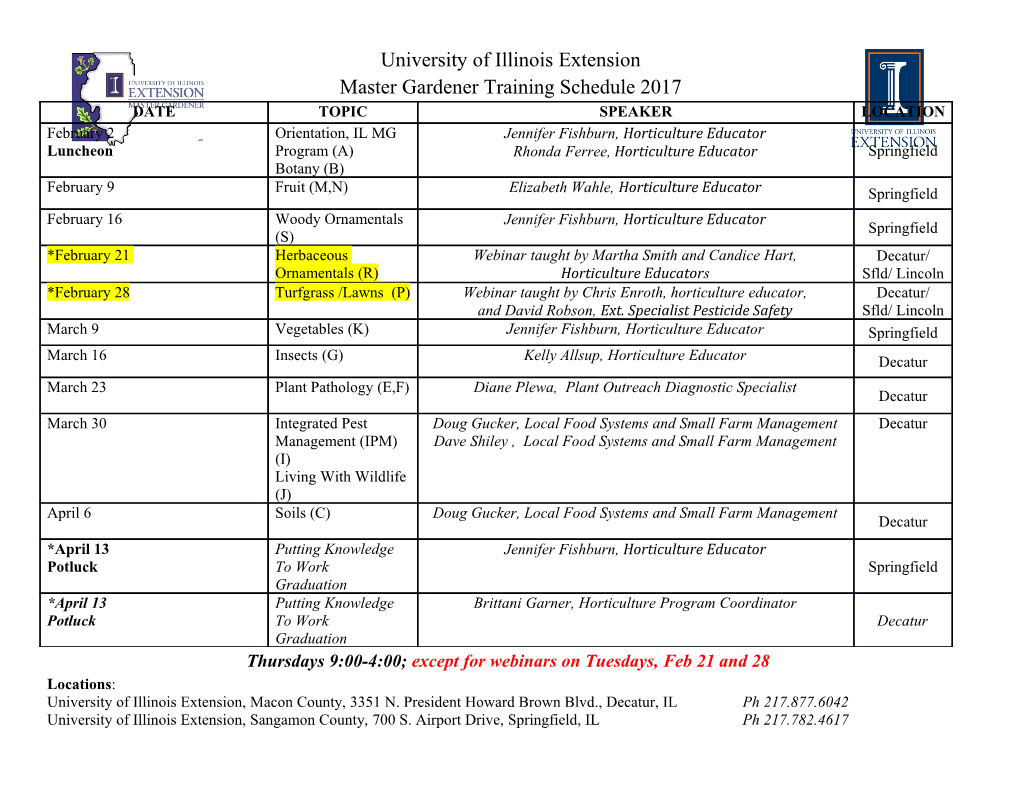
Australian Journal of Basic and Applied Sciences, 5(12): 3112-3121, 2011 ISSN 1991-8178 Cinematic and Kinetic Analyses of the Slider-Crank Mechanism in Engine of MF-285 Tractor 1Mohammad Reza Asadi, 1Heidar Abdollahian and 1Behnam Nilforooshan Dardashti 1Department of Mechanical Engineering, Islamic Azad University, Buinzahra branch, Qazwin, Iran. Abstract: MF-285 tractor has devoted the highest production level in Iran among the other tractors. According to the literature, malfunction of the internal components of engine of this tractor is high; consequently research about it is necessary. In this regard, this paper presents the cinematic and kinetic analyses of the connecting rod. Besides crank mechanism cinematic analysis, kinetic analysis of the connecting rod was done with regard to the forces resulting from ignition pressure, mass distribution in the crank mechanism as well as inertia forces. At the end, the graphs of displacement, speed and acceleration of piston, and also the graphs of ignition pressure, forces on piston, forces on connecting rod and forces on bears in one complete cycle according to the crank angle were drown by mathematica software. The maximum of piston speed equal with 13.5 m/s, the maximum of piston acceleration equal 3550 m/s2, the maximum of ignition pressure equal 2950 KPa, the maximum expansion force on connecting rod equal 10288 N, the maximum of compression force on connecting rod equal 19730 N and the maximum force on bears equal 30000 N were calculated. By the result of this paper there is possibility stress, fatigue, modal, harmonic and etc analyses of rotational part of engine of this tractor and suggest for improvisation of this part. Key word: Tractor; Crank mechanism; Analyses; Cinematic; Kinetic. INTRODUCTION Tractor, as the most important agricultural machinery, has main share in planting, retaining and harvesting operations and then in mechanization sector. Hence, in order to reach sustainable agricultural and to increase mechanization level quality and manufacturing technology of this agricultural machinery and also its quantity must be reached to optimum level. Tractor MF-285 is main production of Iran Manufacturing Tractor Co. Researches show that engine inner parts’ faults of MF-285 are more than other ingredients of this tractor (Anonymous, 2008). Above statements show the importance of optimization of rotating parts of tractor MF-285 engine. The base of engine dynamic mechanism operation is slider-crank mechanism which consist crankshaft, connecting rod and piston. Pressure due combustion, transferred from piston (the part merely has reciprocating motion) to the connecting rod (the part has both linear and rotation motion) and finally to the crankshaft (the part has merely rotation motion). As investigation of phenomena like vibration, resonance, fatigue, noise . , and optimization of these parts, kinematics and kinetic of slider-crank mechanism must be known. Optimization of mechanical instruments has been one of engineer goals. Below paragraphs are some examples: Cveticanin and Maretic have summarized dynamic analysis of a cutting mechanism which is a special type of the crank shaper mechanism (Cveticanin L, 2000). The influence of the cutting force on the motion of the mechanism was Considered. The Lagrange equation was used and boundary