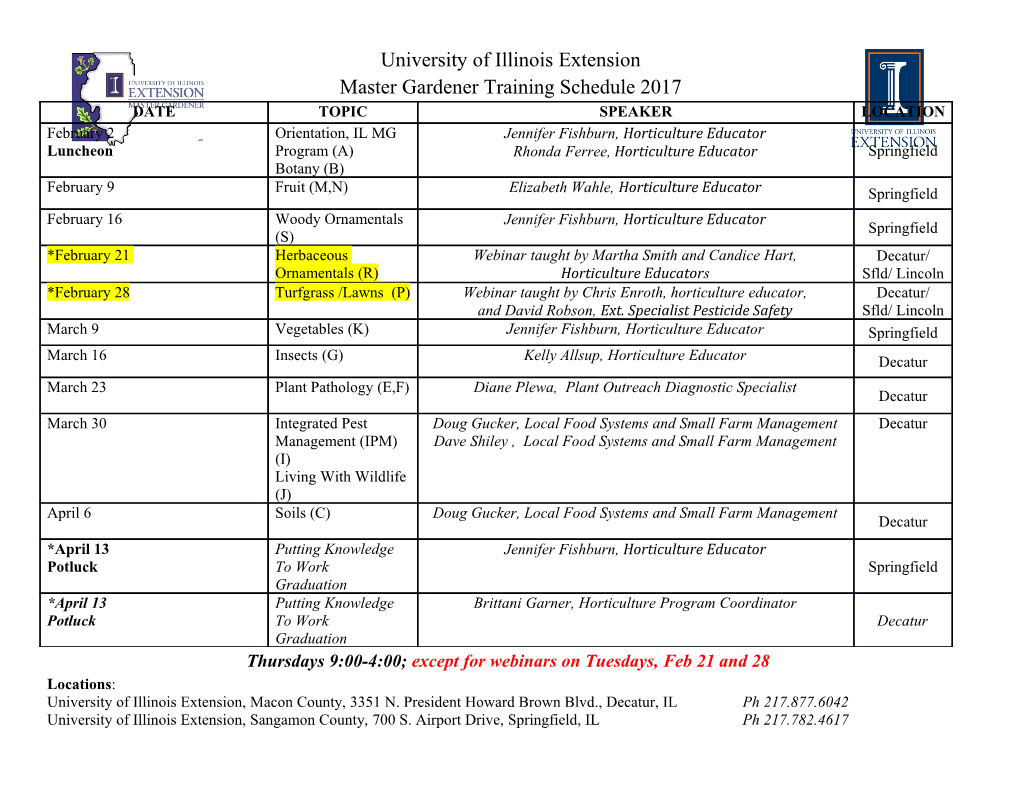
The University of New South Wales Faculty of Science School of Materials Science and Engineering Gaseous Reduction of Titanoma·gnetite Ironsand Eungyeul Park A Thesis submitted in Partial Fulfilment Of the Requirements For the Degree of Doctor of Philosophy September 2002 CERTIFICATE OF ORIGINALITY I hereby declare that this submission is my own work and to the best of my knowledge it contains no materials previously published or written by another penon, nor material which to a substatial extent bas been accepted for the award of any other degree or diploma at UNSW or any other educational institution, except where due acknowledgement is made in the thesis. Any contribution made to the research by others, with whom I have worked at UNSW or elsewhere, is explicitly acknowledged in the thesis. I also declare that the intellectual content of this thesis is the product of my own work, except to the extent that assistance from othen in the project's design and conception or in style, pre acknowledged. ii To My Family iii ACKOWLEDGEMENT I would like to thank my supervisor, Professor Oleg Ostrovski. I have learnt from him what is an engineer as well as what is Doctor of Philosophy. I am grateful for his enthusiasm and kind guidance throughout my study. He always encouraged me with deep patience. I also wish to express my special gratitude to my supervisor for providing financial support during my study. I wish to thank Dr. G. Zhang for the experimental set-up and his help in valuable discussions on the project, Dr. J. Zhang for his help in the former project on iron carbide process, and Dr. S. Gaal for his assistance in experimental set-up and many analysis techniques. Also, I would like to thank Mr. N. Anacleto for the discussions on the fundamentals of thermodynamics. The discussions with them always gave me new ideas and showed further directions. The technical support provided by technician staff in the School of Materials Science and Engineering, UNSW, are also acknowledged. I thank Mr. R. Longbottom, for conducting experiments on the reduction of ironsand by methane-containing gas mixtures. I am thankful to the staff in Electron Microscope Unit, especially, Mr. B. Searle for his guidance in using and understanding EPMA, and Ms. V. Piegerova for SEM. The special thanks should be given to Dr. S. Blimyukov, Dr. S. Thomson and Prof. R. Howe, for their guidance in surface analysis. I thank to my good Aussie friends, Tim, Big Brad and Small Brad. Their warm heart made me feel home in Australia. I appreciate Prof. Dong Jun Min in Yonsei University, Korea, for the valuable discussions and encouragement. I wish to thank Prof. Chang Hee Rhee in POSTECH, Korea. He gave me the chance to study in UNSW and encouraged my work. Finally, I would like to thank my family. iv PUBLICATIONS ORIGINATED FROM TIDS PROJECT I. Eungyeul Park, Jianqiang Zhang, Stuart Thomson, Oleg Ostrovski and Russell Howe: "Characterisation ofPhases Formed in the Iron Carbide Process by XRD, Mossbauer, XPS, and Raman Spectroscopy Analyses" Metallurgical and Materials Transaction B, 32B (5), p839-845, 2001. 