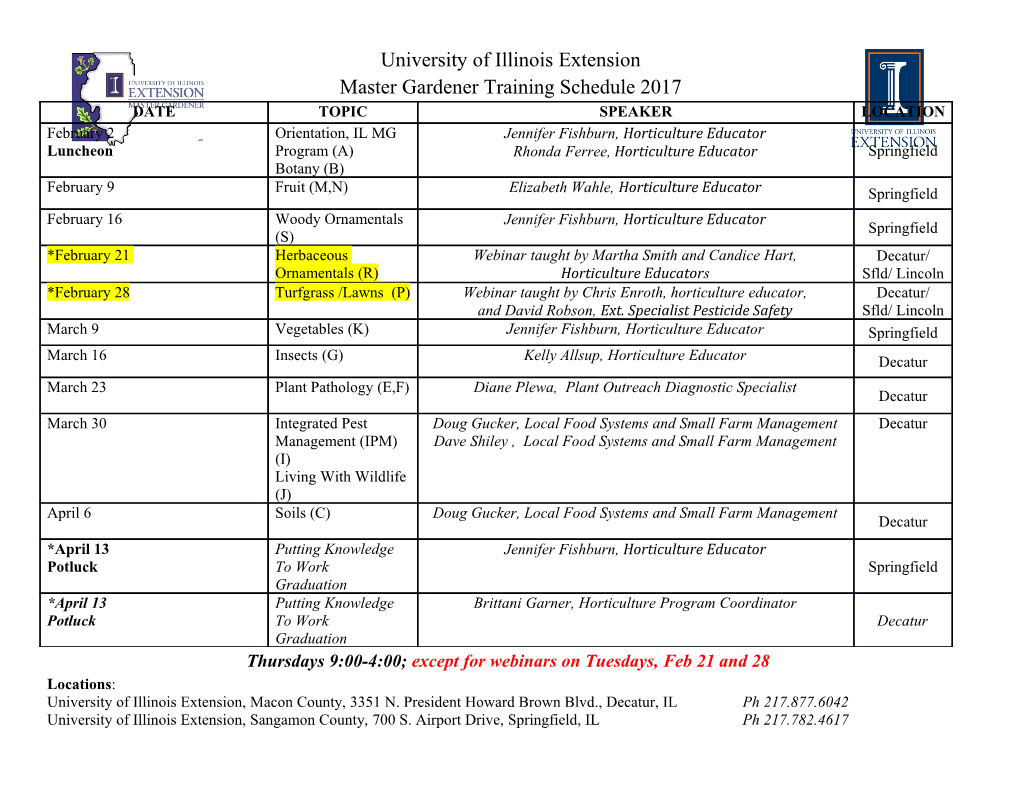
End Mill End Mill Icon Glossary Technical Data 2018 Master Number of Flutes Workpiece Catalog Z3 Material Group Center Cutting Steels Cutting Calculations And Definitions Metric U.S. P Width of cut, radial depth ae = (mm) (inch) of cut Depth of cut, axial depth Stainless Steels ap = (mm) (inch) Lengths of cut M Dc = Cutter diameter (mm) (inch) f = Feed per revolution (mm/rev) (IPR) Cast Iron fz = Feed per tooth (mm/tooth) (IPT) K zn = Number of teeth Number Coatings n = RPM (rev/min) (rev/min) Special Alloys Q = Metal removal rate (cm3/min) (in3/min) S vc = Cutting speed (m/min) (SFM) ALtima® TiAlN TiCN vf = Feed speed (mm/min) (IPM) Hardened Steels Dw = Working diameter (mm) (inch) H (35-65Rc) TiN Fordlube CERAedge® Formulas Non-Ferrous Inch N RPM (n) = SFM (vc) x 3.82/Tool Diam. 30° Helix Angle IPM (vf) = RPM (n) x IPR (f) Conversion Inch to Metric Coolant SFM (vc) to m/min (vc) = SFM (vc) x .3048 Maximum IPM (vf) to mm/min (vf) = IPM (vf) x 25.4 Ball Nose Max. Coolant Metric RPM (n) = m/min (vc) x 318.057/Tool Diam. Coolant Minimal mm/min (vf) = RPM (n) x mm/Revolution (f). Conversion Metric to Inch Neck Relief MMS Coolant m/min (vc) to SFM (vc) = (m/min)/.3048 N mm/min (vf) to IPM (vf) = (mm/min)/25.4 N Corner Radius Shank Made in USA Shank/DIN HB DIN6535 Chipbreaker Safety Note Always wear the appropriate personal protective equipment such as safety glasses and protective clothing when using solid carbide or HSS cutting Chipbreaker tools. Machines should be fully guarded. Technical data provided should be considered advisory only as variations may be necessary depending on the particular application. 300 M.A. Ford® Phone: 800-553-8024 or 563-391-6220 • email: [email protected] • www.maford.com End Mill Troubleshooting PROBLEM POSSIBLE CAUSE POSSIBLE SOLUTION Speed too high Reduce the cutting speed RPM’s (n). Improper feed speed (too slow) Increase feed per tooth (fz). Try 90-100 SFM (vc) with multi-fluted tool Hard workpiece material > 55 Rc (5 flutes+). Use ALtima® 52 hard coating. ® Change feed speed to change chip size or clear Recutting Chips chips with coolant or air pressure. Excessive Flank Wear Ensure you are climb milling unless workpiece material has hard/abrasive outer skin or high impact TuffCut Milling Strategy tool steel like D2, then conventional milling tech- nique is preferred for breakthrough. (see pg 304) Change to correct cutting angle, tilt tool at 15 Improper cutting angle degrees. Too low a primary relief angle Change to larger relief angle. Troubleshooting Icon Glossary / PROBLEM POSSIBLE CAUSE POSSIBLE SOLUTION Implementing corner radius on tool adds strength No Corner Radius and increases tool life. Speed too high Reduce the cutting speed RPM’s (n). Check tool runout in holder/spindle, <.0003" (.0076mm) desired. Hand ground flats can be sus- Excessive Corner Wear Tool Runout pect and common cause. Use collet, milling chuck, or shrink fit holders if possible. Ensure you are using shortest OAL possible, stub Tool Overhang tool in holder. Utilize stronger necked tool for longer reaches. PROBLEM POSSIBLE CAUSE POSSIBLE SOLUTION Information Technical Use shortest end mill available, hold shank deeper Lack of rigidity (tool) in