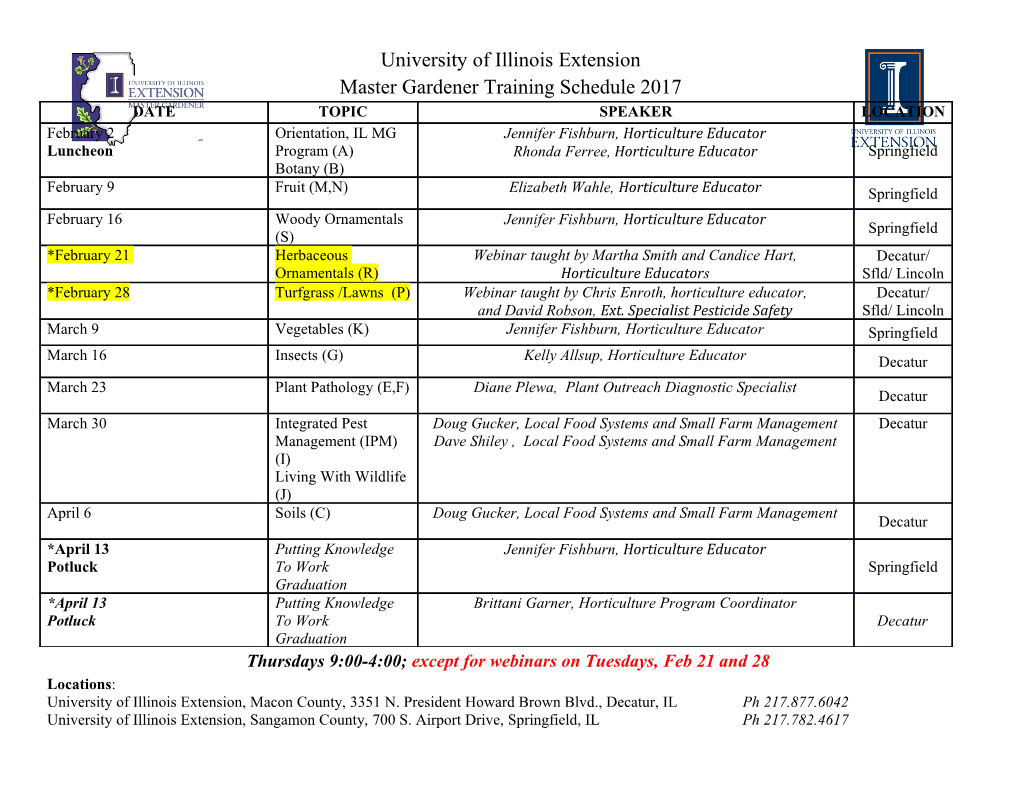
Introduction Long Staple Processing James E. Pardue, Associate Professor School of Textiles, North Carolina State University When discussing the various spun yarn formation systems, the first question that normally comes to mind is, why do we need all these different systems? Why can't one yarn system be utilized to make all spun yarns? The answer is dictated by the end product and the type or characteristics of the yarn needed. For many years we have associated the cotton system with cotton, the woolen and worsted systems with wool. This is not the case, however. Synthetic fibers are being consumed at an ever increasing rate on all yarn forming systems, so using cotton and wool to describe a yarn forming system is a misnomer today. I like to refer to the spun yarn systems as the short staple and long staple yarn fonning systems. The cotton system can be considered as a means of utilizing relatively short staple, fine fibers for the formation of a smooth, strong, lean or low bulk yarn. This is created by the many processes through which the fibers pass with the corre- sponding high draft levels which straightens the fiber to a higher degree. This causes the fibers to lie more parallel to the axis of the strand so the twist can bind a "* greater portion of the fiber length into the cylinder of yarn. NOTE: In theory, with the fiber parallel to the axis before twist is inserted, one-eighth of an inch of each fiber is not trapped by the twist. This means there are more fiber ends per unit length standing out from the surface of the yarn. this means that a decreased portion of the fiber strength is imparted to the yarn, which is why a spun yarn is weaker than a filament yarn of the same size. Most people connect the worsted system with the woolen system, but actually the worsted system takes over where the cotton system ends, as far as fiber length is concerned. We normally consider a fiber of 2.5 inch staple as maximum for the cotton system and as a minimum length for the worsted system. Then the worsted system is used to make the same type yarn as the cotton system, with fiber lengths ranging up to 9 inches. NOTE: With the longer staple length, there are fewer individual fibers per length of yarn; therefore, fewer fiber ends on the surface. Looking at this from another viewpoint, since the fiber length above three inches does not contribute substantially to the strength of the yarn, higher spindle speeds with a corresponding increase in centrihgal force will cause a greater fiber length to stand out from the surface of the yarn, creating a fuzzier yarn, and hence, more surface cover to the fabric. The Woolen system is entirely different from the other yarn forming systems in b regard to the types of yarns produced. with a simplified flow system, fewer 6-2 Long Staple Processing manufacturing processes, and low draft levels