2. Eungyeul Park and Oleg Ostrovski, "Reduction ofTitania-Ferrous Ore by CO­ COrAr Gas Mixture'\ Proceedings of I st International Conference on Advanced Materials Processing, p90-98, 19-23 Nov 2000, Rotorua, New Zealand V ABSTRACT This project examined the gas-solid reduction of New Zealand ironsand which contains 50-60wt°/o of iron and 7-8wt% ofTiO2• The project's aim was to develop further understanding of the reduction mechanism of ironsand by gas-solid reaction with a focus on a structure of ironsand and its transformation during reduction. The reduction of ironsand was investigated in non-isothermal and isothermal reduction experiments using carbon monoxide, hydrogen and methane-containing gas mixtures in a laboratory fixed bed reactor in the temperature range of 700-1100°C. Samples in the course of reduction were characterised using XRD, EPMA, SEM, optical microscope and BET analysis. Ironsand 's structure and phase composition. Two types of particles were identified in raw ironsand; the major type was represented by homogeneous particles of cubic spine} titanomagnetite; and the others, non­ homogeneous particles, were characterised by lamellar structure of rhombohedral titanohematite, exsoluted from the titanomagnetite. The formula oftitanomagnetite was established to be (Fe3O4 ),_x(Fe2TiO4 )x, with the x value of 0.27±0.02. The reduction sequence. Titanomagnetite was reduced to metallic iron and titanium sub-oxides via wustite, ulvospinel and ilmenite in -the following sequence: Fe3_xTixO4 -+" FeO"+Fe + Fe3_x_6 Tix+ 6 O4 -+Fe+ Fe3_x_6 Tix+ 6 O4 -+ Fe+Fe2TiO4 -+ Fe+FeTiO3 -+ Fe+TiO2 -+ Fe+Ti3O5 -+ Fe+Ti2O3 {x= 0.27±0.2; 8, degree ofreaction, 0 ~ '5~(1-x)). Reduction kinetics. The rate limiting stage in the ironsand reduction was the reduction of titanomagnetite to wustite, which involves the reduction 3 2 ofFe + to Fe +. The reduction of the intermediate phases, wustite and ulvospinel proceeded quickly. In the reduction of raw ironsand, the lamellar vi titanohematite phase reduced with higher rate than titanomagnetite, enhancing the overall ironsand reduction rate. Retarding effect oftitanium on the iron oxide reduction. Titanium, which is present in the ore mainly in the titanomagnetite, has a strong effect 4 3 on the mechanism and rate of iron oxide reduction. Ti + substitutes Fe + at octahedral sites of spinel lattice, decreasing Fe3+ activity and increasing Fe2+activity. This retards reduction ofFe3+ to Fe2+, which is a rate-limiting stage in the reduction of titanomagnetite. Effect ofcalcination and preoxidation on the ironsand structure and reduction. The phase composition was not affected by calcination at 1100°C. Preoxidation of ironsand at l 000°C transformed titanomagnetite in ironsand to titanohematite (Fe2.yTiyO3, rhombohedral) and then partly to pseudobrookite (Fe2 TiO5). The preoxidation of ironsand enhanced its reduction as a result of structural transformation of cubic spinel titanomagnetite to rhombohedral titanohematite in preoxidation. The reduction experiments of the raw and the preoxidised ironsand showed that the slow reduction of New Zealand ironsand is due to two factors; 1) the spinel cubic structure oftitanomagnetite and 2) the thermodynamic stability of titanomagnetite due to the