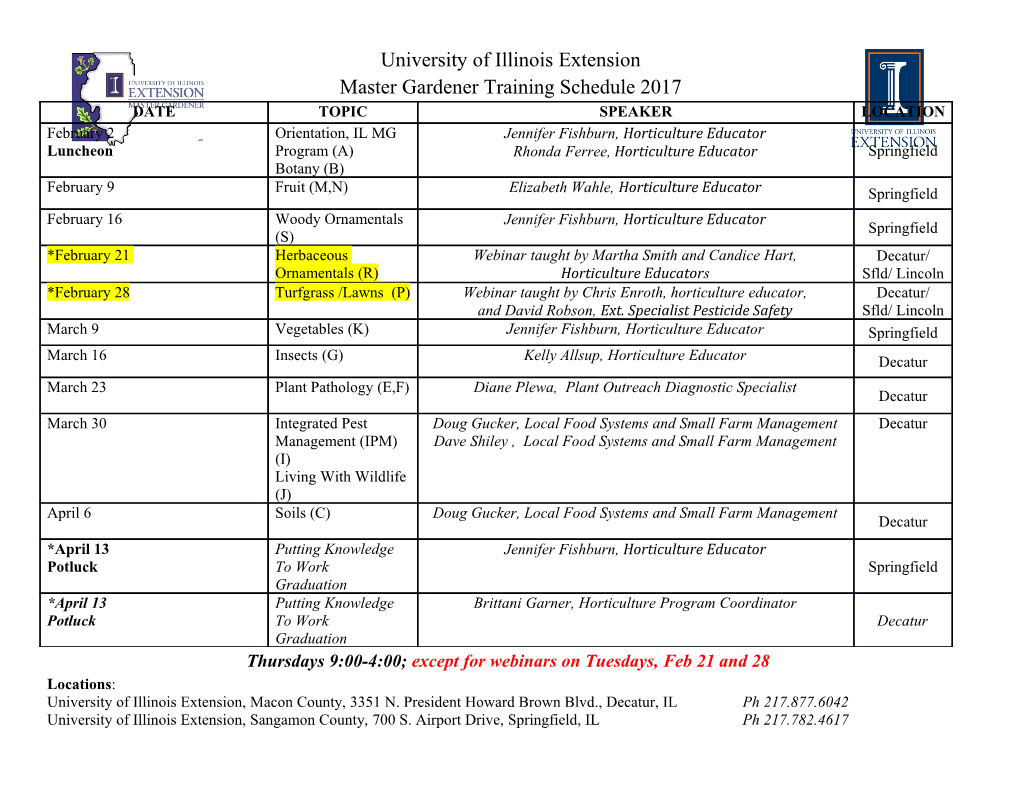
Preface This report has been written within the framework of my master thesis with an assignment from TNO Defence, Security and Safety, Rijswijk, The Netherlands at the Faculty of Aerospace Engi- neering of the Delft University of Technology in the Netherlands. The assignment was to inves- tigate several different ramjet concepts for flight in the hypersonic regime, and to compare them through their overall performance and discuss their gasdynamic phenomena within the engine flow path. This was done in order to determine a pre-design test setup for a proof-of-concept of that ramjet concept which outperforms the other concepts to test its feasibility. During my thesis work I have had the privilege of working with many people from all over the university, and at TNO. Overall, I would like to thank my supervisors, P.G. Bakker, R.G. Veraar and W.J. Bannink, for their advice and comments to my work and their patience. I have enjoyed the discussions and debates with my teachers, fellow students, roommates, friends and family about all the issues I faced during my work on my thesis and appreciated all their support. I could not have done this without them. Bert Tayara. Delft, December 2008 Summary Recently, supersonic combustion ramjets are more and more realised to become the next-generation steady airbreathing propulsion systems operating in the hypersonic flow regime. Due to this re- newed interest, this thesis investigates several hypersonic ramjet engine concepts using supersonic combustion to determine which concept is more viable of becoming the next-generation propulsion system. The investigation of hypersonic ramjets is done by identifying two kinds of supersonic combustion methods for ramjet engine concepts, which are diffusion combustion and pre-mixed combustion. From these two combustion types four different ramjet concepts are investigated: the scramjet, the dual-mode combustor, the shock-induced combustion ramjet (shcramjet), and the oblique detonation wave engine (ODWE). To analyse their overall performance, diffusion com- bustion is modelled as a constant-pressure heat addition process (Brayton model), and pre-mixed combustion (associated with shock-induced combustion) is modelled as a constant-volume heat addition process (Humphrey model). Detonations, however, are modelled as a discontinuity wave where across heat addition occurs (Fickett-Jacob model). The analysis comprises of an ideal ther- modynamic effciency determination and an one-, or quasi-one-dimensional analytic performance analysis with freestream Mach numbers up to 20. The analysis investigates three combustion per- formance charachteristics; the total pressure loss, the entropy increase, and the specific impulse. The results show that detonation waves have the highest ideal thermodynamic efficiency, followed by constant-volume heat addition and then constant-pressure heat addition. The analytical per- formance analysis however shows that detonation waves have the lowest overall performance and constant-volume heat addition the highest overall performance. This contradiction is explained due to the fact of irreversible entropy generation, coinciding with total pressure losses, being higher for detonation waves than for the other two heat addition models. The detonation wave thus remains a theoretical limit of the shock-induced combustion wave. A proof-of-concept test setup pre-design is then suggested to demonstrate the feasibility of shock-induced combustion as a next-generation propulsion system. i Contents 1 Introduction 2 1.1 Thesis Structure . 