causing less fiber orientation, a bulkier yarn is produced. The fibers are not parallel when they reach the spinning process, but are crossed and intertwined. The fibers are trapped in this position with the insertion df twist, creating air pockets in the yarn, and more fiber ends standing out on the surface of the yarn. This increases the volume per unit weight. We can summarize by saying that the primary end use of yarns made on the cotton system are such things as knit undergarments and men’s hosiery, sheetings, broadcloth, summer suitings and other hard finish fabrics, as well as fine flannels, herringbone, etc. The woolen system makes yarns for such things as blankets, heavy suitings for men and women, including flannels, tweeds, herringbone, etc., and spun carpet yarn. Now, how do we process fibers into yarns on the woolen and worsted systems and control their characteristics? _- Long Staple Processing 6-3 Woolen And Worsted Systems Worsted Woolen El Chemical Cleaning Chemical Cleaning scour Acid Treat* Acid Treat* Wash I ;: 1 Oil I Mechanical Cleaning Mechanical Cleaning I Roller-Top Carding v And Tape Condenser Pin Drafting (X Times) I Combing I Pin Drafting (Y Times) I Roving I I I Ringspinning IRing Spinning I I Winding I Winding Or Skeining NOTE: Waste from the worsted process is often sold to woolen processors. * Optional depending on vegetable matter content 6-4 Long Staple Processing A Typical Tow-To-Top System (Stretch-Break System) (To provide potential bulk in product and to reduce the breaking elongation of the Stretch tow to facilitate stretch F"p" breaking). (Rollers are massive and therefore only long staple Stretch can be produced in a single I";"[ pass. Draw ratio greater than breaking elongation of tow feed). (To give cohesion to staple fibers). 8Top (Sliver) Ring Spinning I Long- Stap le Yarn Manufacturing (wool, man-made) MODIFIED WORSTED Preliminary Treatments Preliminary Treatments Tow to Sliver Opening & Blending Opening & Blending Fiber Settting Picking -(optional) Picking Carding Carding (2 or 3 sections) I1 I ServoDrafting Servo Drafting Combing (opt.) T Roving Spinning Spinning 4l A PWinding 9Winding 9Plying vPlying Plying rlWinding xWinding 6-6 Long Staple Processing Characteristics Of Woolen Yarns Wool fibers usually less than two inches in length Made from carded yams Fuzzy; fiber ends protrude from yam Uneven diameter Bulky and thick Wide range of fiber length Spongy and springy feel Result in soft, bouncy fabric structure Hidden weave construction Allow for napping and brushing finishes Replace insulating properties providing warmth (used in outerwear type garments) Resist wrinkling; wrinkles hang out Do not hold a crease well Fibers used can be from soft wastes or hard wastes 9- Shrinking of wool goods after they are woven makes it possible to conceal many varieties of fibers. Long Staple Procwslng 6-7 Figure 6-1 Feeding End