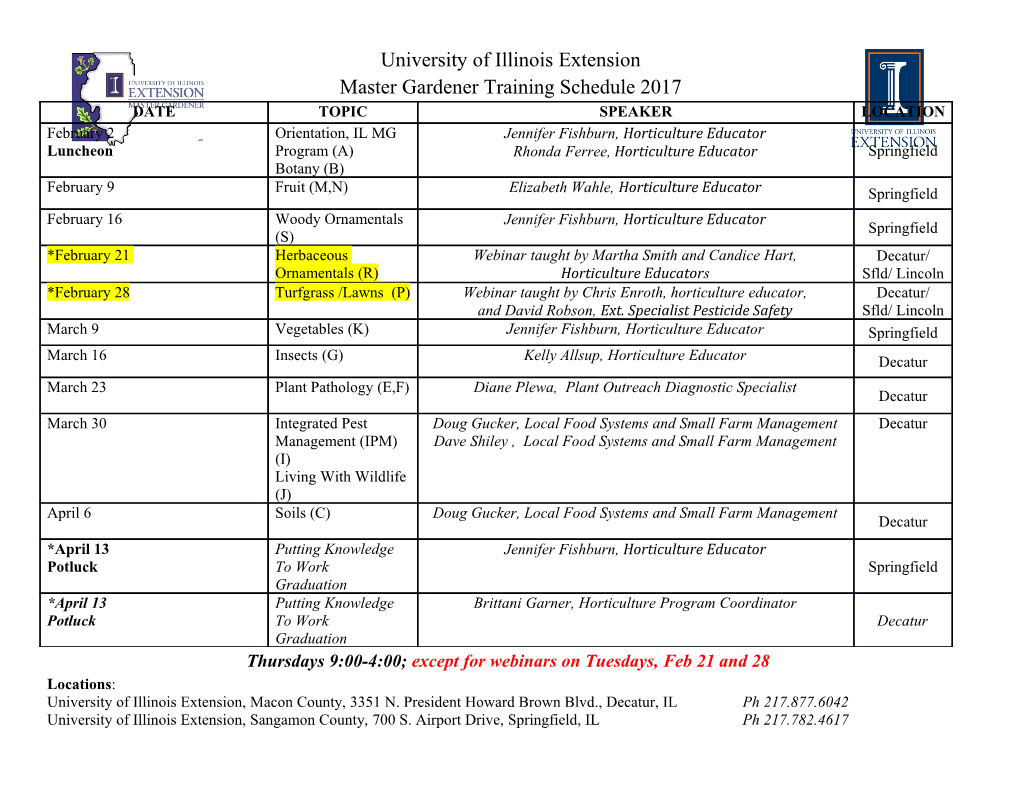
AIAA 2016-4364 AIAA AVIATION Forum 13-17 June 2016, Washington, D.C. 16th AIAA Aviation Technology, Integration, and Operations Conference Slippery When Wet: The Case for More Conservative Wet Runway Braking Coefficient Models John J. O’Callaghan1 National Transportation Safety Board, Washington, D.C., 20594 Over the past eight years, the NTSB has led or participated in the investigation of a number of runway overrun accidents and incidents that occurred after the airplanes involved landed on wet runways. An analysis of the airplane stopping performance during these events indicates that the wheel braking friction coefficient (B) achieved during the landing roll was significantly less than the B predicted by industry-accepted models, and less than the B assumed in the wet-runway landing distance advisory data provided in the manufacturers’ Airplane Flight Manuals. In recognition of this problem, the Federal Aviation Administration has issued a safety alert to operators warning them that the advisory data for wet runway landings may not provide a safe stopping margin under all conditions, and tasked an Aviation Rulemaking Advisory Committee with reviewing the wet runway stopping performance requirements contained in the 14 Code of Federal Regulations (CFR) Part 25 airworthiness standards and guidance (the B that can be assumed on a wet runway during an aborted takeoff is specified by 14 CFR 25.109, and the 25.109 model has been proposed for computing landing distances on a wet runway). This paper presents six wet runway landing overrun events (all involving turbojet airplanes) and compares the B achieved by the airplane in each event with the B predicted by several models and inherent in advisory data. The results indicate that current models and advisory data can significantly overestimate the B achievable on wet runways (and therefore underestimate the required runway length for landing on these runways). Consequently, these events underscore the need for more conservative models of B, and more conservative use of existing advisory data and models in the meantime. Nomenclature Acronyms AA American Airlines AC Advisory Circular AFM Airplane Flight Manual AIR SAE Aerospace Information Report AMC Acceptable Means of Compliance (EASA) AMJ Advisory Material Joint (Europe) Downloaded by BOEING COMPANY on March 17, 2017 | http://arc.aiaa.org DOI: 10.2514/6.2016-4364 ARAC Aviation Rulemaking Advisory Committee ASOS Airport Surface Observation System ATIS Automatic Terminal Information Service BA Bombardier Aerospace BCAR British Civil Aviation Requirements CFME Continuous Friction Measurement Equipment CFR Code of Federal Regulations CG Center of Gravity CMB Combined model CS Certification Specification (EASA) CVR Cockpit Voice Recorder CYMX Montreal Mirabel Airport, Montreal, Canada CYOW Ottawa/MacDonald-Cartier International Airport, Ottawa, Ontario 1 National Resource Specialist – Aircraft Performance, Office of Research and Engineering, RE-60, Member AIAA. 1 American Institute of Aeronautics and Astronautics This material is declared a work of the U.S. Government and is not subject to copyright protection in the United States. DFT Neubert