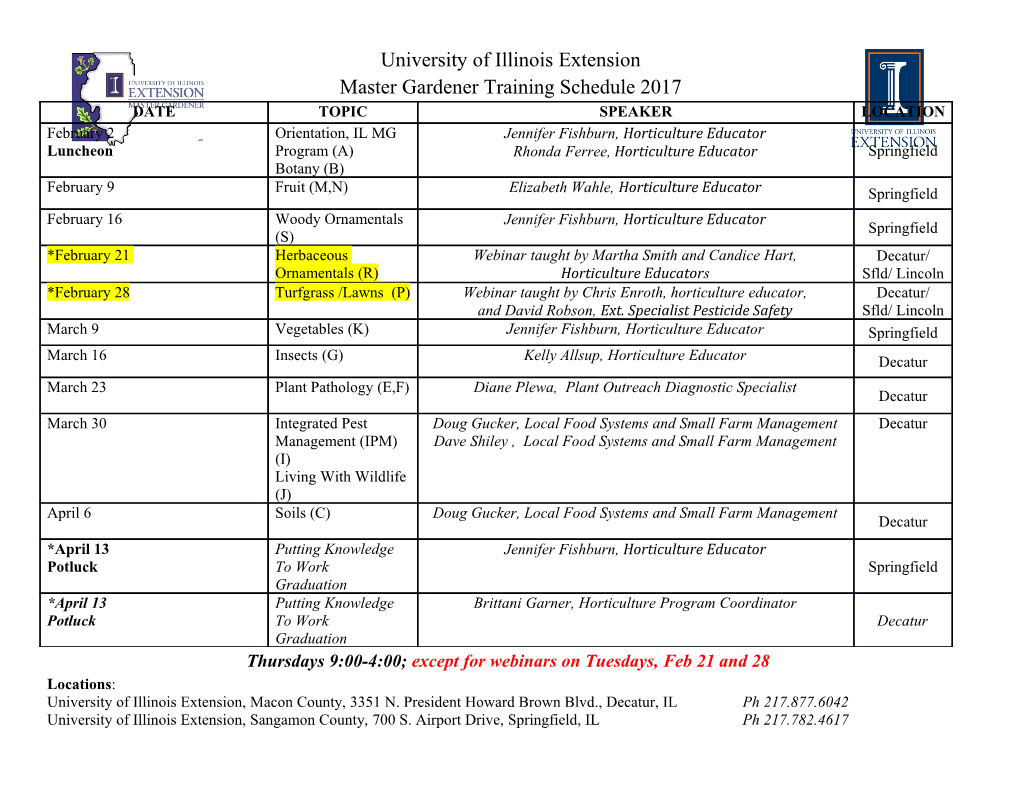
CORROSION BEHAVIOUR OF ALUMINISED STEEL AND CONVENTIONAL ALLOYS IN SIMULATED ALUMINIUM SMELTING CELL ENVIRONMENTS by Nan Xu A Thesis Submitted for the Degree of Doctor of Philosophy School of Materials Science and Engineering The University of New South Wales Australia April 2002 CERTIFICATE OF ORIGINALITY I hereby declare that this submission is my own work and that, to the best of my knowledge it contains no materials previously published or written by another person, nor material which to a substantial extent has been accepted for the award of any other degree or diploma at UNSW or any other educational institution, except where due acknowledgement is made in the thesis. Any contribution made to the research by others, with whom I have worked at UNSW or elsewhere, is explicitly acknowledged in the thesis. I also declare that the intellectual content of this thesis is the product of my own work, except to the extent that assistance from other in the project’s design and conception or style, presentation and linguistic expression is acknowledged. Nan Xu DEDICATION I dedicate this work to my mother RenZhuang Bai. i ACKNOWLEDGEMENTS I wish to express my thanks to the following people for their assistance with this research project: To Professor David J. Young for his valuable technical advice, idea and guidance provided throughout the whole project. I would also like to thanks Professor Young for giving me the opportunity to participate in this project and also for organising the funding for this project. To all technical staff at the School of Materials Science and Engineering for their assistance. To Comalco Pty. Ltd. for their technical support related to this project and supplying required materials. To all other fellow members of the High-Temperature Materials Group for their assistance and helpful general discussion. To my parents and my beloved wife for their encouragement and understanding, and support throughout my studies. ii ABSTRACT Aluminium smelting is a high temperature electrometallurgical process, which suffers considerable inefficiencies in power utilization and equipment maintenance. Aluminium smelting cell works in the extreme environments that contain extraordinarily aggressive gases, such as HF, CO and SO2. Mild steel used as a structural material in the aluminium industry, can be catastrophically corroded or oxidized in these conditions. This project was mainly concerned with extending the lifetime of metal structures installed immediately above the aluminium smelting cells. An aluminium-rich coating was developed on low carbon steel A06 using pack cementation technique. Yttria (Y2O3) was also used to improve the corrosion resistance of coating. Kinetics of the coating formation were studied. XRD, FESEM and FIB were employed to investigate the phase constitution and the surface morphology. Together with other potentially competitive materials, aluminium-rich coating was evaluated in simulated plant environments. Results from the long time (up to 2500h) isothermal oxidation of materials at