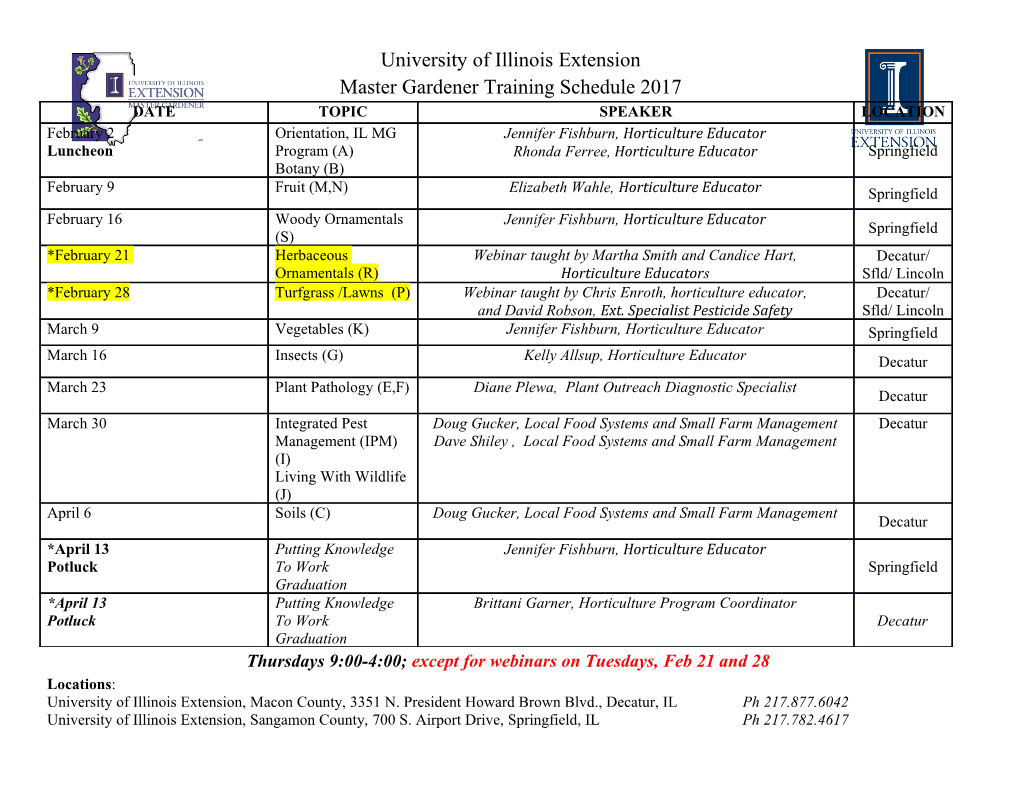
Design of a Robotic Water-Pipe Rehabilitation System by Yip Fun Yeung Submitted to the Department of Mechanical Engineering in partial fulfillment of the requirements for the degree of Master of Science in Mechanical Science and Engineering at the MASSACHUSETTS INSTITUTE OF TECHNOLOGY June 2019 © Massachusetts Institute of Technology 2019. All rights reserved. Sigatue edacted A uthor ................... I f Department of Mechanical Engineering May 19, 2019 Signature redacted Certified by.. Kamal Youcef-Toumi Professor Thesis Supervisor Signature redacted Accepted by ..................... Nicolas Haijiconstantinou FTEO Chairman, Department Committee on Graduate Thesis JUN 13 2019 LIBRARIES H 2 Design of a Robotic Water-Pipe Rehabilitation System by Yip Fun Yeung Submitted to the Department of Mechanical Engineering on May 19, 2019, in partial fulfillment of the requirements for the degree of Master of Science in Mechanical Science and Engineering Abstract Corrosion in water pipeline causes leak and forms tubercle at the vicinity of leaks. Various in-pipe robots have been developed in recent years for locomotion and in- spection along the pipeline. Not much focus is put on in-pipe operations such as pipe maintenance and rehabilitation. This thesis presents an in-pipe robotic system for minimal particle contamination obstruction removal operation of corroded water pipes. It proposes a robotic system with a Manipulation Module and a Compliant Surface Adaptation Module. The Manipulation Module contains a 4-Degree of Free- dom robotic manipulator that is able to remove tubercle in 102mm diameter pipes. The Compliant Surface Adaptation Module contains optimized designs to enclose a watertight volume on a macroscopically rough surface. This robotic platform is the first in-pipe robot designated to rehabilitate water pipe with minimal contamination. Thesis Supervisor: Kamal Youcef-Toumi Title: Professor 3 4 i Acknowledgments I am honored to express my deepest thank to my advisor, Prof. Kamal Youcef-Toumi, for guiding me with extensive knowledge and patience through my first two years at MIT. His vision in future and persistence in details set everyone in Mechatronics Research Laboratory a good model. It is a pleasure for me to learn from and work with such a great professor. I would also like to take this time to thank our sponsor, Mathearth.Inc. Without their proficient resource and technology guidance, this project wouldn't have been possible. I am also grateful to Boston Water and Sewer Commission, for providing us with valuable samples of water pipes and practical advice in water network. I am very thankful to my colleagues on this project, Tyler Okamoto, Xiaotong Zhang and Elizabeth Mittmann for our daily collaboration. They are also excellent mates outside the lab. I really enjoy our time supporting each other. My deepest gratitude towards my friends at MIT and Harvard, especially Chen, who stood by me days and nights for the last two years. Best of luck in your future work. Last but not least, I wish to thank my family members for providing me with consistent love and mental support. I would like to dedicate this thesis to my pet, Sam, who passed away last week after being my dearest friend for 12 years. Rest in peace brother. 