Aero Corporation Dynamic Friction Tester CFME device EASA European Aviation Safety Agency EPB Emergency / Parking Brake ESDU Engineering Science Data Unit EU OPS European operational regulation(s) FAA Federal Aviation Administration FDR Flight Data Recorder FTHWG Flight Test Harmonization Working Group ICAO International Civil Aviation Organization ILS Instrument Landing System IMC Instrument Meteorological Conditions JAR European Joint Aviation Regulations JCAA Civil Aviation Authority of Jamaica KCXO Lone Star Executive Airport, Conroe, Texas KMDW Chicago Midway Airport, Chicago, Illinois KOWA Owatonna Degner Regional Airport, Owatonna, Minnesota KSGR Sugar Land Regional Airport, Sugar Land, Texas MAINT LEVEL AC 150/5320-12C Maintenance Planning Friction Level MIN LEVEL AC 150/5320-12C Minimum Friction Level MKJP Norman Manley International Airport, Kingston, Jamaica MM Mu meter CFME device NAC Neubert Aero Corporation NASA National Aeronautics and Space Administration NEW LEVEL AC 150/5320-12C New Design/Construction Friction Level NRC National Resource Council of Canada NTSB National Transportation Safety Board RCAM Runway Condition Assessment Matrix REP LEVEL Average of AC 150/5320-12C MIN LEVEL and MAINT LEVEL RNAV Area Navigation (instrument approach) SAE Society of Automotive Engineers SAFO Safety Alert For Operators SFT Airport Surface Friction Tester CFME device SW Southwest Airlines TALPA ARC Takeoff/Landing Performance Assessment Aviation Rulemaking Committee TAPHC Transport Airplane Performance and Handling Characteristics TC Transport Canada TSB Transportation Safety Board of Canada TTI Texas Transportation Institute UE United Express Airlines USA United States of America UTC Universal Coordinated Time Downloaded by BOEING COMPANY on March 17, 2017 | http://arc.aiaa.org DOI: 10.2514/6.2016-4364 WOW Weight On Wheels English symbols d Average water depth above the top of the runway macrotexture Longitudinal reaction force at nose gear Longitudinal reaction force at main gear Force along body x-axis Force along body z-axis I Rainfall intensity k Factor on to account for installation and undercarriage effects = (|:) / ( |.) = (|:) / ( |.) L Runway drainage path-length (distance from runway centerline) Moment about body y-axis 2 American Institute of Aeronautics and Astronautics Longitudinal load factor Vertical reaction force at nose gear Vertical reaction force at main gear Tire pressure Effective tire radius Wheel slip ratio , Wheel slip ratio for , Runway cross slope T Average runway macrotexture depth Airplane speed (airspeed or groundspeed depending on context) Takeoff decision speed Groundspeed Groundspeed vector Hydroplaning speed (for dynamic hydroplaning) , Spin-down hydroplaning speed (rotating tire) , Spin-up hydroplaning speed (nonrotating tire) Tangential speed of tire VREF Landing reference speed Airplane weight Component of airplane weight along body x-axis Component of airplane weight along body z-axis Airplane body coordinate system x (longitudinal) axis; see Fig. 1 Airplane body coordinate system z (vertical) axis; see Fig. 1 Greek symbols Angle of attack Flight path angle Anti-skid braking system efficiency Pitch angle Friction coefficient Wheel braking