2 1.2 Steady Airbreathing Engines . 3 1.3 The Ramjet . 5 1.3.1 The TurboRamjet . 6 1.3.2 Ideal Ramjet Performance . 7 1.4 Supersonic Combustion . 12 1.5 Hypersonic Flow . 14 2 Supersonic Combustion Ramjets 16 2.1 The Scramjet . 16 2.1.1 Supersonic Inlets . 17 2.1.2 Supersonic Combustors . 28 2.1.3 The Nozzle . 41 2.1.4 Scramjet Performance . 42 2.2 The Dual-Mode Combustor . 46 2.2.1 The Isolator . 48 2.2.2 Thermal Choking . 53 3 Shock-Induced Combustion Ramjets 56 3.1 Shock-Induced Combustion . 56 ii CONTENTS 3.1.1 Experimental Results with Shock-Induced Combustion . 56 3.1.2 Numerical results with Shock-Induced Combustion . 61 3.2 Detonations . 64 3.2.1 The Chapman-Jouguet Model . 64 3.2.2 The ZND Model . 67 3.2.3 Detonation Wave Structure and Stability . 68 3.3 Propulsion System Designs . 71 3.3.1 The Shcramjet . 71 3.3.2 The Detonation Wave Engine . 75 4 Performance Analysis 80 4.1 Thermodynamic Efficiency . 81 4.2 Quasi-One-Dimensional and Two-Dimensional Analysis of Supersonic Flow with Heat Addition . 85 4.2.1 Quasi-One-Dimensional Constant-Pressure Heat Addition . 85 4.2.2 Quasi-One-Dimensional Constant-Volume Heat Addition . 88 4.2.3 Normal and Oblique Detonation Waves . 95 4.2.4 Performance Analysis Results . 102 4.3 Proof-of-Concept Test Setup Pre-Design . 112 5 Conclusion and Recommendations 118 5.1 Conclusion . 118 5.2 Recommendations . 121 iii List of Figures 1.1 The turboprop, [Source: Cislunar Aerospace Inc.] . 3 1.2 The turbofan, [Source: Cislunar Aerospace Inc.] . 4 1.3 The turbojet, [Source: Cislunar Aerospace Inc.] . 4 1.4 The ramjet, [source: Cislunar Aerospace Inc.] . 5 1.5 The Blackbird . 7 1.6 Ramjet schematic . 8 1.7 Ramjet specific thrust (de Wolf) . 10 1.8 Ramjet specific thrust (de Wolf) . 10 1.9 Ramjet specific thrust (Mattingly) . 11 1.10 Ramjet specific impulse (Mattingly) . 11 1.11 Ramjet combustor entrance temperature . 13 2.1 The X-43 . 16 2.2 Ramjet and scramjet geometry . 17 2.3 Scramjet inlet station definitions . 18 2.4 Starting and maximum contraction ratios . 19 2.5 Operating modes of a scramjet inlet: (a) design mode, (b) flight Mach number higher than the design value, (c) flight Mach number lower than the design value. 20 2.6 2D-planar scramjet inlet design . 21 2.7 Shock wave system used for the analysis, source [Smart, 1999] . 21 2.8 Oblique shock wave definitions . 21 iv LIST OF FIGURES 2.9 Maximum total pressure recovery for two-dimensional scramjet inlets with up to five shocks, source [Smart, 1999] . 22 2.10 Optimal turning angles for two-dimensional scramjet inlets with one internal shock wave: a) n = 3, b) n = 4, c) n = 5 shock waves, source [Smart, 1999] . 22 2.11 Oswatitsch inlet design, source [Curran, 2000] . 