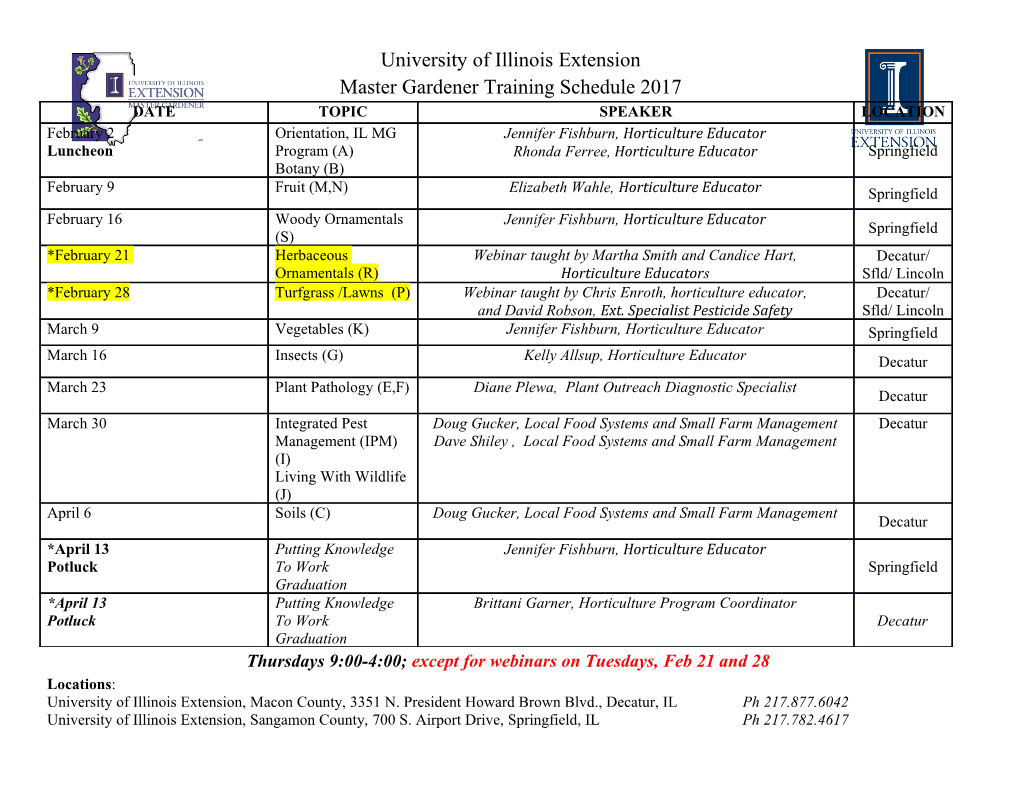
BUILDING THE NEW FIBER LINK NEW TUGBOAT WELCOME TO GRAND RAPIDS CONNECTS CANADA’S & BARGES TORONTO’S PIPELINE FAR NORTH JOIN FLEET NEWEST DISTRICT THEGLOBE FALL 2015 VOLUME THIRTEEN — ISSUE TWO ONE LEDCOR. FULLY INTEGRATED. OUR EXPERTISE IN MANY AREAS ALLOWS US TO SEE EVERY JOB FROM MANY ANGLES. As Ledcor has grown over the decades, we’ve made diversifi cation a key part of how we set ourselves apart. Diverse industries. Diverse off erings. Diverse projects and locations. Diverse expertise. It’s important that new methods for collaboration are created and practiced as diversifi cation grows so that in-house experts can share the benefi ts of their expertise with the company as a whole. Our goal has always been to diversify, to expand and deepen our expertise, yet always remain fully integrated. We call this strategy One Ledcor. It benefi ts our clients on every project, and makes our relationships simpler, clearer, and more direct. In this issue of The Globe, we look at one signifi cant project where One Ledcor is making all of the diff erence. But the fact is that you can see it at work in everything we do— big projects and small projects alike. Sincerely, Dave Lede Chairman & CEO CANARY 10 DISTRICT MACKENZIE VALLEY 2 FEATURE 24 FIBRE LINK FEATURE OIL & GAS 19 Grand Rapids Pipeline DIVERSE. 20 Hangingstone Expansion 21 Polyethylene 1 Expansion UNITED. TRANSPORTATION BUILDING 22 New Tugboat and Barges Join our Marine Fleet 24 Second Avro Jet for Summit Air 8 Chevron Central Reliability Center 8 Industrial Branch Facility PROPERTIES 9 YVR A-B Connector 24 The Cove Waikiki 10 Canary District COMMUNICATIONS 12 Quintet Phase 2 25 Mackenzie Valley Fibre Link 13 10th Avenue 14 Marine Gateway COMMUNITY 15 MNP Tower 26 Hockey Helps Post-Secondary Students 16 Kelly Ramsey Tower 26 Support for the Nevada Blind Children’s Foundation 17 Southern Hills Skilled Nursing Facility 27 Canada’s Ten Most Admired Corporate Cultures 17 Acura Centre of Saskatoon 27 One of BC’s Top Employers AWARDS 28 Silver for Major P3 Project 28 Recognized for Safety at Kearl Oil Sands 9 22 28 DIVERSE. 2 THE GLOBE FALL 2015 UNITED. AT SUNCOR’S MASSIVE FORT HILLS OIL SANDS PROJECT, LEDCOR’S DIVERSITY AND VERTICAL INTEGRATION IS MAKING A COMPLEX JOB SIMPLER AND MORE EFFICIENT FOR OUR CLIENT. PROJECT SERVICES TRANSPORT FORT HILLS is a complex EARTHWORKS project, and we’re on site FOUNDATIONS delivering a lot of diff erent INDUSTRIAL CONSTRUCTION services. Follow the lines to MECHANICAL & ELECTRICAL see how it all comes together. PIPELINES MODULE FABRICATION COMMUNICATIONS In northern Alberta, Ledcor is understated. Fort Hills will process This high degree of integration supporting Suncor Energy in the 110 million metric tons (121 million allows Suncor to focus on what they development of a new mine that’s short tons) of oil sand per year, do best, instead of on managing been called one of the top oil sands yielding around 180,000 barrels of multiple contracts and partners. assets in the world. bitumen per day at peak. Once all is said and done, it The Fort Hills project is Our role in this project is as will mean simplifi ed logistics, situated in the Athabasca region, diverse