friction coefficient , Average in the range of 0.1 ≤ ≤ 0.5 |: CFME values at 50 mph transformed into airplane by NASA model , Maximum wheel braking friction coefficient (at ,) , Wheel braking friction coefficient with locked wheels (i.e., at =1) , Characteristic dry of an airplane , Characteristic dry of a CFME device , Characteristic dry of the NAC DFT CFME device Downloaded by BOEING COMPANY on March 17, 2017 | http://arc.aiaa.org DOI: 10.2514/6.2016-4364 , Characteristic dry of the Findlay Griptester CFME device , Characteristic dry of the SFT CFME device Runway measured by a CFME device Runway measured by the NAC DFT CFME device , Dry-runway (or “characteristic dry”) friction coefficient Rolling friction coefficient at nose gear , / Maximum available on runway |. specified by §25.109(c), at the airplane corresponding to the CFME device speed of 50 mph, and the airplane |: CFME at 50 mph transformed into runway by NASA model Runway measured by the SFT CFME device Wet-runway friction coefficient Wheel angular velocity 3 American Institute of Aeronautics and Astronautics I. Introduction VER the past eight years, the National Transportation Safety Board (NTSB) has led or participated in the Oinvestigation of a number of runway overrun accidents and incidents that occurred after the airplanes involved landed on wet runways. An analysis of the airplane stopping performance during these events indicates that the wheel braking friction coefficient () achieved during the landing roll was significantly less than the predicted by industry-accepted models, and less than the assumed in the wet-runway landing distance advisory data provided in the manufacturers’ Airplane Flight Manuals (AFMs). In recognition of this problem, the Federal Aviation Administration (FAA) has issued a safety alert for operators (SAFO) warning them that the advisory data for wet runway landings may not provide a safe stopping margin under all conditions, and tasked an Aviation Rulemaking Advisory Committee (ARAC) with reviewing the wet runway stopping performance requirements 2 contained in the 14 Code of Federal Regulations (CFR) Part 25 airworthiness standards and guidance (the that can be assumed on a wet runway during an aborted takeoff is specified by §25.109, and the §25.109 model has been proposed for computing landing distances on a wet runway). This paper presents six wet runway landing overrun 3 events (all involving turbojet airplanes) and compares the achieved by the airplane in each event with the predicted by several models and inherent in AFM advisory data. The results indicate that current models and advisory data can significantly overestimate the achievable on wet runways (and therefore underestimate the required runway length for landing on these runways). Consequently, these events underscore the need for more conservative models of , and more conservative use of existing advisory data and models in the meantime. The landing overrun events considered in this paper are: 1. The BAe 125-800A accident in Owatonna, MN (NTSB #DCA08MA085); 2. The American Airlines
Details
-
File Typepdf
-
Upload Time-
-
Content LanguagesEnglish
-
Upload UserAnonymous/Not logged-in
-
File Pages74 Page
-
File Size-