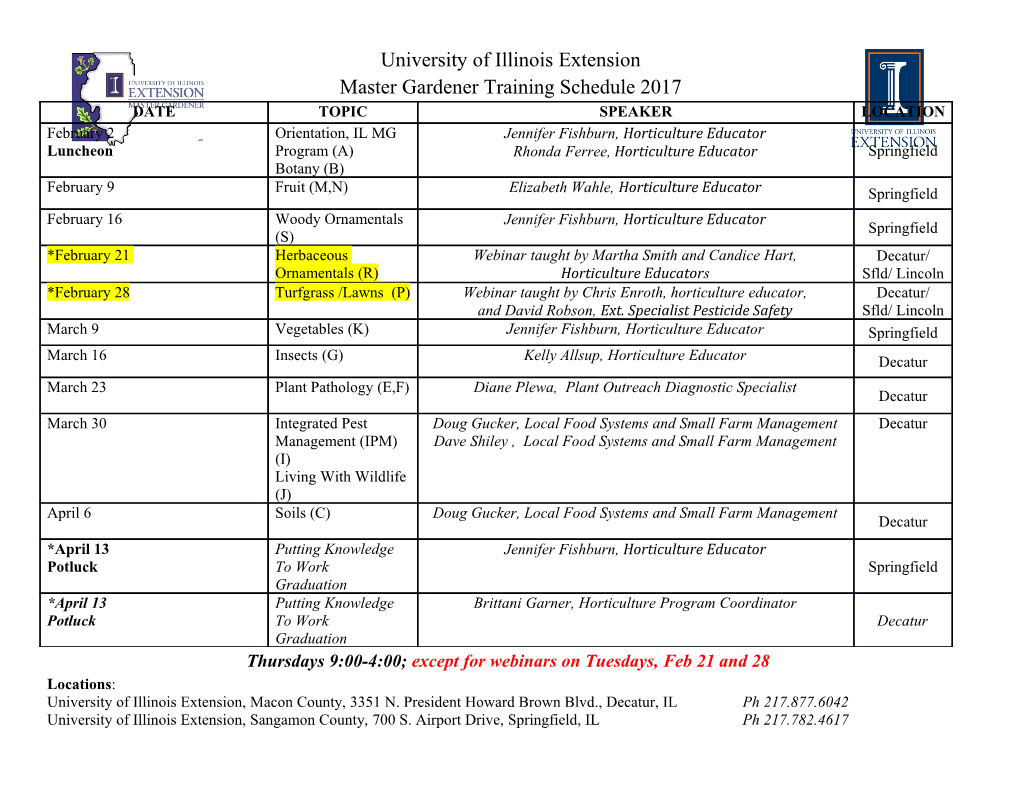
December 2019, Vol. 19, No. 6 MANUFACTURING TECHNOLOGY ISSN 1213–2489 Dynamic Analysis of the Crank Mechanism through the Numerical Solution Marián Minárik, Ferdinand Bodnár Department of Mechanics, Mechanical Engineering and Design, Faculty of Environmental and Manufacturing Techno- logy, Technical University in Zvolen, Študentská 26, 960 01 Zvolen, e-mail: [email protected], e-mail: [email protected] Dynamic analysis of crank mechanism is realised by relaxation method, where a connecting rod is modelled with three manners. In the first case the connecting rod is modelled as a rigid body, in the second case this one is modelled with two mass points and in the third case the connecting rod is modelled with three mass points. Results of all manners of modelling are compared and evaluated. Keywords: Crank Mechanism, Dynamic Analysis, Kinematic Quantities Introduction between kinematic and force quantities. Dynamic analysis of particular engine plant takes place on dynamic model of the system, which provides all needed force, weight and kinematics parameters for solution. Mathematical model consists of motion equati- ons built-up for every body of the solved system. Solution of motion equations provides the wanted quantities which can be needed force actions for the given motion of the system, or kinematics quantities of individual bodies for the given force actions. Analysis of given mechanical sys- tem presents all desired variables from known introdu- ctive quantities. The dynamical analysis of the given me- chanical system can be realised with different methods, e.g. by the relaxation method, used e.g. in [7] and [8], gearing down method of the weight and kinematics quan- tities or Lagrange’s equation of motion of second kind, used e.g. in [4]. Choice of the concrete method is depen- dent on the magnitude of searched quantities of the given mechanical system [1], [2], [9]. The basic and simultaneously the most universal me- thod of the dynamic analysis is relaxation method. The essence of the relaxation method is releasing of individual bodies of the created dynamic model of the system and the couplings between bodies are replaced by reaction forces as is used in the article [6]. Equations of motion Fig. 1 The crank mechanism and conditional equations are written for every released body. Conditional equations express the dependencies Tab. 1 Input values crankshaft length r 0.05 m connecting rod length l 0.134 m crank angle j 0 ¸ 2p rad -1 crankshaft rpm n21 2500 ot.min -1 angular speed w21 261.7994 rad.s force on piston F 2300 N mass of the crank m2 0.9 kg mass of the connecting rod m3 0.94 kg mass of the piston m4 0.04 kg mass of the connecting rod in point A,2 mA2 0.638358 kg mass of the connecting rod in point B,2 mB2 0.301642 kg mass of the connecting rod in point A,3 mA3 0.305449 kg mass of the connecting rod in point B,3 mB3 0.144333 kg mass of the connecting rod in point T,3 mT3 0.490217 kg 2 moment of inertia of the connecting rod IT3 0.00176 kg.m 2 complementary moment of inertia of