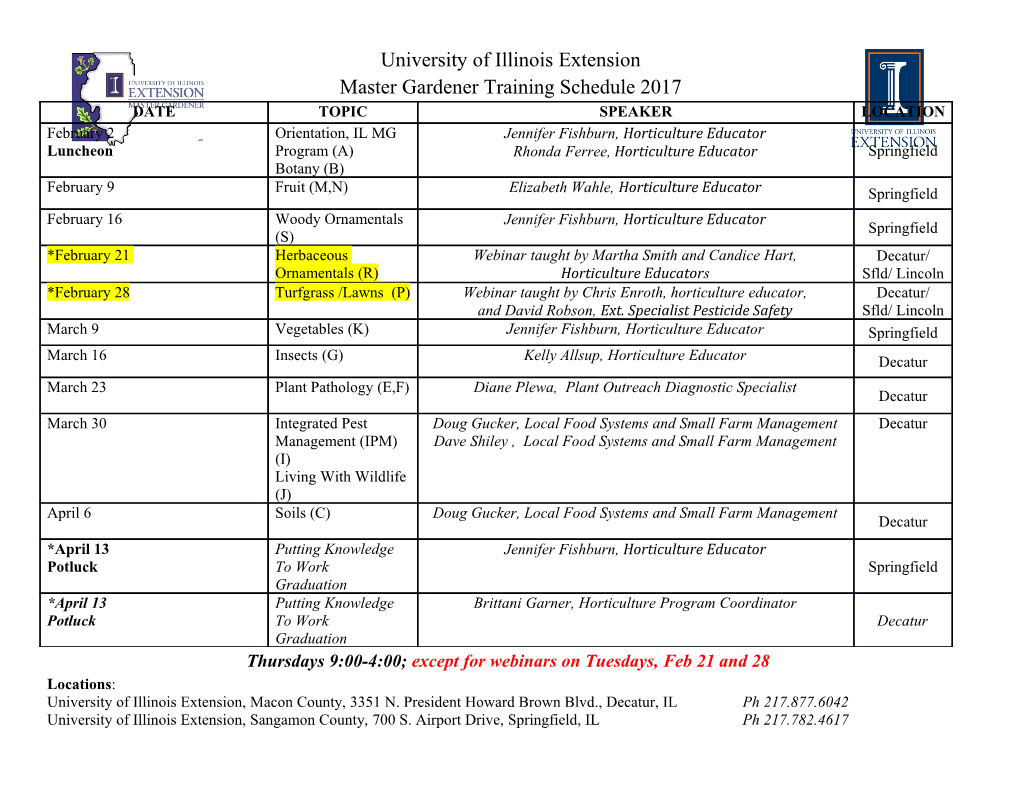
CAN in Automation (CiA) - Controller Area Network (CAN) CAN HLP Members only Map home CAN in Automation (CiA) international users and manufacturers group Founded in March 1992, CiA provides technical, product and CAN Information in marketing information with the aim of fostering Controller Area Dutch Network’s image and providing a path for future developments of the CAN protocol. The non-profit trade association with a persistently increasing number of members develops and supports various CAN-based higher layer protocols: CAN Application Layer (CAL), CAN Kingdom, CANopen, DeviceNet. Higher layer CAN the bus CiA members protocols (HLP) only - General introduction - General introduction - CiA specifications - Specifications - CANopen - Technical info - Controller - Devicenet - Marketing info - Applications - CAN Kingdom Events Standardization Products CiA phone +49-9131-69086-0 fax +49-9131-69086-79 Literature Download News email:[email protected] http://www.can-cia.de/ [14.11.1999 12:45:51] CAN in Automation Higher Layer Protocols HLP DeviceNet CANopen General introduction General introduction Technical introduction Technical introduction Specifications Specifications Conformance test Conformance test FAQs FAQs Vendor list CAN Application Layer CAN Kingdom General introduction General introduction Technical introduction Technical introduction Specifications Specifications © CAN in Automation last update: 1999-07-26 http://www.can-cia.de/hg.htm [14.11.1999 12:46:07] CAN in Automation General introduction DeviceNet Page contents: Features and functionality More: First information Technical introduction Features and functionality Specifications Network Up to 64 nodes Conformance test Size FAQs Network Selectable end-to-end network distance varies with speed Length Page contents: Top Baud Rate Distance Features and 125 Kbps 500 m (1,640 ft) functionality First information 250 Kbps 250 m (820 ft) 500 Kbps 100 m (328 ft) Data 0-8 bytes Packets Bus Linear (trunkline/dropline); power and signal on the same Topology network cable Bus Peer-to-Peer with Multi-Cast (one-to-many); Multi-Master and Addressing Master/Slave special case; polled or change-of-state (exception-based) More: System Removal and replacement of devices from the network under Features power Technical introduction First information Specifications Conformance test DeviceNet is a low-cost communications link to connect industrial FAQs devices (such as limit switches, photoelectric sensors, valve manifolds, motor starters, process sensors, bar code readers, variable frequency drives, panel displays and operator interfaces) to a network Page contents: and eliminate expensive hardwiring. Top The direct connectivity provides improved communication between Features and devices as well as important device-level diagnostics not easily functionality accessible or available through hardwired I/O interfaces. First information DeviceNet is a simple, networking solution that reduces the cost and time to wire and install industrial automation devices, while providing interchangeability of "like" components from multiple vendors. DeviceNet is an open network standard. The specification and http://www.can-cia.de/hdg.htm (1 von 2) [14.11.1999 12:46:16] CAN in Automation protocol are open; vendors are not required to purchase hardware, software or licensing rights to connect devices to a system. Anyone may obtain the DeviceNet Specification from the Open DeviceNet More: Vendor Association, Inc. (ODVA) for a nominal reproduction charge. Any company that manufactures (or intends to manufacture) Technical DeviceNet products may join ODVA and participate in technical introduction working groups that are developing enhancements to the DeviceNet Specifications Specification. Conformance test Buyers of the DeviceNet Specification receive an unlimited, FAQs royalty-free license to develop DeviceNet products. Companies looking for assistance may purchase sample code that eases their implementation, development toolkits, and development services from Page contents: many sources. The key hardware components are available from the largest worldwide suppliers of semiconductors. Top Features and Why the DeviceNet Communication Link? functionality First information For years the process industry has been attempting to develop a single, open standard to address all kinds of field devices. The original scope of their standards effort was aimed at replacing the 4-20 mA standard with a single digital standard. As the scope increased to address complex and sophisticated services (such as high data rate communications between controllers, time synchronization of large numbers of devices scanning at very high speeds), the development of a single standard became delayed. At the same time, the cost of communication technology has dropped