substitution of titanium. For further application of ironsand to DRI process, the project suggests the gaseous reduction of the preoxidation of ironsand is more economical than the carbothermic reduction. The project contributes to further understanding of reduction of titanomagnetite ironsand. vii Contents CERTIFICATE OF ORIGINALITY 11 ACKNOWLEDGEMENTS 1v PUBLICATIONS ORIGINATED FROM THIS PROJECT v ABSTRACT vi CONTENTS viii LIST OF FIGURES xn LIST OF TABLES xvn Chapter 1. Introduction I Chapter 2. Literature Review 4 2.1. Ironsand deposits 4 2.1.1. Characteristics of ironsand deposits 5 2.2. Structure and thermodynamics of ironsand 6 2.2.1. Structure and thermodynamic properties of titanomagnetite 7 2.2.1.1. Structure oftitanomagnetite 7 2.2.1.2. Mixing properties of magnetite and ulvospinel in I 0 titanomagnetite 2.2.1.3. Effect of impurities on structural properties oftitanomagnetite 12 2.2.2. Phase relations in the Iron-Titanium-Oxygen system 13 2.2.3. Summary 18 2.3. Reduction of iron ore 19 2.3.1. Thermodynamics of iron ore reduction 19 2.3 .1.1. Structure of iron oxides 19 2.3.1.2. Thermodynamics of the gaseous reduction of iron oxides 21 2.3.2. Kinetics of iron ore reduction 22 2.3.3. Summary 26 2.4. Reduction of Iron-Titanium oxides 27 2.4.1. Reduction of ilmenite ore 27 2.4.2. Reduction of ironsand ore 30 2.4.2.1. The use ofironsand in steelmaking 30 viii 2.4.2.2. Reduction oftitanomagnetite ironsand 32 2.4.3. Summary 37 2.5. Objectives of the Project 38 Chapter 3. Experimental 40 3 .1. Materials 40 3.1.1. New Zealand ironsand 40 3.1.2. Iron ore 41 3.1.3. Gases 42 3.2. Experimental setup 43 3.2.1. Experimental furnace and reactor 43 3.2.2. Gas system 44 3.2.3. Monitoring of gas composition 47 3.2.3.1. Mass spectrometer 47 3.2.3.2. Dew Point Monitor 47 3.3. Analytical instruments 48 3.3.1. X-ray Diffraction analysis 48 3.3.2. Electron Probe Microanalysis 48 3.3.3. SEM analysis 50 3.3.4. Optical microscope analysis 50 3.3.5. LECO analysis 50 3.3.6. BET analysis 50 3.4. Experimental procedures 51 3.4.1. Isothermal reduction 51 3.4.2. Temperature-programmed reduction 52 3.4.3. Sample analyses 53 3.5. Data analysis 53 3.5.1. Calculation of the extent ofreduction 54 Chapter 4. Characterisation of Ironsand Ore 55 4.1. Characterisation of raw ironsand 55 4.1.1. Phase composition of the raw ironsand ore 55 4.1.2. Surface area, pore volume and size of the raw ironsand ore 61 ix 4.2. Pretreatment of ironsand 62 4.2.1. Preoxidation of ironsand 62 4.2. l. l. Non-isothermal oxidation 62 4.2.1.2. Isothermal oxidation 65 4.2.1.3. Behaviour of impurities 71 4.2.1.4. Thermodynamics of oxidation of titanomagnetite 73 4.2.2. Calcination of raw ironsand 75 4.2.2.1. Non-isothermal calcination 75 4.2.2.2. Isothermal calcination 78 4.2.3. Surface area ofpreoxidised and calcined ironsand 79 4.3. Morphology 81 4.4. Summary 85 Chapter 5. Gas-Solid Reduction of lronsand Ore 86 5.1. Temperature-programmed reduction ofironsand 86 5.1.l. Reduction of raw ironsand 86 5.1.2. Reduction of pretreated ironsand 91 5.1.2.1. Effect ofpreoxidation 93 5.1.2.2.
Details
-
File Typepdf
-
Upload Time-
-
Content LanguagesEnglish
-
Upload UserAnonymous/Not logged-in
-
File Pages186 Page
-
File Size-