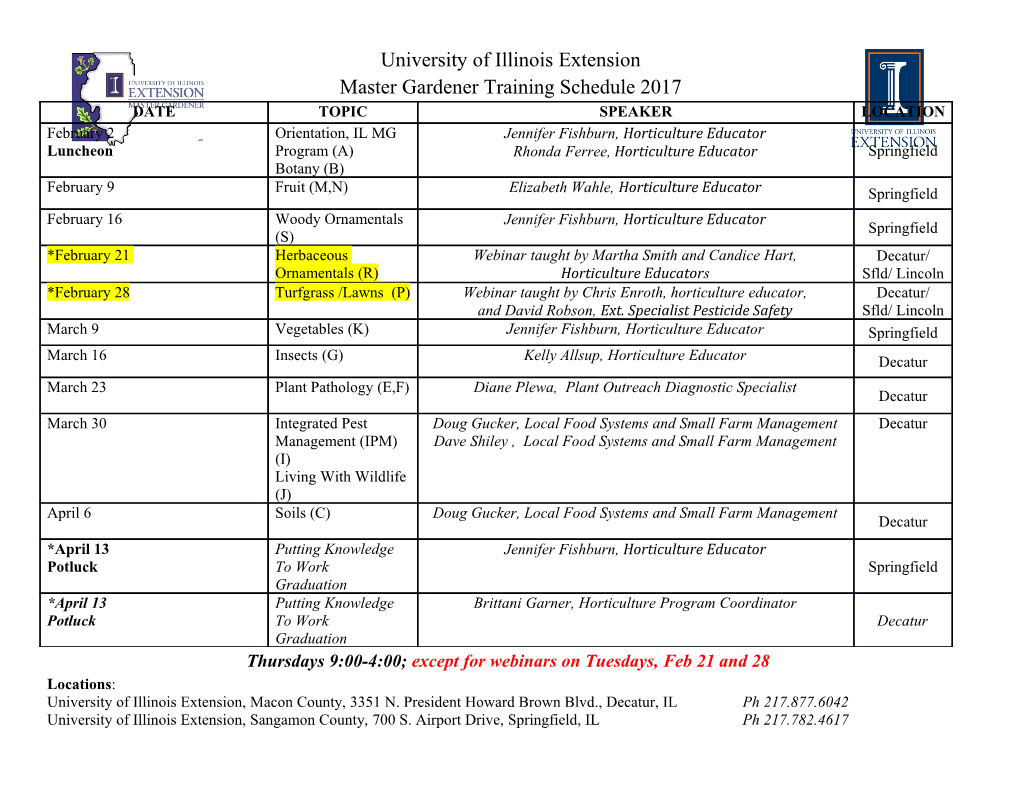
INTRODUCTION Professional bladesmiths create multi-thousand dollar blades using equipment that is worth even more. Altogether, all the equipment in a master bladesmith’s shop can reach nearly $15,000. Most, if not all, beginning bladesmiths have nowhere near that much. Master smiths use huge power hammers, a huge hydraulic-powered machine that uses tons of force to smash metal into shape. These are normally operated by a foot lever, and hit the hot steel with a sound and frequency similar to an AK-47 at full blast. When they have to do hand forging, they use anvils that weigh anywhere from 100-200 pounds, and average at $700. To heat up the steel, they use forges (built by themselves normally) that can reach 2,200 degrees Fahrenheit, and large belt grinders that cost on average at about five thousand bucks. You’re probably reading this and getting pretty daunted by those numbers. But one thing to keep in mind, is that these machines and tools only make the job easier and faster. The reason these master smiths use these expensive pieces of equipment is because it’s their living. The faster you can make a blade, the faster you get money. With any one of these bladesmiths, you can give them a simple coal forge, a railroad track, a couple files, a cement block and a piece of cardboard (for sharpening) and a utility hammer, and they can still make a blade better than any knife you can pick up at Wal-Mart. As a smith progresses, their knives gradually get better, and so they can sell more and more blades, which in turns means faster and better equipment. Some bladesmiths begin in their thirties and have enough money to get good and fast equipment. Others start young, and have rich parents that are willing to buy equipment for them. Almost all bladesmiths start at the bottom of the progression, with a railroad track for an anvil and a utility hammer. This book is for the smiths who are practically broke, just starting out, know practically nothing, but want to make a knife. This won't show you how to make a thousand dollar knife, but it will show you the basics and how to get the equipment you need to begin knifemaking. SAFETY I’m one of those people that always assumes “Oh, I’ll be fine. That’s not gonna happen” but there are still things that you MUST watch out for to avoid chopping a finger off or burning an eye out (honestly though, it would be pretty cool to be a blacksmith with an eye patch). So, here’s a little list of the essential safety things you’ll need, along with some warnings. • Ear plugs. These are more of a long-term safety than protecting against immediate accidents, but you’ll thank me when you’re 60. Honestly, I wouldn’t really wear them if the sound of loud grinders and clanging hammers just plain hurt my ears. A while back, some friends were watching me forge and when I put the steel back to heat up, they asked how come I didn’t blink every time the hammer hit. It’s mostly the sound that makes one blink (body naturally assumes that something loud will have shrapnel, and it considers eyes to have priority), and watching where the hammer hits is essential to exact forging in order to correct a mis-placed blow. After a while of forcing yourself to wear earplugs, it becomes natural and I eventually hate forging without them. Get a packet of cheap earplugs and keep them around the shop. • Face Visor. My dad bought me one of these a few years ago for my birthday, and I was fairly disappointed and thought I’d never use it. Boy was I wrong. Of all the bits and bobs in the workshop (other than the earplugs which I have on almost constantly), this is the tool I probably touch the most. It gets dirty and scratched up after a while, but I use it mainly during grinding and burning, because it blocks out much more irritation and dust than plain safety glasses. Nothing is worse than getting a little bit of something in your eye when you’re holding a high- speed angle grinder with sparks shooting every which way. I keep it on a little hook in a handy place above my workbench. It has an adjustable headstrap, but eventually I just figgered out the best-fitting size and wrapped the strap in duct tape. Much more comfortable and I don’t have to fool around with it coming undone all the time. It's especially handy because the cooling fan inside the angle grinder often blows into my face and that gets very annoying. • o Disposable