holder, investigate for tool slippage. Use short gage length holder. Lack of rigidity (workpiece) Tighten workpiece fixture - a common problem. Feed too high Decrease feed per tooth (fz) Decrease feed per tooth (fz) on first pass through Feed to high on first pass workpiece skin or reduce radial width of cut (ae) first pass. Reduce FPT on entry - implement radius in or Part Entry sweeping entrances - avoid 90º (perpendicular) entry. Ensure you are climb milling unless workpiece material has hard/abrasive outer skin or high impact Milling Strategy Cutting Edge Chipping tool steel like D2, then conventional milling tech- nique is preferred for breakthrough. (see pg 304) Ensure you are using shortest OAL possible, stub Tool Overhang tool in holder. Utilize stronger necked tool for longer reaches. Check tool runout in holder/spindle, <.0003" (.0076mm) desired. Hand ground flats can be sus- Tool Runout pect and common cause. Use collet, milling chuck, or shrink fit holders if possible. Not enough rigidity of machine tool Change rigid machine tool or holder. & holder Ensure tool has proper edge prep for workpiece Cutting Edge Prep material. Teeth too sharp Change to lower cutting angle, primary relief. Technical data provided should be considered advisory only as variations may be necessary depending on the particular application. For product information, call your local distributor. 301 End Mill Troubleshooting Continued PROBLEM POSSIBLE CAUSE POSSIBLE SOLUTION Lack of rigidity (workpiece) Tighten workpiece fixture - a common problem. Speed too low Increase the cutting speed RPM’s (n). Feed too high Decrease feed per tooth (fz). Reduce width of cut, radial depth of cut (ae) & depth of Heavy depth of cut cut, axial depth of cut (ap). Reduce FPT on entry - implement radius in or sweeping Part Entry entrances - avoid 90º (perpendicular) entry. Review tool path and ensure there are no arbitrary moves, extreme arc of engagement increases & undesir- Milling Strategy Breakage able situations for the tool. Keep constant radial engage- ment. See tool path diagrams on page 304. Ensure you are using shortest OAL possible, stub tool in Tool Overhang holder. Utilize stronger necked tool for longer reaches. Check tool runout in holder/spindle, <.0003" (.0076mm) desired. Hand ground flats can be suspect and common Tool Runout cause. Use collet, milling chuck, or shrink fit holders if possible. Recondition at earlier stage. Factory recondition service Excessive edge wear is recommended. See M.A. Ford’s® Redbox recondition- ing program on page 456. PROBLEM POSSIBLE CAUSE POSSIBLE SOLUTION Utilize proper tool coating for workpiece material being Chip Welding to cutting edge cut. Climb mill preferred. Feed too low Increase feed per tooth (fz). Built Up Edge (BUE) Speed too low Increase the cutting speed RPM’s (n). Add coolant or readjust coolant flow, use through tool Coolant Strategy coolant if available. Check coolant mixture concentration. PROBLEM POSSIBLE CAUSE POSSIBLE SOLUTION Insufficient chip room Use end mill with fewer flutes. Feed too high Decrease feed per tooth (fz). Reduce width of cut, radial depth of cut (ae) & depth of Heavy depth of cut Chip Packing cut, axial depth of cut (ap). Apply more coolant to flush chips. Use