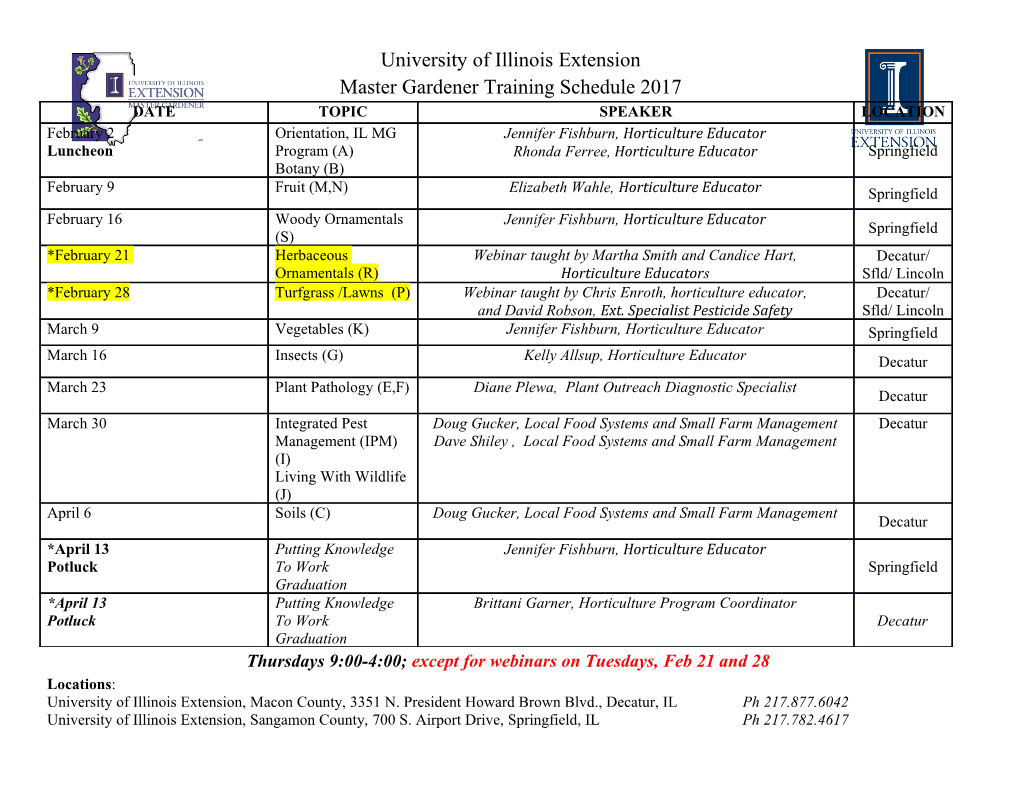
Working fluid selection and performance comparison of subcritical and supercritical organic Rankine cycle (ORC) for low- temperature waste heat recovery Stéphanie Jumel Michel Feidt EDF – Recherche et Développement Theoretical and Applied Energy and Mechanics Laboratory Département Eco-efficacité des Procédés Industriels CNRS, LEMTA, UMR 7563 Site des Renardières F-54500 Vandoeuvre-lès-Nancy 77818 Moret sur loing Cedex France France [email protected] [email protected] Abdelhamid Kheiri Van Long Le (corresponding author) Theoretical and Applied Energy and Mechanics Laboratory Theoretical and Applied Energy and Mechanics Laboratory CNRS, LEMTA, UMR 7563 CNRS, LEMTA, UMR 7563 F-54500 Vandoeuvre-lès-Nancy F-54500 Vandoeuvre-lès-Nancy France France [email protected] [email protected] Keywords waste heat, industrial processes, heat recovery ergy demand is projected to increase from 12,150 Mtoe in 2009 to 16,950 Mtoe in 2035, an increase of 40 %, or 1.3 % Abstract growth per year . Consequently, solutions to face fossil fuels run out have to be found. Nuclear energy can contribute to In the industrial and daily processes, a big amount of energy is meeting the growing demand for energy, but safety and nucle- lost as waste heat. This heat source reduces not only the energy ar waste treatment constrains are also limiting the use of this efficiency of industrial process but it also contributes to green- resource. Therefore, renewable energy production (i.e. solar house gases emissions and thermal pollution. In this context, energy, geothermal energy) is attracting much attention. Most the CERES project (Energy pathways for waste heat recovery in of those renewable energy resources cannot be economically industrial systems), financed by the French National Research transformed into electricity by the traditional steam cycle Agency, aims at developing a decision-making tool to optimize which requires a high-temperature heat source (> 350 °C). waste heat recovery in industrial process. Through this plat- Thus, many thermodynamic cycles for converting low-grade form, the comparison of various technologies (heat pumps, heat into electrical power have been studied, i.e. Kalina cycle, thermoelectricity, ORC …) based on technico-economic basis Goswami cycle, Trilateral Flash cycle, organic Rankine cycles will be possible. (subcritical and supercritical Rankine cycle). Among these In the article, it is proposed to describe one of these tech- cycles, Organic Rankine Cycles are less complex and require nologies, the Organic Rankine Cycles (subcritical and super- less maintenance. Therefore these cycles have aroused much critical cycle), which can be used to valorize low-temperature interest. waste heat. In addition, industrial waste heat recovery is also of great in- The Organic Rankine Cycle performances were analyzed terest. As a matter of fact, industrial sector energy consumption and compared via their thermal efficiencies and exergy analy- is about 27 % of total world energy consumption (2,282 Mtoe in sis. Both of these cycles used a heat source simulated by hot air 2009) (Figure 1.) and many national and international projects with an inlet temperature of 170 °C and a heat sink that is water are carried out to improve the energy efficiency of the indus- at ambient temperature to cool down and condense the work- trial