high temperature (800°C) in air showed that the oxidation resistance of coated A06 is close to that of stainless steel 304 and even better than SS304 in cyclic oxidation tests. Coated A06 was also found to have the best sulfidation resistance among the materials tested in the gas mixture contains SO2 at 800°C. Related kinetics and mechanisms were also studied. The superior corrosion resistance of the coated A06 is attributed to the slow growing a-Al2O3 formed. Low temperature corrosion tests were undertaken in the gas mixtures containing air, H2O, HCl and SO2 at 400°C. Together with SS304 and 253MA, coated A06 showed excellent corrosion resistance in all the conditions. The ranking of the top three materials for corrosion resistance is: 253MA, coated A06 and SS304. It is believed that iii aluminised A06 is an ideal and economical replacement material in the severe corrosive aluminium smelting cell environment. iv TABLE OF CONTENTS Dedication i Acknowledgements ii Abstract iii Table of Contents v List of Figures ix List of Tables xvi CHAPTER 1: INTRODUTION 1 1.1 INTRODUCTION 1 1.2 FAILURE ANALYSIS 3 1.3 CONCLUSION FROM FAILURE ANANLYSIS 11 CHAPTER 2: LITERATURE REVIEW 12 2.1 OXIDATION OF METALS AND ALLOYS 12 2.1.1 Introduction 12 2.1.2 Oxidation of Metals 12 2.1.2.1 Thermodynamic aspects 12 2.1.2.2 Mechanism and kinetics of scale formation 13 2.1.2.2.1 Parabolic law 13 2.1.2.2.2 Linear rate law 19 2.1.3 Oxidation of alloys 19 2.1.3.1 External scale formation 20 2.1.3.2 Influence of alloying elements 21 2.1.3.3 Internal oxidation 23 2.1.4 Oxidation in mixed gas 24 2.2 SULFIDATON OF METALS AND ALLOYS 27 2.2.1 Introduction 27 2.2.2 Properties of metal sulfides 27 v 2.2.3 Sulfidation of metals 28 2.2.3.1 Sulfidation of Iron 28 2.2.4 Effects of the sulfur pressure, temperature and gas 31 2.2.5 Sulfidation of binary alloys 34 2.2.5.1 Sulfidation of Iron-Chromium 34 2.2.6 Sulfidation of commercial alloys 38 2.2.6.1 Sulfidation of carbon steel 38 2.2.6.2 Sulfidation of low alloy steels 39 2.2.6.3 Sulfidation of ferritic stainless steels 39 2.2.6.4 Sulfidation of Austenitic stainless steels 40 2.3 HIGH TEMPERATURE CORROSION OF METALS AND ALLOYS IN ATMOSPHERES CONTAINING HCL/CL2 43 2.3.1 Introduction 43 2.3.2 Thermodynamic aspects 43 2.3.3 High temperature corrosion of iron in atmospheres containing HCl/Cl2 44 2.3.4 High temperature corrosion of chromium in atmospheres containing HCl/Cl2 45 2.3.5 The chlorination of alloys containing chroumium 46 2.3.6 Chlorination of alloys containing aluminium 49 2.3.7 Active oxidation mechanism 52 2.4 PACK CEMENTATION ALUMINIZIED COATING 54 2.4.1 Introduction 54 2.4.2 The pack cementation process 54 2.4.3 Procedure 55 2.4.4 Mechanism of coating formation 56 2.4.5 Process variables in pack cementation 60 2.4.6 Pack aluminizing on Ni-based and Fe-based alloys 60 2.4.6.1 Pack aluminizing on Ni-based alloys 60 2.4.6.2 Pack aluminizing of iron and commercial steels 69 2.4.6.3 High temperature corrosion resistance of iron aluminide 72 2.4.6.3.1 High Temperature Oxidation of Iron Aluminides 72 2.4.6.3.2 High Temperature Sulfidation