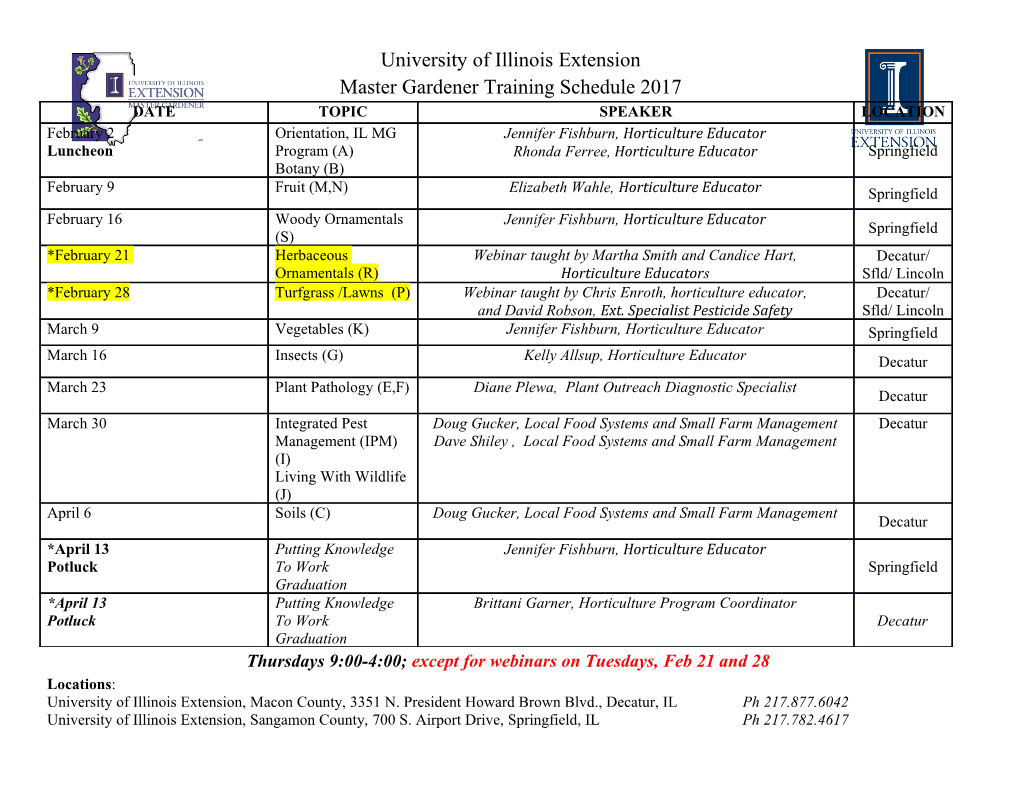
International Journal of Fracture, Vol. 11. No 4 August 1975 Noordhoff International Publishing Leyden 549 Printed in The Netherlands A theory of crack initiation and growth in viscoelastic media !II. Analysis of continuous growth* R. A. SCHAPERY Civil and Aerospace Engineerin9 Departments, Texas A & M University, College Station, Texas 77843, U.S.A. (Received April 19, 1973; in revised form February 21, 1975) ABSTRACT The theory of crack growth developed in Parts I and II is used to predict crack velocity and failure time for an elastomer under simple uniaxial and biaxial stress states. Included are consideration of the effect of specimen size on failure time for initially small cracks, experimental determination of fracture properties, the effect of strain level on crack propagation, and the validity of the plane strain assumption. The second half of the paper examines the effect upon crack velocity of nonlinear viscoelasticityof failing material at the crack tip in media which is otherwise linearly viscoelastic. The dependence of fracture behavior on environmental changes and aging is also considered. I. Introduction In this paper we examine the validity of the opening-mode crack growth theory developed in Parts I [1] and II [2] by comparing predictions of crack velocity and failure time with experimental data obtained by others. Also, certain practical implications of the theory are explored. In Section 2, experimental and theoretical results for the time required for complete failure of centrally cracked elastomeric sheets (Solithane) are compared and found to be in good agreement over a range of constant applied loads and temperatures. Similar agreement is shown in Section 3 for the crack velocity in long, narrow strips of the same elastomer under constant applied deformation; the same mechanical and fracture properties are used in the analysis of both geometries. At relatively large overall strains some discre- pancy between theory and experiment is noted, and a strain-modified stress intensity factor is found to remove this error. In both of these problems, stress intensity factors for plane stress are used in a crack growth equation which is based on the assumption of plane strain at points close to the crack tip; justification for this procedure is given in Section 4. For the particular elastomer investigated, fracture energy and a measure of the strength of the failing material at the crack tip are taken to be constant. However, the underlying theory developed in Parts I and II is not restricted to constant properties. In Section 5 we examine the influence of nonlinear viscoelasticity of the failing material on crack growth behavior in viscoelastic media. Effects of environmental changes and aging are briefly described in Section 6. For the prediction of crack velocity and failure time of the elastomer, we shall use a result obtained in [2, Eqn. (56)]: da/dl=(TC/2) F C2 ][/m ~I/m{]~2(l+i/m,,/~2 12 1_8F(1-K?/K?,)_] "~m ,--t ,, ~,.