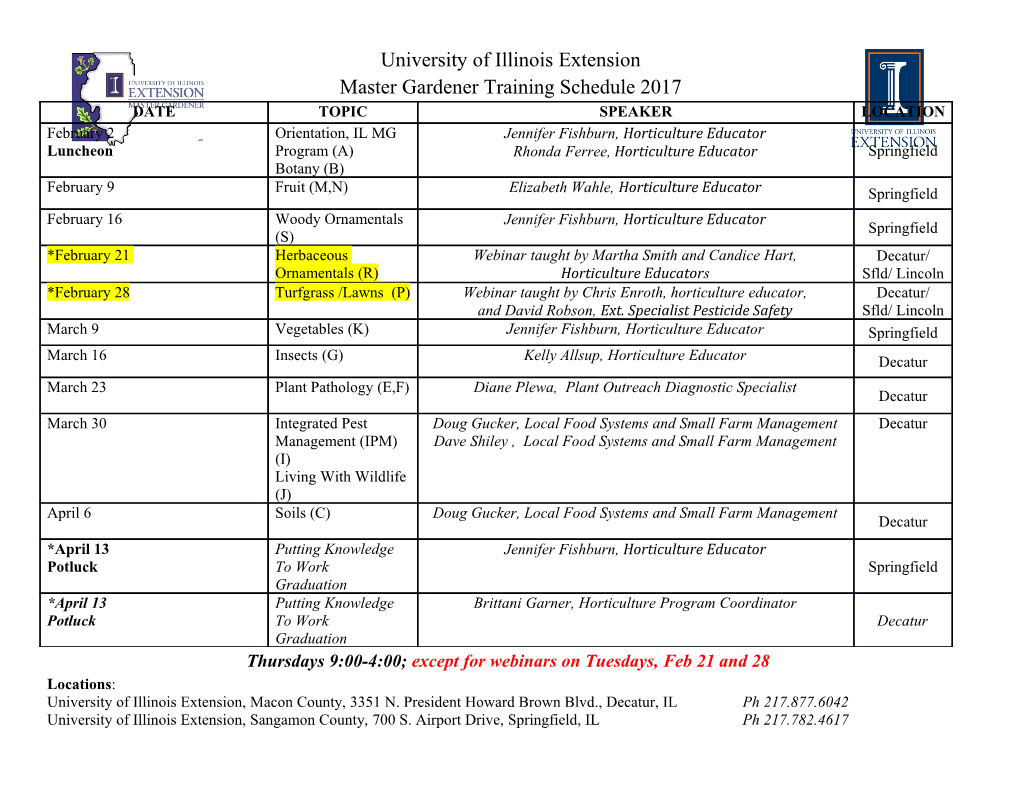
Human Spaceflight Structures Engineering Internship Joshua Peterson NASA’s Johnson Space Center – Spring 2017 University Science Research Association (USRA) 05/11/2017 1 Content • Background • Lightweight External Inflatable Airlock (LEIA) • Cislunar Habitat Module • Artificial Gravity Study • Additional Projects • Conclusions 05/11/2017 2 Content • Background • Lightweight External Inflatable Airlock (LEIA) • Cislunar Habitat Module • Artificial Gravity Study • Additional Projects • Conclusions 05/11/2017 3 Background • Hometown – Suwanee, Georgia • School – Georgia Institute of Technology – 4th Year BS Aerospace Engineering – Graduation: May 2018 • Engineering Work Experience – NASA’s Armstrong Flight Research Center – Lockheed Martin, Missiles and Fire Control – Conway & Owen MEP Consulting Engineers • Engineering Research Experience – Georgia Institute of Technology, High Power Electric Propulsion Laboratory – Georgia Institute of Technology, Unmanned Aerial Vehicle Laboratory 05/11/2017 4 Content • Background • Lightweight External Inflatable Airlock (LEIA) • Cislunar Habitat Module • Artificial Gravity Study • Additional Projects • Conclusions 05/11/2017 5 Lightweight External Inflatable Airlock (LEIA) – Overview • An inflatable crewlock, coupled with an equipment lock, can provide significant weight savings from its metallic counterpart • Inflatable structures only have shape, size, and rigidity when inflated • In order to use an inflatable as an airlock, an additional structure is necessary to maintain shape, size, and rigidity • Conceptual designs based on Bigelow Expandable Activity Module (BEAM) interior envelope Inflatable Tubes Shark Cage Resin Rigidized Structure • Design Concepts – Inflatable Tubes – Shark Cage – Resin Rigidized Structure – Expandable Truss – Inflatable Walls Expandable Truss Inflatable Walls 05/11/2017 6 Lightweight External Inflatable Airlock (LEIA) – Volume Analysis • Compared LEIA volume concepts to the Quest Joint Airlock • Found that all LEIA concepts had plenty of volume to perform airlock procedures • Additional Questions – Will astronauts have trouble rotating to operate EV hatch? Shark Cage Quest Joint Airlock Inflatable Tubes – Will the extra volume in LEIA designs create problems with translation and rotation? 05/11/2017 7 Lightweight External Inflatable Airlock (LEIA) – Shark Cage • Composed of 2024-T3 aluminum tubes • Design includes longitudinal tubes and hoop tubes that are fastened together • Crew will receive Shark Cage in several pieces and assemble within inflatable structure • Major Advantages – Low Mass – High Available Volume – Simple Manufacturing – Simple In-Space Assembly 05/11/2017 8 Lightweight External Inflatable Airlock (LEIA) – Initial Analysis UNITS DESC. MATL SPEC SOURCE Ftu Fsu Fcy • Hand calculations performed on 125 lb. incidental Shark Cage MMPDS-11, 2024-T3 QQ-A-250/4 64 39 42 ksi loads located on outside of EV Hatch Member 3-118 DETAIL LOAD CASE FAILURE MODE M.S.