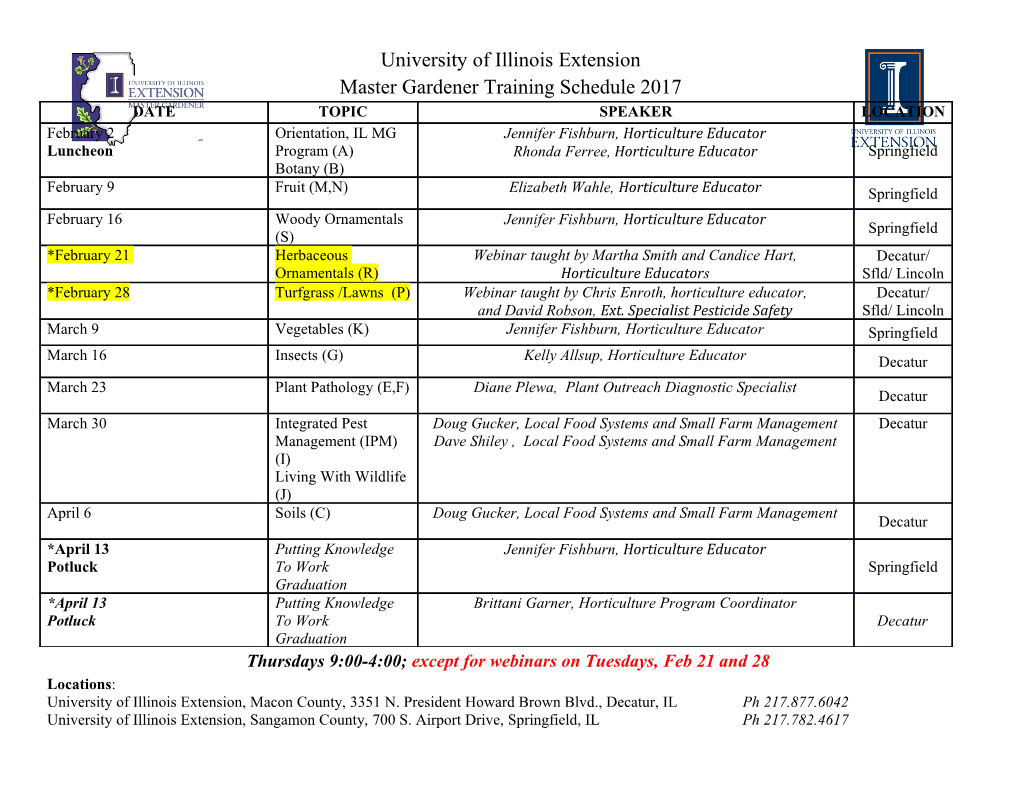
Numerical visualization and quantification of chaotic mixing for micromixers Tae Gon Kang and Tai Hun Kwon Department of Mechanical Engineering, Pohang University of Science and Technology, San 31 Hyoja-dong Nam-gu, Pohang, Kyungbuk, 790-784, Korea E-mail: [email protected] ABSTRACT But there are several drawbacks in this approach. If the deformation of interface is too complicated or the length of We present a systematic way of visualization and channel is too long compared with the dimension of the quantification of mixing in chaotic micromixers with a height or width, the approach mentioned above may not periodic mixing protocol. We name it colored particle catch the precise interface due to the numerical diffusion tracking method, which consists of three steps. One is flow and insufficient resolution of discretization for analysis step to obtain periodic velocity field of a periodic computational domain. For three-dimensional numerical mixing protocol. The other is particle tracking step. At the analysis of flow and mass transport, moreover, it needs inlet, depending on the species of the fluids, particles are enormous computational resources and CPU time to carry labeled with a specific color. Then, using the initial out mixing analysis for the entire micromixer. Therefore distribution of colored particles, we repeat integration most of mixing analysis did not cover the entire micromixer procedure up to the end period. Finally, from thus obtained but is limited to analyze the basic flow characteristics and particle distribution, we can evaluate mixing performance. mixing pattern in a single period or at most two periods. In the present study, we propose a new measure of mixing Micromixers of interest in current work are patterned by adopting the concept of the information entropy. We grooved micromixers. For this kind of micromixers, applied the developed method to three micromixers with recently, there have been several theoretical and patterned grooves and were able to evaluate mixing experimental works [7,8]. More recently, there has been a performance both qualitatively and quantitatively. numerical study for the patterned groove micromixer by Wang et al [9]. To investigate the mixing performance of a Keywords: microfluidics, micromixer, chaotic mixing, micromixer clearly, it is required to carry out a numerical Galerkin/Least-squares (GLS) method, particle tracking analysis for the whole domain. Therefore, it is essential to have an efficient numerical scheme for the entire domain 1 INTRODUCTION and a quantitative measure of mixing for the evaluation of mixing performance. Micromixer has a variety of applications in many The goal of the present work is to develop a systematic biological processes [1]. It is well known that mixing in way of visualization and quantification of mixing in chaotic microchannel is difficult to achieve because most flows in micromixers with a periodic mixing protocol. We name it micro scale belong to the regime of creeping flow, in which “colored particle tracking method”, which consists of three mixing is dominated by molecular diffusion. steps: the first is the periodic velocity field analysis; the Since early micromixer relies on only molecular second is the particle tracking using particles labeled with a diffusion, it takes very long mixing time to mix two specific color depending on the species; and the third is the different fluids [2]. But one can achieve enhanced mixing quantitative measure of mixing from the particle by incorporating chaotic advection [3,4]. In chaotic distribution. Finally, we will present the results of the advection, fluid particles exhibit very complex trajectories application of the developed numerical method to three even in creeping flow regime. Chaotic advection refers to patterned groove micromixers. kinematical phenomena in which motion of fluid particles is chaotic in Lagrangian sense even though the velocity 2 NUMERICAL METHODS field in Eulerian sense is simple. Since chaotic advection is possible to occur in micro scale, it must be a practically Colored particle tracking will be introduced in this attractive mixing mechanism for micromixers. Many section method as an efficient numerical method for researchers have proposed various micromixers analyzing micromixers with the help of a periodic mixing incorporating chaotic advection [5-8]. protocol. It consists of three steps. First, periodic velocity As far as mixing analysis of micromixers is concerned, field of repeating mixing protocol is calculated via most of numerical studies regarding micromixers are Galerkin/Least-squares (GLS) method [10]. Second step is focused on solving mass transport equation in order to the particle tracking. In this step, many particles are tracked visualize and evaluate mixing performance of micromixers. using the velocity field obtained from the first step. The essence of this stage is the color labeled to particles NSTI-Nanotech 2004, www.nsti.org, ISBN 0-9728422-7-6 Vol. 1, 2004 247 according to their species. Since