values of the cutting force were obtained analytically and numerically. Ha et al. (2006) have derived the dynamic equations of a slider-crank mechanism. They, for this purpose, used Hamilton’s principle, Lagrange multiplier, geometric constraints and partitioning method (Ha JL, 2006). Their formulation was expressed by only one independent variable. Finally to obtain the best dynamic modeling, they compared obtained results and numerical simulations. Also, a new identification method based on the genetic algorithm was presented to identify the parameters of a slider-crank mechanism. Koser (2004) investigated on kinematic performance analysis of a slider-crank mechanism based on robot arm performance and dynamics (Koser K., 2004). He analyzed kinematic performance of the robot arm using generalized Jacobian matrix. It was obtained that the slider-crank mechanism based robot arm had almost full isotropic kinematic performance characteristics and its performance was much better than the best 2R robot arm. He used complex algebra to solve that classical problem and he obtained solution as the root of a cubic equation within a defined range. Corresponding Author: Mohammad Reza Asadi, Department of Mechanical Engineering, Islamic Azad University, Buinzahra branch, Qazwin, Iran. E-mail: [email protected] 3112 Aust. J. Basic & Appl. Sci., 5(12): 3112-3121, 2011 Another research about transmission angle was carried by Shrinivas and Satish (2002). They have summarized importance of the transmission angle for most effective force transmission. In this regard, they investigated 4-, 5-, 6- and 7-bar linkages, spatial linkages and slider-crank mechanisms (Shrinivas SB, 2002). 2. Methods: 2.1 Kinematics Analysis Of Slider-Crank Mechanism: MF-285 engine has 4 cylinders with linear arrangement. Engine configuration and qualifications has been shown in Table 1. Table 1: Configuration and qualifications of MF-285 engine (Anonymous, 2008). Number of Cylinders 4 Piston Course (mm) 127 Cylinder diameter (mm) 101 Indicated Revolution (rpm) 2000 Maximum Revolution (rpm) 2200 Indicated Engine Power (Hp) 71 Maximum Torque (N/m2) 278 Revolution in Maximum Torque (rpm) 1300 According to figure (1) distance of piston from center of rotation can be obtained by below equations: Sp Rcos Lcos (1) That: R: Radius of crank shaft L: Length of connecting rod Fig. 1: Schematics of crank mechanism. With regard to triangular equations in OAB triangle: Rsin Lsin (2) By aid of above equation we can delete from equation 1: 1 S R(cos 1 2 sin 2 ) (3) p By developing above equations we will have: 1 (4) S P R cos (cos2) 4 3113 Aust. J. Basic & Appl. Sci., 5(12): 3112-3121, 2011 According to this point that is function of time (a t) for calculating speed and acceleration of connecting rod we calculate differential of equation 4 so: V R(sin sin 2) (5) 2 R 2 (cos cos2) (6) 2-2 Kinetics Analysis Of Connecting Rod: 2-2-1 Forces Due To Ignition Of Fuel: During a work cycle which is a combination of breathing, congestion, explosion and discharge stages, a lot of interactions occur in the engine which will affect on one another and make the calculation difficult. For example, we can mention the heat transfer during the ignition between gas and the engine partition, the effect of the mixture form on the auto-engine and the effect of transfusion quality in the diesel engine. So, only