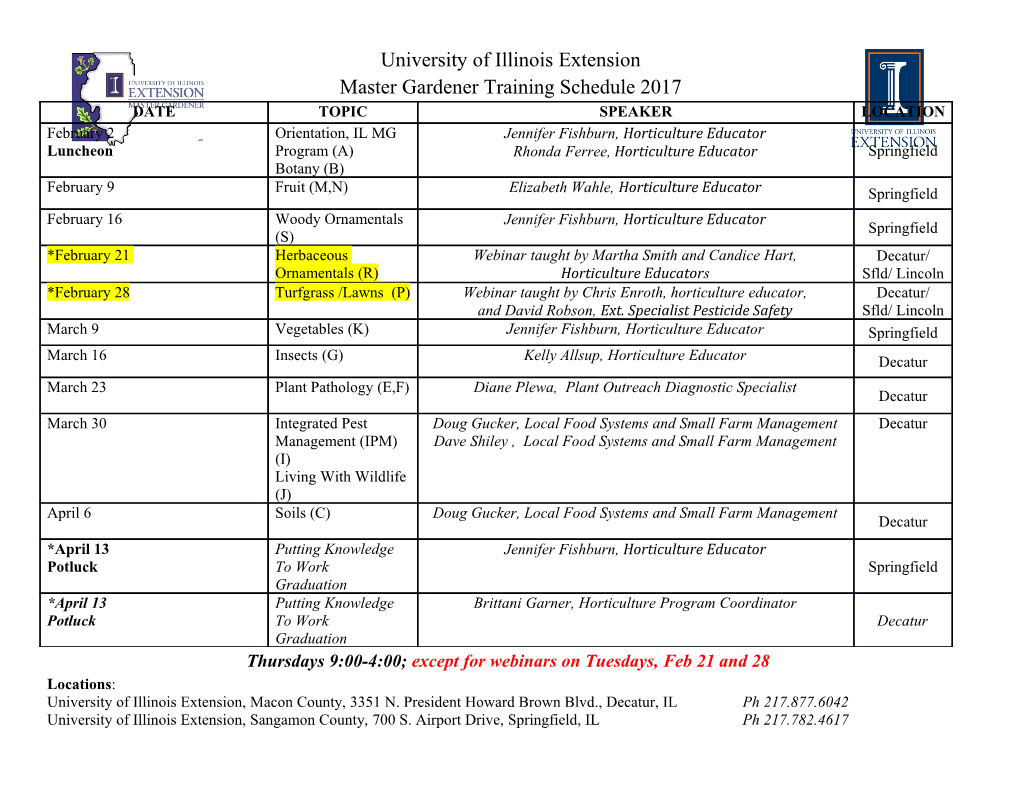
Flotation Column: A Process Unit for Cleaning Up Paper Machine Whitewater Circuits Y. Dionne, Bowater, Gatineau, QC, Canada M. Ricard, FPInnovations, Paprican, Pointe-Claire, QC, Canada G. Dorris, FPInnovations, Paprican, Pointe-Claire, QC, Canada C. Daneault, CIPP/UQTR, Trois-Rivières, QC, Canada ABSTRACT Because column flotation offers many advantages over conventional flotation technology, we sought new applications for its use in the pulp and paper industry. One of them was the cleaning of whitewaters. We studied the performance of flotation column on a paper machine whitewater at the Bowater Gatineau mill: PM6’s silo whitewater. Under proper aeration conditions, flotation performance was very good. Up to 64% of residual inks were removed while improving brightness up to 1.8 points. At the same time, total extractives were reduced by up to 85%. INTRODUCTION In its quest to reduce freshwater consumption, the pulp and paper industry faces many challenges. The accumulation of fines will reduce sheet drainage, while the enrichment of dissolved colloidal solids will promote corrosion and paper machine deposition [1]. These problems may result in a lower quality sheet [2-6]. The most commonly used approach to control fines build-up in the whitewater circuit is to capture them in the wet web via a retention program. In highly closed systems, several chemical measures are however needed to maintain the effectiveness of retention aids and these can be very costly. Except for increasing retention agent dosages or modifying the retention program, we know of no unit operations on a paper machine capable of cleaning whitewater circuits of contaminated fines. Save-alls, such as disc filters, or dissolved air flotation devices (DAF) enable the mill to separate fines and fillers from whitewater circuits. When these units are used in conjunction with paper machines, the contaminated solids are then often returned to the headbox without eliminating or removing them. In fact, this whitewater recirculation amplifies the concentration of contaminated fines and fillers around the paper machine [6]. After many cycles of recirculation, fines lose brightness, are tainted by repeated dye applications, and are contaminated in extractives, micro-stickies and metals. On the paper machine these solids, rich in lipophilic material, can be destabilized by pH or temperature shocks and lead to the build up of deposits which may negatively affect paper machine runnability. Optical and physical properties can also be impaired by the incorporation of contaminated fines to the sheet [5-7]. Though this is not the best practice, recirculated or aged fines are often brought back to the pulp production plants where they reduce pulp brightness. To regain brightness, greater dosages of sodium hydrosulfite or hydrogen peroxide are then needed, which consequently raise production costs. Because theses fines contain the highest proportion of metals contained in the pulp, they will contribute to the decomposition of bleaching agents [8-11], thus amplifying bleaching problems. As these contaminated fines are the source of many problems around the paper machine, we have explored the use of column flotation technology as a mean to decontaminate the paper machine whitewater circuits. Column Flotation Flotation deinking is a key unit operation in most paper recycling plants for the removal of hydrophobic