as it is wide. We’ve been simplifi ed planning, and better 90 kilometers (56 miles) north of on site from the very beginning, project outcomes. Fort McMurray. Jointly owned by working on everything from the Here, we take a closer look at Suncor, Total E&P Canada, and Teck water supply, to the crew camp, to all of the pieces that are coming Resources, the open-pit mine is the multi-stage extraction systems. together at Fort Hills. It’s just one scheduled to produce fi rst oil To do that, we’re drawing on example of how One Ledcor—diverse, in late 2017. resources, equipment, and expertise yet united—is out there every day The scale of this project cannot be from all over Ledcor. moving complex projects forward. THE GLOBE FALL 2015 3 BRINGING IN THE FABRICATING THE 1 CREW AND FLEET 2 COMPONENTS While our crews fl y into Fort Hills, the Just south of Edmonton, in Nisku, Alberta, Ledcor-owned fl eet of heavy construction we get to work on the fabrication and and earthworks equipment also makes assembly of many dozens of modules its way to the jobsite. That fl eet is and panels destined for Fort Hills. These operated and maintained exclusively by modules will end up in everything from our own employees on the ground. the utilities corridor to the primary extraction facility. PROJECT SERVICES 1. PRE-PROJECT 2. FABRICATION & ASSEMBLY TRANSPORT EARTHWORKS FOUNDATIONS INDUSTRIAL CONSTRUCTION MECHANICAL & ELECTRICAL PIPELINES MODULE FABRICATION COMMUNICATIONS 4 THE GLOBE FALL 2015 3. CAMP INFRASTRUCTURE 4. WATER INTAKE BUILDING THE CAMP, SOURCING THE 3 UTILITIES, AND 4 MINE’S WATER COMMUNICATIONS On the edge of the Athabasca River, we get to work building the river water intake We built a 1,500-bed camp for Suncor’s mine facility — first stop in the supply for the crews, designed to be expandable in the future entire mine. The build calls for 5,000 cubic as production is ramped up. It’s a sizable meters (177,000 cubic feet) of structural facility that naturally needs full utilities to concrete, 100,000 cubic meters (3.5 million support its residents. cubic feet) of site grading and excavation, • Water treatment and storage, including and 2,000 meters (6,500 feet) of high- potable water, fire water, and waste density polyethylene (HDPE) and carbon water systems; steel pipeline, and steel driven piles. • Natural gas conditioning, odorization, On the other side of Highway 63, the pressure letdown, and distribution; river water is sent to stop number two: the • Electrical, including natural gas power raw water pond and wet well. This is the generation and power pole installations reservoir for all potable and process water, for a 13,800-volt system; with a working capacity of 60,000 cubic • Communications, with over 10 kilometers meters (16 million US gallons). We’re taking (6 miles) of fiber-optic conduit, cabling, care of everything from foundational piles, and termination. to structural concrete, to HDPE and carbon steel pipelines. The pond itself requires a bentonite perimeter cut-off, 250,000 cubic meters (8.8 million cubic feet) of cut-to-fill material, an HDPE pond liner, and a sump. THE GLOBE FALL 2015 5 PROJECT SERVICES 5. PIPELINES 6. PRIMARY EXTRACTION TRANSPORT EARTHWORKS FOUNDATIONS