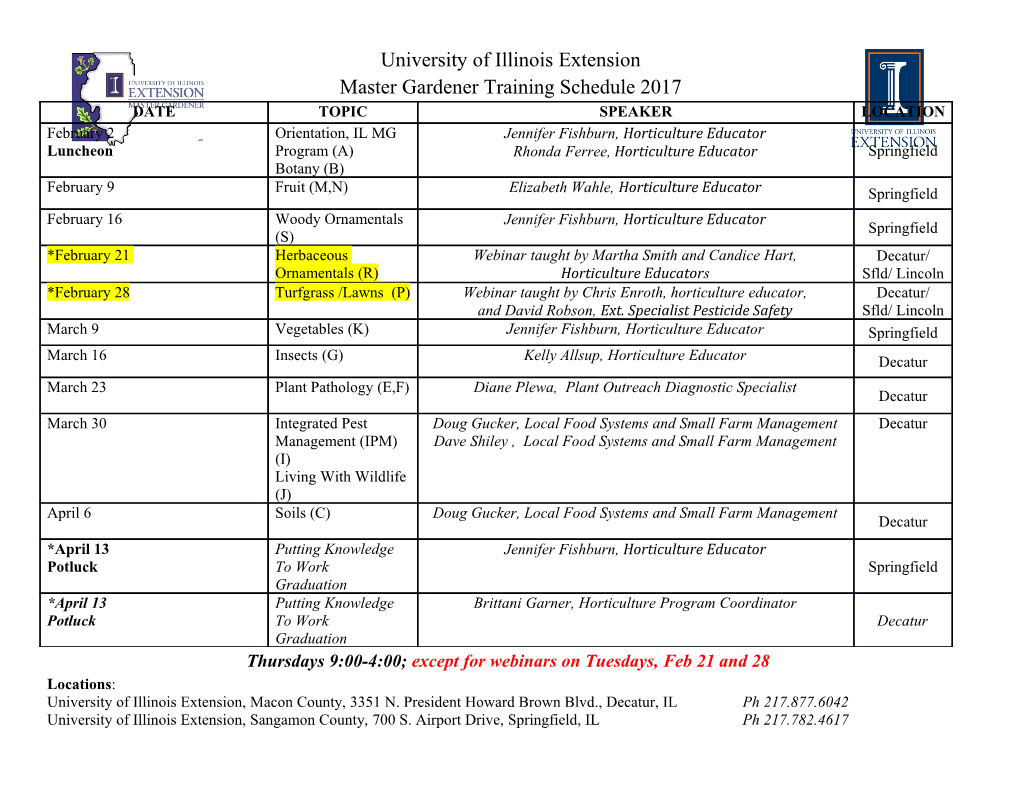
LINEAR MOTION DEVICES ACTUATORS.....................................................A257 rends in the last few the assembly to your ma- decades have led de- BEARINGS........................................................A268 chine. Similarly, you can T signers to rethink CONTROLS.......................................................A271 get an actuator that is syn- concepts of industrial mo- LINEAR MOTION DEVICES ADVERTISING .......A272 chronous-belt-driven for tion. Companion gains in the linear actuation, motor- control theory and hard- ized, and with integral ware allow schemes for geared speed reducer. You complete motion systems not previ- can also get electrohydraulically actu- ously possible. And motion technolo- linear part of its path, with or without ated devices that use the precision of gies from fields as diverse as national special attachments. digital control with the high force of a defense and medical diagnostics are • Plastic drive tape. hydraulic cylinder. You can get any available for exploitation in other • Sliding-action leadscrew (usually such packages with integral control fields. The primary effect is that to- acme screw), with nut. hardware and software. day’s designers must consider not just •Ball-bearing leadscrew (ball- industrial “power transmission” along screw) with nut. The balls recirculate Screw jacks shafts and through reductions, but into and out of the load zone. also the broader concept of industrial • Planetary roller screw, in which One of the older conventional actu- motion and control. And linear mo- a nut engaging several planetary ation packages, the screw jack, comes tion is an essential part of it. threaded rollers mounts on a in a single housing containing the in- Many modern processes call for threaded shaft. The threaded rollers put rotating shaft, the output linear unattended operation, exceptional also engage the shaft. Axes of shaft, motion shaft (screw), all bearings, precision, high throughput, flexibility nut, and rollers are parallel. Threads and the lubricant. The user connects a for short runs, and total manufactur- on the nut and planetary rollers are of motor and the load attachment. There ing integration. Often in such cases, the same helix angle. are three major types. humans can’t perform well enough. • Recirculating roller screw, in Machine-screw jack. In the com- Modern sensors and controls, coupled which a nut engaging several grooved mon machine-screw jack, Figure 1, ro- with diverse and precise linear and rollers mounts on a threaded shaft. tation of the input (worm) shaft turns rotary motion devices, combine to fill The rollers also engage the shaft. Dif- the worm gear and drive nut, which the needs. Thus, designers must con- fers from the planetary roller screw in connects rigidly to the worm gear. sider linear motion as an integral part that rollers recirculate into and out of The leadscrew (also called the lifting of industrial motion and control. the load zone. screw or stem) is of acme or modified The major componentry of linear • Skewed rollers on a rotating cy- square-thread form. It is threaded motion systems can be categorized as: lindrical rod (traction motion on a through the drive nut and converts • Actuators. threadless rod). rotary motion of the nut to linear mo- • Support systems (bearings). • Fluid-power cylinder with direct- tion, if the screw is kept from turning •Control systems and components. driving rod, rodless cylinder, or cable with the drive nut. Many equipment manufacturers cylinder. Rolling-element bearings support supply complete systems that include • Electric solenoid. the input shaft and worm gear to mini- all major types of components. • Electric linear motor, such as lin- mize frictional loss. Thrust bearings ear induction motor or linear step support the load. The stem cover stores motor. lubricant and helps protect the stem ACTUATORS • Adapted electric rotary motor. A from damage and contamination. Common linear actuation devices common type has no shaft. The rotor Machine-screw jacks come in many for single-axis motion include, but are also serves as the mating nut on a stock sizes with load ratings from less not limited to: leadscrew with axis coincident with than 1 to more than 250 tons. A jack • Various complex linkages such rotor axis. can mount stationary so the stem re- as a walking beam or slider-crank Preceding listing order does not im- ciprocates, or an external nut can be mechanism. ply relative importance. used so the stem rotates and the nut • Gear rack and pinion set. Many linear actuation devices (attached to the load) reciprocates. • Plate or disc-cam drive with come as complete packages. For ex- Most machine-screw jacks are self- fixed-axis follower. ample, you can get a motorized ball locking. Thus, the load remains sta- • Cylindrical-cam drive with fixed- screw powered through spur or worm tionary in the event of a power failure. axis follower. gearing, and fully self-contained so The major limitation of machine- • Chain, belt, or cable drive in the that you need only mount and wire screw jacks is low efficiency, typically 1998 PT Design A257 Screw-jack application. Figure 3 de- picts a typical lifting ar- rangement, sometimes called a T-sys- tem. It shows how one motor can power sev- eral synchro- nized lifting points by us- ing couplings and right-an- gle gearboxes. Selection of the best ar- rangement for an application is usually based on space Figure 1—Typical machine screw jack. availability and motor accessibility. 