazelle's
Details
-
File Typepdf
-
Upload Time-
-
Content LanguagesEnglish
-
Upload UserAnonymous/Not logged-in
-
File Pages61 Page
-
File Size-