color information of a particle is an intrinsic property, it is possible to measure © ¢ 2 D()u : D ()v d § mixing from the distribution of colored particles at a specific cross section. The final step is the quantification of ¥ ¢ ()¢ () § mixing with a proper measure. A measure of mixing is − p ∇ ⋅ v d + ∇ ⋅u qd § ¥ introduced by using the concept of information entropy. ¥ This overall approach is thought to be a general way of £ (8) © ¨ § + ¢ ()()∇ − ∇ ⋅()()⋅ ∇ analyzing mixing in a micromixer composed of a periodic p 2 D u q d k k ¥ mixing protocol. The detailed method is described in the k £ following sections. ¦ + []ϕ ⋅()()− + ⋅ − = ¢ ⋅ ui uo vi v o t vd ¤ ∪ ¤ 2.1 Finite element formulation i o A steady state, incompressible Stokes equation and 2.2 Particle tracking boundary conditions are represented by During the particle tracking procedure, one can identify ∇⋅()2µD −∇p = 0 in Ω (1) the species of particles by their intrinsic color assigned initially. The problem of tracing the position of particles ∇⋅u = 0 in Ω (2) can be stated as integrating the following equation = Γ u 0 on w (3) = −∆ + µ ⋅ Γ dx = t pn 2 D n on i (4) u (9) = µ ⋅ Γ dt t 2 D n on o (5) where x is the particle position vector, u is the particle where u is the velocity, p is the pressure, µ is the viscosity, velocity, and t is the time. Instead of dealing with the D is the rate of deformation tensor, ∆p is the pressure drop original equation (9), it turns out to be helpful to modify it within one period, n is the outward normal vector to the to a two-dimensional problem as boundary surface, and t is the traction force. In above Ω Γ Γ Γ equations, , w, i, and o denote bounded domain, wall dx u ~ boundary, inlet boundary, and outlet boundary respectively. = = u dz w In addition to boundary conditions described above (10) equations, periodic boundary condition is applied to the set dy v = = v~ of two corresponding nods, one for inlet and the other for dz w outlet. In equation (10), u, v, and w are the velocity component of = Γ Γ th ui uo on i and o (6) x, y, and z coordinate, respectively. The 4 order Runge- Kutta method is used to integrate the set of ordinary Since periodic velocity condition is a kind of constraint to differential equations. be satisfied by the velocity at the inlet and outlet surface, What we need in integrating equation (10) is the this condition is implemented via Lagrangian multiplier information of velocity at a certain spatial location. In this method as follows. particular case, velocity field is obtained from the solution of finite element formulation. Therefore velocity data is ¡ available at the nodal points. Thus, after searching the ⋅ ()u − u = 0 (7) i o element in which a specific particle is located, spatial interpolation is required to find out the velocity at the The final weak form incorporating periodic boundary desired location. Then a particle can be moved to a new condition is obtained by adding additional terms due to the position and at that location particle has the information of Lagrangian multiplier to the original weak form of coordinates and species. Galerkin/Least squares (GLS) method. In equation (8), ϕ is the weighting function for Lagrange multiplier, λ. By 2.3 Measure of mixing employing GLS method, we can circumvent the compatibility condition of velocity and pressure This section presents a way of characterizing mixing interpolation function so that equal order interpolation performance quantitatively by employing mixing entropy. function may be used [10]. In the present finite element First, a cross sectional area of micromixer is divided by formulation, we use tri-linear interpolation function for all finite number of cells. Then, for a certain particle variables, u, p, and λ. configuration of multiple species, the mixing entropy is 248 NSTI-Nanotech 2004, www.nsti.org, ISBN 0-9728422-7-6 Vol. 1, 2004 defined as a sum of the entropy of individual cells barrier is 20 µm, and the length of barrier is 720 µm, which constituting the cross sectional area: corresponds to the length of six grooves. The most important feature of a micromixer is its flow ¦ £ NcsN characteristics, which determines final mixing performance. ¤ = − ()¡ Therefore, accurate velocity field is essential for the mixing ¥ S wi ni,k log ni,k ¢ (11) i==11k analysis by particle tracking. In the particle tracking stage, particles are just the fluid particle; thus there is no In the definition of mixing entropy, equation (11), i is the interaction between particle and flow so that particles are just convected with the given velocity field of a micromixer. index for the cell, k is the index for the species, wi is the Before mixing analysis via colored particle tracking, weighting factor for the cell, Nc is the number of cells, Ns is Poincaré sections are plotted to examine the dynamical the number of species to be mixed, and ni,k is the particle number fraction of the kth species in the ith cell.
Details
-
File Typepdf
-
Upload Time-
-
Content LanguagesEnglish
-
Upload UserAnonymous/Not logged-in
-
File Pages4 Page
-
File Size-