air pressure or op. Not enough coolant stop to clear chips away. Large heavy chip Utilize chipbreaker style tool to cut chip size. PROBLEM POSSIBLE CAUSE POSSIBLE SOLUTION Feed too high Decrease feed per tooth (fz). Speed too low Increase the cutting speed RPM’s (n). Increase width of cut, radial depth of cut (ae) to stabilize Too light width of cut tool in cut. Check tool runout in holder/spindle, <.0003" (.0076mm) desired. Hand ground flats can be suspect and common Poor Surface Finish Tool Runout cause. Use collet, milling chuck, or shrink fit holders if possible. Built up Edge Use Flood Coolant. Redirect/Evaluate coolant flush - or use fewer number of Recutting Chips flutes. No end tooth concavity Add margin (touch primary with oilstone). Technical data provided should be considered advisory only as variations may be necessary depending on the particular application. 302 M.A. Ford® Phone: 800-553-8024 or 563-391-6220 • email: [email protected] • www.maford.com End Mill Troubleshooting Continued PROBLEM POSSIBLE CAUSE POSSIBLE SOLUTION Lack of rigidity (workpiece) Tighten workpiece fixture - a common problem. Use better machine tool, holder or change Lack of rigidity (machine & holder) condition. Ask your M.A. Ford® representative about BlueSwarf harmonic testing. Check tool runout in holder/spindle, <.0003" ® (.0076mm) desired. Hand ground flats can be Tool Runout suspect and common cause. Use collet, milling chuck, or shrink fit holders if possible. TuffCut Speed too high Reduce the cutting speed RPM’s (n). Chatter/Vibration Feed too low Increase feed per tooth (fz). Troubleshooting Chip too thin Utilize chip thinning adjustment multiplier. Use smaller tools and generate corner radii in pockets. Avoid tools that diameter matches Arc of engagement violation workpiece corner radius, or rough plunge corners. Ensure you are climb milling unless workpiece material has hard/abrasive outer skin or high Milling Strategy impact tool steel like D2 then conventional mill- ing technique is preferred for breakthrough. PROBLEM POSSIBLE CAUSE POSSIBLE SOLUTION Ensure you are using shortest OAL possible, Tool Overhang stub tool in holder. Utilize stronger necked tool for longer reaches. Increase diameter of end mill for higher End mill Diameter strength to length ratio. Higher number of flutes = larger core diameter Information Technical Tool Deflection Increase number of flutes = increased strength. Feed too high Decrease feed per tooth (fz). Too high width of cut Decrease width of cut, radial depth of cut (ae). Climb milling can help reduce the amount of Milling Strategy deflection in some cases. PROBLEM POSSIBLE CAUSE POSSIBLE SOLUTION Add coolant or readjust coolant flow, use Coolant Strategy through tool coolant if available. Check coolant mixture concentration. Tool Deflection See Tool Deflection above. No Dimensional Accuracy Feed too high Decrease feed per tooth (fz). (Wall Tapered) Too high width of cut Decrease width of cut, radial depth of cut (ae). Check tool runout in holder/spindle, <.0003" (.0076mm) desired. Hand ground flats can be Tool Runout suspect and common
Details
-
File Typepdf
-
Upload Time-
-
Content LanguagesEnglish
-
Upload UserAnonymous/Not logged-in
-
File Pages11 Page
-
File Size-