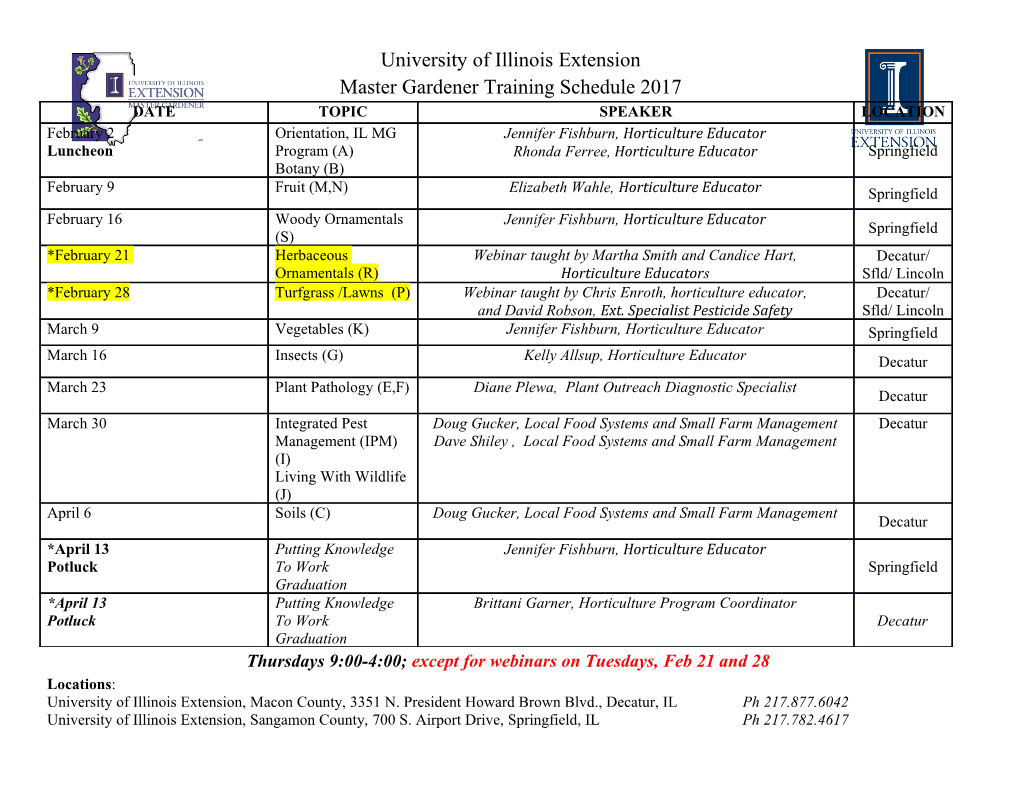
30 CHAPTER 3. CONVENTIONAL RHEOMETRY: STATE-OF-THE-ART This chapter reviews literature on conventional rheometries. Section 3.1 briefly introduces conventional rheometers. In sections 3.2 and 3.3, viscometers commonly used for the viscosity measurements of fluids, which have been used for hemorheology studies, are demonstrated. Section 3.4 provides conventional methods of measuring yield stresses of fluids. Section 3.5 presents the drawbacks of conventional viscometers for clinical applications. 3.1. Introduction Numerous types of rheometers have been used to measure the viscosity and yield stress of materials [Tanner, 1985; Ferguson and Kemblowski, 1991; Macosko, 1994]. In the present study, rheometer refers to a device that can measure both viscosity and yield stress of a material, whereas viscometer can measure only the viscosity of the material. In addition, only shear viscometers will be discussed in the study since the other type, extensional viscometers, are not very applicable to relatively low viscous fluids, such as water and whole blood. Typically, shear viscometers can be divided into two groups [Macosko, 1994]: drag flows, in which shear is generated between a moving and a stationary solid surface, and pressure-driven flows, in which shear is generated by a pressure difference over a capillary tube. The commonly utilized members of these groups are 31 shown in Fig. 3-1. Numerous techniques have been developed for determining the yield stress of fluids both directly and indirectly. Most of these viscometers can produce viscosity measurements at a specified, constant shear rate. Therefore, in order to measure the viscosity over a range of shear rates, one needs to repeat the measurement by varying either the pressure in the reservoir tank of capillary tube viscometers, the rotating speed of the cone or cup in rotating viscometers, or the density of the falling objects. Such operations make viscosity measurements difficult and labor intensive. In addition, these viscometers require anticoagulants in blood to prevent blood clotting. Hence, the viscosity results include the effects of anticoagulants, which may increase or decrease blood viscosity depending on the type of anticoagulant [Rosenblum, 1968; Crouch et al., 1986; Reinhart et al., 1990; Kamaneva et al., 1994]. Drag-flow type of viscometers includes a falling object (ball or cylinder) viscometer and a rotational viscometer. However, the falling object viscometer is not very convenient to use for clinical applications. In the case of the falling object viscometer, the relatively large amount of a test fluid is required for the viscosity measurement. In addition, since the testing fluid is at a stationary state initially, the type of viscometer is not very applicable to a thixotropic fluid like whole blood. The principle of the falling object viscometer is provided in Appendix B. For the yield measurement of blood, most researchers have used indirect methods rather than direct methods for practical reasons [Nguyen and Boger, 1983; de Kee et al., 1986; Magnin and Piau, 1990]. Thus, the details of direct methods will 32 not be discussed in this chapter. As indirect methods, data extrapolation and extrapolation using constitutive models are introduced and discussed in this chapter. 