5 6 A Contents 1 Introduction 17 1.1 Motivations for Water Pipe Rehabilitation . ... .. ... 17 1.2 Background of Water Pipe Rehabilitation . ..... ... 18 1.2.1 Rehabilitation Process ...... ... ..... 18 1.2.2 Robotic In-Pipe Solution ..... ..... .... 19 1.3 Thesis Outline .............. .. ..... .. 21 2 System Overview 23 2.1 Proposed System Layout .. ....... .... ..... 23 2.2 Design and Work-flow ......... ..... ... 24 2.3 Sum m ary ....... .......... ... ..... 26 3 Compliant Surface Adaptation Module - Design 27 3.1 Background of seals ........ .... 27 3.1.1 Dynamic Seal ........... 28 3.1.2 Static Seal ............. 29 3.2 CSAM Functional Requirement ..... 29 3.3 Design Overview ............. 30 3.4 Modelling and Analysis .......... 31 3.4.1 Objective and Review 31 3.4.2 Silicone Cross-section Optimization . .... 32 3.4.3 Compression Spring Suspension Optimization 42 3.5 Sum m ary ..... ...... ...... ...... 46 7 4 Compliant Surface Adaptation Module - Implementation 47 4.1 Silicone Cushion .............. ......... 47 4.1.1 Material Selection ......... ... ..... 48 4.1.2 Substrate Surface Roughness .. ......... 50 4.1.3 Design Process .. .... ... ......... 51 4.1.4 Finalized Design . ..... .. .. ..... .. 54 4.2 Compression Spring Suspension . ... .... ..... 55 4.3 Fabrication . ..... .... ..... ......... 56 4.4 Design Process Summary ... ... .. 57 ......... 4.5 Chapter Summary .. ... ... ... 57 5 Manipulation Module 59 5.1 Functional Requirement . .... ... 59 5.2 Mechanical Design . .... ... ... 60 5.2.1 Assumption ... ... ... .. 60 5.2.2 Design Description . ... .. 60 5.2.3 Forward Kinematics .. ... 62 5.2.4 Force Analysis ... ... .... 64 5.3 Controller Design . .... ..... .. 66 5.4 Material Selection .. .... ..... 67 5.5 Summary .. ..... .... ..... 68 6 System Integration 69 6.1 System Prototype .. .... ... ... 69 6.2 Experiment Overview . .. ... ... 71 6.2.1 CSAM Test . ... ... ... 71 6.2.2 Kinematics Test ... ... ... 72 6.2.3 Maneuverability Test .. .... 74 6.2.4 Corroded Pipe Surface Treatment 75 6.3 Summary ... .... .... ... .. 77 8 q1 11R111" "W-W-1 7 Conclusion and Recommendation 79 7.1 Thesis Summary and Contribution ................... 79 7.2 Recommendations for Future Research ............ ..... 80 A Persson Contact Theory 81 A.1 Persson Contact Theory Key Equations ................. 81 A.2 Surface Roughness Parameters from PCT ............. ... 82 B Concept Validation for CSAM 85 9 10 List of Figures 1-1 Illustration of the leak detection method using a suction force caused by a pressure gradient. ....... ....... ...... 1 9 1-2 Karso Working Robot. .............. 20 2-1 Proposed work flow for each sub-system of MRL pipe rehabilitation robot ................ .. ..... .. .. .. ...... 24 2-2 Demonstration of the Manipulation Module ............. 25 3-1 Demonstration of a dynamic seal. ........ 28 3-2 Mildly corroded water pipe. ........... 30 3-3 Severely corroded water pipe section obtained from Boston Sewer and Water Commission. ................ ....... 31 3-4 Final design of CSAM. .......... .... .... ... 32 3-5 Exploded view of CSAM. ... .......... ....... 33 3-6 Demonstration of CSAM application. ...... ....... 