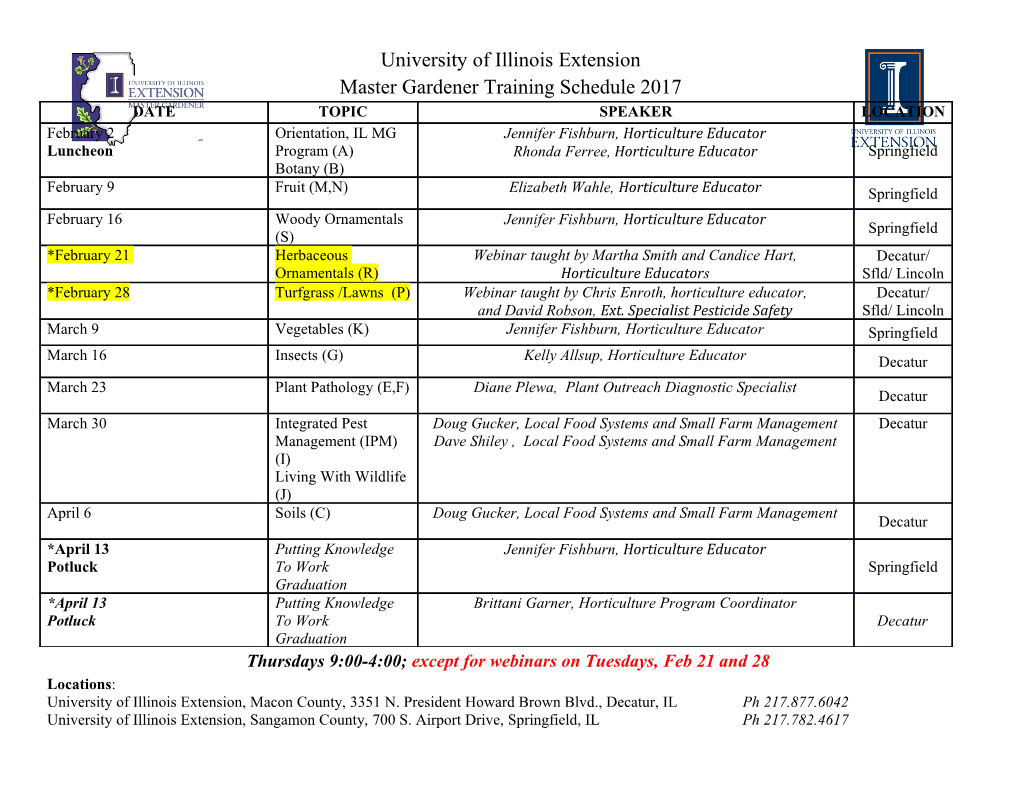
Properties of Copolymers of Aspartic Acid and Aliphatic Dicarboxylic Acids Prepared by Reactive Extrusion Randal L. Shogren,1 J. L. Willett,1 David Westmoreland,2 Sergio O. Gonzalez,1* Kenneth M. Doll,1 Graham Swift2 1Plant Polymer Unit, National Center for Agricultural Utilization Research, USDA/ARS, Peoria, Illinois 2Folia, Inc., Birmingham, Alabama Received 30 April 2008; accepted 24 June 2008 DOI 10.1002/app.28944 Published online 10 September 2008 in Wiley InterScience (www.interscience.wiley.com). ABSTRACT: Aspartic acid is prepared chemically or only about 5 min. Mw generally increased with aspartic/ by the fermentation of carbohydrates. Currently, low mo- diacid ratio but melt viscosities became very high and lecular weight polyaspartic acids are prepared commer- processing became difficult at ratios >16. Most of the cially by heating aspartic acid at high temperatures copolymers exhibited inhibition of calcium carbonate (>220C) for several hours in the solid state. In an effort precipitation at concentrations similar to that of pure to develop a more rapid, continuous, melt polymeriza- polyaspartic acid and thus may find application as anti- tion scheme, aspartic acid was copolymerized with scalants. VC 2008 Wiley Periodicals, Inc. J Appl Polym Sci 110: adipic, azelaic, sebacic, and dodecanedioic acids using a 3348–3354, 2008 vented twin-screw extruder. Copolymers having ratios of aspartic/diacid 16 and Mw up to 9100 were prepared Key words: biodegradable; copolymerization; extrusion; at temperatures of 240–260C and residence times of polyamides INTRODUCTION to the high temperatures and long times required for such a solid state polyamidation. Recently, the use of biobased products to replace To accelerate the reaction, a number of different those made from increasingly costly imported petro- solvents such as toluene, mesitylene, DMF, sulfolane, leum has gained momentum.1–4 For example, there tetralin12 and catalysts such as phosphoric acid, sul- is considerable interest in replacing polyacrylic acid, furic acid, and salts thereof13 have been studied. The a petroleum-based, water soluble polymer, with a drawback of these methods is that the solvent and biobased alternative.5–9 Since polyacrylic acid is catalyst must usually be removed after reaction and used as an antiscalant in water treatment and is not this adds the cost of the product. An alternative biodegradable, there is concern about possible accu- method could involve adding a comonomer having mulation in the environment and toxicity.6 a low melting temperature which would then trans- Poly(aspartic acid) is being manufactured com- form the aspartic comonomer mixture into a melt. mercially and has begun to capture some of the mar- Reaction rates would be expected to be higher in the ket for water treatment polymers.10 The current melt than solid state due to higher molecular mobil- process involves heating aspartic acid at high tem- ity. There have been a number of previous studies peratures (220–270C) for several hours to form of copolymerization of aspartic acid with other polysuccinimide (PSI) followed by hydrolysis with monomers such as 6-aminocaproic acid,14 4-amino- NaOH solution to form Na polyaspartate.5,11,12 How- benzoic acid,15 glutamic