33 Rheometers Viscosity Yield Stress Measurements Measurements Drag Pressure- Indirect Direct Flows Driven Flows Methods Methods Capillary- Data Extrapolation Tube Extrapolation using Viscometer Constitutive Models Falling/ Rotational Rolling Viscometer Object Viscometer Fig. 3-1. Rheometers. 34 3.2. Rotational Viscometer In a rotational viscometer, the fluid sample is sheared as a result of the rotation of a cylinder or cone. The shearing occurs in a narrow gap between two surfaces, usually one rotating and the other stationary. Two frequently used geometries are Couette (Fig. 3-2) and cone-and-plate (Fig. 3-3). 3.2.1. Rotational Coaxial-Cylinder (Couette Type) In a coaxial-cylinder system, the inner cylinder is often referred to as bob, and the external one as cup. The shear rate is determined by geometrical dimensions and the speed of rotation. The shear stress is calculated from the torque and the geometrical dimensions. By changing the speed of the rotating element, one is able to collect different torques, which are used for the determination of the shear stress- shear rate curve. Figure 3-2 shows a typical coaxial-cylinder system that has a fluid R confined within a narrow gap ( i ≥ 0.99 ) between the inner cylinder rotating at Ω Ro and the stationary outer cylinder. Once the torque exerting on either inner or outer cylinder is measured, the shear stress and shear rate can be calculated as follow [Macosko, 1994]: M i M o τ (Ri ) = 2 or τ (Ro ) = 2 (3-1) 2πRi H 2πRo H 35 ΩR Ri γ&(Ri ) ≅ γ&(Ro ) = when 1 > ≥ 0.99 (3-2) Ro − Ri Ro where Ri and Ro = radii of inner and outer cylinders, respectively R + R R = i o 2 M i and M o = torques exerting on inner and outer cylinders, respectively H = height of inner cylinder Ω = angular velocity. 3.2.2. Cone-and-Plate The common feature of a cone-and-plate viscometer is that the fluid is sheared between a flat plate and a cone with a low angle; see Fig. 3-3. The cone-and-plate system produces a flow in which the shear rate is very nearly uniform. Let’s consider a fluid, which is contained in the gap between a plate and a cone with an angle of β . Typically, the gap angle, β , is very small ( ≤ 4o ). The shear rate of the fluid depends on the gap angle, β , and the linear speed of the plate. Assuming that the cone is stationary and the plate rotates with a constant angular velocity of Ω , the shear stress and shear rate can be calculated from experimentally measured torque, M , and given geometric dimensions (see Fig. 3-3) as follows [Macosko, 1994]: 3M Ω τ = and γ& = . (3-3) 2πR 3 β 36 Ω Ri H Ro Fig. 3-2. Schematic diagram of a concentric cylinder viscometer. 37 Torque measurement device Fluid R Cone β Plate Ω Fig. 3-3. Schematic diagram of a cone-and-plate viscometer. 