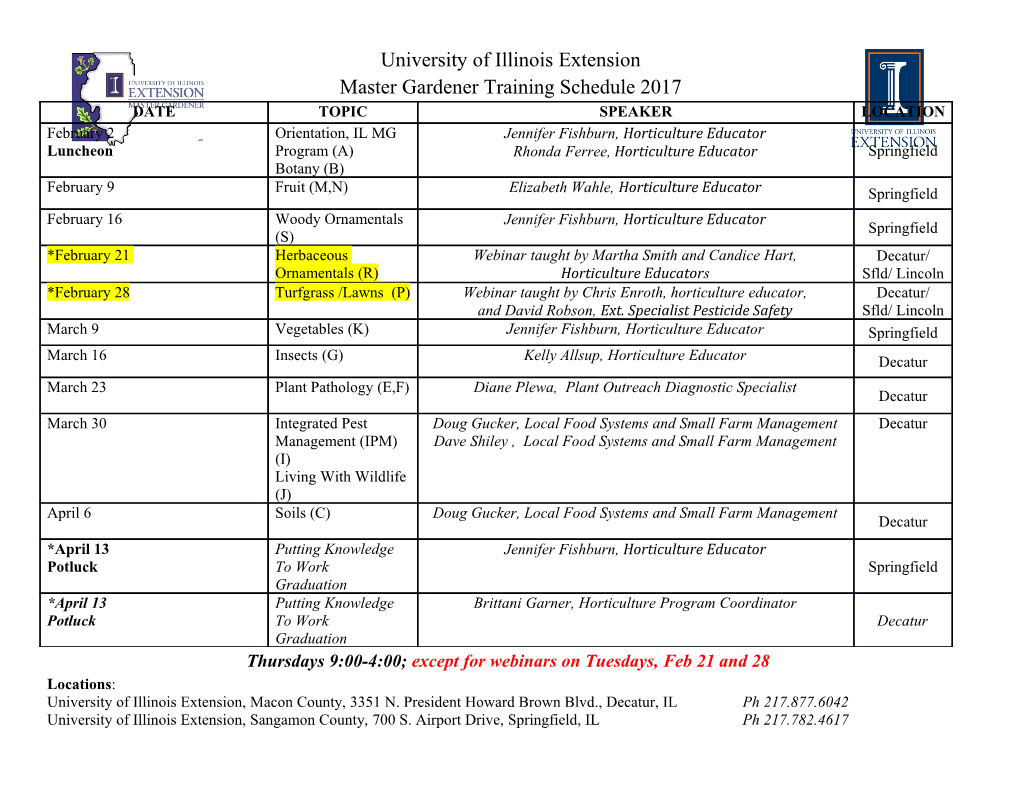
Curved and Layer. Struct. 2019; 6:41–56 Research Article H.-T. (Peter) Liu* Advanced Waterjet Technology for Machining Curved and Layered Structures https://doi.org/10.1515/cls-2019-0004 1 Introduction Received Jun 27, 2018; accepted Nov 14, 2018 Abstract: Considerable advancements in waterjet technol- Waterjet by entraining abrasives or abrasive waterjet (AWJ) ogy take advantage of its inherent merits as a versatile ma- was commercialized in the mid 1980s to take advantage chine tool have been achieved in recent years. Such ad- of its inherent merits of material independence and high vancements include, but are not limited to, process au- power of cutting [27]. At that time, it was introduced merely tomation, machining precision, multimode machining of as a rough cutting tool. Since then, waterjet technology has most materials from macro to micro scales, and cost ef- improved steadily for industrial applications [31, 35].¹ One fectiveness with fast turnaround. In particular, waterjet as of the main enablers is the introduction of the Roctec ce- a cold cutting tool does not introduce heat-affected zones ramic tungsten carbide composite for fabricating reliable (HAZ) and preserves the integrity of parent materials. As mixing tubes for the AWJ nozzle. Automation of waterjet such, for heat-sensitive materials, its cutting speed is over machining became a reality after PC-based motion control ten times faster than those of thermal-based tools, such systems were developed for precision location of the wa- as solid-state lasers, electric discharge machining (EDM), terjet stream.² In the early 2000s, waterjet machine tools and plasmas cutting. Although waterjet is basically a 2D had emerged as the fastest growing segment of the ma- machined tool, novel multi-axis accessories were devel- chine tool industry and such a trend was expected to con- oped to enable 3D machining and for machining on work- tinue.³ According to Frost and Sullivan, the growth rate pieces with 3D geometry. For composites, waterjet unlike was subsequently limited by the lack of awareness of the mechanical routers is capable of minimizing or mitigat- technology. Waterjet inherently possesses several techno- ing tearing and fraying. CNC hard tools that are in direct logical and manufacturing merits unmatched by most ma- contact with highly abrasive composite matrix often ex- chine tools [27], including: perience rapid wearing while the heat generated by ma- • A green manufacturing process that uses no toxic chining processes induces thermal damage to the com- machining fluids and produces no hazardous posite. This is a nonissue for waterjet as it is a noncon- byproduct tact tool. The only issue for machining composites with • Cold cutting that introduces no heat-affect zones waterjet was the damage caused by large stagnating pres- (HAZ) and preserves the structural and chemical in- sure developed inside blind holes during the initial pierc- tegrity of parent materials [18, 19] ing operation (before breakthrough). Considerable effort was made to understand and resolve the waterjet pierc- – High speed cutting ing damage issue. For extremely precise parts, waterjet – No need for secondary process to remove the can serve advantageously as a near-net shaping tool; the HAZ parts can then be finished by light trimming with proper • Material independent for machining most materials precision tools. Since the bulk of the material is removed from metal, nonmetal, composites, laminates, brit- by waterjet, the operating lives of the precision tools can tle materials, and anything in between [20] be greatly extended. This paper presents a collection of waterjet-machined samples to demonstrate many benefits by applying waterjet for multimode machining of curved and layered structures. 1 Refer to www.waterjet.org for extensive waterjet resource on the web 2 U.S. Patents 5,508,596 and 5,892,345 *Corresponding Author: H.-T. (Peter) Liu: OMAX Corporation; 3 (Frost and Sullivan – “The World Waterjet Cutting Tools Markets” Email: www.omax.com Date Published: 30 Aug 2005 (www.frost.com) Open Access. © 2019 H.-T. Liu, published by De Gruyter. This work is licensed under the Creative Commons Attribution 4.0 License 42 Ë H.