acid,16 lactide,17,18 and poly- ever, this process is rather slow and expensive due ethylene glycol19 but these usually were conducted in the presence of solvent and catalyst. For this study, aliphatic diacids were chosen as comonomers The USDA neither guarantees nor warrants the standard because these have not been previously studied and of the product used in this study, and the use of the name diacids such as adipic and sebacic are readily avail- by the USDA implies no approval of the product to the able, inexpensive and biodegradable. Furthermore, exclusion of others that may also be suitable. *Present address: BASF Corporation, Freeport, Texas. molecular weights should be easily controlled by the Correspondence to: R. L. Shogren ([email protected]. ratio of diacid to aspartic acid. gov). The goal of this study was to prepare low molecu- Contract grant sponsor: USDA/ARS, Folia, Inc. lar weight (1,000–5,000) copolymers of aspartic and [Cooperative Research and Development Agreement aliphatic diacids via melt polymerization. This is the (CRADA)], 58-3K95-3-0971. optimal molecular weight range for inhibiting pre- 20 Journal of Applied Polymer Science, Vol. 110, 3348–3354 (2008) cipitation of mineral salts by Na polyacrylate. VC 2008 Wiley Periodicals, Inc. Reactive extrusion was chosen as the processing COPOLYMERS OF ASPARTIC AND ALIPHATIC DICARBOXYLIC ACIDS 3349 TABLE I Source and Properties of Chemicals Used for Extrusion Molecular Melting Name Structure weight temperature (C) Source A A A L-Aspartic acid HOOC CH2 CH(NH2) COOH 133.1 >300 Orsan, Amylum Group, Aalst, Belgium; SCOA, China A A Adipic acid HOOC (CH2)4 COOH 146.1 152 Aldrich, 99% A A Azelaic acid HOOC (CH2)7 COOH 188.2 110 Aldrich, 80% A A Sebacic acid HOOC (CH2)8 COOH 202.3 135 Aldrich, 99% A A Dodecanedioic acid HOOC (CH2)10 COOH 230.3 128 Aldrich, 99% method since twin-screw extruders can easily be rpm). The experimental design is shown in Table II. configured to handle high viscosity melts, water of Samples were collected from the end of the extruder condensation can be vented off and the process is without a die, allowed to cool and then pulverized. continuous. Experimental variables studied in- Residence times were 5 min as determined cluded extrusion temperature, ratio of aspartic to previously.8 diacid and size of diacid (C6-C12). Samples were analyzed for molecular weight by GPC-MALLS and antiscalant activity by inhibition of calcium carbon- ate precipitation. Hydrolysis Hydrolysis of the succinimide rings to the sodium EXPERIMENTAL salt form was conducted following the method of Mosig et al.21 Samples (1 g) were mixed with dis- Materials tilled water (30 g) and titrated with 1M NaOH using Materials used for extrusion as well as source, struc- an autotitrator (Titronic Universal, Schott Instru- ture, and melting temperatures are shown in Table I. ments) in the pH stat mode at a pH of 9.5, tempera- Polyacrylic acid, sodium salt (Mw ¼ 5100), and poly ture of 60 C for 1 h. (a,b)-DL-aspartic acid, sodium salt (Mw ¼ 2100), D20 (99.96%D), and DMSO-d6 (99.9%D) were from TABLE II Sigma-Aldrich. Other chemicals were reagent grade. Experimental Design Aspartic/diacid Extrusion Sample no. Diacid (mol/mol) Temp ( C) A ZSK-30 twin-screw extruder (Coperion, Ramsey, 1 Adipic 4 260 2 6 260 NJ) was used