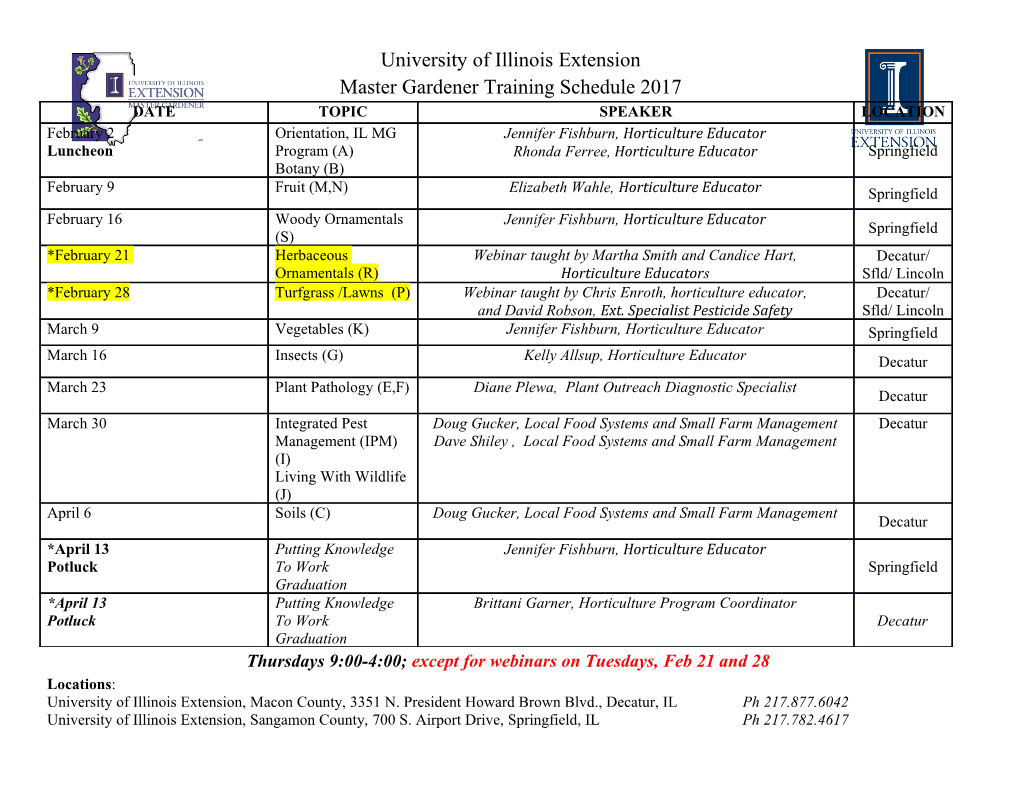
American Journal of Engineering and Applied Sciences Original Research Paper Effect of the Maximum Density Ratio Between Liquid and Vapor on Cavitating Simulation Guangjian Zhang, Weidong Shi, Ling Zhou and Desheng Zhang Research Center of Fluid Machinery Engineering and Technology, Jiangsu University, Zhenjiang, China Article history Abstract: The Filter-Based Model (FBM), which was built into CFX Received: 02-03-2015 through CFX Expression Language (CEL) and a homogeneous cavitation Revised: 18-03-2015 model were employed to simulate cavitating flow around a 2D Clark-y Accepted: 06-04-2015 hydrofoil. The effect of a maximum density ratio between liquid and vapor Corresponding Author: on sheet and cloud cavitating simulation was investigated. The results Ling Zhou show that the maximum density ratio has a significant impact on cavitating Research Center of Fluid simulation. The predicted cavitation with default value 1000 is Machinery Engineering and underestimated compared with experiment. With the increasing of Technology, Jiangsu University, maximum density ratio, the interaction interface between liquid and Zhenjiang, China vapor becomes unstable, accompanying the intermittent shedding of Email: [email protected] small-scale cavities. The cavity length and vapor volume fraction also increase. When the maximum density is increased to some degree, its effect on cavitation flow calculation becomes unobvious. A smaller maximum density ratio can ensure numerical stability but the result predicted with true density ratio is more accurate, so 20000 is recommended as the value of maximum density ratio in cavitation model to reach an optimum between accuracy and convergence. Keywords: Cavitation Model, Maximum Density Ratio, Filter-Based Model, Cavity Shape Introduction for either the mass or volume fraction of vapor, with appropriate source/sink term(s) to regulate the mass Cavitation is a complex phenomenon involving phase transfer between the liquid and vapor phases. Different transition, unsteadiness and multi-scale turbulence. It is source/sink terms have been proposed, including the well known that strong instability of cloud cavitation popular models presented in (Zwart et al ., 2004; often leads to serious problems in hydraulic machinery Singhal et al ., 2002; Kunz et al. , 1998). Huang et al . such as noise, vibration and erosion. There have been a (2009) evaluated the above three kind of transport-based number of recent experimental and numerical studies cavitation models in the same software and showed that examining the complex multiphase structures in all three different cavitation models can predict developed cavitating flows (Leroux et al ., 2005; successively the main characteristics of cavitation and Wang et al ., 2001; Zhou and Wang, 2008; Ducoin et al ., the detailed process of the cavitation development has 2012), which show that the reentrant flow plays a major small differences. Morgut et al . (2011) indicated these role on instability of cavitating flow. Especially, the models share the common feature of employing cavitation model is a critical method determining the empirical coefficients, to tune the