processes. ing fluid. The performance calculations and the cycle simula- In practice, a large amount of energy is still lost as waste tion were carried out by Engineering Equation Solver (EES). heat. This waste heat is generated during a combustion process or several other chemical/thermal processes, then is directly Introduction evacuated in environment (Tchanche, Lambrinos et al. 2011). Nowadays, just as world population is growing, so is world In United States of America, 20–50 % or more of energy inputs energy consumption. According to the New Policies Scenario are possibly lost at the end through flue gases, evaporative or in world energy outlook 2011 (IEA 2011), world primary en- radioactive heat losses and in waste steam and hot water in the ECEEE 2012 SUMMER STUDY on EnergY EffiCiEncy in industry 559 4-086-12 Jumel et al 4. UNDERTAKING HIGH IMPACT ACTIONS: TECHNOLOGY AND … The CERES Project The CERES project is an answer to the need of the energy efficiency and reduction of greenhouse gas emissions in the industry through waste heat recovery. Indeed, the project (2011–2013), supported by the French National Research Agency (ANR), is aimed at developing a decision-making tool to identify the optimal solutions of industrial waste heat recov- ery. This tool will rely on the simulation of industrial processes and waste heat technologies (modelled in Modelica language) under Open Modelica or Dymola environment and a multi- objectives optimisation platform. The use of the tool will allow the selection of the waste heat recovery solutions according to technico-economic criteria. Several processes from Food and Figure 1. Energy consumption in EU-27 (EU 2011). Drink, Metals and Pulp and Paper industries will be studied during the project. Various technical solutions for direct heat recovery (heat exchangers, heat storage, compression and ab- sorption heat pump) or electricity production (thermoelectric- ity, Organic Rankine Cycles …) will be considered (as illus- trated in Figure 3). Among the technologies studied in the CERES Project, ORC technology is particularly interesting for low temperature waste heat recovery. According to the research of (Lakew and Bolland 2010), many industrial processes and power plants emit waste heat at low-temperature (ca 80–200 °C). This papers describes the work currently done to characterize this technology. In this work, a heat source which is hot air at 170 °C was chosen for simulation of ORC system. Subcritical organic Rankine cycles In general, the principle of the Organic Rankine Cycles is the Figure 2. Heat losses in industrial heating processes (source: same as that of the steam water Rankine cycle which includes http://www1.eere.energy.gov). the following components: pump, evaporator, turbine and con- denser but the working fluid is often an organic compound (i.e. refrigerants). In this cycle, working fluid at saturated liquid state industrial plants (Pellegrino, Margolis et al. 2004). Many heat is pumped to the heat exchanger in which it is heated, vapor- losses of an industrial heating process are illustrated in Fig- ized, even superheated by a heat source (i.e. waste heat, thermal ure 2. These waste heat sources not only contain an important oil, hot brine or steam). Then, the vapour at saturated or super- value of thermal exergy but also a large quantity of pollutants: heated state is introduced in