38 3.3. Capillary-Tube Viscometer The principle of a capillary tube viscometer is based on the Hagen-Poiseuille Equation which is valid for Newtonian fluids. Basically, one needs to measure both pressure drop and flow rate independently in order to measure the viscosity with the capillary tube viscometer. Since the viscosity of a Newtonian fluid does not vary with flow or shear, one needs to have one measurement at any flow velocity. However, for non-Newtonian fluids, it is more complicated because the viscosity varies with flow velocity (or shear rate). In a capillary-tube viscometer, the fluid is forced through a cylindrical capillary tube with a smooth inner surface. The flow parameters have to be chosen in such a way that the flow may be regarded as steady-state, isothermal, and laminar. Knowing the dimensions of the capillary tube (i.e., its inner diameter and length), one can determine the functional dependence between the volumetric flow rate and the pressure drop due to friction. If the measurements are carried out so that it is possible to establish this dependence for various values of pressure drop or flow rate, then one is able to determine the flow curve of the fluid. For non-Newtonian fluids, since the viscosity varies with shear rate, one needs to vary the pressure in the reservoir in order to change the shear rate, a procedure that is highly time-consuming. After each run, the reservoir pressure should be reset to a new value to obtain the relation between flow rate and pressure drop. In order to determine the flow curve of a non-Newtonian fluid, one needs to establish the functional dependence of shear stress on shear rate in a wide range of these variables. 39 Figure 3-4 shows the schematic diagram of a typical capillary-tube viscometer, which has the capillary tube with an inner radius of Rc and a length of Lc . It is assumed that the ratio of the capillary length to its inner radius is so large that one may neglect the so-called end effects occurring in the entrance and exit regions of the capillary tube. Then, the shear stress at the tube wall can be obtained as follows: r∆P τ = c (3-4) 2Lc Rc ∆Pc τ w = (3-5) 2Lc where τ and τ w = shear stresses at distance r and at tube wall, respectively r = distance from the capillary axis ∆Pc = pressure drop across a capillary tube. It is of note that the shear stress distribution is valid for fluids of any rheological properties. In the case of a Newtonian fluid, the shear rate at tube wall can be expressed by taking advantage of the well-known Hagen-Poiseuille Equation as: 4Q 4V γ&w = 3 = (3-6) πRc Rc where γ&w = wall shear rate 4 π Rc ∆Pc 2 Q = = πRc ⋅V = volumetric flow rate (Hagen-Poiseuille Equation) 8µ Lc V = mean velocity. 40 Compressed air Air Test fluid Reservoir tank Capillary tube Lc 2Rc Collected test fluid Balance Fig. 3-4. Schematic diagram of a capillary-tube viscometer. 41 3.4. Yield Stress Measurement Whether yield stress is a true material property or not is still a controversial issue [Barnes and Walters, 1985]. However, there is generally an acceptance of its practical usefulness in engineering design and operation of processes where handling and transport of industrial suspensions are involved. The minimum pump pressure required to start a slurry pipeline, the leveling and holding ability of paint, and the entrapment of air in thick pastes are typical problems where the knowledge of the yield stress is essential.
Details
-
File Typepdf
-
Upload Time-
-
Content LanguagesEnglish
-
Upload UserAnonymous/Not logged-in
-
File Pages19 Page
-
File Size-