models of accuracy of numerical simulation. Esfahanian et al . condensation and evaporation processes that can (2012) applied a barotropic state equation that links the influence the accuracy and stability of the numerical density variations to the local static pressure to solve the predictions. Ji et al . (2013) also pointed out the effect of mixture density in the cavitating flow and this method is empirical coefficients in simulating cavitating flow famous as the cavitation model based on state equation. around the 3D twisted hydrofoil. Huang et al. (2010) The other popular approach to simulate cavitating flows showed that the assumed bubble radius and volume is called as the cavitation model based on transport fraction of non-condensable gas in cavitation models equation, which solves an additional transport equation have significant effects on numerical simulation. © 2015 Guangjian Zhang, Weidong Shi, Ling Zhou and Desheng Zhang. This open access article is distributed under a Creative Commons Attribution (CC-BY) 3.0 license. Guangjian Zhang et al . / American Journal of Engineering and Applied Sciences 2015, 9 (1): 119.126 DOI: 10.3844/ajeassp.2015.119.126 The filter-based turbulence model and a ∂k ∂ u k ρm ρ m i ∂µ ∂ k ( ) +( ) = +t ++G homogeneous cavitation model were employed to µm k ρ m ε (4) ∂t ∂∂ xxσ ∂ x simulate cavitating flow around a 2D Clark-y hydrofoil i j kj in ANSYS CFX. The effect of a maximum density ratio between liquid and vapor on sheet and cloud cavitating ∂∂()(ρε ρεu ) ∂ µε ∂ m+ mi = + t µm simulation was investigated. ∂t ∂∂ xxσ ε ∂ x i j j (5) ε ε 2 Numerical Method +C G − C ρ ε1kk ε 2 m k Governing Equations where, k and ε are turbulent kinetic energy and turbulent The vapor/liquid two-phase mixture model assumes dissipation rate respectively, G is turbulence production the fluid to be homogeneous, so the multiphase fluid k rate, C = 1.42, C = 1.68, σ = σ = 0.7176. components are assumed to share the same velocity and ε1 ε2 k ε The eddy viscosity is defined as Equation 6: pressure. The continuity and momentum equations for the mixture flow are Equation 1 and 2: k 2 = µt ρ mCµ f FBM (6) ∂ u ε ∂ρ (ρm j ) m + = 0 (1) ∂t ∂ x j where, Cµ = 0.085, fFBM is the filter function, which depends on the ratio of filter scale ∆ and turbulence scale 3/2 ∂ ∂ lRANS = k /ε . The detailed Equation 7 is as follows: ρmiu ρ mij u u ∂p ∂ ( ) ( ) = − + ∂ ∂ ∂∂ t xj xx i j (2) ∆ f= Min1, C , C = 1.0 (7) ∂u∂u 2 ∂ u FBM 3/2 3 +i +j − k k / ε ()µm µ t δ ij ∂x ∂ x3 ∂ x j i k When lRANS <∆, the filter function returns the value of Where: 1.0, i.e., the RNG k-ε model is recovered. When lRANS >∆, ρm = the density of mixture flow the filter function returns the identical form as the one- ui = the instant velocity in the i direction equation LES model. p = the mixture pressure Cavitation Model µm = the mixture laminar viscosity µt = the turbulent eddy viscosity, which is obtained Cavitation model describes the mass transfer between by the following turbulence model. liquid and vapor. The present paper employed the Zwart- Gerber-Belamri cavitation model derived from a The mixture density ρm is defined as Equation 3: simplified Rayleigh-Plesset equation which neglects