the connecting rod Id -0.00192 kg.m indexed on: http://www.scopus.com 1003 December 2019, Vol. 19, No. 6 MANUFACTURING TECHNOLOGY ISSN 1213–2489 The aim of our dynamic analysis is determining of l = 134 mm, mass of the connecting rod m = 0.94 kg, hole magnitude of the moment transmitted on crankshaft ߈ of diameter for a pin d = 22 mm, hole diameter for a crank the centric crank mechanism and the couplings reactions D = 52 mm, calculated values are: l2 = 91 mm, 2 depending up the position of the crankshaft. Analyses are IT = 0.00176 kg.m . carried for three manners of modelling of the connecting 2.1 Dynamic analysis – the connecting rod is mo- rod. In the first case the connecting rod is modelled as a delled as a solid body (version 1) solid body, in the second case this one is substituted by two mass points and in the third case the connecting rod A free-body diagram for released piston ߊ from Fig. is modelled by three mass points. Results of all the said 1 is in the Fig. 2. The motion equation of the piston is manners of modelling are compared. (1) The crankshaft rotates with uniform angular speed w21 m4a41 = F - B34y and on the piston acts the constant force F from gas pres- Because the piston acceleration in x direction is zero, sure. The mass’s weights and friction forces are neglec- instead the motion equation it is the dependence ted. The input values of geometric and mass magnitudes are listed in the Tab. 1. N14 - B34x = 0 . (2) The connecting rod ߉ in Fig. 1 executes a general Dynamic analysis motion. Motion equations of connecting rod are Moment of mass inertia I and position l of centroid T 2 m a = B - A , (3) of the used connecting rod are determined from the repe- 3 31xT 43x 23x ated measuring of the time of a physical pendulum osci- m a = B - A , (4) llation [5]. For the given input values of the connecting 3 31yT 43y 23y rod: distance of holes axises of the connecting rod IT3j&& 31 -= B43y l2 sinb + B43x l2 cosb - A23y l1 sinb + A23x l1 cosb , (5) j&& 31 where and IT3 are an angular acceleration and a mo- ment of inertia of the connecting rod, respectively. Both are with respect to an axis that is perpendicular to the plane of motion of the connecting rod and passes through connecting rod centroid T3. Fig. 3 Released connecting rod (version 1) Fig. 2 Released piston Fig. 4 Released crankshaft 1004 indexed on: http://www.scopus.com December 2019, Vol. 19, No. 6 MANUFACTURING TECHNOLOGY ISSN 1213–2489 The crankshaft ߈ of Fig. 1 rotates around the fixed lar velocity of the crankshaft w21 and to formulate kine- axis, which passes through point O, with constant angular matic variables a41, aT31x, aT31y, j&& . velocity w21, (Fig. 4). 