the turbine linked with an electri- CO2, NOx, SOx which is responsible for environmental harm- cal generator to produce the electricity. At the turbine exit, the ful impacts (Global warming, acid rain, etc.). According to the working fluid is cooled down and condensed by a heat sink (i.e. report of U.S Environmental Protection Agency, the energy ambient air or cool water) in the condenser before being intro- efficiency of industrial processes can be improved from 10 to duced in the pump to complete and start again the cycle. 50 % with the heat recovery (EPA 1998). The first organic Rankine cycle was built in 1883, by Frank The heat losses in industrial heating processes in the Fig- W. Ofeldt who developed a naphtha engine, i.e. a closed loop ure 2: steam engine that used naphtha instead of water as working fluid (Towne 1991). • Losses in heat storage in the furnace structure The principle of the subcritical Rankine cycle and T-s dia- • Losses from the furnace outside walls or structure gram of R-245fa are illustrated in Figure 4. In reality, a big su- perheating of the vapour in subcritical Rankine cycle would not • Heat transported out of the furnace by the load conveyors, be realized because of the low-exchange coefficient for the gase- fixtures, trays, etc. ous phase (Schuster 2008). Indeed, it is always selected when • Radiation losses from openings, hot exposed parts, etc. the critical temperature of working fluid is higher than heat source temperature (Pan, Wang et al. 2012). • Heat losses carried by the cold air infiltration into the fur- nace Supercritical Organic Rankine cycles • Heat losses carried by the excess air used in the burners. In the state-of-art applications, which are discussed nowadays, saturated or slightly superheated vapour is expanded in the turbine. However, the investigation of the supercritical fluid 560 ECEEE 2012 SUMMER STUDY on EnergY EffiCiEncy in industry 4. UNDERTAKING HIGH IMPACT ACTIONS: TECHNOLOGY AND … 4-086-12 Jumel et al Heat Power Heat recovery solution B Heat recovery solution C Heat recovery solution A Heat recovery solution D Heat recovery solution E T < T1 T> T2 HEX Compression HP ORC Thermoelectricity Legends : Process Process operation Reuse T2 T3 du procédé T1 Waste heat source Hot flue gaz Hot Liquid Hot solid product chaud chaud Waste heat recovery technology Raw Final Materials Operation 1 Operation 2 Operation 3 Product Figure 3. Examples of waste heat recovery solutions according to heat sources. Figure 4. Configuration of a subcritical organic Rankine cycle (left) and T-s diagram of R-245fa (right). parameters is of high importance, since it may lead to higher (e.g. 60–160 bars for CO2 supercritical cycle), the safety con- efficiencies making these plants even more attractive for waste cern, and the investment cost rise due to special materials of heat applications (Schuster, Karellas et al. 2010). The working the system. In present, the supercritical cycle with CO2 as the fluid at the exit of the condenser is directly pumped from satu- working fluid had paid a lot of attention thanks to its desir- rated liquid state to the supercritical pressure in supercritical able properties such as moderated critical point, stability, little Rankine cycle (Figure 5).
Details
-
File Typepdf
-
Upload Time-
-
Content LanguagesEnglish
-
Upload UserAnonymous/Not logged-in
-
File Pages11 Page
-
File Size-