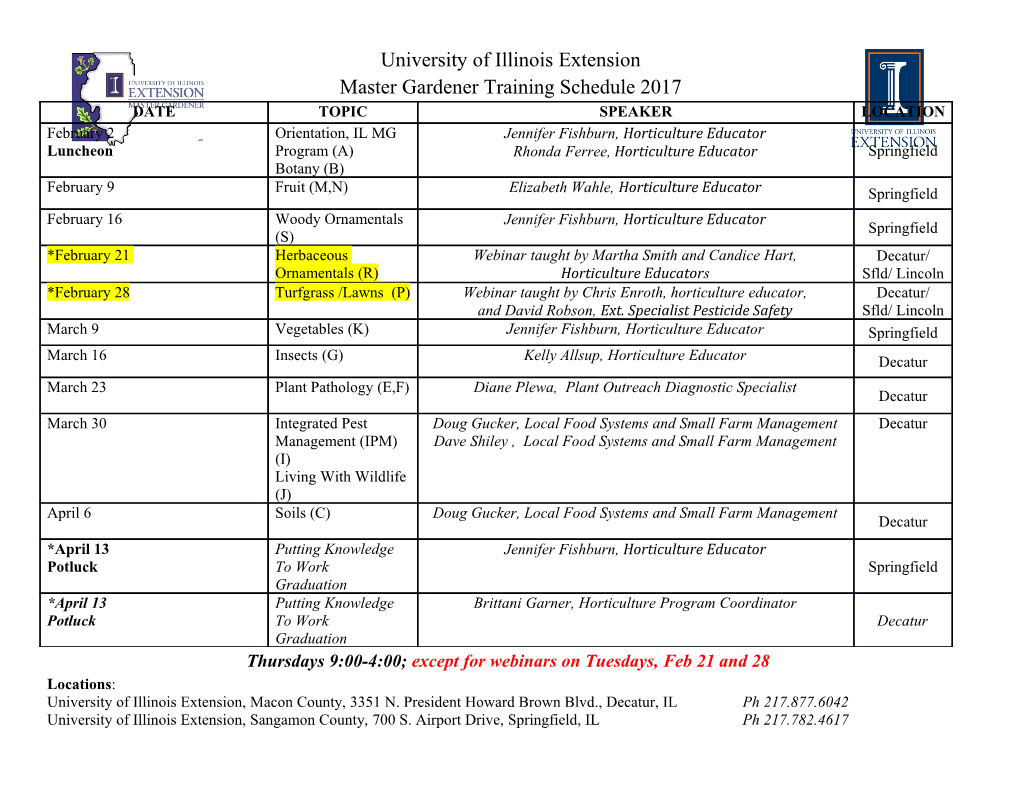
Fabrication and Characterisation of Regular and Complex Shapes Alumina from Aluminium Foil by PEO Process This dissertation submitted in partial fulfilment of the requirements for the degree of Doctor of Philosophy by Husein Meshreghi Department of Materials Science and Engineering November 2017 ABSTRACT Alumina thick and thin films can be used for a variety of purposes, including the semiconductors, electronics, dielectric, piezoelectric and ferromagnetic devices. The films can be produced by conventional methods such as tape casting and roll compaction from ceramic slurry. However, these methods offer limited part geometries and cause defects in the film structure. Plasma electrolytic oxidation (PEO) is a surface engineering technique that converts the surface of light metals and alloys into oxide ceramics layers. In this study, ceramic alumina films were produced by conversion of different shapes aluminium foil (50 µm) substrate using PEO technique. The influence of processing conditions, such as (treatment time, electrolyte composition, current density and sample shape), on the formation, growth behaviour and properties of PEO coatings were investigated. Optical emission spectroscopy was used to investigate the composition of plasma discharge and evolution of its main components during the PEO process. The plasma electron temperature was calculated using two independent peaks of aluminium in the near ultraviolet band. COMSOL Multiphysics software was used to model the distribution of electric field in the electrolyser and investigate a possibility of achieving a uniform coating thickness on complex shape in several electrode configurations. The surface morphology and phase composition of ceramic coatings were analysed using SEM and XRD techniques. The breakdown voltages, thickness of ceramic coatings in different electrolyte were comparatively studied. Depending on the treatment parameters the metal-to-ceramic conversion ratio varies from 10 to 80 %. However, after a treatment for 12 min, complete conversion of aluminium foil into alumina was successfully achieved. The shape of working electrodes strongly influenced the coating thickness. Gamma alumina was the prominent phase in thin coatings, however formation of alpha-alumina was observed when treatments lasted longer than 6 min. Correlations have been studied between characteristics of plasma discharge, such as plasma electron temperature, and phase transitions in the surface layer to develop in situ diagnostic methods for the PEO processes. I The L and U shaped thin-walled 3D ceramic-metal composite structures were successfully fabricated using PEO treatments in specific electrolyte with uniform PEO coatings without cracks grown on the edges and corners at outer surfaces of L and U shape Al foil samples. However, the coating thickness at the inner surfaces was around 30 % lower. II ACKNOWLEDGMENTS I would like to express my whole-hearted gratitude to my supervisor Dr. Aleksey Yerokhin and prof. Allan Matthews for their instructive and excellent supervision during my studies and research work, as well as their kindness and patience. Also i would like to express my deepest gratitude to Dr. Adrian Leyland for his advice and continuous support. My sincere thanks also goes to my friend Mr. M. Gorbatkov and Prof. E.V. Parfenov at Ufa State Aviation Technical University-Russia who were involved in (Chapter 7) for their support, help and useful discussions. Part of the work related to nuclear magnetic resonance experiments in (Chapter 5) has been performed with Department of Chemistry-University of Durham, UK. I would like to thank researchers at this department, D. Apperley and F. Markwell for their help My gratitude also goes to members of the Research Centre in Surface Engineering (Dr. Chen Jui Liang, Dr. Fahima Indeir, Dr. Ming Sun, Dr. Chang Liu, Dr, Lian Liu, Dr, Lian Liu and N. Yaakop). I would like to express my love and most sincere gratitude to my wife for her unlimited and unconditional support and encouragement; for her understanding and patience to share with me this experience. This work is dedicated to her, my sons Abdulalghani, Mohammed and my daughters Aisha, Asmaa and Eman. I gratefully acknowledge the financial support for my doctoral study provided by the Ministry of Higher Education, Libyan Government. I would like to thank Dr. Yerokhin again, you have been so supportive and patience of me from the start, and I am really grateful for giving me this opportunity. Finally, above all I thank the Almighty God whom I believe is the ultimate guide for enabling me to finish the project and my life in general. Husein Meshreghi Sheffield Nov-2017 III Table of Contents Chapter 1 ......................................................................................................................... 