* • The factor of safety used was 2.25 for metallic Shark Cage – EV Hatch 125 lbs AFT Shear Stress +High structure Connection Shark Cage – Midpoint 125 lbs AFT Compression +High • Margins shown are for one longitudinal member with a 2.5” outer diameter and a 1.8” inner Shark Cage – Midpoint 125 lbs AFT Buckling +0.06 Shark Cage – IV Hatch 125 lbs DN Compression +0.52 diameter Connection AFT Load Case DN Load Case 05/11/2017 9 Lightweight External Inflatable Airlock (LEIA) – Initial Analysis • Compared likely weights for Material and Cross Section Weight Comparison aluminum, steel, and titanium tent poles • While each material could withstand all loads with only one 1 Pole pole, the application of more 4 longitudinal members will be 2 3 convenient for handholds and 1 Pole will provide additional stability 6 7 8 1 Pole 2 3 4 5 • Initial Conclusion: Between 4 and 2 3 8 longitudinal members are MS = 0 feasible as a secondary support structure for an inflatable airlock 05/11/2017 10 Lightweight External Inflatable Airlock (LEIA) – FEM Analysis • Set out to optimize the (1) weight of the Shark Cage (2) 500 lb. 500 lb. concept (3) • Loads (4) – Incidental Loads (5) – Crew Egress – Crew Ingress Incidental Loads Crew Egress Crew Ingress – Crew Ingress and Rest 500 lb. 500 lb. – EV Hatch Opening 250 lb. 250 lb. – Crew Movement • Constraints – Longitudinal members fixed to IV Hatch and rigidly connected 250 lb. 250 lb. along EV Hatch Crew Ingress and Rest EV Hatch Opening Crew Movement 05/11/2017 11 Lightweight External Inflatable Airlock (LEIA) – Design Study Margin of Safety v. Longitudinal Members - 2 Hoops • How does the stress change with 1.5 1 OD 0.675" different geometries? 0.5 OD 0.75" M.S. 0 OD 1.0" -0.5 5 7 9 11 13 15 17 • Task: Optimize the Shark Cage design -1 OD 1.5" Number of Longitudinal Members • Design Variables: Margin of Safety v. Longitudinal Members - 4 Hoops 6 – Cross Section Outer Diameter 4 OD 0.675" 2 OD 0.75" M.S. • 5/8”, 3/4”, 1”, 1.5”, 2” 0 OD 1.0" 5 7 9 11 13 15 17 -2 OD 1.5" – Number of Longitudinal Members Number of Longitudinal Members • 6, 8, 12, 16 Margin of Safety v. Longitudinal Members - 5 Hoops 4 OD 0.675" – Number of Circular Members 2 OD 0.75" M.S. 0 • 2, 4, 5 OD 1.0" 5 7 9 11 13 15 17 -2 OD 1.5" Number of Longitudinal Members 05/11/2017 12 Lightweight External Inflatable Airlock (LEIA) – Design Study • The first table displays lightest designs for each number of longitudinal members OD (in) ID (in) Longitudinals Hoops Weight (lbs) Max Stress (psi) M.S. 1.5 1.43 6 2 24 46112 0.387925 – The highlighted design is not the lightest 1.5 1.43 8 2 28 37356 0.713246 overall design but it does provide an optimal 1 0.93 12 4 31 39269 0.629784 amount of members for movement about 1 0.93 16 4 36 37799 0.693166 the airlock Design Trade Summary – This design was chosen for a subscale structural test and a full-scale mockup evaluation DETAIL LOAD CASE FAILURE MODE M.S.* Ultimate Tensile Location 4 125 lbs +X +0.63 • The second table displays the results of the Strength stress analysis performed on the optimized Load Case 34 EV Hatch Opening Compression Yield +0.12 Shark Cage design Load Case 34 EV Hatch Opening Buckling +2.60 – Analysis will be confirmed by full-scale structural test Margin of Safety Summary 05/11/2017 13 Lightweight External Inflatable Airlock (LEIA) – Compression Test UNITS DESC. MATL SPEC SOURCE Ftu Fsu Fcy Shark Cage MMPDS-11, • Finite element analysis is a useful 6061-T6 WW-T-700/6 42 34 35 ksi Member 3-447 tool, but Shark Cage must be tested before it is considered flight ready • Developed a 1:10 scale FEM of Shark Cage which uses the geometry and material of the small-scale test article developed by Mykale – Determined likely failure modes and ultimate stresses – Will correlate test data to FEA data 05/11/2017 14 Lightweight External Inflatable Airlock (LEIA) – Compression Test • Test consisted of 3 configurations each with 4 hoop tubes: 4, 8, and 16 longitudinal tubes were arranged in a small scale test article • Small-scale test article was 1:10 scale to size of Bigelow Expandable Activity Module (BEAM) • Each configuration was compressed until failure in a load frame 05/11/2017 15 Lightweight External Inflatable Airlock (LEIA) – Compression Test • The small-scale compression test showed my FEA was conservative and needs to be Analytical Prediction tuned to represent real-world results Expected Expected Expected Expected Observed • Error between FEA and Test Data: Test Article Number of Yield Ultimate Buckling Max Elastic Failure Configuration Longitudinals = X 100 Strength Strength Strength Deflection Load − – Configuration A: 60% (UTS) A 4 375 lbf 500 lbf 625 lbf 0.0569 in 800 lbf B 8 1125 lbf 1375 lbf 1500 lbf 0.0307 in 2500 lbf – Configuration B: 67% (Buckling) C 16 3000 lbf 3875 lbf 3500 lbf 0.0350 in 3000 lbf – Configuration C: -23% (UTS) • Possible sources of discrepancy Shark Cage: Load-Displacement Data 3500 – All members except EV Hatch connections in Plastic Fastener UTS Failure 3000 FEA were clamped-clamped configuration (did Local Buckling Failure not account for fasteners and distributed load 2500 2000 interactions) 4C 4L 1500 Ultimate Tensile Strength Failure Load(lbf) 4C 8L – EV hatch longitudinal connections in FEA were 1000 4C 16L allowed to rotate 500 – Did not take into account the plastic connectors 0 0.00E+00 -5.00E-02 -1.00E-01 -1.50E-01 -2.00E-01 -2.50E-01 -3.00E-01 -3.50E-01 -4.00E-01 -4.50E-01 used in assembly of test article Vertical Displacement (in) 05/11/2017 16 Lightweight External Inflatable Airlock (LEIA) – Future Work • Refine FEM for better correlation with test data • Develop and test full-scale mock-ups of Inflatable Tube and Shark Cage design • Continue developing resin rigidizable technology • Launch and test final concept on ISS 05/11/2017 17 Content • Background • Lightweight External Inflatable Airlock (LEIA) • Cislunar Habitat Module • Artificial Gravity Study • Additional Projects • Conclusions 05/11/2017 18 Cislunar Habitat Module – Overview • Working to develop next generation space station habitat modules for cislunar space • ISS era modules carried launch loads and instruments around the outer edge of the module • Future cislunar modules will carry launch loads and instruments in the center of the module core structure much like a fighter jet 05/11/2017 19 Cislunar Habitat Module – Task • Previous cislunar habitat module model had a diameter of 4.0 m • Redesigned the module with a maximum diameter for the SLS – Block 1 Fairing – Increased diameter to 5.6 m – 40% larger diameter than previous model 05/11/2017 20 Cislunar Habitat Module – Analysis • Rebuilt finite element model in Femap and used Load Case Axial Load (G) Lateral Load (G) NASTRAN to analyze stress within the structure Transonic X -2 0.75 Transonic Y -2 0.75 • Expected Loads Max Q X -2.5 0.5 Max Q Y -2.5 0.5 – SLS Launch Boost Max X -3.25 0.3 Boost Max Y -3.25 0.3 – Operational / Docking Core Max X -3.5 0.3 Core Max Y -3.5 0.3 Conservative X -4 2 • A safety factor of 1.4 for UTS and buckling and 1.0 for Conservative Y -4 2 yield during launch was used per NASA document SSP-30559-C, Section 3.3.1.
Details
-
File Typepdf
-
Upload Time-
-
Content LanguagesEnglish
-
Upload UserAnonymous/Not logged-in
-
File Pages44 Page
-
File Size-