31 The moment transmitted on the crankshaft is In agreement with Fig. 1 the piston position s is . (9) M = r ()A32x cosj21 + A32y sinj21 . (6) s = l + r - r cosj21 - l cosb Because the crankshaft accelerations in both directi- At the close of kinematic analysis the piston accelera- ons x, y are zero, instead the motion equations there are tion a41 in time t is expressed the dependences 2 d s 2 a41 = 2 =& w21 r ()cosw21 t + l cos2w21 t , (10) A32x - O12x = 0 , (7) dt where l = r / l, accelerations of the gravity centre of the A - O = 0. (8) 32y 12y connecting rod aT31x, aT31y are Solving of equations (1) through (8) requires to 2 execute a kinematic analyse [3] for given constant angu- a 31xT = x&&T 3 -= l2 lw21 sinw21 t , (11) 2 2 a 31yT = y&& T 3 =& w21[]r()cosw21 t + l cos2w21 t - l2 l cos2w21 t (12) and the angular acceleration of the connecting rod a31 is met these conditions: · total weight of mass points must be equal to the 2 && . (13) a31 =j31 -= w21lsinw21 t weight of a body, For solving of equations (1) through (8) it is available · position of gravity centre of the system of mass the Newton’s 3rd Law, that is points must be the same with the gravity centre B34 = B43 , (14) of the body, · the moment of inertia of the body and of the sys- A23 = A32 . (15) tem of mass points, to the axis passing through Solution of equations (1) through (15) was done by the gravity centre perpendicular to plane of mo- numerical methods. Calculated results are visualised for vement, must be the same. one working cycle in Fig. 7 and Fig. 8. 2.2 Dynamic analysis – connecting rod is modelled by Replacement of the connecting rod by two mass points mass points (version 2) At solution of problems of the rigid body dynamics it Position of the one mass point with mass mA,2 is deter- is often convenient to replace a body by system of mass mined by point A and a position of the second point with points. For such replacement at planar motion must be the mass mB,2 is determined by point B. Conditional equations (16) for mass points have a form 2 2 m3 = mA 2, + mB 2, , mA l12, = mB l22, , IT 3 = mA l12, + mB l22, , (16) at which, according to Fig. 5, it is l = l + l . 1 2 2 2 Masses and positions of the mass points are unambi- Id = IT 3 - ()mA l12, + mB l22, = IT 3 - m ll 213 , guously designated by mA,2, l1, mB,2, l2. It means, if one of (18) these quantities is arbitrarily elected, the others follow where IT3 is the moment of inertia of the connecting rod from conditional equations. Because at replacement of with respect to an axis that is perpendicular to the plane the connecting rod by two mass points are elected positi- of connecting rod motion and passes through centroid T3 ons of both points l1, l2, the others follow from (16) of the connecting rod. l l Motion equations of the connecting rod on the basis m = m 2 , m = m 1 . (17) of Fig. 5 are A 2, 3 l B 2, 3 l And the moment of inertia must be compensated by mA 2, aA sinj21 + B43x - A23x = 0 , (19) the additional moment of inertia Id - mB 2, aB - mA 2, aA cosj21 - A23y + B43y = 0 , (20) Idj&& 31 = -B43y l2 sinb - mB 2, B la 2 sinb - A23y l1 sinb + (21) + mA 2, aA cosj l121 sinb + A23x l1 cosb + mA 2, aA sinj l121 cosb + B43x l2 cosb, a = w 2 r a = a j = w t Motion equations of remaining members of the me- at which A 21 , B 41 , 21 21 , chanism are unchanged.
Details
-
File Typepdf
-
Upload Time-
-
Content LanguagesEnglish
-
Upload UserAnonymous/Not logged-in
-
File Pages7 Page
-
File Size-