1 Introduction................................................................................................................. 1 Aims and objectives .................................................................................................... 1 Thesis organisation ...................................................................................................... 2 Chapter 2 ......................................................................................................................... 4 Literature review .............................................................................................................. 4 Alumina films ............................................................................................................... 4 Manufacturing methods of thin and thick alumina films ........................................... 6 2.2.1. Roll compaction ................................................................................................... 6 2.2.2. Tape casting ......................................................................................................... 7 Plasma electrolytic oxidation ...................................................................................... 8 2.3.1. PEO processes and associated mechanisms ........................................................ 9 2.3.2. PEO coatings on aluminium alloy substrates ..................................................... 12 2.3.3. Effect of treatment time .................................................................................... 17 2.3.4. Effect of electrolyte composition ...................................................................... 20 2.3.5. Optical emission spectroscopy of PEO process on aluminium .......................... 27 2.3.6. Mechanical properties of PEO coatings ............................................................. 28 Summary ................................................................................................................... 30 Chapter 3 ....................................................................................................................... 31 Experimental Procedures ................................................................................................ 31 Samples materials ..................................................................................................... 31 Fixing the samples ..................................................................................................... 32 Electrolyte solution ................................................................................................... 34 PEO treatment ........................................................................................................... 35 Preparation of mounted samples ............................................................................. 36 Coating characterization methods ............................................................................ 37 3.6.1. Scanning electron microscopy ........................................................................... 37 3.6.2. Coating thickness measurements ...................................................................... 39 3.6.3. X-ray diffraction analysis .................................................................................... 40 3.6.4. Nanoindentation tests ....................................................................................... 41 IV 3.6.5. Optical emission spectroscopy .......................................................................... 43 COMSOL-Multiphysics modelling .............................................................................. 43 Summary ................................................................................................................... 44 Chapter 4 ....................................................................................................................... 45 Effects of treatment time on formation of PEO coatings on regular shape aluminium foil substrates ...................................................................................................................... 45 Introduction............................................................................................................... 45 Experiments ............................................................................................................... 46 Samples analysis ........................................................................................................ 47 Characterization of current density during plasma electrolytic process .................. 48 Thickness measurements .........................................................................................
Details
-
File Typepdf
-
Upload Time-
-
Content LanguagesEnglish
-
Upload UserAnonymous/Not logged-in
-
File Pages202 Page
-
File Size-