23 2.12 Busemann inlet design, source [Curran, 2000] . 23 2.13 Aft sweep and forward sweep inlets, source:[Curran, 2000] . 24 2.14 Three-dimensional inlet design, source:[Curran, 2000] . 24 2.15 Main characteristics of a boundary layer . 25 2.16 Impinging oblique shock wave with and without a boundary layer . 26 2.17 Originating oblique shock wave with and without a boundary layer . 26 2.18 a) weak combustion and b) strong combustion . 30 2.19 REST inlet model (Smart, 2006) . 31 2.20 Control volume constant area combustor . 32 2.21 Course of G3 ....................................... 32 2.22 Rayleigh functions for a constant area channel with heat addition . 34 2.23 The pressure ratio p3/p2 as function of entrance conditions and energy addition . 35 2.24 Control volume divergent area combustor . 35 2.25 The local Mach number Mx in a divergent combustor and in a Rayleigh flow . 36 2.26 The total pressure loss in a divergent combustor and in a Rayleigh flow . 37 2.27 Schematic of an acoustic-convective feedback loop in a scramjet combustor, source: [Li, 2007] . 37 2.28 Transverse injection flowfield two- and three-dimensional, source: [Gruber 2000, Lee 2003] . 39 2.29 Parallel injection scheme . 39 2.30 Flame holding cavity design . 40 2.31 Transverse injection without and with cavity, source: [Mingbo, 2007] . 40 2.32 Scramjet nozzle design SERN . 41 2.33 Inlet kinetic energy efficiency non-viscous flow and viscous flow for different values of M3 ........................................... 43 v LIST OF FIGURES 2.34 Total pressure ratio across the combustor . 44 2.35 Scramjet and ramjet specific thrust . 45 2.36 Scramjet and ramjet specific impulse . 46 2.37 a) dual-mode combustor schematic, b) typical axial distribution of wall pressure when operating in scramjet mode . 47 2.38 Structure of the flow in a shock train region, source: [Matsuo, 1999] . 48 2.39 Structure of the flow in a pseudo shock region, source: [Matsuo, 1999] . 49 2.40 Schlieren photograph of a shock train, moving from left to right with M = 1:75 . 49 2.41 Experimental photos of shock diamond patterns in an overexpanded flow, source: www.aerospaceweb.org . 50 2.42 Typical shock train patterns with increasing Mach number M, source: [Matsuo, 1999] 50 2.43 Control volume for the isolator containing a shock train . 51 2.44 Variation of M3 with increasing p3=p2 and constant M2 . 52 2.45 Variation of A3c=A2 with increasing p3=p2 and constant M2 . 52 2.46 Flow visualization by schlieren photographs of runs conducted by Schnerr; a) sub- critical flow with Mk ≈ 1:27, b) supercritical flow with Mk ≈ 1:16, c) supercritical flow with Mk ≈ 1:13, and d) supercritical flow with Mk ≈ 1:1 . 54 2.47 Schematic of acoustic-convective feedback loops in a dual-mode combustor . 55 3.1 Pulsating reaction waves in 2D (left) and 3D (right) with different velocities, source: (Lehr, 1972) . 57 3.2 Change in oscillation frequency with changing velocity, source: (Lehr, 1972) . 58 3.3 McVey and Toong's x-t diagram along the stagnation streamline, source: (McVey, 1971) . ..
Details
-
File Typepdf
-
Upload Time-
-
Content LanguagesEnglish
-
Upload UserAnonymous/Not logged-in
-
File Pages147 Page
-
File Size-