-, (1) This expression for crack velocity da/dt is based on the use of a creep compliance Cv(t) which is written in the form of a generalized power law : Cv(t) = Co --}- C2 t m (2) where Co=C~(0); C2 and m are positive but not necessarily constant. For a constant * Parts I and II are published, respectively, in Vol. 11, No. 1 (1975) 141-159, and Vol. 11, No. 3 (1975) 369-388. Int. Journ. of Fracture, 11 (1975) 549-562 550 R.A. Schapery Poisson's ratio v, this compliance is simply related to the creep compliance D (t) under uni- axial stress [1, Eqn. (38)], c (t) = 4(1 -,,2)o (t) (3) where D (t) is the axial strain for a unit uniaxial stress applied at t = 0. Additionally, F = frac- ture energy, am= maximum stress within the failing material near the tip, I x =integral measure of the shape of the stress distribution in the failing material (0 < 11 =< 2, with I1 = 2 when this stress is uniformily distributed) and 2~/"=parameter depending only on m (:1/,,~ 1 for O<m< 1). The opening-mode stress intensity factor is denoted by K~, as defined by the relation K, = lim~,~o (2n¢1) ~ a ° (4) where ayo= ao (~1) is the normal stress acting across the plane of crack prolongation and ~1 is the distance ahead of the crack tip; by definition, a ° is the singular stress corresponding to a mathematically sharp crack tip without a finite zone of failing material. Also, K,g =_ (st~Co) ~ (5) is identical to the critical stress intensity factor for an elastic body having a constant compli- ance Co. The compliance parameters, Co, C2 and m, and the fracture properties, F and am I1, will be assumed constant in Sections 2 and 3. 2. Crack growth and failure of a sheet under constant load Consider a centrally cracked plate, such as shown in Fig. 1. Assuming the instantaneous crack length, 2a, is large compared to sheet thickness but small compared to the in-plane dimensions, the stress intensity factor is approximately [e.g., 3], K, = (an) ~ a (6) where a is the applied stress. Substituting Eqn. (6) into Eqn. (1), assuming a is applied at t = 0 and is constant thereafter, and integrating yields t = (2/n 2) (a~ I21/a 2) (Co/2,, C2) 1/rn Ial/a°[(Oy/O0) ') -- 1]l/m(d~}/) ') (7a) where 2a o is the initial crack length, and a o is defined as a o =-- 8F/nCo a 2 . (7b) When the central crack reaches length 2ag (assuming 2a o < 2ao) complete failure of the sheet occurs; this point follows from Eqns. (1), (5), (6) and (7b) which imply fi--*~ as a--*ag. The time at which a = a 9 is called the failure time, t/, which, after changing the integration variable in Eqn. (7a), becomes t r = (2/n2)(a2 12/a2) (C0/2," C2)1/,, J'~o/o,(1 - u) 1/m U -(1 + 1/m, du. (8) The integral can be expressed in terms of incomplete Beta functions. It is of interest to notice that when ao/a o >> 1 and 0_< m < 1 the integrand in Eqn. (7a) goes quickly to zero as 7 increases. In fact, the current time is already 90 ~o of t f when Int. Journ. of Fracture, 11 (1975) 549 562 Theory of crack initiation and gru~th m ui.s~,ul, t,tiu