-T. Liu – Annealed and hardened steel (mitigating dis- Window-based control software is intuitive with no steep tortion resulting from post heat treatment) learning curve. The above advancements have elevated – Non-conductive and reflective materials waterjet as a precision machine tool often competing with lasers and EDM on equal footing. In some cases, water- • One tool assisted with accessories qualified for jet with the above merits is often superior to lasers, EDM, multi-mode machining – from cutting, facing, chemical etching, and CNC hard tools. These tools are ei- drilling, trimming, milling, turning, grooving, etch- ther material selective, part thickness limited, and/or sub- ing, and beveling/countersinking [23] ject to rapid tool wear. For example, cutting metals with • Amenable to meso-micro machining [27] CO lasers or plasma cutter results in considerable heat • No direct tool contact other than the waterjet with 2 damage in terms of warping, recast, and even material va- the workpiece porization [18, 20]. In order to minimize the HAZ, solid- – Negligible side force exertion onto the work- state lasers pulsed at high frequencies and wire EDM cut piece (required only simple fixturing and in- with multiple passes were applied successfully at signifi- duced minimum part distortion) cantly reduced cutting speeds. As a result, waterjet is capa- – Tool wear independent of material properties ble of cutting heat sensitive materials over ten times faster Such merits are the drivers for the rapid maturing of than solid-state lasers and wire EDM [20]. the technology for a wide range of manufacturing applica- Layered structures consist of composites and lami- tions. nates. For machining composites, there are considerable challenges in applying CNC hard tools [5, 7]. The quality • Process automation through the development of of the drilled holes for aircraft fastener in terms of rough- novel Window-based CAD/CAM that is powerful but ness/waviness of its wall surface, roundness, and axial intuitive with no steep learning curve straightness of the hole section causes high stress on the • Precision through the incorporation of high resolu- rivet, leading to premature failure. The drilling process tion linear encoders for the traverse system and min- often induces mirocracking and delamination, leading to imizing system vibration (stiff and rigid construc- significant reduction in the strength of composites. There- tion, vibration isolation, and matched thermal ex- fore, the quality of the drilled holes can be critical to the pansion of components) life of the riveted joints for which the holes are used [8]. • Environmental friendliness through the incorpora- The reduction in residual mechanical properties of the tion of a full enclosure to minimize/mitigate air- drilled hole due to the stress concentration owing to the borne dust and mist and to facilitate quiet (< 80db), softening and resolidification of the matrix material, that safe, and clean operation has different thermal properties than the fiber, is another • Meso-micro machining capability through develop- problem. The lower values of coefficient of thermal con- ment of micro abrasive waterjet (µAWJ) technology ductivity and temperature transition in plastics lead to – Novel micro abrasive waterjet nozzles thermal damages and burning of the matrix. Tool wear is a – Patented process for consistent feeding of fine consequence of composite abrasiveness and low thermal and powdery abrasives conductivity that causes tool heating superior to what is • Cold cutting and low side force exertion enable ma- normally observed in the drilling of metallic materials. In chining extremely thin walls/webs without thermal carbon/epoxy drilling, 50% of the energy is absorbed by and mechanical distortion the tool and the remainder is absorbed almost equally by • Advanced pressure controls for piercing delicate the workpiece and chips [2]. Noticeable wear of drill bits materials such as composites, laminate, and brittle takes place after drilling approximately 30 holes leading to materials frequent replacement of consumables in order to meet the • Multi-axis accessories for multi-mode machining precision and edge quality requirements. In other words, • Precision optical locator (POL) to align the nozzle applying CNC hard tools could cost thousands of unneces- with features on parts sary dollars in tool wear and replacement. Initial applications of waterjet to machine composites In essence, the waterjet is qualified with a single tool and laminates had encountered a major issue of pierc- for 2D/3D machining of virtually any material from macro ing damage. The issue was due primarily to the low ten- to micro scales with a wide range of part size and thick- sile strength (relative to metal) of composites and ad- ness. It does not induce HAZ and preserves the structural hesive strength of laminates. During the initial waterjet and chemical integrity of parent materials. In addition, piercing, large stagnating pressure developed at the bot- Advanced Waterjet Technology for Machining Curved and Layered Structures Ë 43 tom of blind holes (before breakthrough). Piercing dam- droplets upon exiting the orifice. For machining relatively age, in the form of delamination, chipping, and microc- soft materials such as foam and rubber, the
Details
-
File Typepdf
-
Upload Time-
-
Content LanguagesEnglish
-
Upload UserAnonymous/Not logged-in
-
File Pages16 Page
-
File Size-