with 30-mm diameter screws, L/D 3 8 260 ¼ 44 and 14 barrel sections. Barrel sections and 4 8 275 screw elements were stainless steel to avoid corro- 5 8 260 sion and contamination of the products. The screw 6 8 240 configuration consisted of four mixing sections 7 8 220 8 8 260 located between barrel sections 4–5, 7–8, 10–11, and 9 10 260 13–14. The first mixing section had three kneading 10 Azelaic 10 260 elements with 45 forward stagger angle and 11 12 260 decreasing width. The three additional mixing sec- 12 12 260 tions each had two forwarding kneading elements 13 12 260 14 14 260 (45 stagger), a neutral element (90 stagger) and a 15 Sebacic 10 260 reverse element (45 stagger). The mixing sections 16 12 260 were separated by vented barrel sections. 17 14 260 Aspartic acid and diacids were sieved then mixed 18 14 260 and placed in a loss-in-weight feeder (Accurate, 19 14 260 20 16 260 Whitewater, WI) over barrel section 1. Barrel sec- 22 Dodecanedioic 10 260 tions 6, 9, and 12 were open (plugs removed) to 23 12 260 allow evaporation of steam and suction trunks were 24 14 260 placed over these. Feed rates were 0.11 lb/min and 25 16 260 screw speeds were 100 rpm (except for aspartic/ 26 16 260 27 16 260 diacid ¼ 16 where speed was increased to 150–180 Journal of Applied Polymer Science DOI 10.1002/app 3350 SHOGREN ET AL. FTIR KBr pellets were made by grinding 1 mg sample with 200 mg anhydrous KBr in an agate mortar fol- lowed by compression in a Carver die and press at 10,000 psi for 2 min. FTIR spectra were obtained with a Thermo-Nicolet Avatar 370 FTIR. NMR Extruded samples (15 mg, PSI form) were dissolved in 0.7 mL DMSO-d6 while hydrolyzed (sodium salt 1 form) samples were dissolved in D2O. H-NMR spectra were obtained at 25C (60C for PSI form in DMSO) on a Bruker Ultrashield 500 at 500 MHz. Figure 1 FTIR spectra of an aspartic/adipic acid copoly- Conversion mer extruded at 260C, aspartic acid and adipic acid. The amount of residual unreacted aspartic and diac- ids was estimated from the relative areas of the GPC ment of absorbance at 400 nm. Plots of absorbance refractometer peaks for the monomers and copoly- versus inhibitor concentration were used to deter- mer at 12.1–12.6 and 10–11 min, respectively. Weight mine at what concentration absorbance fell to 0.01 percent of unreacted monomer was calculated as 100 and this was designated the minimum inhibitory A (monomer)/(A(polymer) þ A(monomer)). concentration (MIC). GPC-Malls RESULTS GPC-MALLS was carried out using a Waters 1525 The chemical structure of a copolymer made with HPLC system, a Waters 717 plus autosampler, a aspartic acid/adipic acid 8/1 at 260C was evaluated Waters 2414 refractive index detector and a Wyatt using FTIR and 1H-NMR. The FTIR spectrum of this Technologies Dawn EOS light scattering detector. sample (Fig. 1) as well as the rest of extruded sam- GPC analyzes were performed using a Polymer Labs ples (data not shown) had a large absorbance at aquagel-OH 30 column (300 Â 7.5 mm), an injection 1720 cmÀ1 corresponding to carbonyl stretching in volume of 10 lL of 1% solutions and a temperature the succinimide residues.9 Ratios of 1H peaks at 4.6 of 30C.
Details
-
File Typepdf
-
Upload Time-
-
Content LanguagesEnglish
-
Upload UserAnonymous/Not logged-in
-
File Pages7 Page
-
File Size-