More: considerably in recent years, making it cost-effective to connect simple Technical devices never considered for SP50 fieldbus directly to a network. Such a standard for simple devices requires the same level of introduction interchange-ability as exists for 120/220 VAC and 24 VDC discrete, Specifications hardwired I/O. DeviceNet allows the interchangeability of simple Conformance test devices while making interconnectivity of more complex devices FAQs possible. In addition to reading the state of discrete devices, DeviceNet provides the capability to report temperatures, to read the load current in a motor starter, to change the deceleration rate of Page contents: drives, or to count the number of packages that have passed on a conveyor in the previous hour. Top Features and © ODVA - The Open DeviceNet's Vendor Association functionality First information © CAN in Automation last update: 1999-07-27 http://www.can-cia.de/hdg.htm (2 von 2) [14.11.1999 12:46:16] CAN in Automation Technical introduction DeviceNet Page contents: Physical Layer and Media More: Indicators and Configuration Switches General introduction Communication Protocol and Application Specifications The Object Model Conformance test Messaging FAQs Predefined Master/Slave Connection Set Device Profiles Page contents: Physical Layer and Media Top Chapter 9, Volume 1 in the DeviceNet Specifications defines the Physical Layer and allowable Topologies and components. The variety of Topologies Media that are possible is shown in Figure 2. The specification also deals Indicators and with system grounding, mixing thick and thin media, termination, Configuaration Switches and power distribution. Communication Protocol and Application The basic trunkline-dropline Topology provides separate twisted pair The Object Model busses for both signal and power distribution. Thick or thin cable can Messaging be used for either trunklines or droplines. End-to-end network Predefined Master/Slave distance varies with data rate and cable size. Connection Set Device Profiles Data Rates 125 Kbps 250 Kbps 500 Kbps Thick Trunk Length 500 m 250 m 100 m (1,640 ft) (820 ft) (328 ft) Thin Trunk Length 100 m 100 m 100 m (328 ft) (328 ft) (328 ft) More: Maximum Drop Length 6 m 6 m 6 m (20 ft) (20 ft) (20 ft) General introduction Cumulative Drop Length 156 m 78 m 39 m Specifications (512 ft) (256 ft) (128 ft) Conformance test FAQs The end-to-end network distance varies with data rate and cable thickness. Devices can be powered directly from the bus and communicate with each other using the same cable. Nodes can be removed or inserted from the network without powering-down the network. Power taps can be added at any point the network, which makes redundant power supplies possible. The trunkline current rating is 8 amps. An opto-isolated design option allows externally powered http://www.can-cia.de/hdt.htm (1 von 15) [14.11.1999 12:47:01] CAN in Automation devices (e.g. AC Drives starters and solenoid valves) to share the Page contents: same bus cable. Other CAN-based networks allow only a single power supply (if at all) for the entire network. Top Physical Layer and Media Indicators and Configuaration Switches Communication Protocol and Application The Object Model Messaging Predefined Master/Slave Connection Set Device Profiles More: General introduction Specifications Conformance test FAQs Page contents: Top Physical Layer and Media Indicators and Configuaration Switches Communication Protocol and Application The Object Model Messaging Predefined Master/Slave Connection Set Device Profiles http://www.can-cia.de/hdt.htm (2 von 15) [14.11.1999 12:47:01] CAN in Automation More: General introduction Specifications Conformance test FAQs Page contents: Top Physical Layer and Media Indicators and Configuaration Switches Communication Protocol and Application The Object Model Messaging Predefined Master/Slave Connection Set A simplified block diagram of transceivers with both isolated and Device Profiles non-isolated physical layers is shown in figure 3 and figure 4. The DeviceNet Specifications contain additional information concerning component requirements, protection from mis-wiring, and examples. More: General introduction Specifications Conformance test FAQs Figure 5. Open and Sealed Connectors are available on DeviceNet Several different connector types can be used on DeviceNet (see figure 5). Both sealed and unsealed connectors are available. Large (mini-style) and small (micro-style) sizes of pluggable, sealed connectors are available. For products, which do not require sealed connectors, open-style connectors can be used. Screw or clamp connections can be made directly to the cable if a pluggable connection is not required.
Details
-
File Typepdf
-
Upload Time-
-
Content LanguagesEnglish
-
Upload UserAnonymous/Not logged-in
-
File Pages150 Page
-
File Size-