contaminants from pulp [12]. There is a wide variety of flotation cells available for deinking but the dominant technology typically consists of multiple horizontal flotation cells in series, with each cell being aerated by several injectors. To reduce fibre losses, flotation rejects of this primary stage are generally treated in secondary cells. In flotation, hydrophobic particles, including ink, become attached to air bubbles that are injected into the pulp slurry. These ink-laden bubbles then rise to the surface of the flotation cell and accumulate in the froth where they are removed by overflow or suction. Ideally, only the ink particles should be floated. However, some hydrophilic material such as fibres, fines, and fillers, are physically entrained into the flotation froth, which reduces the selectivity of the flotation process [13]. Flotation columns that were developed by the mineral industry for the separation and recovery of ores [14, 15] use these same flotation principles as horizontal cells. Compared to them, flotation columns have a greater height-to- width ratio and are equipped with a downwards washing shower to prevent entrainment of the longer fibres. Advantages of the column over conventional flotation cells include higher selectivity driving higher fibre yield, small floor space requirement, adaptability to automated control, and lower capital, operating, and maintenance costs [16-19]. Recently, Ben et al. [20] adapted the small pilot-scale flotation column from McGill University [21, 22] to recuperate valuable fibres from dissolved-air flotation rejects and to remove macrostickies and waxes from an old corrugated container pulp [20, 23]. EXPERIMENTAL Flotation Column This study was performed on a laboratory-scale flotation column built at FPInnovations, Paprican [20]. The column, shown in Figure 1, has a 10.2-cm diameter and a height of 4.65 m. The principle of the flotation column is simple. The pulp slurry, which is fed just underneath the froth level, descends in the column counter current to the raising bubbles, which are injected at the bottom of the column. This air can be generated by internal or external sparging systems. It is common to separate the flotation column in two distinctive zones: the froth zone and the collection zone. In the collection zone, hydrophobic materials are collected by the air bubbles and transferred to the froth zone. The froth is pushed by incoming bubbles to the top and overflows as rejects, while the accepted pulp slurry is removed at the base of the column. At the top of the flotation column, wash water can be added in the froth zone to reduce fibre entrainment which in turn increases the process yield by increasing the selectivity of flotation for hydrophobic contaminants such as ink. The wash water also contributes to froth stability. Residence time in the flotation column was controlled by increasing proportionally the feed and accepts flow rates. For our tests, the air content in the collection zone was maintained stable at 20% (v/v) and the froth height was kept at 50 cm. WASH WATER Froth Zone REJECTS Collection Zone FEED ACCEPTS AIR Figure 1. Schematic of FPInnovations flotation column with froth and collection zones [20]. Whitewater As a means to decontaminate paper machine whitewater circuits, we evaluated the performance of column flotation on a sample of whitewater from Paper Machine 6 of the Bowater Gatineau mill in Canada. Samples