34 3-7 Demonstration of self-affine surface. ....... ... .. 35 3-8 Dimensional analysis of two H2 values. .... .. ... .. 38 3-9 Dimensional analysis with 14/U15. ........ ... .. 39 3-10 Grooved CSAM silicone cross-section. ...... ....... 40 3-11 Grooving the cross-section significantly reduces 11,. ......... 40 3-12 Experimentally determine aspect ratio to maintain structural rigidity. 41 3-13 Change in pipe wall profile statistically affect average height of the tub ercle. .......... ..................... .. 42 3-14 Simplified model of silicone-spring assembly. ........ ..... 43 11 3-15 Compression spring suspension materials and critical dimensions. .. 45 4-1 Experimental setup for Compression Experiment I. ..... .... 48 4-2 Compression Stress-Strain curve for Ecoflex 00-30. .... ..... .. 49 4-4 Topology of 3d-printed rough surface to simulate tubercles. ..... 50 4-5 Height distribution of the 3d-printed rough surface. ..... .... 50 4-3 Power spectrum for the 3d-printed rough surface. .. .... .... 50 4-6 Dimensionless H groups for the 3d-printed substrate. .. ..... .. 51 4-7 Dimensions of cylindrical specimens. .... ...... ...... .. 52 4-8 Leak experiment setup. ... ..... ..... ...... ..... .. 52 4-9 Leak pressure pi for the cylindrical tests. ... .... .... .... 53 4-10 Experimental and theoretical result represented in dimensionless H group ....... ........ ........ ....... ...... 54 4-11 Finalized design of silicone cross-section. .... ..... .... ... 55 4-12 Fabricated CSAM .. .... .... .... .... .... .... ... 56 5-1 Demonstration of MRL pipe rehabilitation robot and global coordinates. 60 5-2 Robot kinematics and D-H notation for robotic platform. .... ... 61 5-3 Workspace for the spindle and the CSAM when in contact with 102mm diameter pipe surface. ..... ..... ..... .... ..... .. 63 5-4 End effector workspace for the 22mm tool head. ... .... .... 64 5-5 Bench-top tubercle removal experiment. ..... .... ..... .. 65 5-6 Force analysis of MPCOR. ... ..... ...... .... ..... 65 5-7 Schematic for automated tubercle removal task. .. ..... ..... 66 6-1 Prototyped CSAM with modifications to connect with Manipulation M odule. ... ... .... ... ... .... ... ... .... ... 69 6-2 Prototyped MPCOR. A: 2-DOF Manipulator; B. CSAM; C. CSAM attached to Manipulation Module; D: Full assembly of MPCOR. 70 6-3 Mock rough surface board with obstructions and height drops corre- sponding to tubercle and pipe profile change. ...... ........ 71 12 6-4 Experiment demonstrates the good sealing performance of CSAM with grooved design and compression spring suspension. ......... 72 6-5 Step response of each joint of Manipulation Module given a simulated deploym ent task. ..... ....... ........ ........ 73 6-6 Prototyped MPCOR is tested in a 102mm pipe with 3d-printed tubercle. 74 6-7 MPCOR in maneuverability test. ....... ........ ..... 75 6-8 MPCOR in maneuverability test. ....... ........ ..... 76 A-1 Energy equilibrium of Persson Contact Theory. ........... 82 B-1 Surface contact FEA of hyperelastic material. .. ........... 86 13 14 List of Tables 3.1 Unit for each parameter in fundamental dimensions.
Details
-
File Typepdf
-
Upload Time-
-
Content LanguagesEnglish
-
Upload UserAnonymous/Not logged-in
-
File Pages89 Page
-
File Size-