the second-order derivation of the bubble radius. The vapor = +1 − density is clipped in a user-controlled fashion by the ρm ρα ll ρ v( α l ) (3) maximum density ratio ρl/ρ v,clip to control the numerical stability. The maximum density ratio is used to clip the where, ρ and α are the density and the volume fraction. vapor density for all terms except for the cavitation The subscript v and l refer to the vapor and liquid source term, which uses the true density specified as components respectively. the material property. The vapor volume fraction is governed by the Filter-Based Turbulence Model following Equation 8 and 9: FBM is a hybrid model proposed by Johansen et al . (2004) based on the standard k-ε model, which blends ∂ ∂ u ρ, α (ρv, clip α v j ) v clip v + = mɺ (8) the RANS and LES methods. The turbulence with ∂t ∂ x different scales can be solved by different methods via j applying the filter function, which improves the − − prediction accuracy of multi-scale turbulent flow. ɺ 3αnuc (1 α v ) ρ v 2max(p v p ,0) m= F e Considering the advantage of RNG k-ε model RB3 ρ l compared to the standard one, the FBM employed in (9) 3αv ρ v 2 max(p− p v ,0) the present study will be based on the RNG k-ε model. -Fc The detailed equations are as follows Equation 4 and 5: RB3 ρ l 120 Guangjian Zhang et al . / American Journal of Engineering and Applied Sciences 2015, 9 (1): 119.126 DOI: 10.3844/ajeassp.2015.119.126 Where: ρ/ ρ Substituting ρ= l v ρ into Equation 8, it mɺ = The cavitation source term, which v, clip/ v ρl ρ v, clip controls the mass transfer rate between can be written as: liquid and vapor ρ = The clipped vapor density v,clip ∂ u / ∂ρ α (ρv α v j ) ρl ρ v, clip pv = The saturated liquid vapor pressure v v + = mɺ (10) ∂t ∂ x ρ/ ρ Fe and Fc = The empirical coefficients for j l v vaporization and condensation processes. αnuc = The non-condensable vapor fraction As expressing in Equation 10, the cavitation mass RB = The bubble size. transfer rate (the right term) has a strong relation with the maximum density ratio. As described in Wang et al . (2001), the flow regime These empirical constants are set as Fe = 50, Fc = 0.01, α = 5×10 −4, R = 10 −6 m. around the hydrofoil is sheet cavitation when cavitation nuc B number σ = 1.4. The sheet cavity attaches on the suction Numerical Setup and Description side of hydrofoil from the near leading edge to 0.4 c. The main part of the cavity is stable while the rear region of The computational domain and boundary the sheet is unsteady rolling up into a series of bubbles conditions are as shown in Fig. 1. The Clark-y that shed intermittently. The simulation was hydrofoil is fixed in the center of a water channel with implemented to study the effect of maximum density the angle of attack α = 8 degrees and the chord length ratio with three specific values, that is 1000 (the default c = 70 mm. The condition of no-slip wall is imposed value in CFX), 20000 (a compromised value) and 43197 on the hydrofoil surface and side surfaces of the (the true thermodynamical density ratio at room −1 tunnel.
Details
-
File Typepdf
-
Upload Time-
-
Content LanguagesEnglish
-
Upload UserAnonymous/Not logged-in
-
File Pages8 Page
-
File Size-