media. III 551 a/a o -~ I(Y". (9) One can easily show that if the assumption ao/a o >> 1 is removed, the crack growth at t = 0.90 t/will be even less than given in Eqn. (9). These observations are important because they tell us if the stress intensity factor, Eqn. (6), is valid over most of the time period 0_< t _< t/ or if the effect of finite sheet width must be included when predicting failure time. For three typical values of m, Eqn. (9) yields 10 , m= 1 a/a° ~- i 3.3, m=0.5 (10) ( 1.6, m=0.2. Surprisingly, most of the time required for failure is consumed while the crack is still relatively small, especially for 0< m< 0.5. As a point of comparison, if the bracketed term in the integrand in Eqn. (7a) is replaced by (ag/ao7) TM for all 0_< t< t/, the failure time is derived by setting a/ao= oo to find tf= [(2ma2~I~)/Tz(2+ 1/"'](8r/2mCzao)t/ma 2,1 + l/m) (11) which brings out very simply the effect of stress on failure time. This is the same result as would be obtained by neglecting (KZ/KZg) in Eqn. (1) at the outset of the analysis. ///////// ~ 0.25" oJ 13 0 ° C "~l t° • 5 ° C ~eO I - 0 I0 ° C ~Z~e ./--The°ry' -- O • 15 ° C ~/ (..9 O A 25 ° C ._1 • :30 ° C 0 40" C '%. I I I \l O( 2 4 6 8 LOGio tf/aT, SEC. Figure 1. Experimental and theoretical failure time t~. as a function of the applied gross stress a for Solithane 50/50. Theory: Eqn. (13). Experimental data after Knauss [3]. Equations (8) and (11) will be compared to experimental data on Solithane 50/50, which is a crosslinked, amorphous, polyurethane rubber. The experimental data for failure time, which are shown in Fig. 1, have been normalized with respect to the stress cry, where ao~ =- (8FE~c/3~zao) ~ (12) Int. Journ. of Fracture, 11 (1975) 549 562 552 R. A. Schapery is the critical stress for the onset of crack growth in an elastic plate having Poisson's ratio ~' = ½ and Young's modulus Eoo = 4 (1 - v2)/Cv (~) = 3/C~ (~); thus, no crack growth occurs for log (a/aoo)2< O. Also, all data have been reduced to a common temperature of 0°C by recognizing that the material is essentially thermorheologically simple [3]; according to Section 6, the major effect of temperature can be introduced by replacing t/with t//aT in Eqn. (8). Since log (t/aT)---- log t-- log aT, the theory, if valid, implies experimental failure data obtained at different temperatures can be superposed by means of horizontal translations of magnitude log aT SO as to form a single curve; the failure data at the temperatures indicated in Fig. 1 were shifted to the data at 0°C. (One can interpret the reduced failure data as being the results of tests conducted entirely at 0~ C.) We should add that the uniaxial creep compliance for this material, which is shown in Fig. 2, was formed in the same way; in fact, the values of log a T used to shift the failure data are those obtained by shifting the creep compliance.
Details
-
File Typepdf
-
Upload Time-
-
Content LanguagesEnglish
-
Upload UserAnonymous/Not logged-in
-
File Pages14 Page
-
File Size-