by studying the actions and reactions one by one, we can reach to an accurate conclusion. Therefore, it is necessary to study the engine performance under the simple hypotheses, and neglect the unimportant effects. The selected process for designing the diagram of gas pressure in terms of crank angle consists of following hypotheses (Asadi, M., 2008); 1. The mixture of gas and fuel is considered the ideal gas. 2. There is no physical or chemical change in the congested weather in the congestion stage and before the explosion. 3. Immediate alteration of gas and fuel mixture with the hot gas product of combustion. 4. The congestion and explosion stages are adiabatic. 5. The suction and discharge occur in the atmosphere pressure. The forces produced by combustion, are the factors which make the mechanism move. For dynamic calculations, we substitute the pressure on the piston with a force in the direction of the cylinder. Amount of this force in any moment is calculated from this equation: Fg (Pg P0 ).AP (7) Pg: the gas pressure at any moment Po: the pressure of the weather outside AP: the area of the piston surface The only unknown variable in the above equation is Pg which is a function of the angle and is calculated from thermodynamics relationship by the above hypotheses. A) The Congestion Stage: Considering the adiabatic process of the gas congestion we will have: n P2 V1 (8) P1 V2 P1 and P2 are respectively the primary and secondary pressure V1 and v2 are respectively the primary and secondary volume The primary pressure changes, in terms of the movement velocity of piston, the relative size of tubes, the appearance of tubes and other factors. When the engine works at low speed with maximum load, the pressure approaches the atmosphere pressure. The analysis of indicator diagrams has shown that the "n" value for this engine is about 1.21 (Prvardhans, 2005). The height of cylinder chamber is calculated through this equation: l h (9) r 1 l: the length of piston r: congestion ratio 3114 Aust. J. Basic & Appl. Sci., 5(12): 3112-3121, 2011 The distance of the cylinder head to the piston crest, while piston is at the bottom dead center is: l rl l (10) r 1 r 1 Now we assume the piston is in the distance x from the top dead center. The pressure in this stage will be: 1.21 rl 1.21 r l rl 1.21 Pg Pi Pi x (11) x r 1 P1: the gas pressure at the beginning of congestion B) The Explosion Stage: In this stage, the pressure is constant until the fuel is sprayed, and after the spraying interruption and explosion ending, the pressure decreases with the increase of the combustion chamber volume. So we can define this stage consisting of two kinds of pressures: the constant pressure and the variable pressure. Knowing that the fuel spraying continues up to 30 degrees after the top dead center, so the pressure will be constant from the top dead center to 30 degrees after top dead center, which is calculated by this equation: n P4 V3 (12) P3 V4 P4: the gas pressure at the end of explosion stage P3: the gas pressure in the fuel spraying stage V4: the volume at the end of explosion stage V3: the volume at the end of fuel spraying stage From the equation above, the pressure at the time of fuel spraying was found 2950 KPa.
Details
-
File Typepdf
-
Upload Time-
-
Content LanguagesEnglish
-
Upload UserAnonymous/Not logged-in
-
File Pages10 Page
-
File Size-