were shipped to FPInnovations in totes of 1 m3 capacity from the mill and treated within three days. They were heated to 50°C in a thermostatically controlled reservoir during the trials. Table 1 provides some characteristics of these whitewater samples. Table I. Characteristics of mill whitewater samples. Type of whitewater Silo Mill Product Newsprint DIP, % 50 TMP, % 50 Consistency, % 0.53 Ash Content, % 15.2 ISO Brightnessa, % 56.1 ERICa, ppm 195 DCM Extractivesa, % 2.1 a Measured on handsheet of fines Analytical Methods After flotation, the overflowing material (rejects) was weighed and the decontaminated whitewater (accepts) was sampled from the base of the flotation cell. Whitewater consistency and ash content were measured according to PAPTAC standard methods D.16 and G.30P, respectively. For measurement of optical properties and chemical analyses, handsheets of 1.2 g of whitewater feed, accepts and rejects were made according to PAPTAC standard method C.5, except that a number 500-mesh screen was used for the sheet formation [5, 24]. To prevent washing of the fines during handsheet formation, no dilution water was added to the samples in the deckle. Brightness was measured on handsheets according to PAPTAC Standard Method E.1. The effective residual ink concentration (ERIC) was measured using the Technibrite ERIC 950 Instrument using the instruments defaults that assumes a scattering coefficient of 47 m2/kg [25]. Ink removal efficiency of whitewater solids through flotation was calculated as: % ink removal = ((ERICfeed - ERICaccepts) / ERICfeed) × 100. Total dichloromethane (DCM) extractives were determined on freeze-dried pulp using the Soxtec method with DCM as the solvent in a single extraction step [26]. Deresination of whitewater solids through flotation was calculated on a weight basis as: % extractives removal = ((Extractfeed - Extractaccepts) / Extractfeed.) × 100 The particle size distribution of suspended solids (feed, accepts and rejects) were determined using the Mastersizer S Particle Size Analyzer (Malvern Instruments) [5, 27]. RESULTS AND DISCUSSION During this study, we examined the effects of residence time and washing water flow rate on the flotation response of silo whitewater from a newsprint mill using 50% deinked pulp in its furnish. The flotation performance was evaluated by measuring the brightness gain and by estimating the ink and extractives removal. Particle size distribution of whitewater samples was also determined. Deresination Column flotation was very effective at removing the DCM extractives. Figure 2 shows that at six minutes, up to 85 % (w/w) extractives were removed. These results show that column flotation may be an effective process unit for deresination of a whitewater stream. It removes hydrophobic material like contaminated fines and fillers which may negatively impact the strength properties of paper [3, 6, 28]. 2.5 2.0 , %(w/w) 1.5 1.0 0.5 DCM Extracts DCM 0.0 0 3 6 Flotation Time, min Figure 2. Removal of extractives from whitewater by column flotation. Brightness Improvement Figure 3 shows that at a residence time of six minutes, the mean brightness gain was 1.8 points whereas the gain at three minutes flotation time was smaller at 0.1 units. 59 58 57 56 Brightness, % 55 54 0 3 6 Flotation Time, min Figure 3.
Details
-
File Typepdf
-
Upload Time-
-
Content LanguagesEnglish
-
Upload UserAnonymous/Not logged-in
-
File Pages8 Page
-
File Size-