INDUSTRIAL CONSTRUCTION MECHANICAL & ELECTRICAL PIPELINES MODULE FABRICATION COMMUNICATIONS CONNECTING COMPLETING 5 IT ALL 6 THE PRIMARY EXTRACTION PLANT Between the water intake, the utilities, and the mine’s extraction plants, there are about nine When Fort Hills is up and running, oil-sand slurry kilometers (five and a half miles) will be sent to primary extraction, where two trains of ground to cover. of separation cells start removing the bitumen. We’re building the entire pipeline This yields a froth of bitumen, water, and clay. corridor. It starts with the utility It’s a big job at the heart of the mine. And modules that we fabricate down making it all a reality is a big job for our fabrication in Nisku. Then, up at Fort Hills, crews down in Nisku. They’re responsible for the 47 we do the whole installation from piperack and process modules that make up much excavation, to bedding, to laying, of the plant, as well as the 57 building panels that to backfill. house everything. The work in the field at Fort Hills is even larger. All told, the corridor will house Our crews are tackling the mechanical completion pipelines for natural gas, raw water, of the plant, which will take around 2,000,000 drinking water, wastewater, treated work-hours. That includes piping, tie-ins, and water, and effluent discharge — equipment installation as well as erection of the ranging from 10" HDPE to 30" buildings themselves. carbon steel . 6 THE GLOBE FALL 2015 7. SECONDARY EXTRACTION GOING FORWARD. TOGETHER. Of course, this is just one snapshot of one of our projects with Suncor. As a long-term partner, we’re looking forward to being there, supporting them, as they continue to build and expand — at Fort Hills and beyond. SECONDARY EXTRACTION, 7 FROM THE GROUND UP After primary extraction, bitumen froth is sent pipelines. It’s a large civil project, with a to secondary extraction. That’s where it’s mixed forecast of 500,000 work-hours. with solvent and sent through two stages of Along the way, we’ll drive 2,733 piles. If lined counter-current settlers to remove asphaltenes, up end to end, they would stretch 59 kilometers sand, and excess water. The bitumen then goes (37 miles). to a solvent recovery unit; the final product is We’ll excavate approximately 260,000 cubic marketable bitumen. meters (9.2 million cubic feet) of material, and To build secondary extraction from the complete 305,000 cubic meters (10.8 million ground up, we’re working together with Sunlake, cubic feet) of backfill. the Canadian subsidiary of SK Engineering & We’ll install over five kilometers (three miles) Construction (SK E&C). of carbon steel and HDPE pipe. Our focus here is on extensive civil works And we’ll pour 21,000 cubic meters (742,000 in twelve distinct work areas. We’re doing cubic feet) of structural concrete, 17,500 cubic the excavation and foundations for froth meters (618,000 cubic feet) of lightweight tanks, bullet vessels, pumphouses, e-houses, cellular concrete, and 19,000 square meters piperacks, and underground sumps and (205,000 square feet) of concrete paving.
Details
-
File Typepdf
-
Upload Time-
-
Content LanguagesEnglish
-
Upload UserAnonymous/Not logged-in
-
File Pages32 Page
-
File Size-