dust mask. I generally only use these when there’s a lot of smoke, or if I’m using a high-speed tool to cut wood. There are many toxic varieties of wood, and you do NOT want either fumes or dust to get into your lungs. Smoke in general (like when I’m quenching or burning the tang into a wood handle) requires it, even when it's not toxic, because it is pretty painful to breath smoke in, and you don't need anything to keep you from complete concentration. • Safety Glasses. These basically fill the role of the face visor, but you can see through them easier, they’re less clunky, and you can put ‘em anywhere. However, they’re less comfortable, you normally need two hands to put ‘em on, (that is a big factor right there, you’ll soon find out) and they provide less protection. The main reason I prefer the face visor is because the cooling fan on the angle grinder often blows into my face, which gets very annoying unless if the visor blocks it. • Work Gloves. I generally use these to hold hot things; they’re perfect for holding a blade as I grind it. I don’t use them too much, but they’re handy in a panic. While forging, I generally don’t wear much safety equipment, other than glasses occasionally. Until you get very comfortable with holding hot steel and it is not likely to go flying out of your hands, you don’t need much safety equipment. Of course, there is always hot scale. Scale is the thick oxygen layer that forms over the steel at high temperatures, and is what makes the steel look black afterwards. During forging, it forms over the steel like lizard or snake scales, and heavy blows from a hammer often make it fly off. During its flight, it normally cools in the air, but sometimes it’s still hot and lands on bare skin. It stings a little, and makes you a little angry sometimes, but falls off and cools quickly. It rarely shoots upwards, but it can do a bit of damage to the eye. When starting out forging, wear gloves and eye protection until you feel really confident that it will not go flying. Drilling steel is where you really have to be careful. Drill bits are very brittle, and they, especially the thin ones, tend to snap easily. Drilling steel takes a long time, and sometimes one just pushes harder on the drill to speed things up. If you do do this (and unless you have a drill press, you definitely will), make sure that the pressure is not on just the handle of the drill, but above it, because it can bend the bit too far, it snaps, the drill shoots down at an angle, and you succeed in getting either the end of the drill bit embedded into your palm, or a nice deep gash from the point of the blade you’re drilling. I made the dumb choice once of hot drilling steel; heated up the tang of the steel and tried drilling it like that. Two mistakes there: one, that heat over-tempered and probably ruined the drill bit. Two, I drilled too much at an angle; the bit snapped, drill shot down, end of the drill bit flew to unknown parts of the garage, and my right- hand finger was jammed onto the hot steel. The steel slid along my fingernail and burned the flesh directly above it, making a yellow burn spot all over the end joint. I still have the scar, and it took months to heal up. Funny thing is, the pain wasn’t too bad; my guess is the heat just burned away the nerve endings, instead of just damaging them a little. https://mail.google.com/mail/u/0/?ui=2&ik=d9fac4d133&view=att&th=143fe23dec9890a6&atti d=0.1&disp=safe&realattid=a5b60368bff01ab5_0.1&zw Another word of warning when drilling: Once the drill is just about or all the way through the steel, it tends to grab the steel and spin it around. This is very uncomfortable for any fingers unlucky enough to be in the way. Be sure to clamp down a blade before drilling. Whenever you forge an unknown steel, or a piece of scrap, be SURE that it is not galvanized. The chemical layer, or galmanization on steel, is extremely dangerous when heated up to the point where it becomes a fume. I have heard many stories of people breathing in fumes from galvanized steel, the best-case scenario is hospital, the worst, grave. Do not risk heating up galvanized steel. If the steel has some sort of coating of something over it, and you still want to forge it, at the very least grind or file every bit of it off.
Details
-
File Typepdf
-
Upload Time-
-
Content LanguagesEnglish
-
Upload UserAnonymous/Not logged-in
-
File Pages45 Page
-
File Size-