Of A Continuous Scouring Train SCOURING BOWL DE LIVERY SQUEEZE --FEEDER 52ft. x 42in. LAlllCE ROLLERSI OhFOR WASTE UQUOR -- 6-8 Long Staple Processing I Table 6-1 Operational Data For Desuin ling Method Bowl 1 2 3 4 Length, ft 32 24 16 16 Capacity 2,000 1,500 1,000 1,000 Initial charge, lb Soda ash 75 10 Soap 10 7 Hourly Feed Soda ash 25 5 Soap - 3 Immersion Time, min. 3 2.5 1.5 1.5 Temperature, OF 90 130 125 120 -- Long Staple Processing 6-9 I Table 6-2 Operational Data For Neutral Scouring Process Bowl I 112 314 I Length,ft 32 1 24 I Capacity, gal 2,000 1,500 1,000 1,000 - I Initial charge, a lb detergent +10 I Hourly feed, Ib detergent 5 - I. Flow back, gph - I 750 750 750 I Immersion time, min 3 I 2.5 1.5 1.5 I Temperature, OF 90 I 150 150 I 120 'r, Initial charge and feed rate for fine domestic wool 6-10 Long Staple Processing Figure 6-2 Drying End Of A Continuous Scouring Train _- Long Staple Processing 6-1 1 Figure 6-3 Fearnaught Teaser Or Picker 6-12 Long Staple Processing Figure 6-4 Worsted Card I GOSSETT MACHINEWORKS Long Staple Processing 6-13 Figure 6-5 Diagram Of Three-Cylinder Woolen Card 6-14 Long Staple Proceslng Figure 6-6 Cross Lapper Breaker cardset To Finisher Card Set -- Long Staple Processing 6-15 Figure 6-7 Tape Condenser Flwn card Rubbings WebDivision W 6-16 Long Staple Processing Figure 6-8 Sectional Elevation Of The Double-Sides MWR 5 Platt Ring Spinning P Long Staple Processing 6-17 I Figure 6-9 HMG Chain Gill Drafting System 6-18 Long Staple Processing Figure 6- 10 Raper Autolever Pindrafter 3' ------- I- - .f I II m Long Staple Processing 6-19 3 Figure 6-1 1 Schlumberger Comb _- 6-20 Long Staple Processing rIt t Figure 6-12 Details of a French Comb A. FeedRolls F. Drawing-off Rolls B. Feeding Gills G. BrushRoller -- C. Nipper Jaws H. Noil Roller D. Comb Cylinder I. DofferComb E. Top or Intersector Comb Long Staple Precessing 6-21 I Figure 6- 13 Intersecting Pindrafter, Three-Roll Delivery , ! ‘L ! 6-22 Long Staple Processing Figure 6- 14 Roving _- Long Staple Processing 6-23 Figure 6- 15 Ring Spinning ROVING DRAFT ROLLERS 1' 1' THREAD GUIDE .E R TR RAIL U _- 6-24 Long Staple Processing I Figure 6-16 Open Wind Coner Yam-Groove Traverse Cam-Acthrated Traverse Take-L Driving 'Traverse / Drum Long Staple Processing 6-25 I Characteristics Of Worsted Yarns Wool fibers usually 2 - 8 inches in length 0 Made from combed yams Smooth Even diameter Tightly twisted Fine, hard yarns Distinct weave construction -cI Do not produce insulating properties Show undesirable wrinkles Maintain desired crease 6-26 L~ngStaple processing Figure 6- 17 Heat Stretch 00 4'g Q I I Long Staple Processing 6-27 Figure 6- 18 Continuous Sliver Relaxer (CSR) Piping Arangement Hkrh inhlDhrrkded 13m) ppe k." I 6-28 Long Staple Processing .
Details
-
File Typepdf
-
Upload Time-
-
Content LanguagesEnglish
-
Upload UserAnonymous/Not logged-in
-
File Pages30 Page
-
File Size-