25% or less. Sliding between drive nut Here are some guide- and screw generates heat. This heat- lines: ing restricts duty cycles of machine • Keep screw load di- screws to 5 to 7 1/2 min/hr at full load. rection parallel to the Ball screw jack. If an application screw axis as much as calls for the advantages of a machine- possible. Figure 2 — Typical ball screw jack. screw jack, but needs a longer duty • Keep the span between drive cycle or higher efficiency, a better components as short as practical. • You can include other torque-sens- choice may be a ball screw jack, Fig- That keeps interconnecting shafting ing devices into a jack or a motor to pro- ure 2, or a roller-screw jack. See also short and limits the chance of a criti- tect the whole system from overload. discussions “Ball screws” and “Roller cal-speed problem. To select a screw jack, use a system screws” which follow. The heart of a • When necessary, use pillow- design manual having illustrations, ball screw jack is an assembly com- block supports, dynamically balanced column strength charts, power and posed of a screw and nut, separated shafting, or both, to help avoid criti- torque data, and sample calculations. by a recirculating series of balls. The cal-speed vibrations. ball screw jack works like a ball bear- • Select shaft cou- ing and has similar life predictability. plings with high Rolling friction of the ball screw, strength-to-bore ra- compared with sliding friction of the tios (such as gear cou- machine screw, generates little heat. plings) to minimize This allows higher lifting speeds in system inertia. the ball screw jack and much better • Use three and efficiency, typically 92 to 95%. The four-way miter boxes higher efficiency reduces input power whenever possible, requirement to about two thirds that to shorten intercon- of a machine-screw jack for a given necting shafts. load. Besides higher efficiency than • Use limit machine-screw jacks, ball screw jacks switches to restrict have a lower ratio of starting to run- extremes of stem ning torque. Because of low rolling travel, or connect ro- friction, many ball screw jacks can be tary switches di- back-driven. See the discussion on rectly to one unused back driving under “Ball screws.” side of the double- Roller-screw jack. You can also extending input improve on a machine-screw jack’s shaft of a jack. advantages by using a roller-screw • Use a slip cou- jack. See the discussion under “Roller pling between motor and jack input Figure 3 — Typical screw jack system screws” which follows. shaft to provide overload protection. arrangement. A274 1997 Power Transmission Design Before selecting any jack equip- preloaded ball screws, a common back- screw does add resisting torque. In ment, determine: lash range is 0.002 to 0.013 in., de- some applications such as numeri- • Number of lifting points. pending on screw size and ball diame- cally controlled machines, in order to • Total load per jack. ter. To avoid backlash, one nut can be specify the screw’s motor drive com- • Load direction (tension or com- preloaded against another on the pletely, you must know preload pression). screw so there is no play. Similarly, torque in addition to load torque. Con- • Speed at which load must move. one ball circuit can be preloaded sult the ball screw manufacturer. • Total distance load must move. against another within the one nut. In Life expectancy. A ball screw is Also, consider duty cycle and envi- some assemblies, slots cut in the nut like a ball bearing in many ways, and ronmental conditions such as tempera- make it act as a preloaded spring when life expectancy is based on similar ture and contaminants. Next, using a mounted, or a clamping device can principles. For a ball screw, life expec- system design manual, make calcula- draw it up against the screw thread. tancy depends on: tions to determine input torque, speed, Mountings. Critical speed of any • Applied force, including accelera- and power requirements. Then check long shaft, including a ball screw, is a tion and friction loads. column strength and select the jack. speed at which it vibrates violently in • Number and length of load a transverse direction. It results from strokes. Ball screws rotating-system unbalance. The mem- For best life, the load should be ap- ber can have several critical speeds, plied along the same axis as that of The ball screw jack is a specific use all multiples or submultiples of one the ball screw.
Details
-
File Typepdf
-
Upload Time-
-
Content LanguagesEnglish
-
Upload UserAnonymous/Not logged-in
-
File Pages15 Page
-
File Size-