and Oxidation/Sulfidation of iron aluminides 76 vi 2.4.6.3.3 High temperature chlorination of iron aluminide alloys 86 CHAPTER 3: EXPERIMENTAL PROCEDURES 93 3.1 SPECIMEN PREPARATION 93 3.2 PACK ALUMINIZING PROCESS 95 3.2.1 Pack Materials 95 3.2.2 Pack Preparation and Coating Deposition 96 3.2.2 Coating Analyses 97 3.3 HIGH TEMPERATURE OXIDATION 98 3.3.1 High Temperature Isothermal Oxidation 98 3.3.2 High Temperature Cyclic Oxidation 101 3.4 CORROSION TESTS IN MIXED GASES 101 3.4.1 Corrosion Tests in Gas Mixtures at Low Temperature 101 3.4.2 Corrosion Tests in Gas Mixture at High Temperature 102 CHAPTER 4: PACK ALUMINIZING COATING FORMED ON A1006 STEEL 104 4.1 INTRODUCTION 104 4.2 THERMODYNAMIC CALCULATION 104 4.3 RESULTS 105 4.3.1 Coatings Formed on Steel Using Different Activators without Yttria Deposition 105 4.3.2 Coating formed using NaF activator on steel pre-coated with yttria slurry 110 4.3.3 Surface morphologies of coating grown using NaF activator 114 4.3.4 Phase constitution of coatings formed for various deposition times 114 4.3.5 Coating growth kinetics 123 4.4 DISCUSSION 124 4.4.1 Effect of activator type on coating formed on A1006 steel 124 4.4.2 Surface morphology and kinetics of coating formation 125 4.4.3 Effect of yttria slurry deposit on coating constitution 127 4.5 CONCLUSIONS 128 CHAPTER 5: HIGH TEMPERATURE OXIDATION 129 5.1 INTRODUCTION 129 vii 5.2 RESULTS 129 5.2.1 Isothermal Oxidation 129 5.2.1.1 TGA Experiment 129 5.2.1.2 Long Time Oxidation Experiments 140 5.2.2 HIGH TEMPERATURE CYCLIC OXIDATION 146 5.3 DISCUSSION 153 5.3.1 Oxidation Kinetics for Materials Tested Using TGA 153 5.3.2 Scale morphology study 154 5.4 CONCLUSION 158 CHAPTER 6: HIGH TEMPERATURE SULFIDATION 159 6.1 INTRODUCTION 159 6.2 THERMODYNAMIC ASPECT 159 6.3 RESULTS 162 6.4 DISCUSSION 191 6.5 CONCLUSION 197 CHAPTER 7: LOW TEMPERATUER TESTS 198 7.1 INTRODUCTION 198 7.2 THERMODYNAMIC ASPECTS 198 7.3 RESULTS 203 7.4 DISCUSSION 228 7.5 CONCLUSION 235 CHAPTER 8: SUMMARY AND CONCLUSIONS 236 CHAPTER 9: REFERENCES 240 APPENDIX 1: LIST OF DATA USED IN COMPUTER CALCULATIONS 258 APPENDIX 2: XRD RESULTS FOR LONG TERM ISOTHERMAL OXIDATION EXPERIMENTS 260 viii LIST OF FIGURES FIGURE PAGE 1.1 (a) Aluminium reduction cell-ferrous component degradation; 2 (b) Schematic diagram showing the high temperature oxidation/corrosion occurring on the anode stub at the site above the carbon anode of a reduction cell [1] and (c) Corroded stub. 1.2 Schematic drawing of hopper and section where samples were 5 taken from. 1.3 Corroded samples sectioned from hopper. 6 1.4 (a) Optical image of the cross-section of sample 1 (etched by 8 5wt% nital); (b) Optical image of the cross-section of sample 2 (etched by 5wt% nital); (c) Optical image of the cross-section of sample 3. 1.5 (a) Thinned plate (sample 2) and scale at its HAZ (etched by 10 5wt% nital); (b) Open surface of thinned plate (sample 2); (c) Thicker plate (sample 2) and its HAZ (etched by 5wt% nital).
Details
-
File Typepdf
-
Upload Time-
-
Content LanguagesEnglish
-
Upload UserAnonymous/Not logged-in
-
File Pages287 Page
-
File Size-